How to avoid single-use bag leakages in bioprocessing
Table of contents
ShowSingle-use bag leakage can be a severe issue in bioprocessing, particularly considering that cost-intense production can be ruined in a fraction of a second. Therefore, biopharma manufacturers as well as health authorities are bound to make sure that primary packaging is intact at all times in order to avoid costly product loss, production delays, and safety and supply chain concerns.
Easier said than done, since there are several factors to be considered that have an impact on bag integrity – some depending on bag manufacturers, others on proper handling, storage and transport when already containing valuable biologics.
In this article, we will not only discuss why it pays off to bother with the integrity of single-use bags in bioprocessing at all, but also take a look at how manufacturers can effectively reduce the risk of single-use bag leakages.
Single-use bag leakage – why bother?
Over the past years, single-use technologies have increasingly been replacing stainless steel solutions within biopharmaceutical manufacturing. This has brought several advantages for manufacturers, patients, and the environment.
However, the implementation of bags made of single-use plastic also brings the necessity to deal with their integrity and protection. Of course, this is true for all kinds of single-use and reusable bags, but the consequences of leakage in the biopharma industry are much more severe than breakage of a full shopping bag right in front of the entrance door.
Patients might suffer from delays in their course of treatment that may result from single-use bag leakage – especially in the field of personalized medicine, where drug substances are tailor-made for a small number or even individual patients during complex, time-consuming and costly manufacturing processes.
This is what makes certain drug substances not only indispensable for patients, but also extremely costly. In fact, the cost of one single bag to break was estimated to range from USD 100.000 to USD 1 million on average.1
Additionally, biopharmaceutical manufacturers often deal with hazardous substances, such as ADCs (Antibody-Drug Conjugates): Both staff and the environment need to be protected from exposure to such solutions, which adds to the aforementioned reasons for the biopharma industry to be able to rely on intact and safe single-use bags.
Read more: Weak Point: Avoiding leakages of Single-Use Tubings in Biopharma1
The impact of freezing on single-use bags
In the course of countless biopharmaceutical production workflows, freezing biologics is an essential step: It aims to preserve valuable intermediates and drug substances from degradation that would otherwise occur in ambient temperature, and allows long-term storage and transport of biological materials.
Freezing single-use bags – be it with plate freezing, reaching temperatures as low as -80 °C, or cryogenic freezing down to -170 °C – can pose stress not only to the frozen drug substances itself, but also to their bioprocess containers. The bag and its attached single-use assemblies enter a glass-like state at sub-zero temperature, making them very sensitive and fragile. Friction, bumps and minor bending may cause damage to the multi-layer films, leaving the contained product unprotected and thus unusable. Additionally, freezing water leads to a volume increase of about 8%, resulting in a higher pressure in single-use bags. Also, when the liquids are thawed, there may arise severe safety concerns due to leaking single-use bags containing hazardous substances.
Manufacturers need to be aware of these concerns and implement adequate protocols and single-use bag protection to unlock the advantages that single-use containers bring to bioprocessing. However, there are plenty.
Why single-use bags are still the option of choice
Single-use bags in bioprocessing offer several key advantages. They help lower greenhouse gas emissions and have a lower environmental impact over their life cycle. These bags can be versatile substitutes in various industries, offering cost-effective solutions.
While they do not reduce plastic waste, they reduce the need for laborious cleaning and sterilization processes, which would otherwise require significant amounts of water, energy, chemicals, and human workforce.
Due to their shape, single-use bags allow for a higher storage density both for storing and shipping. Furthermore, they enable advanced plate freezing as an essential freezing method for a variety of biologics.
The versatility of single-use bags is yet another reason why they have become a popular choice in the biopharma industry, allowing for easy scale-up and other changes in the production process. However, manufacturers need to establish workflows with adequate handling, single-use bag quality and protective measures.
Designing robust single-use bags
Designing robust single-use bags is a critical aspect of bioprocessing, ensuring the integrity and efficiency of the entire production process. The character of these bags must adhere to stringent bag regulations and meet specific standards to guarantee their suitability for biopharmaceutical applications. Furthermore, different bag shapes can significantly impact bioprocessing efficiency, affecting fluid dynamics, mixing, and product yield.
Moreover, the choice of materials is a vital element in ensuring the robustness of single-use bags. It is imperative that these materials are selected with care, as they must withstand the demands of bioprocessing while adhering to ASTM and other standards. The materials used should not only meet these regulations but also consider the character and composition of the substances they will contain – also regarding the necessity to provide a low extractables and leachables profile. Among the most frequently used inner films of single-use bags are:
- PE Multifilms (e.g., IRIS Bag)
Material: Polyethylene
Characteristics: Flexible, durable, chemically resistant - EVA
Material: Ethylene Vinyl Acetate
Characteristics: Milky appearance, stretchable - Fluoropolymer
Material: Polytetrafluoroethylene (PTFE), Ethylene Tetrafluoroethylene (ETFE)
Characteristics: Chemically resistant, high purity, non-reactive
The robustness of single-use bags is vital, as any compromise in design and material selection can lead to leaks, contamination, or loss of valuable product. Therefore, meticulous attention to detail in the design phase, while considering bag regulations, bioprocessing efficiency, bag consumption, materials, and adherence to regulatory standards, is crucial.
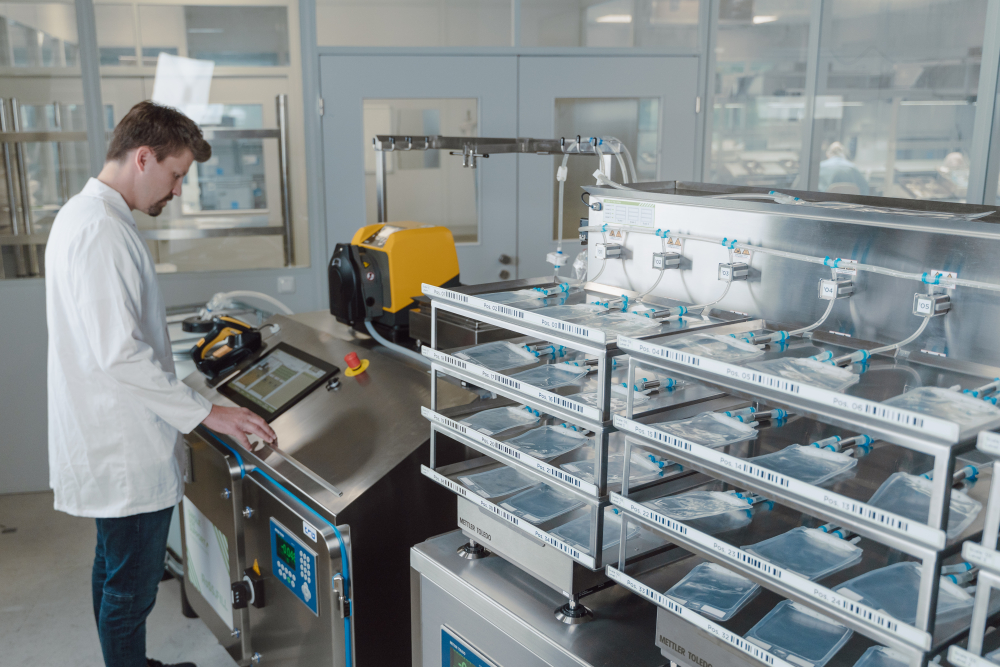
Secondary packaging for single-use bags
Secondary packaging for single-use bags is indispensable to ensure their protection during shipping and storing processes. Packaging solutions can prevent single-use bag leakage by shielding them from external stress, enhancing safety and reliability in bioprocessing – not only, but especially when dealing with hazardous substances.
Considering that CDMOs often have to deal with different types of single-use bags, it is essential for them to have vendor-agnostic single-use bag protection solutions at their disposal. Options like RoSS® Shell are therefore frequently chosen to keep manufacturing processes both flexible and scalable: They can shield single-use bags of different sizes and from various manufacturers, adding to their versatility.
Furthermore, packaging solutions must aim to allow for high storage density: Keeping biologics at ultra-low or cryogenic temperatures is a costly process, which is why storage space is precious and has to be used efficiently.
Automation – minimizing human intervention for increased process safety
Automation is a game-changer in the biopharma industry when it comes to handling single-use bags. Automated fluid management systems like Single Use Support’s RoSS.FILL platform streamline the entire process, from bag setup to monitoring, ensuring precision and minimizing the risk of human error.
Manual handling poses the risk of inadvertent mishandling, which may result in leaks, contamination, or product loss. In contrast, automation offers consistent and controlled manipulation of single-use bags and can reduce the risk of overfilling. Moreover, automated systems often include real-time monitoring, providing instant feedback on the bag's condition and enhancing traceability.
The result is a more robust and efficient bioprocessing workflow that is less susceptible to human error, thereby ensuring the integrity of single-use bags and increased compliance with regulations issued by policymakers.
IRIS Single-Use Bioprocess Containers – bags in outstanding quality
IRIS Single-Use Bioprocess Containers by Single Use Support are single-use bags that provide an exceptional solution for biopharmaceutical needs. These containers are qualified for a wide temperature range, from -196°C to +50°C (-320°F to +122°F), offering outstanding versatility.
IRIS bags are tailored to your specific requirements, ensuring secure primary packaging for cell culture media and drug substances. They protect against product loss during freezing, storage, and transport, making them a top choice for the biopharmaceutical industry.
With a smart material composition (PE and EVOH), these bags offer robustness and flexibility, combined with a low extractables and leachables profile. They are customizable in size, fill volume, tubing, ports, and connectors. IRIS Single-Use Bioprocess Containers are a reliable and adaptable solution for the biopharmaceutical industry, ensuring the integrity and safety of high-value liquids while reducing product loss to a minimum.
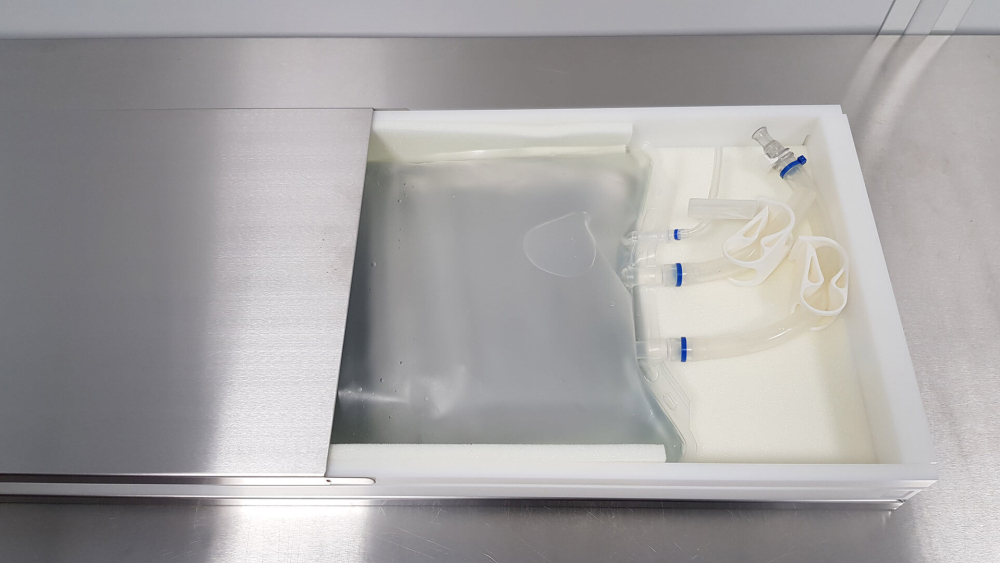
RoSS®: Full protection for your single-use bags
Protecting single-use bags is paramount, especially when they reach a glass-like state due to freezing. In this delicate condition, the slightest mishandling can lead to product loss and compromise. RoSS® Shell, with over 200,000 units sold worldwide and a product loss rate of less than 0.001%, is the ultimate solution.
This robust storage and shipping system provides impeccable safeguarding for 2D single-use bags of any size and from any vendor. Traditional methods often incur a product loss of around 1% to 5% during transport, freezing, and thawing steps, whereas the RoSS® shell reduces this risk to a negligible minimum.
The RoSS® Shell, inspired by the structure of an oyster, features a smart combination of materials that ensures a 100% protective shell, stackable for optimized storage density. The 3D foam at the inside becomes firm at -20 °C, keeping the single-use bags coated and firm. For smaller volumes, RoSS.KSET option is ideal, making it the perfect choice for cell and gene therapies or clinical studies.
For CDMOs - dealing with multiple single-use bags - very important: The RoSS® system is vendor-agnostic, offering flexibility and compatibility without requiring system changes. It supports every available single-use bag, regardless of brand or size. Its high storage density and ergonomic design make it a practical and cost-effective choice, resisting even extremely low temperatures. With RoSS®, you can trust in the safety and integrity of your single-use bags throughout the freezing and transport process.
- Point-of-Use Leak Testing of Single-Use Bag Assemblies, https://www.biopharminternational.com/view/point-use-leak-testing-single-use-bag-assemblies, Published 2017