Seed train intensification - the next big step in biopharma?
Table of contents
ShowSeed train intensification is an approach in upstream bioprocessing that is gaining more and more attention. With the growing demand for new drugs, manufacturers have to ensure both efficient and flexible production processes. While generally applicable standards must always be adhered to within the seed train, labs and plants are expected to operate as cost-effectively as possible in all phases of process intensification, process development and production.
Processes for seed train intensification by Single Use Support are increasingly of interest. They help manufacturers accelerate their traditional process of cell cultivation to shorten production times, enhanced flexibility and most importantly, to maximize CHO cell viability.
In this article, we will take a closer look at the conventional seed train and how seed train intensification can be achieved.
Improving the seed train for CHO cell culture – cornerstone of upstream intensification
Typically, mammalian cell lines, like CHO cells, are used for intensified production processes of monoclonal antibodies. During cell expansion infrastructures and production processes are changing along with the varying volumes.
Seed train intensification is an agile production process. It allows labs and manufacturers to grow an adequate number of cell lines for the inoculation of production bioreactors. High density cells can be aliquoted from the seed train into single-use bioprocess containers and cryopreserved. These frozen bag intermediates function as working cell banks to further boost productivity in upstream bioprocessing.
Seed train as part of upstream bioprocessing
The conventional cell culture process is an integral part in the production of several biopharmaceuticals, as it involves the production of significant amounts of biomass to produce various proteins, such as immunoglobine G (IgG) or other antibody drug products. The different steps of the workflow are currently performed with open and manual handling. Cell culturing in flasks have to be carried with great attention to not expose cells to contamination.
Traditional seed train process from cryovial to production bioreactor
The traditional seed train procedure begins with the thawing of mammalian cells that have been cultivated as the master cell bank. Fed batch size at this point is around 1mL which is cryopreserved in a cryovial or epipen. As part of the upstream bioprocess, these cells will then be fed to reach a level that is sufficient for the inoculation of a bioreactor.1
Once the number of cells for the working cell bank has been reached, they are cultivated throughout multiple steps in shake flasks, rocking motion bioreactors and stirred tank bioreactors with the required titer and viable cell density, until they have reached volumes up to 2,000 liters in a single-use bioreactor and up to 15,000 liters in a stainless steel bioreactor.2
As the traditional procedure of the production process is laid out for large-scale production in larger bioreactors, it is very time-consuming to reach a sufficient cell growth. Further, this manufacturing process requires the handling of cell cultures in the open during transfers, which leads to a higher risk of contamination and causes issues with reproducibility. Open processing and open handling of cells represents an increased likelihood of cross-contamination in multi-product facilities and thereby elevates the risk of product loss.1 2 3
Tools required for the seed train
The following list contains the cultivation systems as part of the conventional seed train process in biomanufacturing in the order they are used, starting with the smallest equipment for cell culture processes and gradually moving towards larger bioprocessing devices.
Tools required for the traditional seed train include:
- Cryovials or Epipen used as master cell bank
- Inoculation flasks
- Spinner flasks
- Wave rocker or wave bioreactor
- N-3-bioreactor
- N-2-bioreactor
- N-1-bioreactor
- N-bioreactor (=Production bioreactor)
Why seed train intensification helps save time and costs
With process intensification as strategy to make upstream bioprocessing more efficient, it's main focus is to maintain or improve cell viability after freezing and thawing and establish more automated, enclosed solutions that make sure that no contamination occurs during the whole process.
Seed train intensification based on modern technologies applying High Cell Density Cryopreservation (HCDC) is both time-saving and cost-effective compared to conventional alternatives, like fed batch production processes.
Single-use systems enable fluid transfer of cells in aseptically closed systems not only during upstream processes overall, but also during seed train intensification. Single use technologies as part of seed train intensification provides more process flexibility and scalability. In other words, seed train intensification based on disposable single-use components allows manufacturers to speed up reproducible cell culture growth, regardless of cell bank densities or volumes of high-density cell banks.
While the traditional approach involves the linear cell cultivation from master cell banks to production bioreactors, process intensification processes help make cell expansion more efficient with the inocluation of intermediates working cell banks. In other words: Instead of constantly having to start the entire process from scratch, labs and manufacturers can simply fall back on already cultivated cells as intermediates.
How can a seed train be intensified?
To start protein production in biomanufacturing with animal cells like Chinese Hamster Ovary cells (CHO cells) in an optimized way, there are different strategies available to opt the cell lines for scale-up at faster rates.
One strategy to achieve high cell density and viability is the attachment of a cell retention device to the N-1-bioreactor.4 One of such a device to achieve higher cell density is Repligen's XCell® ATF, based on alternating tangential flow technology5. Through this method, it becomes possible to use a smaller bioreactor due to the higher initial cell density in the suspension cell culture and seed the production reactor. Theoretically, this step can also be performed in the earlier N-2-bioreactor stage of the work flow, saving considerable amounts of time in the production process.
Another strategy for seed train intensification is the cryopreservation of a working cell bank with a high cell density in single-use bags. High cell density cryopreservation removes the need for traditional seed train expansion.4 5
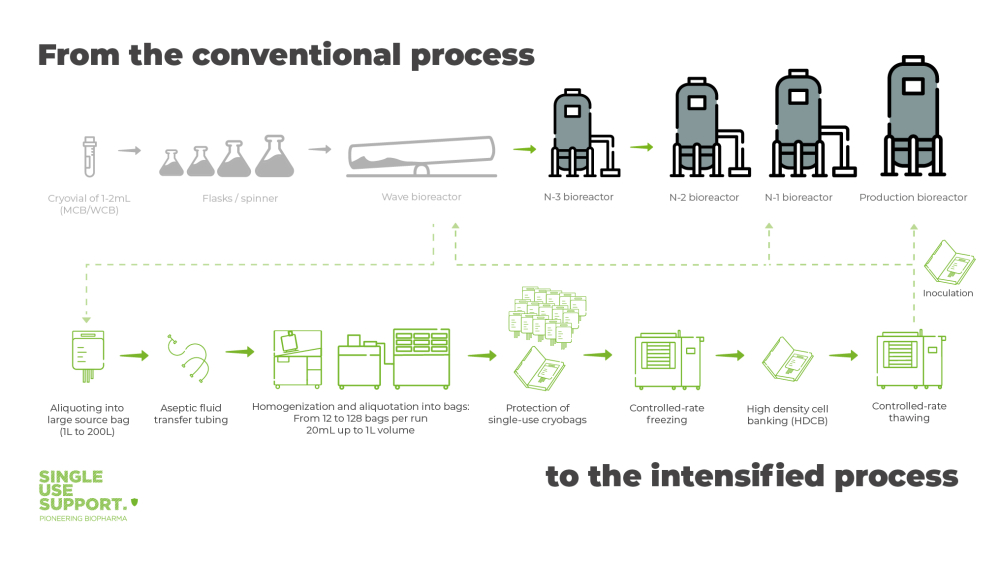
Seed train intensified with high-density cell banks
Banking high-density CHO cells (HDCB) is the essence of seed train intensification. As speed and reproducibility are highly important factors in the production of biopharmaceuticals, the development of a working cell bank (WCB) that can be used for the production of large product quantities is essential. When a small number of cells has been extracted from the master cell bank (MCB), these cells are cultured in large aliquots with cell suspensions. Aliquoted into single-use bags that range from 20mL up to 1L, they are frozen to cryogenic temperatures.
What is high cell density cryopreservation?
In high cell density cryopreservation (HCDC), intermediates with a high cell density are aliquoted in single-use bags and then frozen at -80 °C, before they are transferred into liquid nitrogen in its vapor phase. Keeping cells at cryogenic temperatures and performing controlled freeze-thaw cycles help ensure process reproducibility with optimal cell viability after thawing. Both are crucial aspect in the production of biopharmaceuticals. Process development can start earlier, making the whole endeavor of cell culturing more cost- and time-efficient.
The working cell banks used for seed train intensification can differ in cell density and aliquot volume: High density cell banks can be for example 107 cells/mL filled into a 500mL single-use biocontainer that can then inoculate a 200L bioreactor. The cell density and volume being aliquoted and cryopreserved depends on production specifications of the manufacturer.
It is important to note that case studies have shown good results with cryopreservation with regards to growth and recovery rates of CHO cell lines, the current cell line of choice for the production of monoclonal antibodies used in pharma production. Another critical quality attribute is to maintain a viable cell density (VCD).
Seed train intensification with HCDC comes with several advantages, some of which are:
- Time efficiency: HCDC allows for faster cell growth and higher cell densities, reducing the overall time required for the seed train process. This results in shorter manufacturing timelines and quicker production of the final product.
- Cost-effectiveness: By achieving higher cell densities in a shorter time, HCDC can lead to reduced resource and facility usage, lowering production costs and increasing cost-effectiveness.
- Increased productivity: HCDC enables the production of a larger number of cells in a smaller footprint, maximizing the productivity of bioreactors and improving the overall yield of the biopharmaceutical manufacturing process.
- Consistency: The use of HCDC in seed train intensification helps maintain the consistency of the cell culture and VCD and reduces variability between batches, resulting in more reliable and predictable production outcomes.
- Scalability: HCDC is easily scalable, allowing biopharmaceutical companies to efficiently transition from small-scale seed train operations to large-scale production without significant changes to the process.
- Process optimization: HCDC facilitates better process optimization by providing a controlled and reproducible environment, leading to improved product quality and performance.
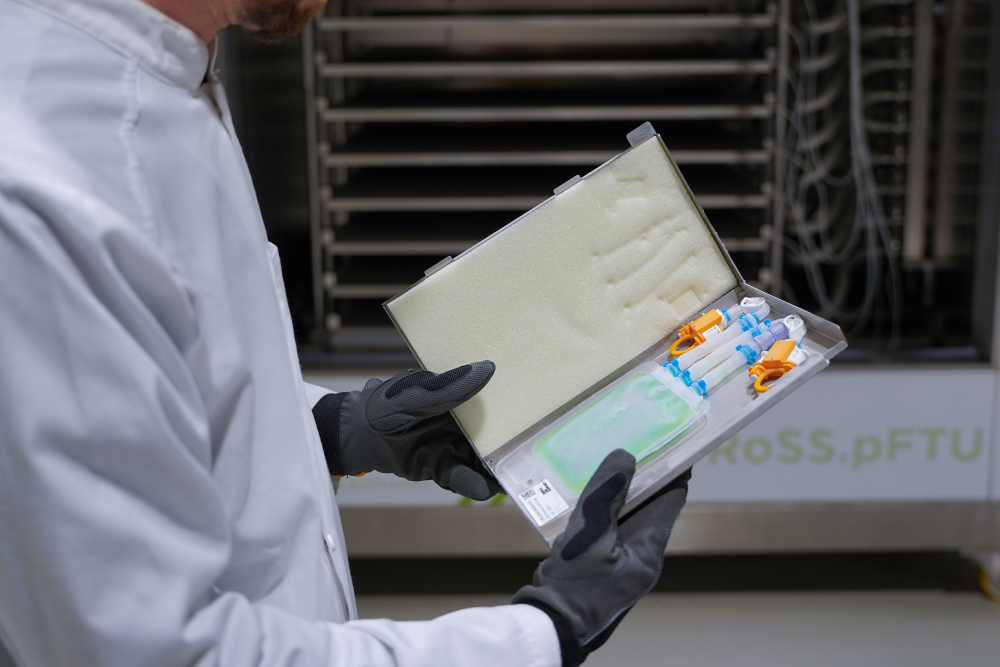
Fed-batch or perfusion seed train?
Two different approaches to intensify the seed train process are fed-batch or perfusion:
- Fed-batch includes the addition of nutrients to cell cultivation without medium removal. It is therfore considered simpler and its implementation is less expensive. Fed-batch may have limitations in achieving best conditions for longer periods.
- Perfusion adds medium continuously while removing waste products. It thereby reaches higher cell densities and productivity. However it also requires more complex devices and control systems.
Manufacturers choose between fed-batch and perfusion processes based on specific performance criteria, typcially the desired cell density, product quality requirements, process complexity, and scalability or flexibility needs .
Equipment in seed train intensification with HCDC
Seed train intensification requires innovative tools and up-to-date technologies for fluid and cold chain management to optimize the time and cost aspects of a project. This does not only mean that time efficiency has to be increased, but also that scalability needs to be taken into account, given that different life science projects require different product quantities.
Before cells are aliquoted into single-use bags as primary packaging, it must be ensured to have a consistent cell count from bag-to-bag. Homogenizing devices, like RoSS.PADL, ensure an even distribution of the high cell density solution while simultaneously cooling it down. The latter functionality fosters cell viability by extending the time before freezing when cryoprotectants, such as DMSO, are already added.
In contrast to traditional seed trains, where the aliquoting and transferring of cells is often carried out manually, exposing the cells to contamination, fully automated aliquoting solutions like RoSS.FILL erase this problem – product loss due to human errors can be reduced to a minimum.
Controlled rate freezing, best achieved with RoSS.LN2F a cryogenic liquid-nitrogen freezer or RoSS.pFTU a plate-based freeze-thaw platform, optimizes high cell viability of cells during cryopreservation. This way cells can be frozen down to -170 °C for storage.
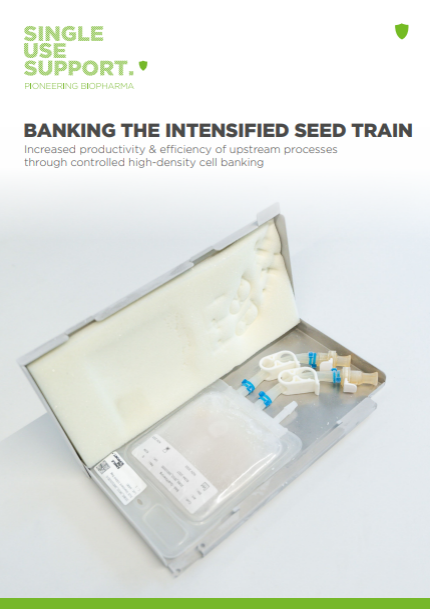
Download Whitepaper
Banking the intensified seed train
Bring cell culturing to the next level! Find out how seed train intensification can improve time efficiency and lower costs in cell culturing applications.
Seed train intensification with Single Use Support
As the cultivation of cells is an integral part in the production of many pharmaceutical products and applications, there is a high demand for process solutions that facilitate a more time- and cost-efficient manufacturing process in the early process stages of manufacturing. This is best achieved with fully automated solutions securing an aseptically closed system that reduces the risk of contamination during different production steps where cells have to be transferred from one device to another.
Solutions from Single-Use Support address these problems with single-use technologies and consumables that enable the cultivation cells as well as their preparation for the logistics process. Cells can be filled into single-use bags in an automated filling process before being frozen for sterile cell retention. Following compliance with cGMP and 21 CFR part 11, the freeze-thaw process is fully automated, ensuring sterility while simplifying all process steps.
Single Use Support'solutions are not only scalable and highly automated, but can also be configured to meet specific manufacturing needs. The high level of automation process steps and improved cell viability promotes process efficiency and also contributes to greater patient safety.
FAQs on seed train intensification
What is a seed train?
A seed train is a series of steps in biopharmaceutical manufacturing used to grow and expand cells for producing therapeutic proteins or biological products. It starts with a small cell culture and gradually increases in size to achieve large-scale production while maintaining quality and consistency.
What is seed train expansion?
Seed train expansion is a biopharmaceutical manufacturing process that involves sequentially increasing the volume and number of cells from an initial small culture (seed) to achieve larger cell populations suitable for large-scale production of therapeutic proteins or biological products.
Why is high cell density important?
High cell density cryopreservation, which is the meaning of HCDC, offers many opportunities to make the conventional cell expansion process in upstream bioprocessing more efficient. Small volumes of CHO cell with high density can be used to inoculate larger bioreactors to intensify the seed train process in this regard.
What is the difference between a seed train bioreactor and a production bioreactor?
A seed train bioreactor is used for early-stage cell culture expansion, while a production bioreactor produces the final product at a larger scale later on.
- Seed train optimization for suspension cell culture, http://dx.doi.org/10.1186/1753-6561-7-S6-P9, Published 2013-12-04
- Model-based strategy for cell culture seed train layout verified at lab scale, http://dx.doi.org/10.1007/s10616-015-9858-9, Published 2015-03-20
- Seed Train Optimization for Cell Culture, http://dx.doi.org/10.1007/978-1-62703-733-4_22, Published 2013-12-02
- “Jumping Seed Train Intensification Hurdles to Maximize Yield,” BioPharm International 34, https://www.biopharminternational.com/view/jumping-seed-train-intensification-hurdles-to-maximize-yield, Published 2021
- XCell® ATF Devices and Controllers. Repligen, https://www.repligen.com/products/upstream-filtration/xcell-atf/xcell-atf-devices-and-controllers, Published