Single-use technology & the implementation in biopharma
Table of contents
ShowNot least since it was recommended by the FDA as a way to reduce the still-existing risk of contamination of bulk drug substance, single-use technology based on the application of disposable components has found validation and has seen a rise in popularity in the pharmaceutical industry.
In light of this commendation, it comes as no surprise that this relatively new technology, first employed in the 1990s, has been and still is being adopted by an increasing number of players in the biopharma field – and is here to stay. Manufacturer-independent flexibility rather than the utilization of rigid and sluggish technology is the way forward in bioprocessing and biopharmaceutical production.
Current trend towards Single-Use Technologies
It is a well known fact that this industry is changing incrementally due to heavy regulatory burdens. While some single-use products, such as tubing and filter cartridges, have been in use for quite some time and their markets approaching saturation, several products were just recently introduced on commercial scale, e.g. disposable chromatography devices, media bags and tangential flow filtration devices. Their markets even showed double-digit growth rates in 2017. (Source: American Pharmaceutical Review)
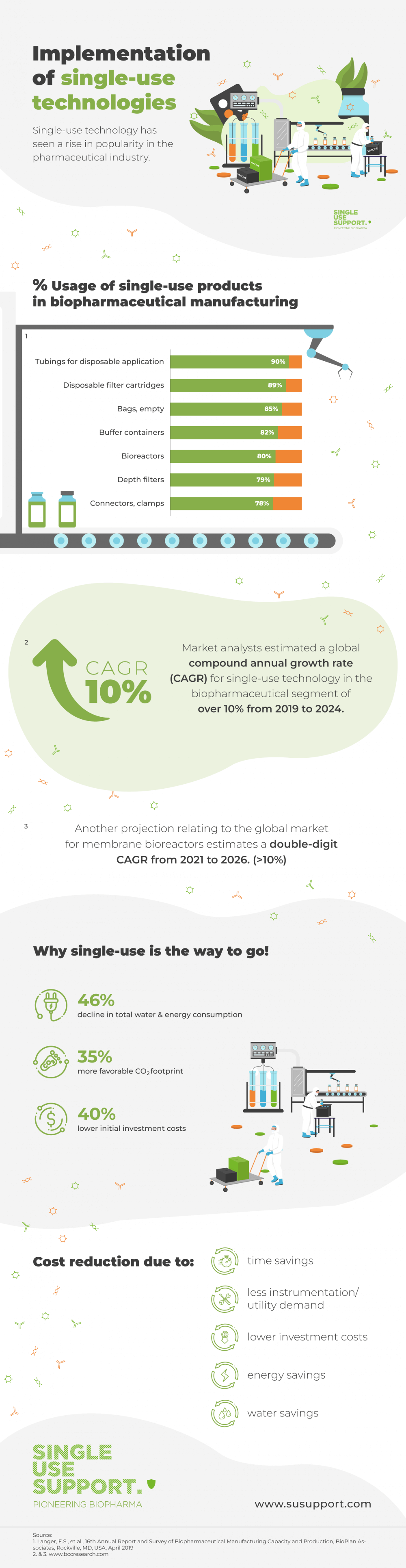
Market analysts estimated a global compound annual growth rate (CAGR) for single-use technology in the biopharmaceutical segment of over 10% from 2019 to 2024. (Source: BCC Research)
Another projection relating to the global market for membrane bioreactors estimates a double-digit CAGR from 2021 to 2026. (Source: BCC Research)
Those are astonishing and especially promising numbers and would help improve the biopharma industry, not only in making production smarter and cheaper, but also by keeping supply chains intact.
Adding to that, this shows, today, single-use systems challenge the procedure of re-using stainless-steel equipment, which was an established technique in biopharmaceutical manufacturing, that entails complex cleaning processes to avoid risks such as cross-contamination or the failure to achieve sterility.
Single-use systems in Biopharma - an overview from the beginning
Single-use technologies have been in use since the early 1990s. Due to the need to move ever-increasing volumes of serum, biotech labs initially started using plastic bags common in the food industry.
Once the serum arrived at the manufacturers’ labs packaged in plastic bags, it didn’t take long for them to start imitating and adopting this type of container for their high-quality drug substance. Consequently, this brought with it the need for specific technologies geared towards single-use consumables that were both flexible and scalable.
While avoidance of tedious and costly cleaning and maintenance processes were the initial drivers for the development of single-use technologies, they are now not only seen as more cost-effective, but also as a safer alternative to traditional technologies. Since then, major milestones have been achieved.
In the early 2000s, aseptic disposable sampling systems have been introduced. Another milestone was the introduction of single-use bioreactors. Manufacturing facilities realized the immense advantages of single-use technology for the pharma industry, e.g. in gene therapy. Since then, many single-use facilities have been opened and counting. For example, in 2017 already 66% of pharmaceutical companies preferred single-use bioreactors over the traditional stainless steel bioreactors.
And the figures from the previous paragraph on the trend toward single-use technology show that the development is still continuing. But why exactly are so many manufacturers switching to single-use systems?
Main factors for the use of single-use technology
With the containers and the fluid pathways being preassembled and guaranteeing sterile handling of pharmaceutical goods, the production-line process picks up speed and allows for an increased output in shorter intervals. GMP (Good Manufacturing Practice) can be guaranteed and, thus, adding another benefit. One of the key factors of single-use technology, however, is that its employment provides for a streamlined process that is both monitored and scalable.
The adoption of single-use technologies becomes more popular and the utilization of such technologies in the scope of labs and studies increases, so do the volumes produced using this relatively new and flexible method. This calls for innovative solutions, as the scale-up from miniscule amounts (small-scale) required in labs to blockbuster production of several thousand liters can prove difficult and problematic.
One and the same state-of-the art process and technology can be used in all areas, be it for lab production for testing or study purposes or blockbuster production of approved and certified compounds. In addition, single-use platforms allow for the optional integration of components such as filters where and as required.
Financial Advantages of single-use technologies
As a result of the application of SUT, the manufacturers can rely on financial assets. With the switch to single-use tubing assemblies, costs are reduced in many ways.
- Cost reduction through time savings
- Cost reduction through energy savings
- Cost reduction through water savings
- Less instrumentation/utility demand required
- Lower investment costs
- more capacities can be purchased with limited start-up budget
- investment sum to be amortized is lower
- overall, variable costs are lower
The reduction in costs is just one of the numerous advantages of using SUT in biopharmaceutical manufacturing. The simplified application also promises advantages for the user. Find all the benefits of single-use systems in the specific fields of application in the following paragraphs. (Source: NNE, Beroe)
Agility and scalability of single-use platforms
While conventional stainless-steel systems have been established as the basis of safe and reliable manufacturing processes for both classical pharmaceuticals and advanced biologics over decades, they are not exactly flexible and agile. However, the complex processes involved in the production of biopharmaceutical compounds require great flexibility, while they should at the same time be cost-efficient.
This is where disposable single-use components come into play: Not only do they reduce the risk of (cross) contamination, they are also less expensive, easier to use and provide more flexibility than traditional processing technologies.
The advantages that set them apart from the traditional and rather unwieldy stainless-steel systems and cryovessels speak for themselves, even at a glance:
- Increased flexibility:
Tubing and filters are made of flexible materials such as plastic or silicone and can be modified easily and quickly, as opposed to rigid stainless-steel pipes. - Reduced cleaning requirements:
While steel components need to be cleaned after every batch, single-use equipment comes pre-sterilized and ready to use, leading to- increased turnaround times and
- reduced risk of cross-contamination
- Decreased footprint and costs:
Single-use technology requires less equipment to be stored on-site, plus the omission of cleaning and maintenance further reduces costs and storage requirements
Potential limitations of single-use technology
There are still hurdles in single-use systems for the biopharma
While single-use technologies still have their limitations, ongoing research and development are providing new and improved solutions at an accelerated rate. Until recently, single-use bags were the main source of constraint, as they could only handle small to medium-sized volumes of highly valuable drug substance.
However, advances in bioprocessing technology, notably a steadily increasing upstream productivity, are consistently pushing the limits. Single-use platforms can now accommodate up to 2,000 L; especially when having multiple systems running in parallel, they can compete with stainless steel vats and systems when it comes to producing enough to supply commercial markets.
So even though to date nearly all commercial manufacturing of biopharmaceuticals has involved the use of unwieldy stainless steel-based tanks and facilities, this is starting to change. And it is expected to transform the industry even more dramatically in the near future, with some new facilities implementing multiple 1,000 to 2,000 L bioreactor-based single-use systems in parallel in order to manufacture volumes comparable to traditional stainless-steel production lines.
Another reason for increased adoption of single-use can be found in the growing trend and need for personalized therapies such as CAR-T cell therapies and CGTs (short for Cell and Gene Therapies) that are based on the patient’s very own cells. The small amounts required for such treatments could never be processed in massive tanks and single-use platforms offer the perfect solution, both in terms of adaptability and scalability.
Bottlenecks and solutions for single-use technologies
In an annual survey of biopharmaceutical manufacturing professionals conducted by BioPlan Associates, the potential “breakage of bags and loss of production material” was still cited as a major disadvantage of single use systems by 46.2% of respondents.1
It remains one of the main weak points of single-use, but there is a solution:
The very nature of single-use bags for biopharmaceutical purposes, which are generally made of a high-quality, yet thin and sensitive plastic membrane, makes them prone to breakage and ruptures caused by external stress and impact. This can lead to contamination and loss of highly valuable drug substance.
In order to eliminate this risk, Single Use Support has developed the so-called RoSS.shell that offers a protective sleeve for filled and frozen single-use bags protection of any size. It is made up of a layer of soft 3D foam and a protective sleeve of robust and compact stainless steel to keep the content safe from external impact. It is just the last piece to make the entire puzzle called “single-use” complete. To find out more about the RoSS.shell and its compatibility with our single-use technology systems, click the button below.
Solutions based on single-use systems
Single Use Support's end-to-end solutions are based on single-use consumables and platform systems for controlled freezing and thawing, ultra cold storage and automated filling and draining.
In the next paragraphs we present some solutions for optimal cold-chain handling or fill and filtration applications with the advantages of using single-use technologies.
Automated bulk filling systems for monitored single-use processes
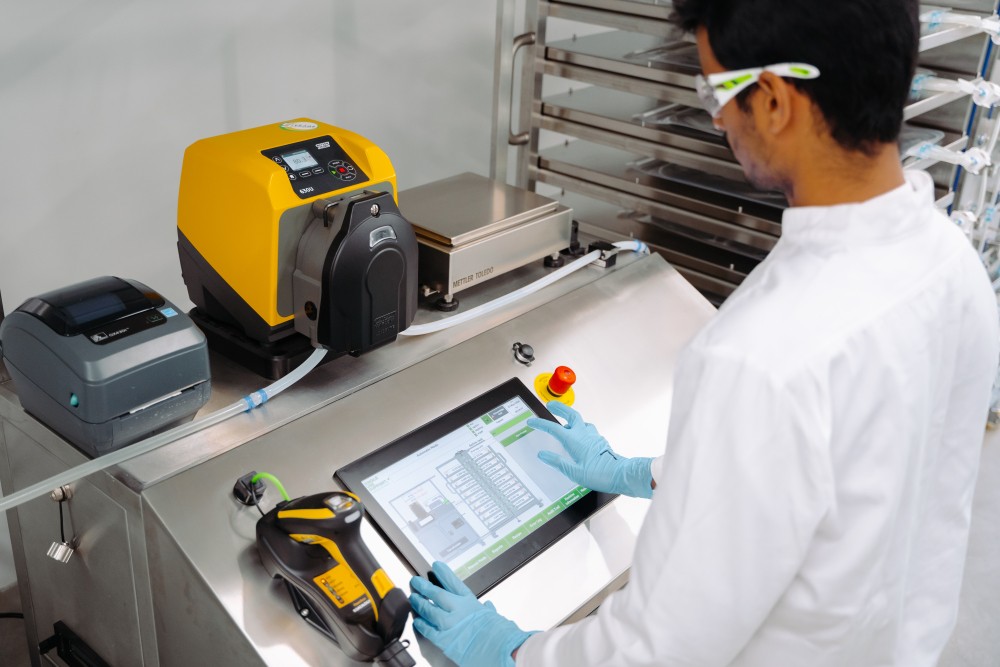
The latter, namely a decreased footprint of biomanufacturing at better costs, is one of the key advantages to be considered when contemplating a change to single-use systems: With their relative compact size automated filling systems for single-use bags, both for bulk and lab purposes, are a space- but also cost-saving and time-efficient solution to handle the entire pharmaceutical logistics process, including filtration, filling as well as freezing and thawing – simply put, they are the way forward.
Single-use bioprocess containers, which are the initial cause for the emergence of and the basis for all single-use technologies, also score on several levels: When empty, single-use bags are compact and require very little storage space, especially when compared to bulky cryovessels or bottles.
In addition, they are widely available in a range of sizes and capacities to cover different needs. Single-use technologies are generally compatible with bioprocess containers of any brand and size, without the need for complicated and tedious adaptations or adjustments.
Unlike stainless-steel systems that incorporate fixed components such as connectors, filters and pipes, single-use systems make use of pre-sterilized disposable parts that require no cleaning.
Flexible single-use filtration systems
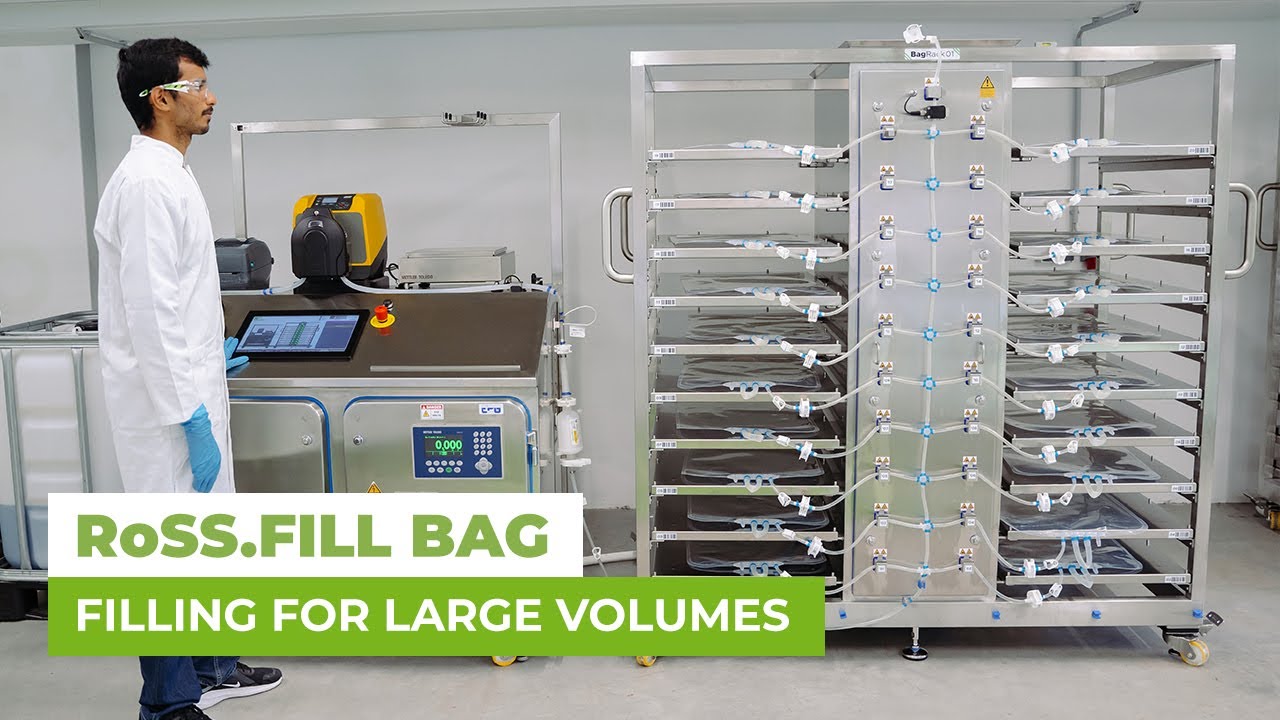
In environments and industries where sterility is the norm, filtration becomes an important part in the handling of drug substances. A number of applications performed in clean rooms, such as the recovery of antibodies or the reduction of bioburden after cell harvest, require large filtration areas.
And as different substances have different requirements, not every filter may be suitable for every substance – adding yet another challenge calling for a flexible solution. Due to increasing batch volumes from pilot to manufacturing scale, production processes become increasingly complex. This can require filter areas varying in size and covering more than 100 square feet, as well as the incorporation of one or numerous filter capsules and connectors.
In terms of handling and efficiency, the ideal solution would be a flexible filtration system that can be integrated into existing filling, freezing and thawing platforms. Single Use Support offers just that, and with filters coming not only in a choice of sizes but also for different pore sizes, this ready-to-use application not only minimizes time and effort but – above all – the risk of contamination.
Advanced cold chain handling and storage with SUT
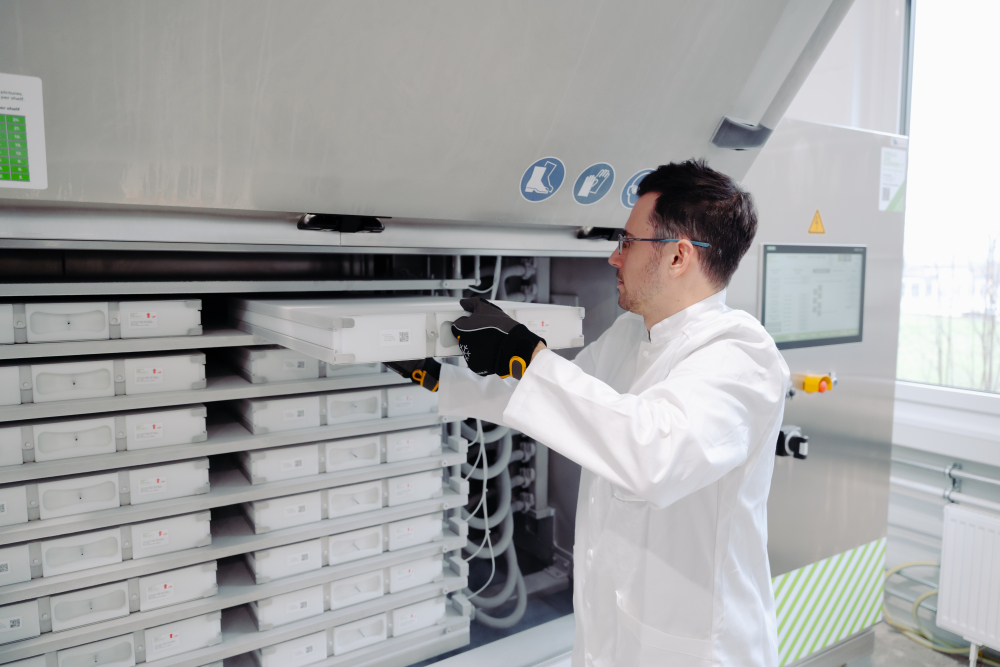
Single-use bioprocess containers have also proven to be the ideal approach for the entire cold-chain process, including storage. They are a versatile and multilateral solution for a flexible – and above all scalable – freeze-thaw process, plus they add to the quality of the frozen goods.
Plate freezing allows for a speedy and at the same time controlled freezing of the valuable liquid solution contained in the single-use bag: Direct contact between freezing plates and the bag leads to a more consistent freezing of the single-use bag’s content at a higher velocity. Slow freezing rates of traditional freezers, on the other hand, lead to the formation of large crystals that can cause friction and will increase cryoconcentration which impacts the quality of the drug substance.
However, due to their sensitive nature, single-use bags require some sort of protection, not least during shipping. Within the freezing process temperatures between -20 °C (-4°F) and -80 °C (-62°F) can occur. This can cause assembly components with inadequate protection to break and single-use bioprocess containers to rupture, which will invariably cause an excessive waste of valuable drug substance. (Source: BioProcess International)
Single Use Support has developed the stainless-steel RoSS shell to protect single-use bags during the freezing process, the stainless steel not only acting as a protective shield but also offering the best possible temperature transfer from freezer to bag to liquid.
On the inside, the bag is further embedded in a layer of soft 3D foam which hardens at approx. -20°C (-4°F) which fully immobilizes the single-use bag. The shell is tamper-proof, so the bag contained within cannot be accessed during the entire controlled freezing and logistics process.
Single-use technology - independent choice of the supplier
Traditional systems that have been established over the years usually require all components from a single source; as a consequence, pharmaceutical manufacturers become dependent on their supplier.
Changes are near impossible or require a complete refit, while modular single-use technologies are compatible with a range of brands, be it for single-use bioprocess containers or filters. They offer a versatile solution both for blockbuster production and lab purposes and can be modified and scaled as required, but without the need of adapting entire processes or systems.
Single-use solutions leave room for constant improvement, so it can be adjusted and customized to newly arising needs and requirements. It is the perfect basis for an agile and flexible technology that keeps up with the times.
- American pharmaceutical review™, https://www.americanpharmaceuticalreview.com/Featured-Articles/354820-Biopharmaceutical-Manufacturing-is-Shifting-to-Single-Use-Systems-Are-the-Dinosaurs-the-Large-Stainless-Steel-Facilities-Becoming-Extinct/, Published 23.10.2018