Vaccine manufacturing: Introduction to the process from development to large-scale production
Table of contents
ShowVaccine manufacturing is a complex journey, merging scientific breakthroughs with global necessity. From the identification of antigens to large-scale production and the use of cutting-edge solutions, this journey reflects the continuous pursuit of creating effective vaccines for a healthier world.
Vaccines rank among the most cost-effective health interventions against pathogens and infectious diseases, annually saving millions of lives. However, growing global demand presents significant challenges for vaccine manufacturers. As the array of new vaccine types and manufacturing methods expands, the establishment of robust processes that could enhance overall efficacy, safety, and cost-effectiveness is hindered.
Efficient production, marked by flexibility and easy scalability, becomes increasingly crucial. In this article, we will give an introduction to vaccine manufacturing, the stages from development to large-scale production, explore challenges faced by manufacturers, and examine potential solutions and future prospects.
What is vaccine manufacturing?
Vaccine manufacturing is the complex and highly regulated process of producing vaccines, which are biological products designed to stimulate the immune system and provide protection against specific diseases. Vaccine development involves several stages, including vaccine research and development, production of raw materials, formulation, and quality control.
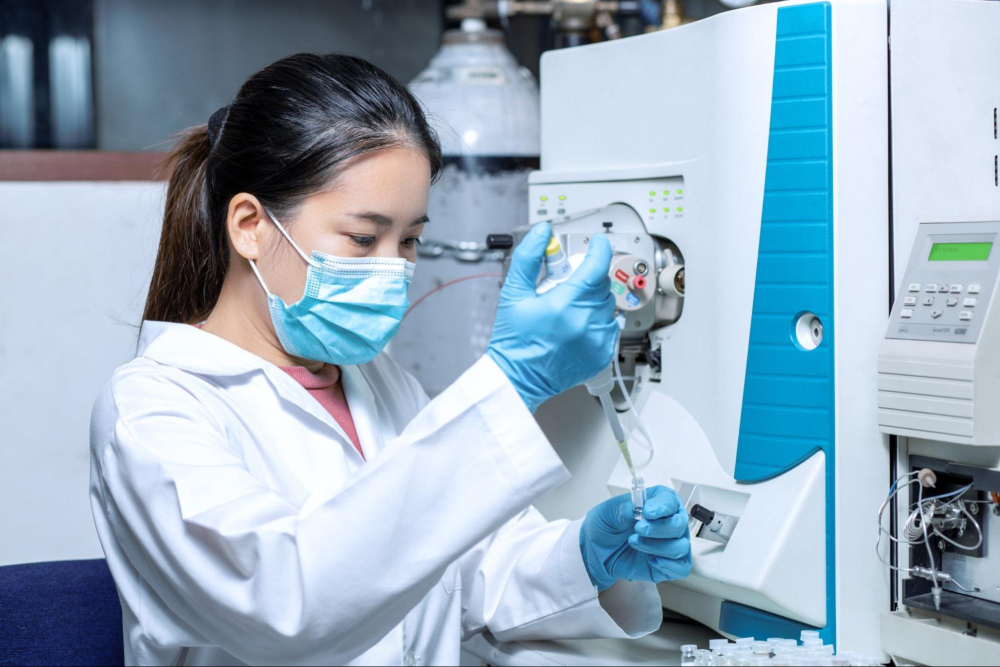
Types of vaccines
Just as there are multiple pathogens, each demanding a tailored approach, diverse vaccine technologies come into play for effective immunization. Depending on the targeted pathogen—be it a bacteria or virus—various vaccine platforms are harnessed to stimulate a potent immune response.
From traditional methods like live attenuated and inactivated vaccines to cutting-edge advancements like mRNA vaccines, the arsenal of vaccine platforms continues to expand, and can be divided into small molecule vaccines and the more complex and sensitive large molecule vaccines, requiring more elaborate cold chain management:
Small molecule vaccine technology platforms:
- Live Attenuated Vaccines: Utilizing weakened forms of the pathogen to induce a robust immune response.
- Inactivated Vaccines: Employing killed pathogens to stimulate an immune response without causing illness.
- Toxoid Vaccines: Using inactivated toxins to generate an immune response, particularly effective against bacterial diseases.
Large molecule vaccine technology platforms:
- Subunit Vaccines: Focusing on specific components of the pathogen to elicit a targeted immune response.
- mRNA Vaccines: Leveraging genetic material to instruct cells to produce antigens, prompting an adaptive immune response.
- Virus-Like Particle Based Vaccines: Mimicking the structure of viruses without the genetic material, inducing an immune response.
- Viral Vector Vaccines: Harnessing other viruses as vectors to deliver genetic material, stimulating an immune response against the target pathogen.
Vaccine production
Vaccine production commences with the implementation of various manufacturing techniques, including cell culture, recombinant methods, viral vectors, and RNA-based approaches. The need for respective techniques depends on the vaccine type that is to be produced: The more complex the product, the more elaborate are the processes involved.2
This distinction depends on the scope of the production line, such as for small-molecule or large-molecule vaccines. The latter requires far more precise solutions, e.g. in cold chain management, due to their increased sensibility.3
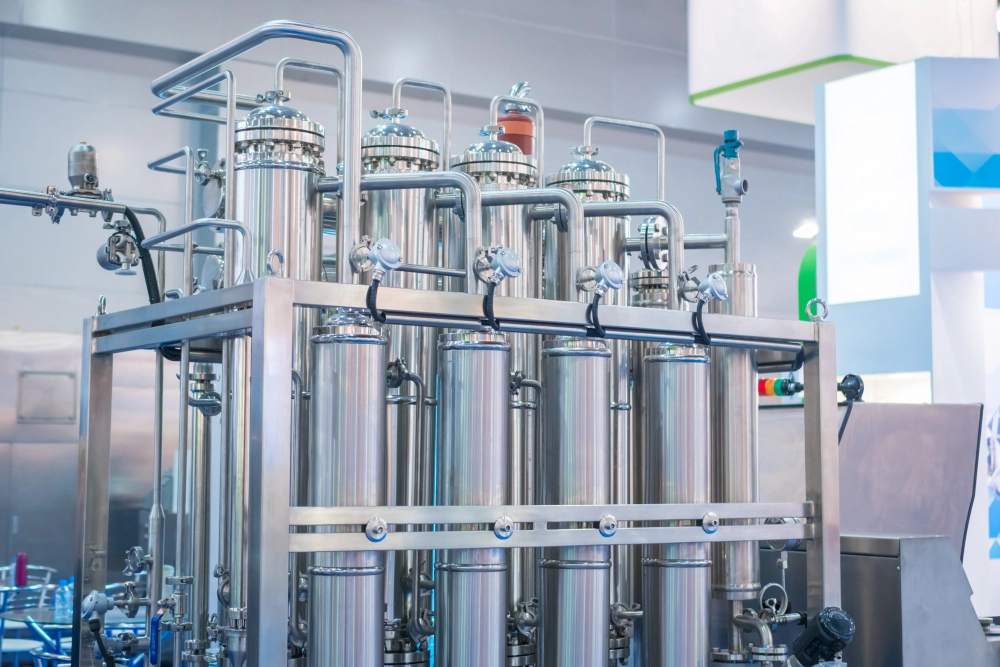
Vaccine manufacturing process
Behind vaccines' potency lies a complex manufacturing process, supported by crucial elements that ensure a safe and efficient production as well as a widespread distribution. The heart of vaccine production lies in diverse manufacturing techniques and processes, each playing a crucial role.
- Cell culture methods involve cultivating cells to generate the necessary components for the vaccine.
- Recombinant techniques utilize genetic engineering to produce specific proteins, contributing to the vaccine's effectiveness.
- Viral vector methods and RNA-based approaches harness cutting-edge technologies to create vaccines with unique mechanisms of action.
Typical vaccine manufacturing with cell culture methods include the following manufacturing steps:
1. Cell culture and harvesting
Cell culture and harvesting serves as a crucial bridge between discovery and large-scale production. Cell culture techniques contribute to the optimization of cell growth, enabling the efficient generation of high-quality antigens essential for the development of advanced immunization solutions.
Harvesting, a precision-oriented process, separates cells and extracts antigens with innovations minimizing damage. The synergy of cultivation and harvesting drives vaccine development toward the creation of safe, effective, and globally accessible immunization solutions.
2. Purification process
Purification involves the removal of impurities from the harvested material, ensuring the final product meets stringent safety and efficacy standards. Cutting-edge purification technologies, such as chromatography and filtration, are applied to separate the valuable antigens from unwanted elements.
3. Formulation and filling
The formulation process involves crafting a precise mixture that ensures stability, efficacy, and the preservation of the vaccine's therapeutic power. Formulation technologies, such as lyophilization, contribute to the longevity and stability of selected vaccines. Once formulated, the drug substance is precisely filled into small bioprocess containers, ensuring accurate dosages.
4. Quality control
The final stage of quality control ensures the alchemy of safety and potency is perfected. This stage subjects the vaccine to a battery of tests and inspections, guaranteeing it meets stringent regulatory standards and also manufacturer's critical quality attributes (CQA). Every batch undergoes scrutiny for purity, potency, and consistency.
Scalable vaccine production
A significant phase in vaccine manufacutirng marks the scale of laboratory to large-scale production. Scaling up vaccine production and increasing manufacturing capacity to meet global demand requires intensive planning and execution.
This phase ensures that the developed vaccines transition seamlessly from small-scale to mass-produced, high-quality immunization solutions. Manufacturing and scale-up vaccine production demand meticulous cold chain management with the need for effective solutions for filling and freezing the drug substances to ensure the safety and viability of the vaccines throughout the journey. Process experts and project heads for technology transfer benefit from the safe handling of vaccines with single-use technologies to perform fluid & cold chain management. Vaccines are safely contained in single-use systems that safeguarding the frozen material during storage and transport.
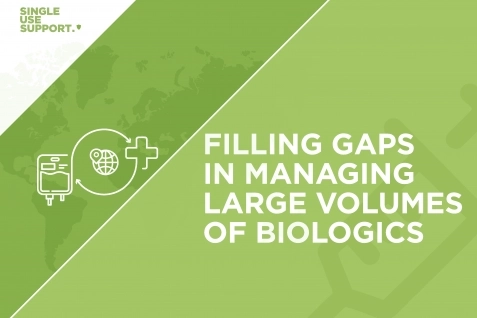
Download eBook
eBook: Filling gaps in managing large volumes of biologics
This eBook identifies key gaps in bioprocessing, provides guidance on selecting appropriate primary packaging, and addresses common hurdles faced in pharmaceutical handling. Furthermore, it introduces a new approach to overcome these challenges and offers a forward-looking perspective on the future.
Vaccine manufacturers you need to know
Vaccine manufacturing companies, including prominent players like Pfizer, Moderna, and AstraZeneca, alongside innovative biopharmaceutical firms such as Novo Nordisk, have assumed a big role in global public health.
The companies with the highest turnover in 2021 are listed from 1 to 10. With the industry’s tendency to constantly change, the names on the list might change in the future.3
Top 10 vaccine manufacturing companies by turnover 2021:
- Pfizer’s latest success, which put the company’s name on everyone’s map, was the Covid-19 vaccine. There are also a number of other vaccines in the pipeline, including meningococcal disease, influenza, Lyme disease, respiratory syncytial virus (RSV), and C difficile.
- Johnson & Johnson developed and manufactured the ebola vaccine Ad26. ZEBOV/MVA-BN-Filo, which shows good success rates. The American pharmaceutical corporation concentrates on the development of vaccines against HIV, Zika and Influenza.
- GSK (formerly known as GlaxoSmithKline) is a British company with manufacturing sites in Europe, North America and Asia. GSK overtook the shingles vaccine market with Shingrix.
- Sanofi, the French based pharma company, is mostly known for its vaccines against polio, haemophilus influenza type B and pertussis. Immunization projects in Sanofi’s pipeline are vaccines for yellow fever, rabies and more.
- Merck & Co. is American based and was founded as the American arm of the European Merck Group. Since then, it acted as an independent pharmaceutical company with a focus on vaccines with a focus on HPV, as well as the mumps, measles and rubella vaccine, MMR. Further, Merck is involved in the production of various drug products like Ketyruda, a humanized antibody, which is used in oncology.
- Novartis is a Swiss pharmaceutical company with focus areas on cardiovascular, immunology and a broad range of oncology therapies.
- BioNTech ("Biopharmaceutical New Technologies") developed the first mRNA vaccine against Covid-19 approved for human use by the FDA. The German company's main research point remains in mRNA therapeutics against different cancers and immunotherapy.
- AstraZeneca's main focus lies in the development and manufacturing of DNA based drugs and recombinant antibodies. It has also developped Beyfortus, a passive RSV immunization.
- Moderna’s success didn’t begin with its COVID-19 vaccine, which was among the first to be approved by the FDA in 2020. The Massachusetts based company specializes in the discovery and development of messenger RNA biologics. Or, as the name implies, to “mode RNA”.
- Bharat Biotech has been actively involved in the development of COVID-19 vaccine Covaxin. In 2024 it has received approval from the Central Drug Standard Control Organization to conduct a phase II clinical trial of the MTBVAC vaccine for TB prevention in adults and adolescents.
Some other vaccine manufacturing companies have potential to break into the top 10 soon:
- Novo Nordisk is a Danish headquartered pharmaceutical company. As world's leading insulin manufacturer Novo Nordisk attracted more attention and significantly increased sales in 2024 with its semaglutide products Ozempic and Wegovy.
- Bavarian Nordic is a biotechnology company from Denmark which specializes in the manufacturing of vaccines against infectuous diseases and cancer immunotherapies. The most prominent has become IMVAMUNE, a vaccine agains monkeypox (mpox), but there are several others agains chickenpox, rabies and chikungunya virus.
Sources:4
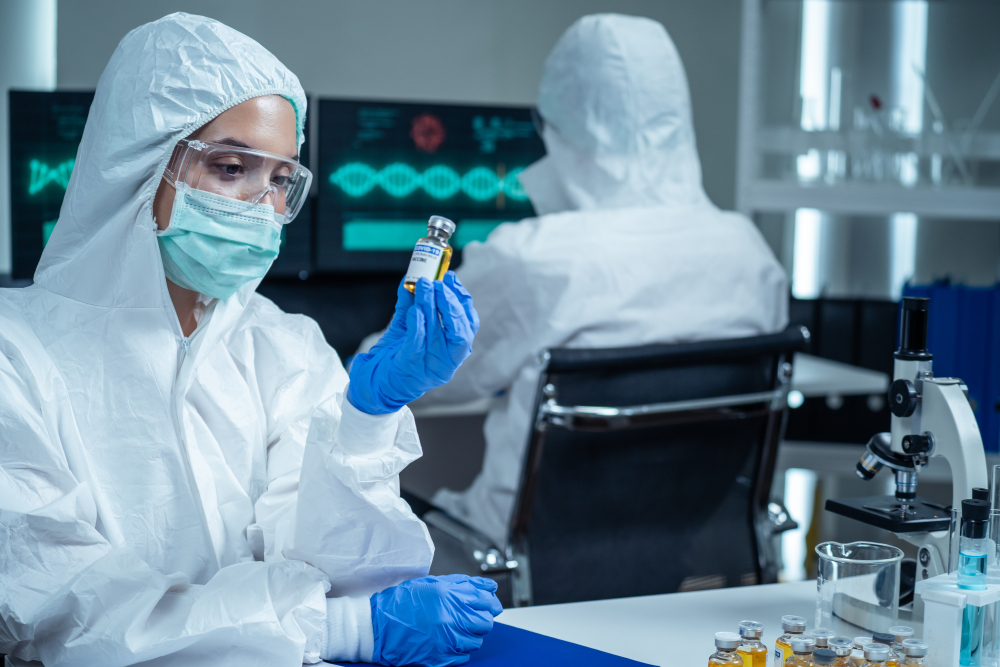
Challenges in vaccine manufacturing
A considerable challenge in vaccine manufacturing comes with the adequate handling of different substances. The individual components need to be cultivated, stored and processed with high accuracy and under sterile conditions in order to provide patients with safe and effective vaccine products, which have to be dealt with equally carefully.
Another critical factor in vaccine development and manufacturing are the associated costs, spanning from research and development in laboratories to large scale manufacturing and subsequent distribution. Balancing the financial aspects while maintaining affordable vaccine accessibility poses a continuous challenge.5
Efficiency
In order to limit both costs and time expenses involved in vaccine development and manufacturing, process efficiency is key. Streamlining production processes, minimizing waste, and optimizing resource utilization contribute to addressing this challenge. Additionally, efforts have to be taken to enhance product viability and to avoid product loss, as this results in unutilized productivity, delays, and increased overall costs. The implementation of efficient technologies and systems not only impacts the cost-effectiveness of vaccine manufacturing but also ensures a more sustainable and scalable approach.
Cold Chain Challenges
From first clinical phase studies in labs to the global distribution of vaccines, it is crucial to maintain an unbroken cold chain. Cold chain challenges encompass the need for consistent temperature control, especially for vaccines that are sensitive to temperature variations, such as cell-based or mRNA vaccines. It is of utmost importance to achieve a high product quality, especially when dealing with large molecules, which requires dedicated manufacturing solutions.
The transition from research and development settings to large-scale manufacturing facilities and eventual distribution to diverse geographical locations introduces complexities in sustaining the required cold chain conditions.
Innovation in cold chain solutions, such as advanced plate freezing technologies, safe and flexible ultra-cold storage solutions and temperature-monitoring systems, becomes imperative to maintain satisfactory product quality. As an expert in the field of fluid management Single Use Support is supplying vaccine manufacturers from laboratory heads to process managers with solutions for a seamless cold chain management including freezing, cold storage and cold shipping.
Scaling-up vaccine manufacturing
Apart from the investment that is involved in a scalable production of biopharmaceuticals, there are several challenges in vaccine development that need to be considered.
Challenges for vaccine manufacturers when scaling up (or out) are associated with the following factors:
- Limited space capacities: The manufacturing process of vaccines is laborious and involves many steps until the final vaccine doses can be shipped. In order to prevent bottlenecks due to a lack of manufacturing capacity, this can be outsourced, either through partnerships with CDMOs or other pharma companies that have the required equipment and space at hand or through scalable technological solutions.
- Staff shortages: The global demand for vaccines is high, but the resources not only in regard to production components like vials, filters or tubing but in trained personnel are often low. Intellectual property in how to handle equipment etc. has proved to be as important as having the right technology available.
- Supply chain delays: The supply chain, starting from acquisition of raw materials and ending at the distribution of vaccine doses, has to run smoothly. The risk of supply chain issues is particularly high at the touchpoints of manufacturer, CRO and CDMO. Additionally, errors when planning new construction sites have to be avoided, e.g. supported by EPC contracts or A&E firms.
- Regulatory requirements: Manufacturing facilities have to prove that the risk for contamination of vaccine components is kept at a minimum through current good manufacturing practices (cGMP). The products are regularly tested and validated for quality and compliance to changing or new regulatory standards, such as Annex1.
When it comes to upscaling vaccine manufacturing, it is most important to be prepared, as circumstances and demands can change quickly. This is why the landscape of vaccine manufacturing calls for more flexible solutions that allow for quick and efficient upscaling when the hour strikes.6 7 8
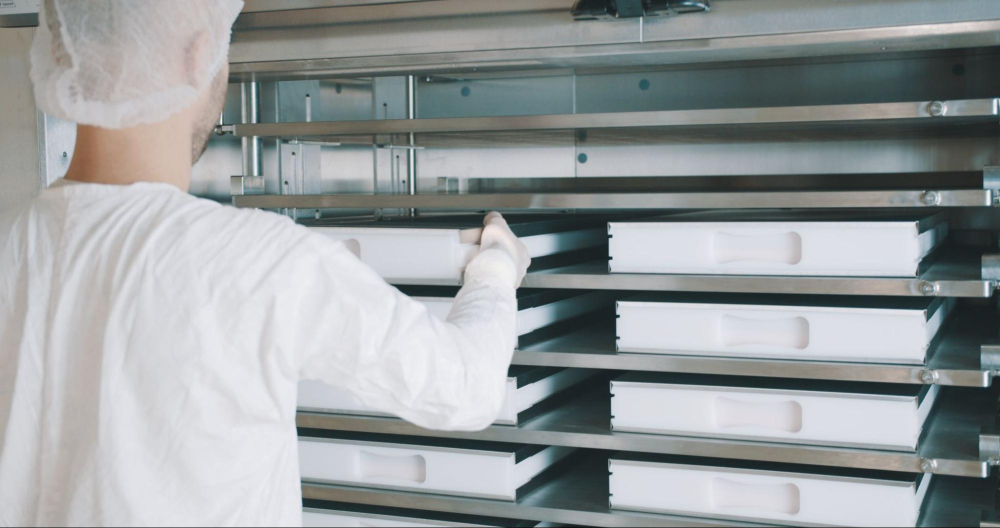
cGMP regulations in vaccine production
Good Manufacturing Practice (GMP) and Current Good Manufacturing Practice (cGMP) regulations serve as a cornerstone to ensure the safety, quality, and consistency of vaccine manufacturing processes. These regulatory requirements, set by the FDA, establish a comprehensive framework that vaccine manufacturers must adhere to during every stage of production.
Important cGMP guidelines for companies are
Standard operating procedures (SOP): Facilities define the frameworks within which they operate. In vaccine manufacturing the goal is to maintain a clean and hygienic environment that shows with no risk of cross-contamination.
Quality controls: Any changes and deviations have to be documented to ensure that each batch has the same quality and product features. Accomplishing this involves extracting samples from individual batches, adhering to specific guidelines to ensure the reliability of the sampling procedure.
Standardized listing and instructions: Guidelines on products have to be clear and easy to understand, expiry dates on the packaging and ingredients listed.
Trained staff: Employees have to be competent and trained in their specific field. cGMP regulates the requirements for education and training for jobs in healthcare manufacturing.
Facility equipment: Technologies and consumables have to correspond to cGMP standards. The highest standards and the latest technologies are often needed to ensure the required quality of products.9 10
Where cGMP compliance is of essence
The following shows how cGMP requirements regulate the different process steps in vaccine manufacturing:
- Raw material control: Vaccines rely on the use of raw materials like yeast extract or natural and recombinant enzymes. These materials are often at risk of contamination because they can be derived from animal hosts and might have been exposed to microbes or viruses. cGMPs call for regular testing and standardized formulas in regard to the proportions of raw materials in vaccines.
- Manufacturing process: To maintain cGMPs compliance, manufacturers are wise to have up-to-date equipment for each step of vaccine manufacturing. These steps include filling, mixing, dispensing and freezing of vaccines. Facilities and production equipment have to be maintained and kept meticulously clean to prevent the risk of contamination. In addition, the standard operating procedures (SOPs) must be documented and followed without deviation to ensure staff safety and product quality.
- Quality control testing: Constant quality control is an important factor in vaccine manufacturing to ensure that batches have the same quality and are safe for patients to use. They are validated by sampling, starting specifications, and a number of tests which are all documented with determined methods. Testing is not only limited to the finished vaccine itself, but also necessary for starters, in-process fluids and packaging materials. Additionally, it's noteworthy that sampling for quality controls can also be integrated into the dispensing process step using single-use bags.
- Packaging and labeling: When it comes to packaging and labeling vaccines, cGMPs regulate the standards for displaying ingredients and the order they have to be listed on the packaging. Vaccines rely on aseptic packaging to prevent any contamination in vials and other containers. Moreover, single-use bags can also be labeled in the course of aliquoting for batch allocation and subsequent track & trace, ensuring a comprehensive and compliant approach.
- Documentation: Manufacturing and batch records complying with cGDP must be maintained to evaluate production performance and product quality. According to cGMP regulations, these records have to be stored for a certain period of time. That is why a lot of manufacturers switch to automated systems that help to streamline the process of documenting.
Manufacturing equipment for vaccine production
Vaccine manufacturing requires many solutions that help enhance efficiency in vaccine manufacturing. Several innovative manufacturing equipment for vaccine production contribute to optimize various stages of the production and distribution process the fluid management process of vaccines more efficient whilst ensuring their quality.
Fluid management solutions for vaccine manufacturers
Fluid transfer in vaccine production is a meticulous process, demanding precision in dosage of biologics. It is challenging to ensure aseptic conditions to prevent contamination, e.g. when transferring fluids between bioreactors and different production phases. Dealing with various product specifications, such as viscosities and material sensitivities, amplifies these challenges, requiring nuanced handling and careful monitoring throughout the liquid transfer process. The demand for accuracy and sterility in these transfers is critical for the final vaccine's safety and efficacy.
RoSS.FILL revolutionizes vaccine manufacturing with its automated, single-use aseptic filling and filtration. Its exceptional speed, with the capability to fill one batch with up to 1000 L, ensures swift production, reducing time and resource investment. Single Use Support's fully scalable system guarantees absolute sterility within an aseptically closed system, vital in vaccine manufacturing. RoSS.FILL's adaptability accommodate various volumes, enhancing efficiency and minimizing product loss. Its integration of supplier-independent filters optimizes processes, making it a game-changer in vaccine production.
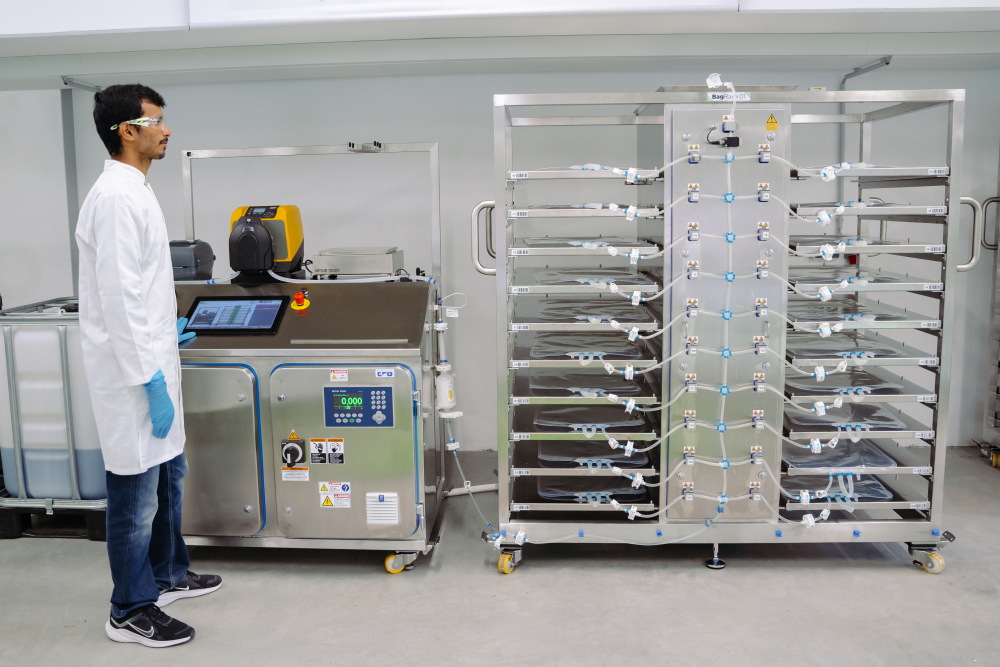
Cold chain solutions
Maintaining the integrity of vaccines during storage and transportation is an important aspect of the cold chain. Implementing advanced cold chain solutions for vaccine development involves employing cutting-edge freeze-thaw technologies, ultra low temperature storage and temperature-monitoring systems. These solutions based on single-use technologies play a crucial role in preventing inadequate cooling that could compromise the efficacy of vaccines, especially those sensitive to environmental conditions.
Single Use Support takes the individual fluid management spectrum in vaccine manufacturing into consideration to provide tailored end-to-end solutions ranging from automated filling into single-use bags to freezing with plate freezers. Notably, the plate-based freezing technology employed by Single Use Support is a flagship solution in terms of the quality of the freezing and thawing process. Covered in single-use shells, the single-use bioprocess containers undergo rapid and controlled rate freezing. The controlled freezing rates based on product characteristics prevents unwanted effects that potentially reduces product viability, such as cryoconcentration or crystallization.
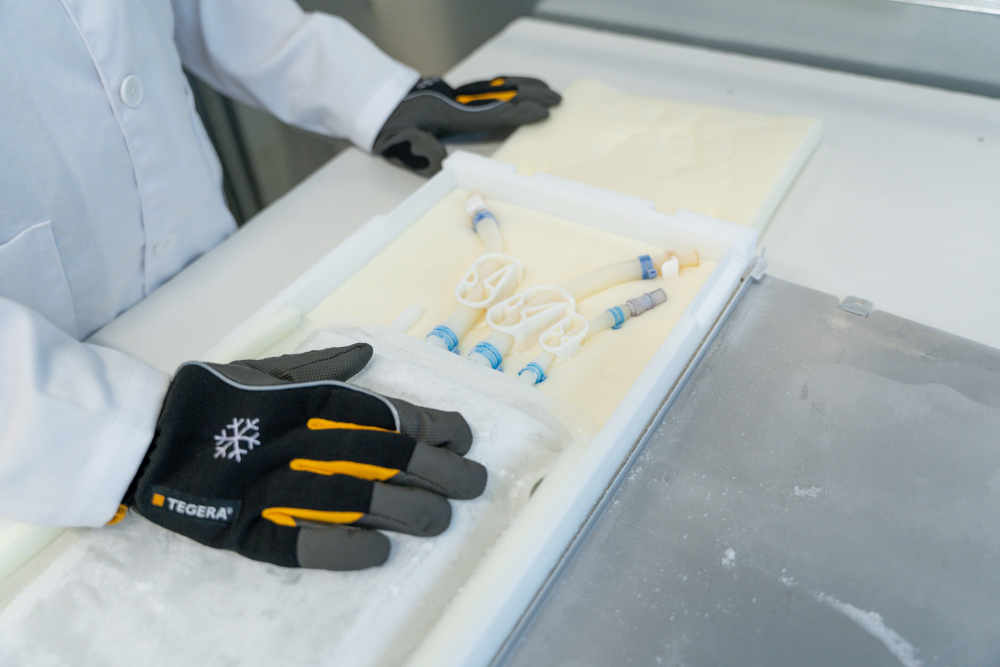
Ultra low temperature (ULT) storage of vaccines
To further enhance the preservation of frozen substances, Single Use Support’s solution for ultra low temperature storage of vaccines, RoSS.ULTF, comes into play. This solution allows precise temperature control during storage and transportation.
Such modular innovative storage solutions have emerged as a game-changer in the production and supply chain of vaccines as well as raw materials for vaccine production. Vaccines, especially those utilizing advanced technologies like mRNA, often require storage at extremely low temperatures. Ultra-low temperature storage solutions provide a reliable and efficient means of preserving the potency of these vaccines, ensuring they remain viable during production, distribution and administration, without the need to build large walk-in freezers.
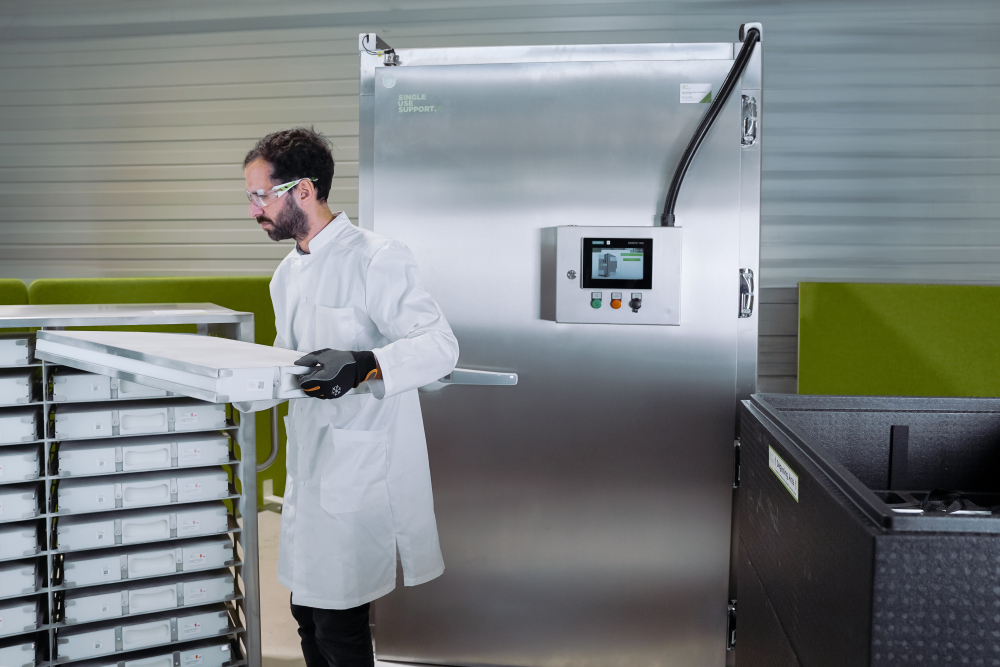
How single-use technologies improve vaccine production
The adoption of single-use technologies in vaccine production offers notable advantages. This approach replaces to a large extend traditional stainless-steel equipment with disposable components, streamlining the manufacturing process and reducing the risk of cross-contamination.
Single-use technologies in today’s vaccine market
In today's vaccine market, single-use technologies represent a game-changing production approach that is being adopted by vaccine manufacturing companies in the last decade. Single-use components like bioreactors, mixers, filtration systems and single-use assemblies play crucial roles in both streamlining and simplifying manufacturing, mainly because of the flexibility they bring to various processes. State-of-the-art vaccine production equipment collectively contributes to efficient vaccine manufacturing by addressing logistical challenges, optimizing storage conditions, and streamlining production processes. Fluid management solutions based on single-use technology, such as those from Single Use Support, facilitate flexible and scalable vaccine production, accompanying manufacturers from laboratory development to large-scale production.
Benefits of SUT in the production of vaccines
Single-use technologies (SUT) enhance flexibility, scalability, and efficiency in vaccine production. Their scalability allows manufacturers to adapt swiftly to varying production demands without significant infrastructure changes. SUT also allow manufacturers to maintain critical quality attributes (CQA) along different scales in production, e.g. controlling freezing rates with freezing protocols from lab scale through commercialized vaccine production. Moreover, single-use technologies are considered more sustainable than stainless steel installations, as they minimize water and energy usage by eliminating the need for cleaning and sterilization.
Cost-effectiveness stems from reduced cleaning and downtime, but also from the minimized risk of product loss due to automated processes in closed sterile systems. In addition, automated single-use technologies diminish human intervention, curbing the risk of errors and contamination.
The most important benefits of single-use technologies in vaccine manufacturing are:
- Reduced processing times
- Shortened time to market
- Adaptability of production capacities, market demands, and scales
- Reduced risk for cross-contamination
- More sustainable
- Easy implementation and quick changeovers, thus reducing size and cost of facilities
Novel methods & trends in vaccine production
The landscape of vaccine production is continually evolving, with emerging technologies driving innovation. Recombinant DNA technology, mRNA vaccines, and viral vector methods are novel vaccine manufacturing methods that have gained a foothold in the market.
What will be coming more and more are novel drug delivery systems, such as viral and non-viral vectors. For example in gene therapy or with bioconjugates, the choice of a suitable and effective delivery system to transport vaccine components into the body is one decisive aspect of modern vaccine manufacturing. In mRNA vaccines, these delivery systems are crucial. Viral vectors, such as adenoviruses, deliver mRNA into cells, while lipid nanoparticles serve in non-viral approaches, encapsulating mRNA to ensure its safe passage into cells. Their role lies in facilitating efficient mRNA delivery, ensuring its stability and protection until it reaches the target cells, thereby enhancing vaccine effectiveness and immune response.
- Viral vectors utilize modified viruses to transport genetic material into cells, leveraging their natural ability to invade.
- Non-viral vectors, like liposomes or lipid nanoparticles (LNPs), encapsulate genetic material, facilitating its entry into cells without using viruses.
Further ongoing developments in vaccine manufacturing that improve bioprocessing are the role of controlled freezing of valuable biopharmaceutical products and the rising importance of automation within bioprocessing.
Controlled freezing of biopharmaceutical products
Temperature-control is a main consideration to be made when producing, storing and shipping vaccines. Not all, but most vaccines must be stored and shipped at ultra-low temperatures in order to maintain product quality, resulting in safe and effective administration into patients.
Ultra-low temperatures as low as -80 °C pose significant stress to both the drug substance and the bioprocess containers subjected to such freezing process: It is vital to control the freezing rate and more parameters in order to prevent damages that might affect on the usability of a vaccine. Innovative freeze-thaw platforms, such as the RoSS.pFTU plate freezers by Single Use Support, can perform effective and scalable cooling of any vaccines, resulting in highest product quality (or cell viability) after thawing. The same attention must be paid to ultra-low temperature storage freezers that are at the heart of vaccine storage at sub-zero temperatures.
Automation in bioprocessing
Future trends in vaccine development suggest a continued focus on personalized therapeutics, tailoring immunization strategies to individual needs. Additionally, advancements in data analytics, artificial intelligence and Pharma 4.0 are likely to play a pivotal role in optimizing production processes and accelerating vaccine development. But before thinking about operational intelligence, bioprocessing must be automated.
This is true for process steps, such as fluid management in vaccine manufacturing: Both the individual components and the finished product need to be processed not only with great precision, but also reproducibly and with as little risks for contamination as possible, such as with the automated filling platform RoSS.FILL. Other tasks that profit from the reduced need for manual intervention are process steps like sample preparation, freezing, packaging and labelling. Single Use Support's automated process solutions make fluid and cold chain not only safer, but also more efficient. A shift towards increased utilization of single-use technologies brings notable advantages, encompassing manufacturing efficiency, contamination safety, and enhanced scalability and flexibility based on demand.
FAQs about vaccine manufacturing
What is meant by vaccine production?
Vaccine production is the way scientists and engineers create vaccines to help our bodies fight off certain diseases. The different types of vaccines produced, including live attenuated vaccines, inactivated vaccines, subunit vaccines, and mRNA, involve a lot of careful research, often involving years of research and testing, following strict rules to ensure safety and effectiveness, and obtaining regulatory approvals before the vaccine can be widely used to protect people from infections.
What are the benefits of vaccine production?
Vaccine production serves as a critical pillar of global health, providing vital protection against various diseases. The benefits of vaccine production include disease prevention, increased stability in the healthcare sector, control of epidemics and pandemics, reduction in healthcare costs, and new treatment methods facilitated by therapeutic vaccines.
What are regulatory bodies in vaccine development and production?
Regulatory bodies overseeing vaccine development and production include the FDA (Food and Drug Administration) in the U.S. and the European Medicines Agency (EMA) overseeing and regulating vaccine development and production, particularly within the European Union. The CDC (Centers for Disease Control and Prevention) is another key regulatory body in the rise of endemic and pandemic events. The These organizations play a crucial role in ensuring the safety, efficacy, and compliance of vaccines within the healthcare system.
How are vaccines produced?
Vaccines are produced through a complex process involving several key steps. First, antigens or components of the pathogen are identified. These antigens can be cultivated in bioreactors using specific cell lines. Subsequently, the purified antigens undergo formulation, often with adjuvants to enhance the immune response. The purification process ensures the removal of impurities, resulting in a high-quality vaccine that stimulates the production of antibodies, crucial for effective immunization.
What is the process of creating a vaccine?
Creating a vaccine involves a defined process that typically includes identifying antigens, conducting pre-clinical research, performing clinical trials, and obtaining regulatory approval. This process aims to ensure the safety, efficacy, and immunogenicity of the vaccine before it is manufactured and distributed for public use.
What is the adverse reporting system?
In pharmacovigilance, the adverse reporting system is a crucial mechanism for individuals, healthcare professionals, or manufacturers to report any adverse events or side effects associated with vaccines or medications. It plays a vital role in monitoring and ensuring the safety and immunogenicity of vaccines, as well as other biopharmaceutical products. By collecting and analyzing data on potential risks, this system contributes to the continuous improvement of public health and the overall safety profile of these medical interventions.
Read more about vaccine manufacturing
- Vaccine platforms, https://ncirs.org.au/vaccine-platforms, Published 2023
- Understanding Six Types of Vaccine Technologies, https://www.pfizer.com/news/articles/understanding_six_types_of_vaccine_technologies, Published
- Vaccine manufacturing, http://dx.doi.org/10.1016/B978-1-4557-0090-5.00019-7, Published 2013-10-18
- The top 10 vaccine manufacturing companies in 2024, https://www.extrapolate.com/blog/top-10-manufacturers-in-vaccines-market-2024, Published 2024
- The complexity and cost of vaccine manufacturing – An overview, http://dx.doi.org/10.1016/j.vaccine.2017.06.003, Published 2017-06-22
- Upscaling vaccine manufacturing capacity - key bottlenecks and lessons learned, http://dx.doi.org/10.1016/j.vaccine.2023.05.027, Published 2023
- Regulatory Aspects of Vaccine Development, Manufacture, and Distribution, https://www.ncbi.nlm.nih.gov/books/NBK236432/, Published
- Manufacturing, safety and quality control of vaccines, https://www.who.int/news-room/feature-stories/detail/manufacturing-safety-and-quality-control, Published 2020
- Current GMP standards for the production of vaccines and antibodies: An overview, http://dx.doi.org/10.3389/fpubh.2022.1021905, Published 2022-11-03
- Facts About the Current Good Manufacturing Practices (CGMP), https://www.fda.gov/drugs/pharmaceutical-quality-resources/facts-about-current-good-manufacturing-practices-cgmp,, Published 2023
- The complexity and cost of vaccine manufacturing – An overview, http://dx.doi.org/10.1016/j.vaccine.2017.06.003, Published 2017-06-22
- Current GMP standards for the production of vaccines and antibodies: An overview, http://dx.doi.org/10.3389/fpubh.2022.1021905, Published 2022-11-03
- , Published 1970-01-01
- , Published 1970-01-01
- Is Sustainability Possible With Single-Use Technology?, https://www.bioprocessonline.com/doc/is-sustainability-possible-with-single-use-technology-0001, Published 2015
- Single-Use Bioprocessing Technologies Enabling More Rapid Vaccines Production, https://www.americanpharmaceuticalreview.com/Featured-Articles/596309-Single-Use-Bioprocessing-Technologies-Enabling-More-Rapid-Vaccines-Production/, Published 2023