Aseptic bag filling – 5 critical considerations
Table of contents
ShowAseptic bag filling is a process that is very important to the biopharma industry. For the process, aseptic bag filling machines are used specifically.
The technique of aseptic packaging is applied when sterilization of medical applications is not possible after the packaging step. This is very common for sensitive high-value biopharmaceutical products like CAR-T cells and related Cell and Gene therapies (CGT). The same process is also used in the food industry to package food products like purée, dairy products or fruit juice to enhance their shelf life.
This article will give you the basics of aseptic bag filling, highlights the most critical factors of the technique and discusses key considerations pertaining to the commercial use of aseptic bags.
Aseptic bags and other bioprocess container
Aseptic bags and other bioprocess bags are sterile plastic containers that are available in multiple bag sizes, ranging from a few milliliters well into the multi-liter range. These bags are designed to provide a hygienic and safe environment and used both for high acid and low acid products, setting high demands on their individual components.
Bioprocess bags are usually manufactured from polyethylene (PE) foils. This material has proven ideal for biopharmaceutical products and food alike, due to its biocompatibility (non-toxic and FDA-compliant), outstanding mechanical properties even at low temperatures (hard to tear or break, while being very flexible), great resistance against chemicals, and its ease to be sterilized by several methods (irradiation, treatment with ethylene oxide, high pressure steam).
During filling of drug substance in bags, the sterilized bags are filled with an aseptic liquid product using fully or semi-automatic filling machines in a sterile environment and finally sealed to prevent contamination. Specialized filling equipment (bag-in-box filling machines) allows to manufacture bag-in-box packagings (BIB), which contain the PE bag inside a cardboard box, or analogously bag-in-drum packages.
In Q2 of 2022, Single Use Support launched its own single-use bioprocess containers that are optimized for use with biotechnological intermediates and biopharmaceutical substances. In the next section, we will elaborate the critical factors to consider when using aseptic bags.
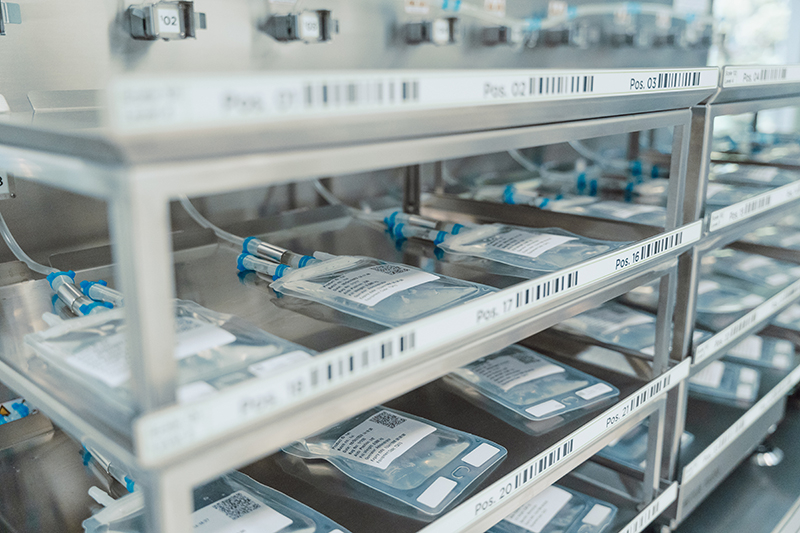
1. Compatibility - a key aspect in aseptic filling of bags
Many manufacturers strive to secure their market share by the use of proprietary fitments, valves, capping, spouts, connectors and other accessories for their aseptic bag fillers and production lines.
However, compatibility across all filling technologies and component manufacturers is of utmost importance for efficient production lines. It is our goal to supply our customers with single-use components that are compatible with all major brands (e.g. Sartorius, Thermofisher, Merck Millipore).
2. Speed - the faster the better
Time equals money. This statement holds in every business sector. In biopharma, time equals lives saved and patients treated, too. That’s why high speed without compromising high quality during manufacturing and processing steps is of crucial importance.
Single Use Support single-use tubing assemblies are compatible with all major manufacturers and aseptic filling machines, therefore simplifying all steps including handling of components (attaching and removing bags, fitments, tubing, etc.). Moreover, full compatibility reduces the likelihood of errors along the filling process, leading to leaks and contamination.
3. Safety - sterile and smart without product loss
A critical safety consideration for aseptic filling of bags is ensuring the sterility of the bags’ contents. Single-use bags are supplied after sterilization with either high pressure steam, gamma irradiation or through chemicals that permeate the bag (e. g. ethylene oxide).
The components of an aseptic filler that are in contact with the sterile goods (filling heads, tubings, etc.) are made of materials like stainless steel that are compatible with clean-in-place and sterilize-in-place (CIP & SIP) procedures. In addition, the filling step is executed in a filling chamber, that is kept aseptic through various methods.
4. Costs - as low as possible
The employment of single-use components is economic. At first sight, this appears counterintuitive and not sustainable.
On the contrary, single-use components reduce equipment down-time for cleaning and sterilization procedures. These processes are time and energy consuming and possibly involve the use of hazardous chemicals, which leads to hazardous waste and concerns regarding sustainability.
Moreover, single-use components decrease the risk of product loss due to contamination of aseptic products, thereby increasing the efficiency of manufacturing plants.
5. Scalability - customizable aseptic filling solutions
Novel biopharmaceuticals like CAR-T cells and similar cell and gene therapies (CGT) come with challenging supply chain bottlenecks inherent in their underlying biology. Single Use Support is a front-runner in supplying major CGT manufacturers with scalable customizable solutions, from single milliliter scales to intermediate bulk container (IBC) components.
Read more: Aseptic filling of large volumes
Single Use Support offers countless custom designs to fully match the customer’s needs. Customers can either select from a variety of pre-configured single-use assemblies or design their own custom solutions – according to their individual requirements.
Pioneering biopharma with Single Use Support
Single Use Support is a leading supplier of fluid management solutions, offering a product portfolio not only including single-use bioprocess containers, compatible with various manufacturers. Instead, there is a wide range of platform systems and assemblies for biopharmaceutical fluid management.
RoSS.FILL, for instance, is an automated aseptic filling system that is fully scalable in order to cater applications from research to bulk scale. Accompanied by customizable single-use assemblies, the filling platform can increase flexibility and efficiency in fluid transfer while ensuring sterility throughout the entire process.
Followed by aseptic bag filling, biopharmaceuticals often undergo ultra-low or even cryogenic freezing processes. Not only are Single Use Support’s bioprocess containers able to withstand sch extreme temperatures: The company also provides dedicated freezing and storing systems for biopharmaceutical cold chain – such as the plate freezing platform RoSS.pFTU or the ULT freezer RoSS.FRDG.
Powered by Single Use Support’s end-to-end solutions, biopharma companies can either optimize individual process steps or streamline entire production lines, taking advantage of advanced single-use technologies for maximized flexibility, efficiency, and safety.
Related products
The Single Use Support Configurator allows the customer to draw and assemble designs according to his unique needs. The configurator tool offers a graphic interface and is easy and intuitive to use. Never has ordering of single-use components been more convenient.
FAQs about aseptic bag filling
Is there a difference between sterile filling and aseptic filling?
In their definition yes, sterile filling and aseptic filling are not the same, although they are closely related processes. Sterile filling refers to the process of filling containers (such as bags, syringes, or bottles) with a product (such as drugs, vaccines, or biologics) under sterile conditions. The goal is to ensure that the product remains free from contamination by microorganisms, ensuring its safety and efficacy. Aseptic filling, on the other hand, is a broader term that encompasses not only the filling process but also the entire manufacturing environment. Aseptic filling involves maintaining a sterile environment throughout the entire manufacturing process, from the preparation of components and equipment to the filling and sealing of containers. This includes sterilizing equipment, maintaining cleanrooms, and implementing strict procedures to prevent microbial contamination.
What is an aseptic bag?
An aseptic bag is a germ-free container that is used within the supply chain of several drug products. Sufficiently sealed, aseptic bags like Single Use Support’s IRIS Single-use bioprocess containers are designed to prevent the products that are stored within them from being contaminated.
Aseptic bags undergo sterilization before they can be used; the four main ways to do so are:
- Sterilization by heating
- Sterilization by radiation
- Mechanical sterilization
- Chemical sterilization
What are the requirements in the aseptic area?
The aseptic area requires maintaining a sterile environment for drug materials all the way from the manufacturing site to the place of application. This implies the necessity of specialized equipment that accompany this complex process as soon as the drug product is sterilized, including aseptic filling machines and tubing, sterile containers and a sterile filling environment.
Additionally, the containers have to be sufficiently sealed in order not prevent contamination along the supply chain of the drug product.
What is an aseptic filling machine?
An aseptic filling machine is part of the supply chain of various goods, including several drug products. It is designed to facilitate the filling of drug products into pre-sterilized containers, before these are sealed.
Considering the need for highest accuracy within this process, aseptic filling machines need to be extremely reliable; Single Use Support has therefore developed the RoSS.FILL platform with high quality aseptic filling machines for different fields of application.