Bubble point test: Purpose & Procedure
Table of contents
ShowEnsuring the integrity of filtration processes is fundamental for the safety of bioprocessing. Among the array of methods available for assessing filter integrity, the bubble point test emerges as one of the most frequently used techniques. By scrutinizing the behavior of filters under specific conditions, this test provides insights into their efficacy and integrity, aiding in the identification of potential flaws and ensuring compliance with Annex 1 and other, stringent GMP standards.
Along the following lines, we will take a closer look at the bubble point test, including its purpose and the way it is performed. Also, we will present alternatives and possibilities to integrate filter integrity tests directly into end-to-end fluid paths.
What is the bubble point test?
The bubble point test is a method used to evaluate the integrity of sterilizing grade filters in pharmaceutical manufacturing. It determines the pore diameter by observing the first bubble formation in a controlled testing setup. By applying air pressure to the filter, the point at which the first bubble appears indicates the minimum pressure required to push air through the largest pore.
This test ensures that filters maintain their specified pore size, essential for maintaining product quality and safety in pharmaceutical processes, and is also described by the ASTM (American Society for Testing and Materials).
What the bubble point test is used for
The bubble point test is crucial in the pharmaceutical industry for validating the integrity of sterilizing grade filters. It serves as a non-destructive test method to ensure that membrane filters maintain their specified pore size and effectively remove contaminants.
By conducting this test, pharmaceutical manufacturers can validate the reliability and effectiveness of their filtration processes, ensuring product quality and safety. Additionally, the bubble point test is applicable to various types of filters used in pharmaceutical manufacturing, such as disc filters or cartridge filters, providing a versatile tool for quality control.
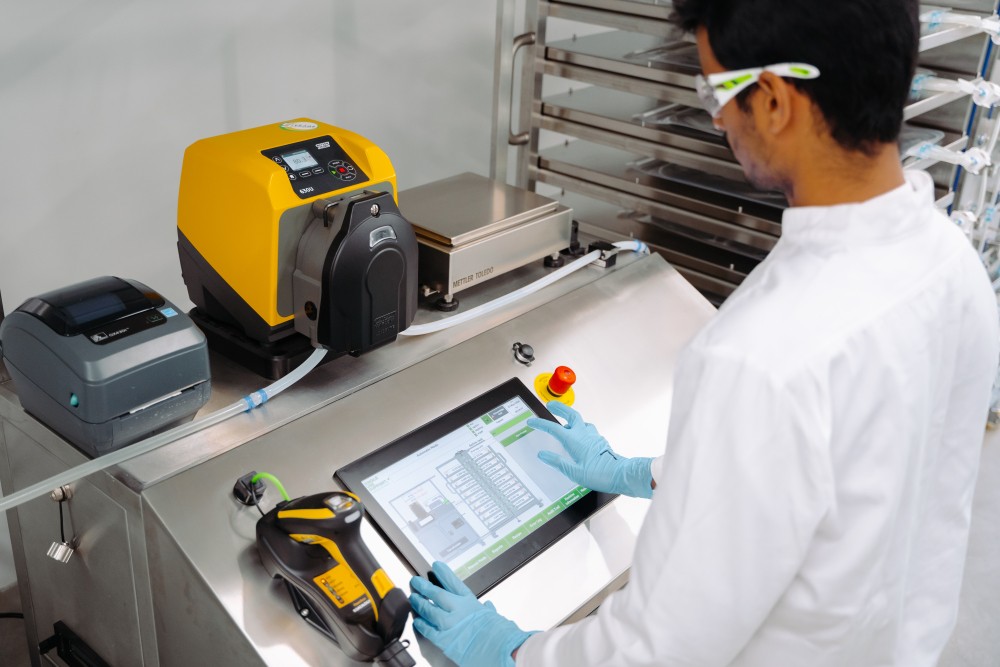
Filter integrity testing – when is it performed?
Filter integrity testing is mandatory in the sterile manufacturing of pharmaceutical products to ensure compliance with regulatory standards and to uphold product quality and safety.
Regulatory agencies such as the FDA and EMA mandate filter integrity testing to verify that sterilizing grade filters effectively remove contaminants and maintain their specified pore size. The revision of EU GMP Annex 1, for instance, includes PUPSIT (Pre-use Post Sterilization Integrity Testing) as a mandatory step in the production of sterile pharmaceutical products.1
Procedure: Performing the bubble point test in 5 steps
Performing the bubble point test follows a straightforward procedure, demanding both precision and thorough documentation. The process is framed by the following 5 steps:
- Preparation – Gather all necessary equipment, including a beaker, filter holder, gas pressure source, pressure regulator, pressure gauge, and a filter with known specifications. Ensure tight sealing of connections to prevent air leakage.
- Setup – Submerge the filter holder with the filter into a beaker filled with a wetting fluid like water. Connect the gas pressure source to the holder's inlet using tubing. Attach the pressure gauge to monitor pressure changes accurately.
- Initiate testing – Gradually increase gas pressure using a regulator, enabling airflow through the filter. Observe the filter's surface for the emergence of first bubbles.
- Bubble point detection – Continue increasing pressure until the bubble point pressure is reached, indicated by pores releasing trapped air. Monitor the pressure gauge closely to note the pressure required for a steady air flow.
- Completion – Record the results and calculate pore sizes using fluid properties and observed pressure. Depressurize the system after testing.
Source: Merck2
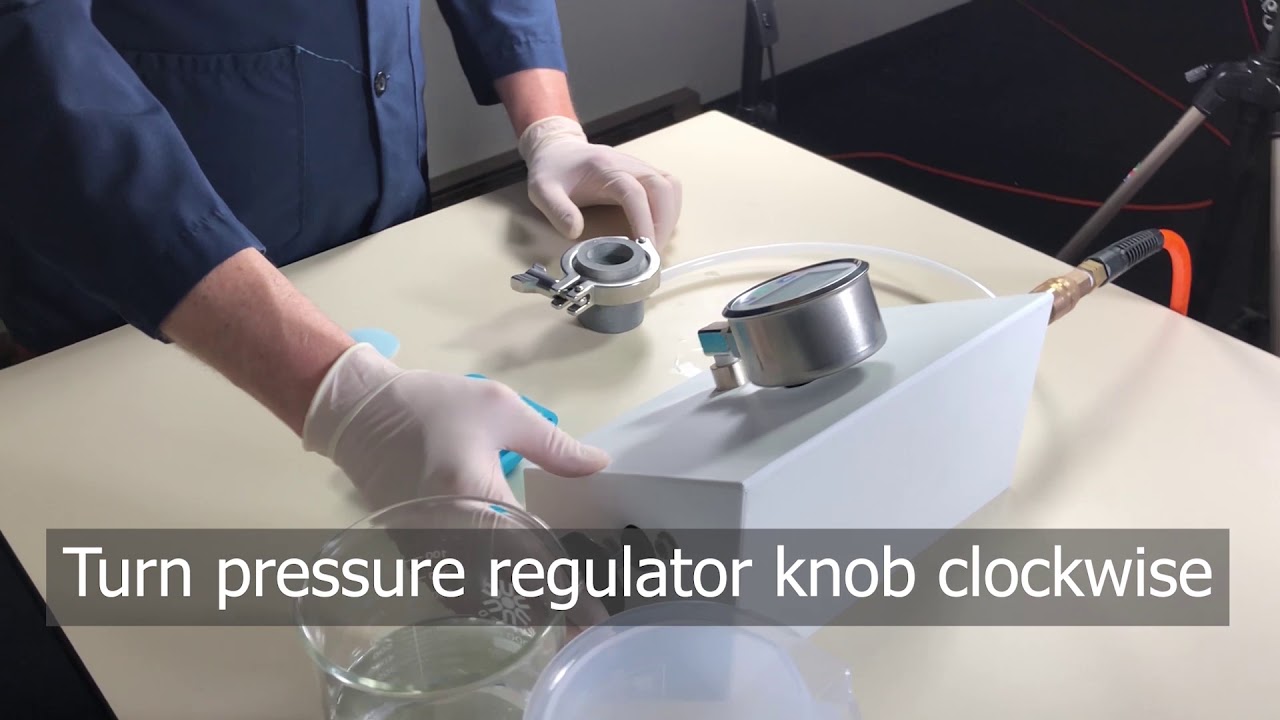
Video: Sterlitech Corporation
Advantages and limitations of the bubble point test
The bubble point test offers several advantages in assessing the integrity and performance of filters, particularly hydrophobic filters commonly used in pharmaceutical applications. One significant advantage is its ability to detect the largest pores in the filter matrix accurately. By observing the formation of a steady stream of bubbles at the bubble point pressure, the test provides a clear indication of the filter's pore size distribution and its ability to retain particles of specific sizes.
Moreover, the bubble point test procedure is relatively straightforward and can be performed quickly, making it a convenient method for routine quality control assessments. Additionally, it offers a non-destructive means of evaluating filter performance, allowing filters to be tested without compromising their structural integrity.
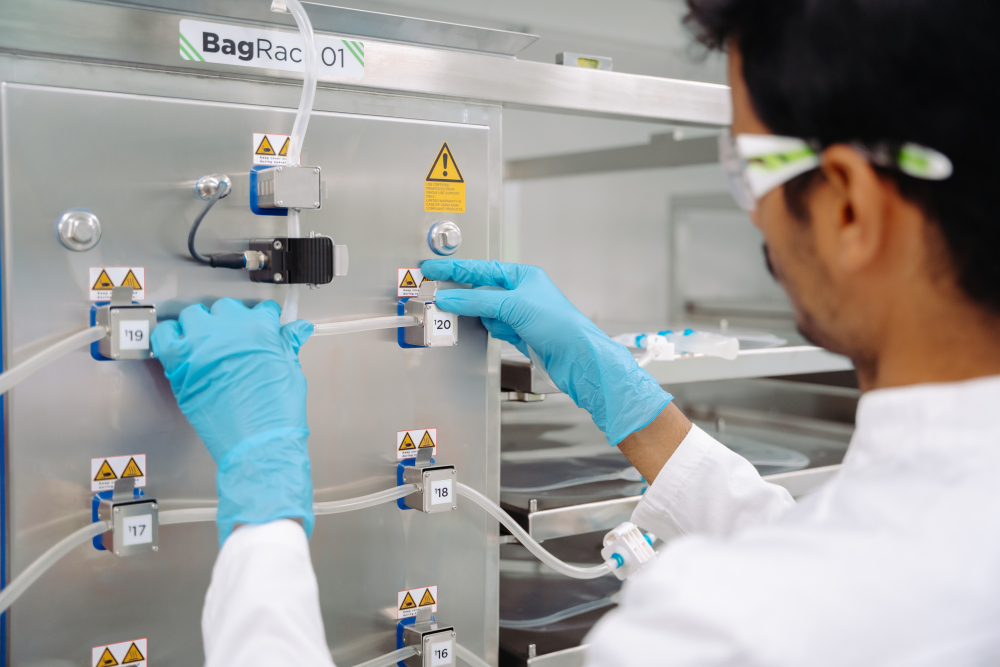
However, the bubble point test also has its limitations. For instance, variations in flow rate and the wetted membrane can influence the accuracy of the results, requiring careful standardization to ensure consistency.3
Alternative filter integrity test methods
The bubble point test is not the only way of determining the integrity of a pharmaceutical filter. Additional filter integrity testing methods include:
Water intrusion test
The water intrusion test involves applying water pressure to the filter membrane to detect any breaches or leaks. By subjecting the filter to increasing water pressure, this test evaluates its ability to withstand pressure without allowing water to penetrate through.
Pressure hold test
The pressure hold test evaluates the filter's integrity by subjecting it to a specified pressure and monitoring its ability to maintain pressure over time. This test helps detect any leaks or breaches in the filter membrane that may compromise its integrity.
Diffusion test
The diffusion test measures the rate at which a gas or liquid diffuses through the filter membrane. By assessing the filter's ability to retain particles or molecules, this test provides insight into its integrity.
Automating filter integrity testing with Single Use Support
Integrating filter integrity testing methods such as the bubble point test into the closed fluid paths offered by Single Use Support presents numerous advantages for biopharmaceutical manufacturing processes. By incorporating these tests directly into the single-use systems, manufacturers can test the integrity of the filters they use with high efficiency while ensuring compliance with cGMP standards and regulatory requirements like Annex 1 and PUPSIT.
The seamless integration of filter integrity testing into single-use systems reduces the need for manual handling and reduces the risk of contamination or human error. This not only improves process reliability but also saves time and resources by eliminating the need for separate testing setups.
Furthermore, the use of single-use assemblies, such as filters or tubings, enhances process flexibility and scalability. These disposable components reduce the risk of cross-contamination and simplify cleaning and validation procedures, as they come pre-sterilized and ready to be implemented in pharmaceutical fluid paths, powered by Single Use Support’s fluid management system RoSS.FILL.
This way, automating filter integrity testing with Single Use Support's closed fluid paths offers significant benefits in terms of compliance, efficiency, and process optimization, making it an invaluable solution for modern biopharmaceutical manufacturing facilities.
- The Rules Governing Medicinal Products in the European Union Volume 4 EU Guidelines for Good Manufacturing Practice for Medicinal Products for Human and Veterinary Use, https://health.ec.europa.eu/system/files/2022-08/20220825_gmp-an1_en_0.pdf, Published
- Integritätstestmethoden, https://www.merckmillipore.com/AT/de/product/Integrity-Testing-Methods,MM_NF-C537, Published
- Abstract of integrity tests 2/3 – Bubble Point Test (BPT), https://www.filtrainternational.com/abstract-of-integrity-tests-bubble-point-test, Published 01.2020