Solutions for mAb development and manufacturing
Table of contents
ShowThe development and manufacturing of monoclonal antibodies represent fundamental processes in the production of several biologics, and require dedicated solutions to be carried out. As it is a highly complex procedure where much can go wrong, laboratories as well as biopharma companies seek improvements in order to guarantee top-notch antibody products. After all, with applications such as therapies for conditions like cancer and infectious diseases, mAbs have become integral to modern medicine.
In this article, we will walk you through various solutions from Single Use Support’s product portfolio and explain how they can become key elements in the mAb production process.
Critical aspects in mAb production
mAb production is a multifaceted biotechnological approach, with several critical aspects to it. One of them revolves around safe and aseptic filling of monoclonal antibodies, requiring meticulous precision for consistent aliquotation. Furthermore, human error is to be avoided, which can lead to contamination and product loss. This makes it crucial to maintain an aseptic environment that, in addition to avoiding impurities, focuses on efficiency and precision in the fluid transfer of often highly viscous mAb solutions.1 2
Introducing suitable freezing technologies adds further complexities, requiring precise and controlled freezing rates. This is crucial to preserve the structural integrity of mAbs, preventing potential degradation during the cooling of monoclonal antibodies.
Meanwhile, storage and transport solutions grapple with the dual challenges of maintaining temperature-controlled conditions while being as space-efficient as possible. However, these solutions must not compromise in scalability of mAb production, either, as this is another critical consideration to be made. From the initial research and development phase to the market roll-out of a biopharmaceutical – the transition between the various scales must be smooth and cost-effective.1 2
First things first – primary packaging
Monoclonal antibody products are transported using primary packaging throughout their supply chain. The selection of primary packaging can have a considerable impact on their quality and safety, which is why they demand special attention. IRIS Single-Use bioprocess containers have been developed for this very purpose: These containers with ultra-low extractables & leachable profile are operational across a temperature range from -196°C to +50°C and play a pivotal role in maintaining the integrity of cell culture media, mAbs, and other sensitive drug substances. With a smart material composition of PE and EVOH, the IRIS 2D bag strikes a balance between robustness and flexibility, safeguarding liquids during storage, transport, and freezing processes.
IRIS single-use bioprocess containers come in various sizes and offer a versatile solution for various applications, from cell and gene therapies to bulk drug substance production. IRIS containers emerge as robust protection, ensuring the safe freezing, transport, and storage of monoclonal antibodies.
On second thought – secondary packaging is just as important
Considering the natural expansion of liquids and the significant stress that packaging solutions undergo during freezing shipping and storage, the use of secondary packagings is paramount. The RoSS® Shell by Single Use Support stands as a powerful solution in minimizing product losses and ensuring integrity of single-use bags during and beyond the mAb production process.
With a track record of 300,000 shells sold worldwide and product loss below 0.001%, it offers robust protection for single-use bags across various manufacturers and volumes. As a cornerstone in the mAb manufacturing process, the RoSS® Shell plays a vital role in optimizing efficiency and reliability in secondary packaging operations.
Aseptic fluid management of mAb products
After discussing different packaging options for monoclonal antibodies, the question arises: how should they be filled into these containers? This is where aseptic filling machines come into play, with the RoSS.FILL fluid management platform taking center stage.
RoSS.FILL is a groundbreaking system revolutionizing aseptic filling and filtration processes. Being fully automated, it provides standardization in aseptic aliquotation. And with its modular design, it ensures scalability from small-volume laboratory applications to large-scale bulk production.
This innovative platform by Single Use Support offers unmatched flexibility, accommodating diverse filling volumes and achieving remarkable speeds of up to 300 liters per hour while not compromising in precision. That allows RoSS.FILL to set new standards in the aseptic filling of mAbs, enhancing productivity while maintaining stringent quality standards.
Freezing solutions for monoclonal antibodies
Once mAbs are thoroughly transferred into suitable single-use containers, freezing monoclonal antibodies is typically performed to protect them from deterioration during long-term storage. With a proven track record, Single Use Support's freeze-thaw platform RoSS.pFTU is used to improve the freezing process of monoclonal antibodies.
The fully automated system ensures precise control over the crucial freeze/thaw rate, ensuring the stability of mAb drug substances. Designed for compatibility with diverse batch sizes and bags from various manufacturers, RoSS.pFTU becomes a versatile solution in advancing the product viability in mAb manufacturing.
Whether for research and development, clinical trials, or large-scale commercial production – the freezers in the RoSS.pFTU platform address the specific needs of mAb production. The lab-scale benchtop version is tailored for early-phase studies, while the mid-scale and large-scale units offer expanded capacity while maintaining efficiency and safety of mAb manufacturing.
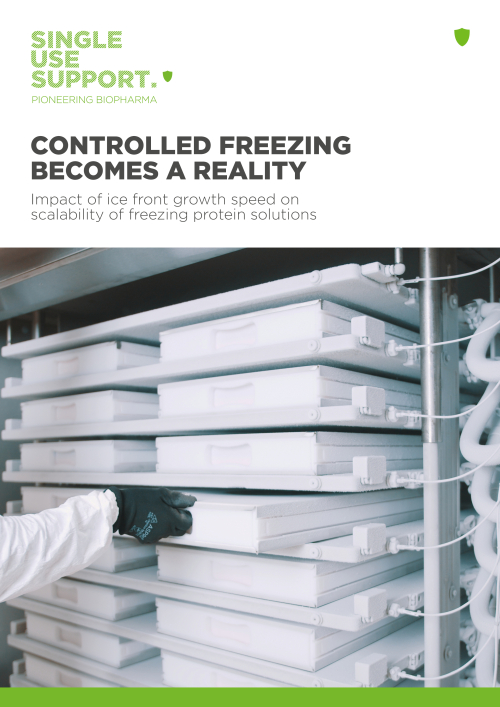
Recommended Download
Whitepaper: How Controlled & Scalable Freezing Becomes Reality
Storing and shipping mAbs with Single Use Support
RoSS.ULTF, an ultra-cold storage freezer, is an ideal partner in frozen drug substance preservation, with its capability to maintain temperatures down to -75°C. This upright freezer integrates seamlessly with RoSS® shells, ensuring optimum storage density and flexibility in handling bioprocess containers.
The modular design allows easy loading, accommodating up to 300L of drug substance in 2D single-use bags and even more in more bulky primary packagings. With GMP-compliant alarm management and compatibility with RoSS single-use technologies, RoSS.ULTF represents an efficient, fully movable, reliable, and customizable solution for monoclonal antibody storage.
RoSS.SHIP, on the other hand, is Single Use Support's cutting-edge transport solution. Engineered for international shipping of several days, RoSS.SHIP ensures the secure and reliable transportation of mAb products with dry ice. This transport system supports various primary packaging types and is an additional puzzle piece in the bigger picture of mAb manufacturing solutions provided by Single Use Support.
Recommended articles
- Aseptic Vial Filling, http://dx.doi.org/10.1385/1-59259-076-4:313, Published 2003-11-15
- Ongoing Challenges to Develop High Concentration Monoclonal Antibody-based Formulations for Subcutaneous Administration: Quo Vadis?, https://jpharmsci.org/article/S0022-3549(21)00614-6/pdf, Published 2021