Downstream processing with single-use systems
Table of contents
ShowOne would think that a sector like the fast-paced biomanufacturing industry could not get any faster. Yet, increased speed-to-market and ever more efficient manufacturing continue to drive product and process development. This is why single-use technologies have become increasingly popular – they are the key to flexible and modular processing systems, replacing rigid multi-use stainless-steel systems in all bioprocessing unit operations.
Downstream processing – steps and requirements
Downstream processing describes a biochemical engineering process that deals with the recovery and purification of substance cultivated and grown of cell culture in the previous process step using fermentation. The purpose is to isolate, purify and concentrate the previously synthesized product by means of filtration, crystallization, precipitation, centrifugation and/or chromatographic methods.
Biopharmaceutical downstream processing is applicable in the manufacturing process of biopharmaceuticals, such as mAb (monoclonal antibodies), various vaccines, recombinant antibodies or enzymes.
Steps in downstream processing
All downstream purification steps have the goal to recover purified substances to be used in biochemical products.
- Step 1: Harvest and filtration – this serves the separation from bulk debris with the intent to optimize yield and quality.
- Step 2: Primary capture – aims to minimize impurities and by-products after all cell debris has been removed.
- Step 3: Buffer exchange and concentration – molecules are separated using ultrafiltration based on membrane pore size or molecular weight cutoff, while diafiltration services the exchange of products from an existing buffer to a new buffer or a final formulation buffer.
- Step 4: Purification – residual impurities are removed, while at the same time as much product as possible is retained, with methods like polishing chromatography and virus inactivation.
In most cases, water is the main impurity, and solvent extraction, adsorption, ultrafiltration, and precipitation are some of the unit operations involved.
As an optional additional step, downstream may include formulation activities, signifying the transition from drug substance to large-scale drug product (DP) manufacturing, bringing the product molecule from an environment, solvent or other physical state into a form suitable for clinical administration.
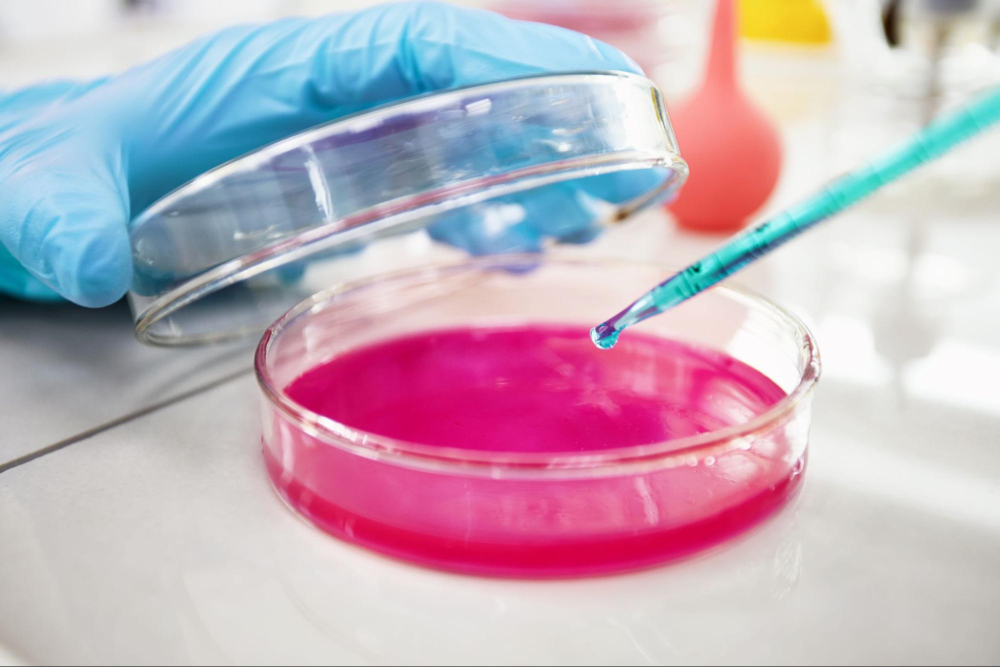
Where do single-use systems come in?
Single-use solutions have been used in both upstream processing and downstream processing. In addition to offering benefits in filtration and sampling, they can help reduce the risk of contamination. Thanks to its process flexibility, single-use technologies foster process optimization, serve process optimization and facilitate an efficient workflow that can prevent bottlenecks. This allows for scale-up if and as required.
Today, most downstream processing (DSP) unit operations rely on single-use systems, as they offer a number of undisputable benefits, which we will take a closer look at in the next paragraph.
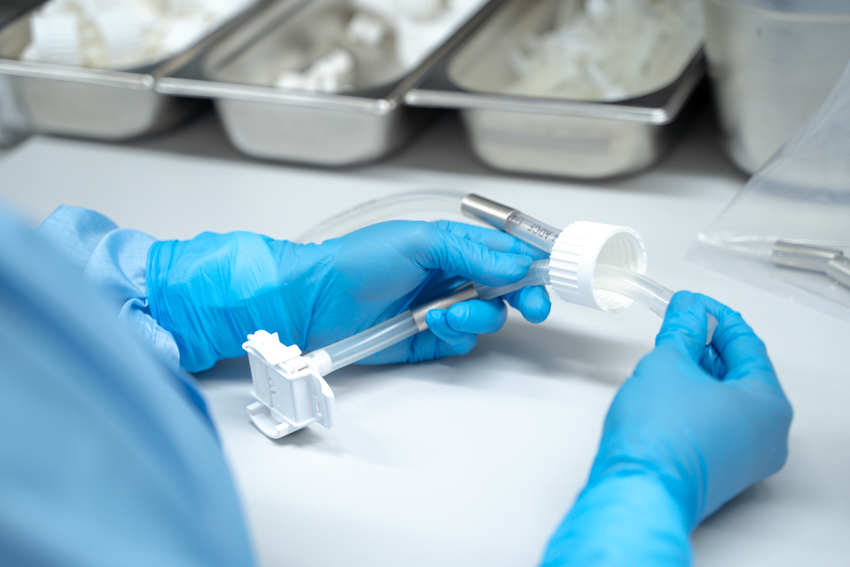
Benefits of using single-use systems in downstream processes
One of the main benefits is speed of implementation and adaptation, combined with process versatility and flexibility, ease of use and the possibility to implement them without intense regulatory obstacles, all of which are crucial in the fast-paced biotechnology and biopharmaceutical industries. Single-use equipment provides advantages across all steps of downstream processing, be it in terms of filtration systems, buffer preparation systems or sampling and dispensing systems. Coupled with single-use bioprocess containers, single-use mixers can increase a DSP suite’s throughput as there is no more need for resource-intensive cleaning operations, such as CIP and SIP. Without CIP and SIP, the ecological footprint of the biopharmaceutical production process is reduced.
However, while the use of single-use systems for downstream operations is clearly growing, there still are limitations. Chromatography in general (affinity chromatography, hydrophobic interaction chromatography, ion exchange chromatography) has been the last purification process to move into disposable equipment, not least because the industry’s adoption of pre-packed, limited-use chromatography has been slow. Single-use technology can help address column packing and minimize the risk of bioburden.
What are challenges with single-use technology in downstream processing?
Along with the ever increasing demand for bioreactors, the constraints on downstream processing keep increasing. The efficient recovery and purification of antibodies from cell culture medium is a critical part of the production process. Partnering with a third-party antibody expression specialist can contribute to maximizing manufacturing output.
Lorenzo De Benedictis, Product Line Manager at Single Use Support, sees a realistic chance of single-use technologies solving about 90% of all challenges, ideally including the issue of material compatibility. Even though single-use containers are currently limited to 2,000 L of cell culture bioreactor capacities, there are ways to navigate around it. “Some of our customers split up, for example, a 12,000 L vessel into 2,000 L single-use bioreactor bags and, therefore, they are able to harvest continuously.”
Single Use Support offers solutions for downstream processing
For processes including highly sensitive aggregates, where product loss caused by impurities can be very costly, it pays off to implement flexible filtration and purification steps (for instance intermediate or protein purification) and to have systems in place that are accurate and automated. End-to-end solutions based on single-use technologies are agile and flexible, allowing for scalable chemical engineering and manufacturing processes. At the same time they offer comprehensive logistics approaches to prevent product loss during storage and shipping while addressing regulatory and validation issues that the life sciences are faced with.
Single Use Support has created a line-up based on single-use technologies that provides specialized products for various steps in downstream processing and solutions. This not only includes RoSS.FILL for fully automated aliquotation in advanced fluid management, but also RoSS.PADL for drug homogenization, IRIS SMPL for aseptic sampling and various customized and vendor-agnostic single-use assemblies.