cGMP - everything you need to know
Table of contents
ShowThe current Good Manufacturing Practice (cGMP) regulations - originated and checked by the FDA - apply to companies operating in pharmaceutical, biotech, or med tech industries.
They require the latest standards in terms of production, manufacturing, and packaging and thereby ensure pharmaceutical quality meaning quality in biopharmaceutical processing and patient safety as the ultimate goal. The detailed guidelines, importance of cGMP, and how companies can best meet the cGMP regulations, are discussed in the following.
Current good manufacturing practices in the biopharmaceutical industry
Manufacturers in the biopharmaceutical industry are required to comply with cGMP. For good reason: Taking medicines must be safe for patients. The complex regulations affect many different areas involved in the production and manufacturing process, such as facilities, equipment, staff, testing, or documentation. But what are ways to comply with cGMP?
End-to-end solutions based on automated single-use technologies are an auspicious choice for drug substance manufacturers given their many advantages. Their implementation in the manufacturing process promises efficiency, high product quality, cost reduction, and energy savings.
cGMP definition
Current Good Manufacturing Practice, also known as cGMP, are a set of regulations that ensure the quality of pharmaceutical products, medical devices, biotechnology products, food and beverage, and dietary supplements. They therefore apply to all organizations involved in the manufacturing processes of these products.
To be compliant with the cGMP regulations, companies must meet the latest quality standards. These apply to buildings and facilities, equipment, production, process controls, laboratory controls, packaging and labeling, and returned or salvaged drug products.1
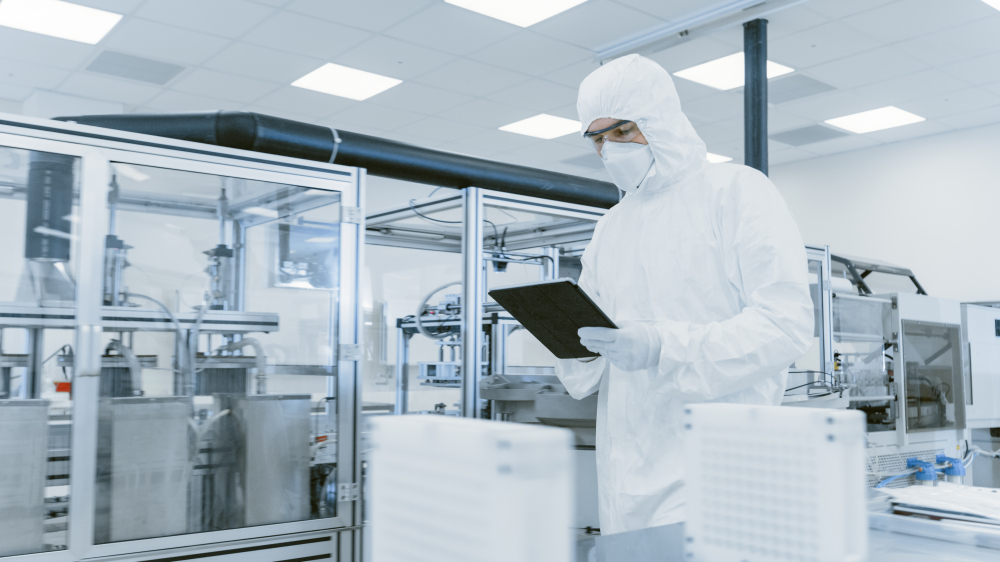
What is GMP?
Like the cGMP, Good Manufacturing Practice (GMP) is part of quality assurance and ensures that companies involved in manufacturing, processing, and packaging drugs, medical devices, some sorts of food, and blood follow certain quality and effectiveness standards. Thereby they should eliminate or at least minimize any kind of contamination, mix-ups, or errors guaranteeing that customers purchase effective and safe products. They concern issues such as equipment verification, process validation, record keeping, and process improvements in form of standardization.
GMP guidelines are very general in nature, meaning that the manufacturers decide and interpret themselves how to best implement them in their business. However, they do have the force of law and can in some cases result in fines, recall, seizure, and jail time if failed to comply.
Since those regulations frequently change, the so-called current Good Manufacturing Practice (cGMP) is a more recent version of the GMP requiring companies to use technologies and systems that are up-to-date.2
cGMP vs GMP: What is the difference?
Seemingly no difference, the timeliness of the regulations results in differences between GMP and cGMP in terms of quality, cost, and standards:
- Quality: While GMP covers the required standards of an industry, cGMP ensures that a company is following/applying the latest regulations.
- Cost: Due to additional testing and state-of-the-art technologies, cGMP is more expensive to implement and maintain than GMP.
- Standards: GMP regulations are the minimum standards required for pharmaceutical, biotech, medtech, and medical devices industries. With cGMP, on the other hand, companies make sure that they are compliant with the most recent rules and regulations applicable to their industry and also that each step was completed using the latest available methods
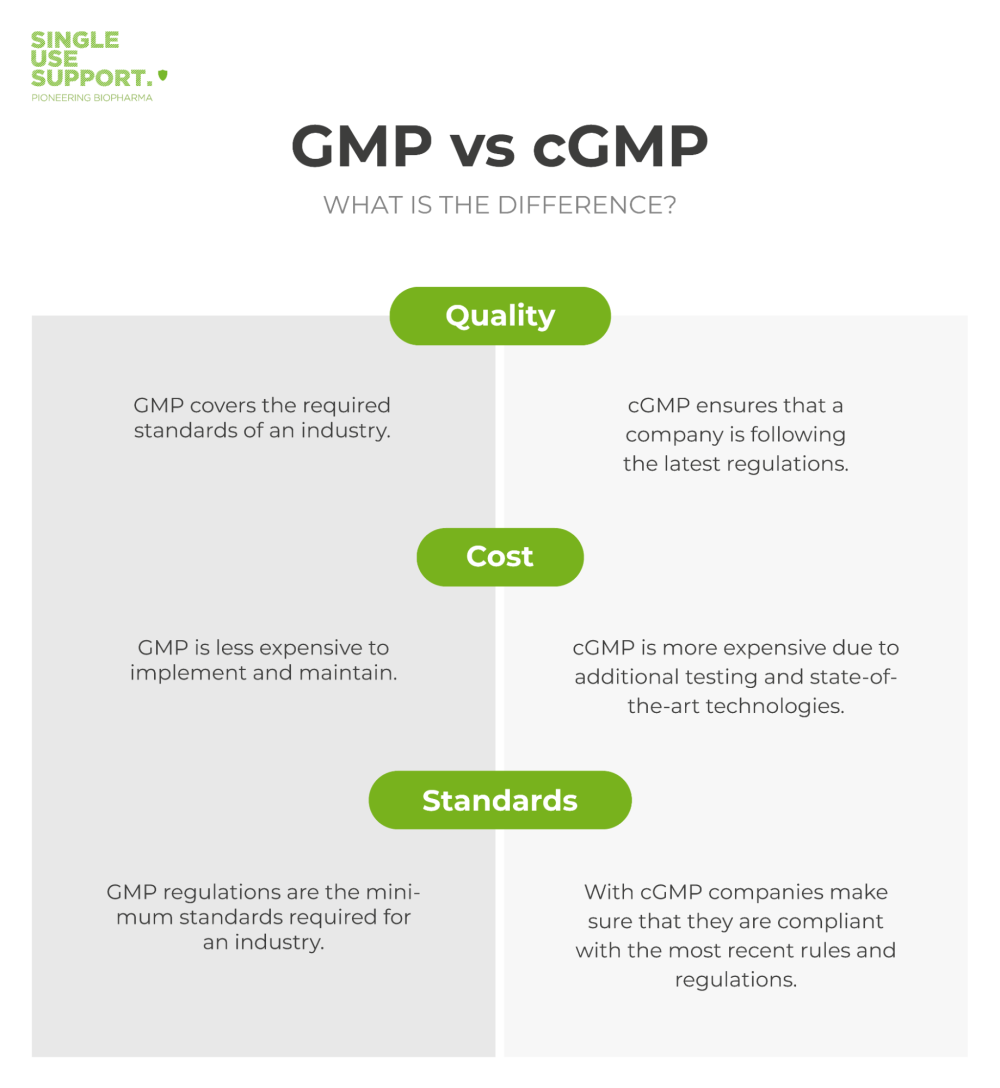
What is EU GMP Annex 1?
EU GMP Annex 1 is a regulatory guideline that sets standards for manufacturing sterile medicinal products. The guidelines are set by the European Medicines Agency (EMA) and FDA. It focuses on aseptic processing and contamination control to ensure product safety and quality. The annex covers various areas such as facility design, environmental monitoring, personnel training, and process validation. One significant aspect influenced by Annex 1 is the use of single-use assemblies in fluid management processes. It emphasizes the need for a risk-based approach to ensure the integrity and sterility of single-use systems used in closed systems for fluid management. Compliance with GMP Annex 1 is crucial for companies operating in the biopharmaceutical industry to meet regulatory requirements and maintain high-quality standards.
FDA cGMP guidelines
cGMP compliance is monitored by the Food and Drug Administration (FDA). It sets the rules of CFR (Code of Federal Regulation) Title 21 based on the Federal Food, Drug and Cosmetic Act. The parts addressing the cGMP, list the minimum requirements of the production process from start to finish in order to ensure that the drug product has the identity, quality, strength and purity promised.3
The cGMP guidelines are described in several parts of Title 21 and allow a good understanding of the regulatory process:
21 CFR Part 314: Applications for FDA Approval to Market a New Drug
21 CFR Part 210: cGMP for Manufacturing, Processing, Packing, or Holding of Drugs
21 CFR Part 211: cGMP for Finished Pharmaceuticals
21 CFR Part 212: cGMP for Positron Emission Tomography Drugs
21 CFR Part 600: Biological Products: General
cGMP requirements:
The following three paragraphs will outline 21 CFR Part 210 in which most regulations revolve around requirements for staff, equipment, facilities, and the production process.
1. cGMP requirements of staff
Especially for companies and organizations involved in drug manufacturing and therefore representing a key cGMP requirement, qualified and trained staff is crucial. The personnel must be appropriately qualified and trained and keep up-to-date with the latest training and knowledge relevant to their tasks.
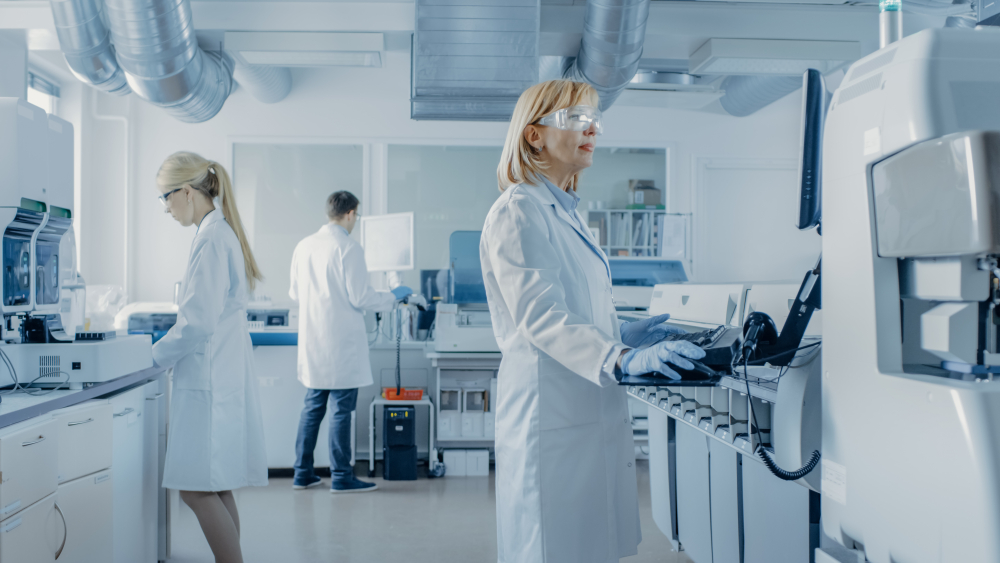
2. cGMP requirements of facility & equipment
To be compliant with cGMP regulations, pharmaceutical companies’ buildings and production facilities must be properly and thoroughly maintained to ensure safe and effective manufacturing conditions. Similarly, current Good Manufacturing Practices require organizations to have modern equipment that is conscientiously maintained and not outdated at any time. The same applies to the Standard Operating Procedures (SOP).
3. cGMP requirements of processes & products
cGMP recommend that the processes used to manufacture pharmaceutical products involve the latest science and technology. In addition, it is crucial that a master formula is adhered to for each product throughout the manufacturing process without any deviations.
How is the FDA controlling cGMP compliance?
The FDA’s role is to first promulgate cGMP regulations and guidance documents and then to determine whether the quality of pharmaceutical products comply with those regulations. In doing so, trained FDA assessors and investigators inspect companies around the world to verify that the facilities, where active ingredients and finished pharmaceutical products are manufactured, meet the standards. Inspections follow a standard procedure and are often based on reports or concerns flagged by the public and the industry. If cGMP violations are found, the manufacturer should implement corrective and preventive actions as part of the overall quality management system.
Meeting cGMP regulations with single-use technology
Implementing fully automated single-use technology in the manufacturing process can help companies to follow the regulations given by the FDA and thus improve their cGMP compliance. Manual processes are replaced by automated technologies and thus fulfill important factors for GMP such as reproducibility, standardization and reduced risk.
Furthermore, a single-use system promises safe storing and transporting during laboratory testing, automated documentation processes and effective and reliable staff processes - everything in line with the CFR Title 21.
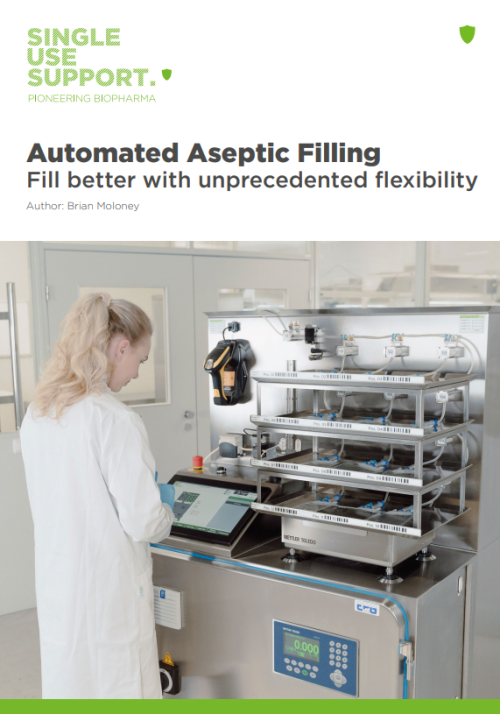
Download Whitepaper
Whitepaper: Automated Aseptic Filling
Read our Whitepaper about Automated Aseptic Filling in Pharmaceutical Manufacturing | Discover why automatic filling solutions are preferable to manual filling.
cGMP compliance implementation: What it takes
In order to adhere with cGMP compliance, the FDA requires drug manufacturers to meet various standards. The regulations are set out in 21 CFR (Code of federal regulations) and are flexible in their implementation. Companies can decide for themselves how to best apply the different processing methods and testing procedures.
cGMP requirements are:
- Buildings and facilities in good condition
- Regularly maintained and calibrated equipment
- Qualified and well-trained staff
- Reliable and reproducible processes
- cGMP certification
Manufacturers can implement the listed requirements by:
- Developing a strong quality management system
- Procurement of raw materials of appropriate quality
- Establishing robust operating procedures
- Identifying and investing deviations in product quality
- Maintaining reliable testing laboratories
Documentation of batch production records and manufacturing processes
One reason why manufacturers often fail to comply with cGMP regulations is an inadequate master manufacturing record and batch record. However, these are crucial for pharmaceutical manufacturing sites as they keep records about the production performance and the quality of a product. According to 21 CFR 11, both records must be stored electronically over a predetermined time. Automated systems can help to streamline such processes by taking over this documentation.
Automated single-use platform systems conduct data such as audit trails, batch reports, performance data, etc. electronically, save it, and communicate with each other, meaning that data is forwarded to the next platform it goes through.
They replace manual documentation and thereby require fewer staff, reduce mistakes to a minimum, and are more time efficient. GMP are interrelated with Good Documentation Practices (GDP), which offer directives for the creation and compilation of all types of documents necessary to satisfy GMP and other regulatory requirements. This guarantees the dependability, authenticity, and accuracy of data obtained throughout the research, development, manufacturing, and testing of drugs and medical devices.
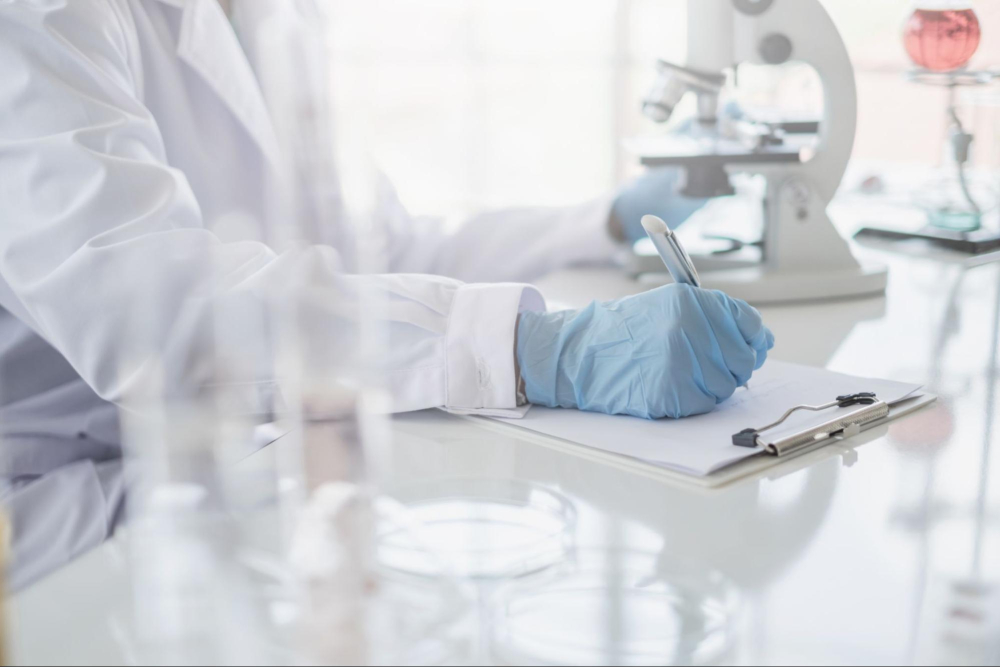
Staff performance & SOPs
To adhere with the cGMP regulations, company employees must follow Standard Operating Procedures (SOP) and be constantly informed of their changes.
This requires experience and appropriate staff training. Automated single-use solutions help to standardize and simplify these processes. Single-use technology increases the scalability and efficiency of manufacturing and also the security for the personnel, where safe handling of bulk drug substance is key.
Fully automated systems also decrease human errors, which can be dangerous and contaminate the quality of the products. This is also one of the core fundamentals of the Good Automated Manufacturing Practice (GAMP), which are guidelines emphasizing that quality should be tested at every stage of the manufacturing process - from raw materials, facility and equipment, to staff training and hygiene. These guidelines offer a dependable framework for pharmaceutical companies to maintain GMP compliance and deliver top-notch products to their end customers.4
cGMP compliant fluid management solutions
An automated process solution during fluid management, incl. aspetic filling of drug substance, freezing and packaging, help optimize the manufacturing process and comply to cGMP. Thanks to their automated, standardized processes, single-use technologies provide high efficiency, unrestricted scalability and flexibility.
The safe and controlled processes ensure that the drug substances are of high quality and product losses as well as contamination are minimized. And above all, the possibility of storing data electronically, makes single-use technologies compliant with the 21CFR11.
cGMP compliant process for filling
cGMP compliant process for freezing
GMP Annex 1 regulations and single-use technologies
GMP Annex 1 is a regulatory guideline that focuses on manufacturing sterile medicinal products. It addresses aseptic processing and contamination control to ensure product safety and quality. One effective solution to meet Annex 1 requirements is the implementation of single-use technology. By utilizing single-use assemblies, companies can enhance sterility and integrity while minimizing the risk of cross-contamination. Single-use technology offers advantages such as reduced cleaning validation, faster changeovers, and improved operational flexibility. It aligns with the principles of Annex 1 by providing a closed system approach for fluid management, promoting product safety, and simplifying compliance with regulatory guidelines.
Conclusion: What is necessary for cGMP compliant manufacturing?
As single-use systems are constantly improving, there are now more compelling reasons for manufacturers to adopt this technology. Striking arguments are time efficiency in terms of the reduced setup time for the processes as well as the ease of scalability. Moreover, single-use technologies are also proven to be more sustainable compared to traditional stainless steel equipment, as they take less time to clean and decrease the risk of contamination and product loss.
Single Use Support does not only offer individual products, but also provides complete end-to-end processes that can be customized to meet the specific needs of each manufacturer. Automated processes are a safe option for companies aiming to not only comply with GMP, but the most current version of it. They are reproducible and standardized, and thus help to minimize human error and enable the processing of substantial quantities of drug substances within a few hours.
Read more about cGMP regulations
- Current Good Manufacturing Practice (CGMP) Regulations, https://www.fda.gov/drugs/pharmaceutical-quality-resources/current-good-manufacturing-practice-cgmp-regulations, Published 01.03.2023
- Facts About the Current Good Manufacturing Practices (CGMPs), https://www.fda.gov/drugs/pharmaceutical-quality-resources/facts-about-current-good-manufacturing-practices-cgmps, Published 01.03.2023
- The impact of cGMP compliance on consumer confidence in dietary supplement products, https://www.sciencedirect.com/science/article/abs/pii/S0300483X06000345?via%3Dihub, Published 01.03.2023
- Adherence to the Current Good Manufacturing Practice (CGMP) Regulations in the 21st Century, https://stap1701en.previ3w.com/PDF/cphi_annual_rep_2016_v6_lo_res.pdf#page=4, Published 01.03.2023