Go with The Flow: How Sustainable is the Trend Toward Single-use Systems?
Table of contents
ShowSpeed to market, flexibility, and process efficiency are more important than ever in biopharmaceutical production. Single-use systems support novel approaches to aseptic fluid management and aseptic liquid transfer. However, regarding the sustainability of single-use systems, there are still concerns within the scientific community. BioPharm International sat down with Single Use Support to address these apprehensions and discuss the future of single-use systems in biopharma.
Single-use systems in biopharma: would you see it as the rising trend or a short-term buzz?
We would see it as the rising trend, meaning a long-term trend. Different customers have different requirements regarding their processes in terms of scalability and primary packaging in the variety of products. As a company, we see more and more customers focus on sustainability topics like energy consumption and waste material. When we hear clients talking about problems and requirements, single-use technologies meet their requirements. Cell and gene therapies have an influence on the trend of single-use technologies - where short turnaround times are crucial - as well as highly-adaptive systems to different demands in equipment. For example, one of our clients has a huge manufacturing facility where only stainless-steel tanks are connected with single-use equipment. This enables agility in a facility, even if stainless-steel tanks are still used. This means that this setup requires a variety of single-use assemblies to meet the demands of different processes instead of building a new facility fully made of stainless steel. For example, another client goes even further by replacing the stainless-steel tanks with single-use bioreactor bags, meaning those bags include the complete sensor technology for process monitoring. So, to sum it up, there’s definitely a trend toward single-use equipment.
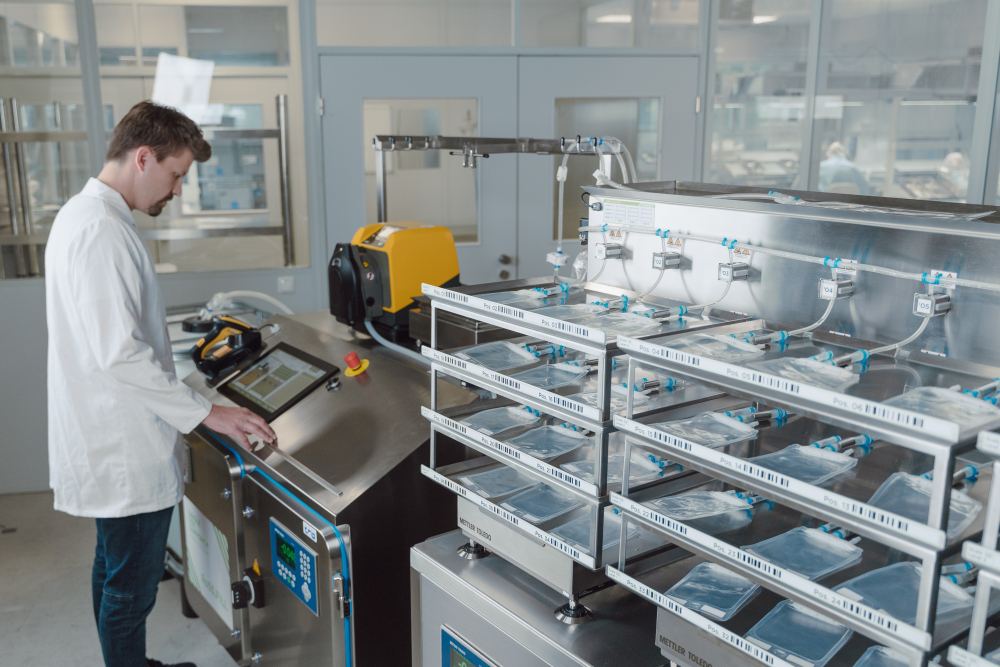
What are the key benefits of single-use systems over stainless steel?
Single-use systems can be disposed immediately after their utilization, as they do not require any elaborate cleaning and disinfection (CIP, SIP). It takes eight months less project lead time for implementation of single-use production. So, single-use systems are much more flexible and scalable, as well as suitable for small and large amounts of drug substances. When we compare single-use systems to stainless-steel facilities, the complexity of automatization is markedly higher. Complex steps like cleaning and validation take a lot of time between separate production steps. Plus, non-disposable liquid pathways make installation more elaborate. Stainless-steel processes also require a significant amount of infrastructure for processing and cleaning on site.
Another factor I would like to point out is safety. With the disposal of the liquid pathway after each batch, single-use technologies overcome risks of cross contamination. In terms of stainless steel, the risk of contamination is particularly high in different antibodies, if proteins are manufactured in the same facility. Contamination leads to a loss of drug substance and requires additional cleaning steps. Another crucial factor for the key benefits is cost efficiency. Single-use systems reduce initial investment as well as R&D costs. The initial investment costs are approximately 40% lower than the price for a comparable stainlesssteel facility. So, compared to stainless-steel bioreactor systems, they have high costs for complex production stages like cleaning and sterilization. Furthermore, costs for implementation, utility, and maintenance are comparatively high. Another factor is the operational expenditures, which are decreased due to the efficient use of time and resources, especially regarding cleaning-in-place and steaming-in-place procedures and/or relevant supportive actions and resources, meaning human capital.
How would you assess the risks of cross contamination comparing single-use systems with stainless steel?
While talking about single-use systems, you can’t talk about a closed system without any potential contact to the environment. The entire single-use system is sterilized under validated conditions and, compared to stainless-steel parts, all parts are touched. It means knowing eventually that volumes are there, which might be a source of contamination. That liquid transfer can be done in a whole closed system with different technologies - sterile connectors, single-use filters, pressure sensors, flow meters, and many more - without cleaning. The different parts of the single-use assembly already come sterilized and double packaged to the customer and are ready to use. Operators only need to click different parts together and then the sterile system is good to go. There is no need to wait on results of different departments of the company, like the microbiology lab of quality, which can take hours to days before it can start production. Furthermore, a huge volume of water for injection (WFI) needs to be used to rinse the stainless-steel system.
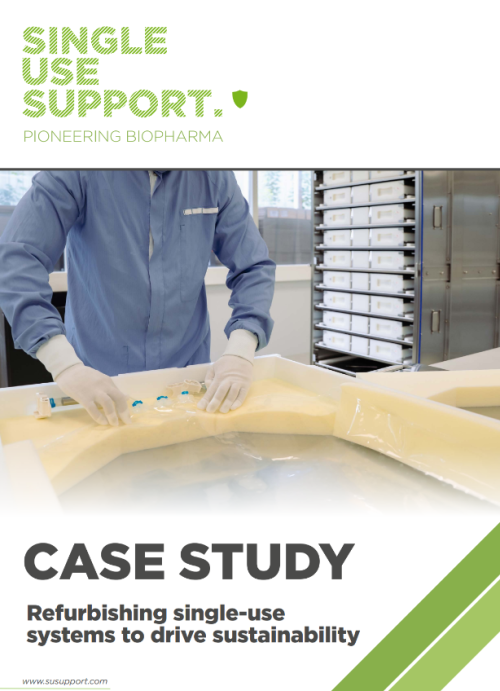
Download Case Study
Case Study: Refurbishing single-use systems
In collaboration with a US-based vaccine innovation company, Single Use Support has implemented a reusability model for single-use systems. To ensure secure cold chain transport between CMOs, 125 trolleys - each carrying 10 reusable RoSS® shells with 50L single-use bags - circulate within a closed, sterile, and controlled loop. Download our Case Study.
Increasingly interesting for the industry are sustainable solutions. How sustainable are single-use systems?
Single-use technology used in biopharma produces about only 0.01% of the total plastic waste. End-to-end life is rigorously collected, decontaminated, and treated. That’s one crucial point for the sustainability aspect of single-use systems. Furthermore, materials used in single-use equipment follows very high regulation standards with different kinds of certificates and studies, for example, extractables and leachable studies, REACH, certificates, including BSE, TSE, Bis-Phenol-A, phthalates, melamine, dioxin, and many more. Compared to stainless steel, you’re safe. Heat, water, chemicals - so meaning the whole energy management and waste management - is completely different from the conventional and traditional stainless-steel systems. The single-use technology also saves electricity due to reduced size and classification of controlled areas. To sum it up, the average reduction of the carbon footprint, including the reduction of water, energy, chemicals, etc., is 40% compared to stainless steel, which is huge.
Looking into the future, could single-use systems completely replace stainless steel?
We would say not completely, but to a large extent. Possibly up to 90%, but with time passing by and more and more users switching to single-use systems, technologies will definitely be developed further, and a lot of today’s challenges will be solved. The main disadvantage of switching from stainless steel to single-use systems is scalability. Scales are limited by current 2,000 L cell culture bioreactor capacities. However, some of our customers split up, for example, a 12,000 L vessel into 2,000 L single-use bioreactor bags and, therefore, they are able to harvest continuously. With this, the customer converted the disadvantage to an advantage in terms of dynamic harvesting. The technical term is continuous harvesting. Single-use systems have become increasingly popular over the past few years, and they are now an established standard in the biopharmaceutical industry.
As mentioned before, there are a few advantages compared to the traditional stainless-steel reactors. You can raise the question: why are some manufacturers still hesitant when it comes to switching from stainless steel to single use? Stainless-steel tanks, as single-use bags protection, pose no such risk. On the other hand, the contamination rate is substantially higher. Additionally, cleaning and sterilization can be an issue. The same is true for wrongly positioned seals or liquid pathways. However, new developments should never be ignored; after all, new technologies that allow for a more effective production process are key to staying competitive. Single-use systems offer biopharmaceutical companies a new and reliable logistics process for liquids on the basis of standardized single-use bags. Therefore, we strive to fulfill the requirements of our customers in that sector. Such demand can only be met by applying single use-technologies.