Increasing Patient Safety: Risk assessment for small volume fluid management
Table of contents
ShowAdvanced cell and gene therapies, such as autologous therapies, exhibit certain specific requirements. The scale of such therapies is very different from what we typically see in conventional biopharmaceutical manufacturing processes in commercial facilities.
The volumes are much smaller than usual. The pharmaceutical liquids require special handling and care as they must be shipped in a sterile and protective packaging. Both logistics and cGMP compliance are an important part of the manufacturing process of these therapies. However, fluid and cold chain management still pose certain challenges in this yet emerging field of novel medicines. One of the most overlooked aspects that cannot be handled with traditional methods is the aseptic filling process step.
According to experts, the process of filling autologous cell therapies presents several challenges1 like producing a single batch for each patient, which redefines the term “small batch filling”. The filling process on such a level is comparable with clinical phase-1 studies or even pre-clinical trials. Small batch filling is applicable to many areas in bioprocessing as well, such as cell banking, viral vector production and more.
Although established processes can address some of these challenges. As autologous therapies are becoming more commercialized, it is important to develop best practices for automated filling.
Single-use technology to improve the filling process of autologous therapies
Sticking to the example of autologous therapies, in most cases cells are collected from the patient and filled into a primary packaging, such as single-use bags or vials for further processing.
Along with experts recommendations to use "a closed and pump-driven system that constantly checks the bags’ weight" during the filling process, manual processes often fail to maintain consistency and accuracy of performing a standardized aliquotation into single-use bags. Moreover, the open architecture of manual filling procedures bear increased risk of contamination, whereas a closed automated system prevents such occurences.
Single Use Support has established a fully automated and fully scalable filling and draining system for single-use bags of various sizes and of all established manufacturers. The system ensures highest filling accuracy thanks to different technologies, gravimetric and flowmeter. Depending on the filling volume this can be down to few mL.
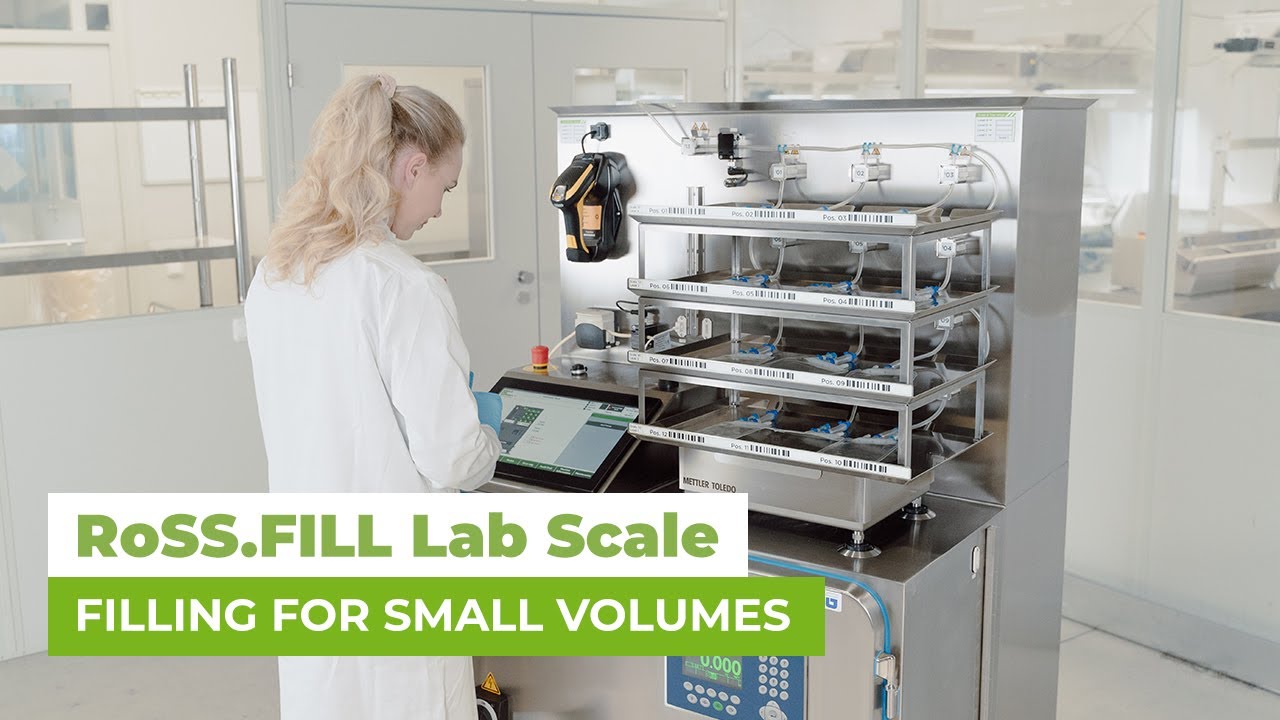
Protecting ATMP in small single-use bags
The filled bags are advised to be protected in a robust secondary packaging to prevent leakages during freezing, storage and shipping processes, such as Single Use Support’s RoSS.KSET, the small version of the RoSS shell. 1
The RoSS® shell and RoSS.KSET are protective shells for 2D single-use bags that prevents product loss through breakages to <0.001%. The secondary packaging is vendor-agnostic which means that all types of bags from multiple vendors can be accommodated safely.
It is suitable for small volumes in clinical studies, clinical trials, but also for commercial production of viral vectors, plasmid DNA, autologous cell therapies and more.
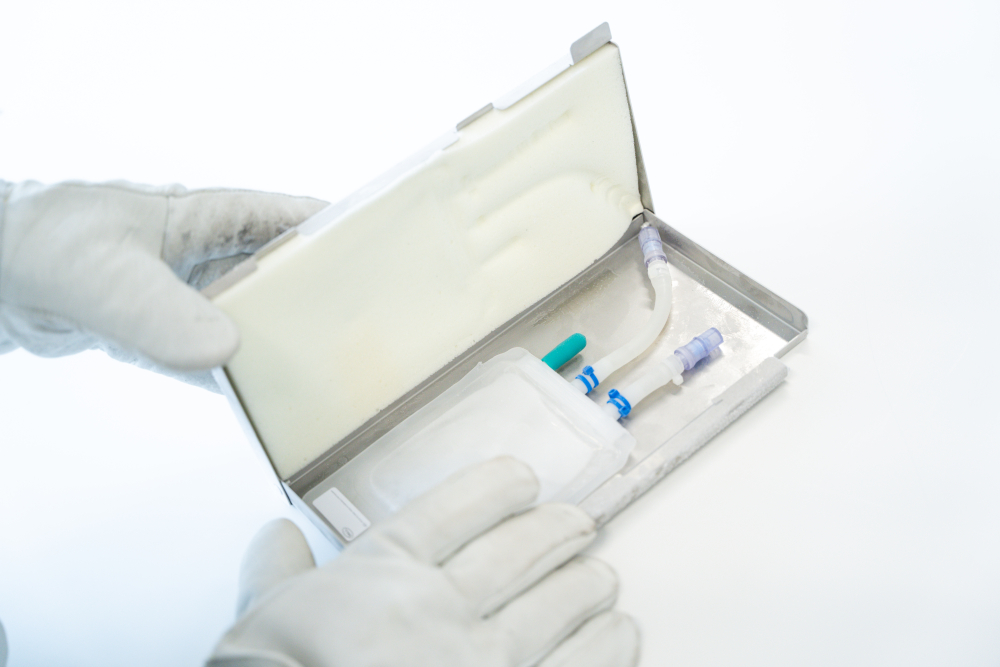
The 3D foam inside the shell offers optimum bag protection against external forces. The frame is made of high-quality plastic and stainless-steel that withstands extremely cold temperatures. Its design even enables to advance the freezing process with plate-based freezers to ensure advanced methods to cool the valuable liquids to -80°C and less.
Patient safety thanks to bag protection and closed systems
RoSS.KSET boasts an innovative and intuitive locking mechanism, allowing for full tamper-evident single-use bag protection This is a non-negotiable requirement for autologous therapies such as the CAR-T cell therapy. If the liquids are not protected and are damaged in transit, the vital therapy is rendered useless.
Volumes for traditional therapies consist of several hundred bags, whereas autologous therapies may only require a handful of containers. But scale-up can be earlier than expected and the transfer from clinical to commercial production must be prepared. Planning automation and scalable technologies help immensely to ramp up production once it is needed. It also supports the process consistency throughout different scales. When handling of small volumes is already automated in an early stage, it is a way more straightforward path to commercialization of the drug product.
The benefit of a closed systems with automated solutions add value by offering a higher degree of sterility, safety, and process flexibility. Therefore, the risk of contamination is minimized which in turn enables efficiency and product viability during manufacturing.
1. Bozenhardt H.F., Bozenhardt, E.H., 2019: Overcoming The Unique Filling Challenges Of Autologous Therapies. Available at: bioprocessonline.com