Employing Single-use Technology to Control Frozen Bulk Drug Storage: The Cold Hard Facts
Table of contents
ShowIn cooperation with Single Use Support and Biogen, Entegris has published a new white paper concerning the employment of single-use technology to control frozen bulk drug storage.
Single Use Support advocates the use of single-use systems in the production of biopharmaceuticals as well as cell- and gene therapies. We close the gap between downstream and the fill & finish process. On the basis of single-use bags we offer manufacturers of biopharmaceuticals access to a new and 100% reliable drug substance logistics process . Our technologies increase patient safety while at the same time minimizing the risk of biocontamination and product loss to 0%. It is our mission to push patient safety to the highest possible level by optimizing single-use technology for the biopharma industry.
Development and production requirements for biopharmaceuticals
Newly developed biopharmaceuticals that are constantly improving and potentially life-saving can be very profitable for their developers. However, R&D is cost-intensive and requires major investments, which is why reliable and cost-effective storage and logistics of frozen drug substances play a decisive role.
This is especially true in terms of the transition from R&D through clinical trial to high-volume production. The minimization of capital and operating expenses as well as the reduction of storage space and of time and energy spent on cleaning and sterilization are important objectives when choosing a new storage and logistics solution. At the same time, the valuable drugs have to be protected from cross-contamination and other sources of contamination.
Compared to traditional systems, single-use systems have considerable advantages
Traditionally, bottles and stainless-steel Cryo vessels are used for storage and shipment of frozen biopharmaceutical bulk drug substances. While both of these containers have their strengths, they also have their deficiencies: Bottles are bulky and non-scalable; they can slow freezing and thawing. Systems based on Cryo vessels are expensive and increase the complexity of cleaning processes as well as the containers’ reusability. This is why manufacturers of biopharmaceuticals are increasingly introducing single-use systems. Single-use systems exhibit a higher degree of scalability and allow for a controlled freezing and thawing process. Plus, they do not require any time-consuming returning and reutilization processes.
The last 15 years have seen an increased implementation of single-use technologies to successfully deal with critical process challenges when manufacturing drug substances designated for the international market. An improved production process spanning several production sites, reduced cleanroom floor space, improved process economics/plant flexibility and reduced Clean-in-Place (CIP) and Steam-in-Place (SIP) processes are just some of the advantages associated with the implementation of single-use technologies.
White paper concerning the implementation of single-use systems in the biopharmaceutical industry
The implementation of single-use systems poses certain challenges that need to be overcome in order to fully exploit the technology’s advantages. The white paper “Employing Single-Use Technology to Control Frozen Bulk Drug Storage” addresses challenges in terms of storage, logistics and other critical factors that manufacturers have to consider in deciding whether and how to adopt single-use technologies. The paper deals with material requirements as well as requirements concerning (single-use filtration system) the filling-, freezing-, storage-, logistics- and thawing processes. Finally, the paper also introduces and discusses specific options for the one-way storage of pharmaceuticals.
Overview
Single-use Technology - New biopharmaceutical drug products that alter and even save lives can be very profitable for their developers. They are, however, costly to develop and represent significant investment, particularly at the end of the manufacturing process.
For this reason, safe cost-effective frozen storage and shipping are critical, especially as drugs transition from R&D through clinical trial and to higher volume production.
The objectives for choosing a new storage/transport method include minimizing both capital and operating expense, reducing facility space requirements, and cutting time and energy for clean-in-place and steamin-place processes.
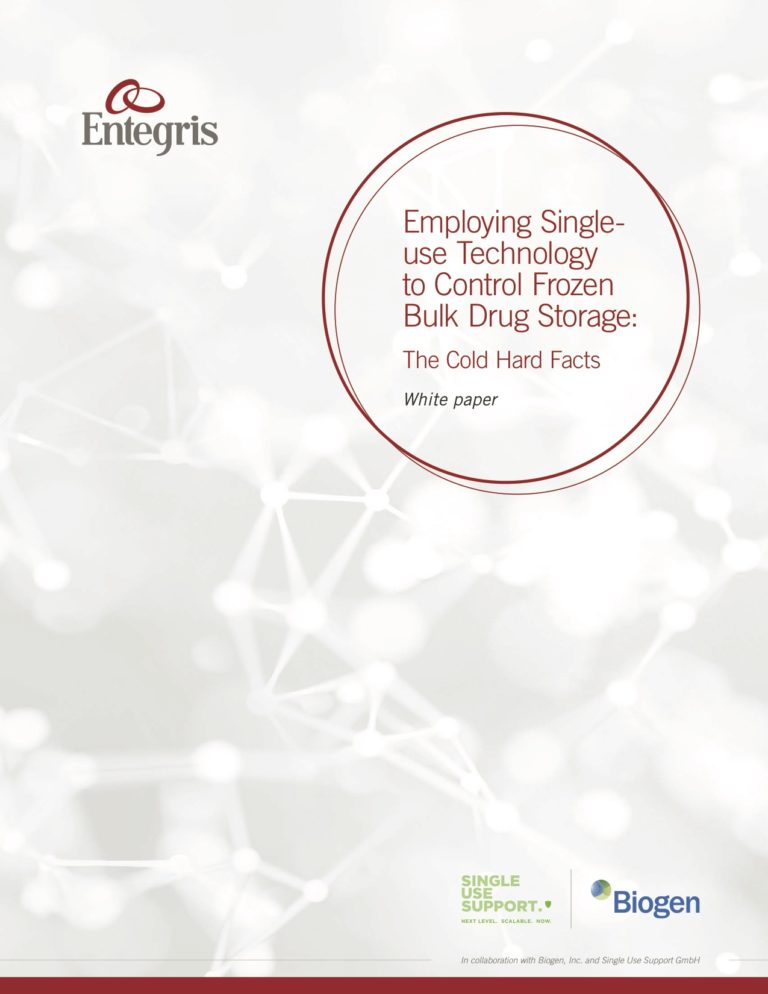
At the same time, valuable product must be protected from cross-batch or other sources of contamination.
The traditional approaches for primary packaging in frozen applications have been bottles and stainless steel cryo vessels. While each has its strengths, both have significant shortcomings.
Bottles are bulky, non-scalable, and can slow freezing and thawing. A system of cryo vessels is costly to build and operate and adds layers of complexity in the return, cleaning, and reuse of vessels.
For these reasons, manufacturers are adopting a system of single-use bioprocess containers to eliminate bulk, scale as necessary, control freezing and thawing, and eliminate the need to manage container returns and reuse.
This paper addresses the challenges of bulk drug substance (BDS) storage, shipping, and other critical factors users must consider in deciding whether and how they will adopt the technology.
It will touch on material challenges and on the filling, freezing, storing, transporting, and thawing process requirements that single-use packaging must meet. Finally, it will present specific options to consider in moving toward single-use drug substance storage.