Freezing drug substance – taking control over large volume pharmaceutical freezing
Table of contents
ShowDuring the manufacturing process, delivery, or long term storage, freezing drug substance is a necessary step to ensure product quality. However, various process parameters in freezing/thawing methods are related to overall product quality. One of the most common process parameters is controlled freeze and thaw rate. Also the choice of drug substance container does have an impact on the freezing result. Finally, cost and time reduction in process chains have to be considered for efficient drug substance management.
Freezing bulk drug substances – why take the effort?
While freezing drug substances or active pharmaceutical ingredients does not only help to ensure product quality and enable safe transport without product damage for biotech companies, there are also legal regulations which have to be taken into account to guarantee safe handling of bulk drug substances.
Freezing allows for storage of large volumes of biopharmaceuticals until demand arises. At the same time, cryopreservation reduces the risk for structural changes and mechanical damage of protein or cells during transportation. When freeze thaw logistics is outsourced to CDMOs – due to cost-reduction and more streamlined processes – such production steps are necessary.
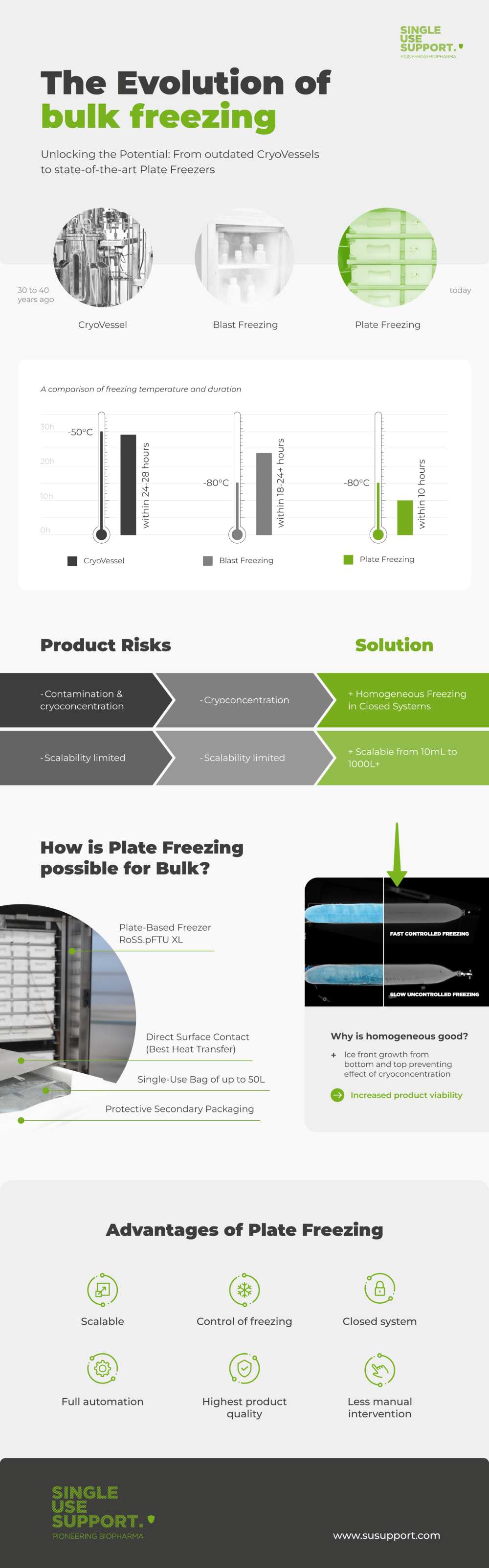
Main considerations along the freezing process of large volume drug substances
In order to guarantee product stability and prevent protein denaturation, several aspects have to be considered in process development – including the impact of freeze and thaw rates. The speed at which freezing is performed can have a big impact on a drug substance’s efficacy. Fast freezing rates has been shown to result in lower levels of crystallization and higher protein stability in protein formulations. Further, the goal of an efficient freeze and thaw technology is to prevent alterations in the drug substance through the minimization of protein aggregation.1 2
Facing challenges with conventional freezers
The traditional method for freezing bulk biopharmaceuticals is to use static or blast freezers. However, compared to plate-freezers, they show comparatively slow and inflexible freezing rates. Through an inefficient heat transfer, slow freezing can lead to a low external area compared to volume, which can cause damage in complex proteins and alter protein stability. Protein denaturation can potentially impact product quality attributes: Slower freezing can lead to greater cryoconcentration which results in higher zones of protein and excipient concentrations in the center bottom area.
Read more: Cold storage requirements of APIs
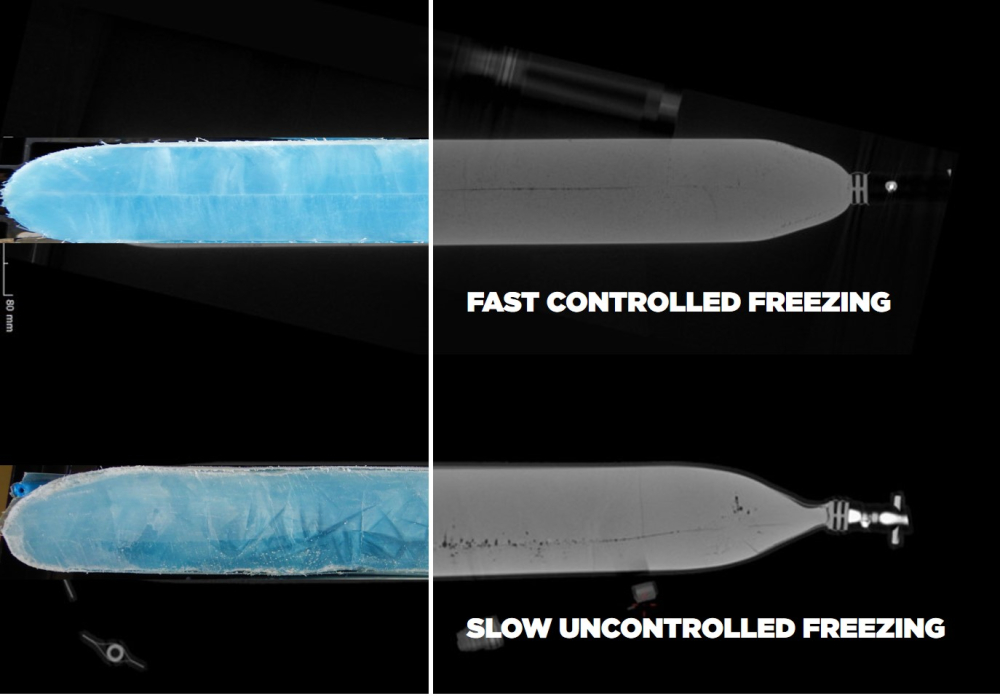
With plate-based controlled freeze and thaw platform concepts, it is possible to maintain the homogeneity of a drug product, facilitating optimal freezing results for drug substances. Especially for products in larger primary packagings like vaccines, monoclonal antibodies (mAbs) and viral vectors, homogeneity is of utter importance.
Read more: Advanced cold chain solutions for the development of vaccines
What bioprocess containers to choose
When choosing bioprocess containers for frozen storage, stainless steel vessels or bottles have long been the traditional choice. Even though their use is well-established, they tend to take up too much space in storage, their freeze/thaw process is harder to control and they can lead to process inflexibility.
In comparison, freeze-thaw single-use bags can minimize cryoconcentration by fast freezing and thawing of all scales, up to large volumes of pharmaceuticals. Furthermore, single-use bags take up less space and come already fully assembled and sterilized, meaning they are ready to use.
Minimizing risks – maximizing resource and cost efficiency
The process of drug product manufacturing as well as transporting biopharmaceuticals in a frozen state has a high potential for product loss due to contamination and human or mechanical error. While product and staff safety is one of the main challenges for the biopharmaceutical industry, minimizing costs is an important goal for companies to stay economically competitive – especially during the transition from scale-down models to large-scale production. Single Use Support provides a combined solution to all these challenges through automated filling, freezing, thawing and filtration processes.
Freezing bulk drug substances with single-use technologies
Handling sensitive substances like active pharmaceutical ingredients is an everyday task in biopharma and biotechnology. Single Use Support has developed automated end-to-end solutions for aseptic fluid management as well as solutions for plate-based controlled freeze and thaw cycles of drug substances. While these systems are compatible with other brands, additional products have been developed to provide a streamlined process from start to finish.
Its RoSS Shell, for instance, is designed to ensure robustness and protection of frozen drug substances in single-use bags that can be filled with a minimized risk of product loss by Single Use Support’s aseptic filling systems.
Part of the character of Single Use Support’s product line up, including its dedicated freeze-thaw platform, is its enormous scalability. This allows the products to be scaled to industrial large-scale batches – such as large-scale freezing – as well as for small-scale demands.
Sustainable Freezing of drug substances
Handling sensitive substances is an everyday task in biopharma and biotechnology. Single Use Support has developed automated end-to-end solutions for aseptic fluid management as well as solutions for plate-based controlled freeze and thaw cycles of drug substances. While these systems are compatible with other brands, additional products have been developed to provide a streamlined process from start to finish.
Its RoSS Shell, for instance, is designed to ensure robustness and protection of frozen drug substances in single-use bags that can be filled with a minimized risk of product loss by Single Use Support’s aseptic filling systems.
Part of the character of Single Use Support’s product line up, including its dedicated freeze-thaw platform, is its enormous scalability. This allows the products to be scaled to industrial large-scale batches – such as large-scale freezing – as well as for small-scale demands.
- Freeze–thaw characterization process to minimize aggregation and enable drug product manufacturing of protein based therapeutics, http://dx.doi.org/10.1038/s41598-021-90772-9, Published 2021-05-31
- Large-Scale Freezing of Biologics: Understanding Protein and Solute Concentration Changes in a Cryovessel—Part I, https://www.biopharminternational.com/view/large-scale-freezing-biologics-understanding-protein-and-solute-concentration-changes-cryovessel-par, Published 2010