Gene therapy manufacturing - 5 requirements to scale up
Table of contents
Show
Gene therapy manufacturing continues to cause a stir in the biopharma industry. Gene therapies have become a highly promising field of groundbreaking next generation treatment approaches that use personalized therapies for rare diseases and allow innovative procedures such as in vivo therapies based on viral vectors (e.g. adeno-associated viruses, AAV).
Despite the outstanding potential demonstrated by hundreds of clinical trials and an increasing number of FDA approvals, gene therapy manufacturing comes with unprecedented challenges. The underlying science was established during therapy development, but the manufacturing technology is highly complex, and in autologous gene therapy every batch is individually tailored for each patient.
The logistics of the supply chain and distribution networks for individualized medicines is breaking the traditional paradigm for biologics of multi-kilogram to multi-ton batch manufacture of therapeutics and subsequent inventory keeping.
This article will highlight five key factors that will be crucial in overcoming the challenges of upscaling gene therapy manufacturing with single-use technology.
1. Cooperation and partnership
Cooperation and partnerships are key in gene therapy products manufacturing. In recent years, unprecedented supply chain challenges pertaining to CGT (cell and gene therapy) manufacturing became clear and outsourcing of distinct steps and processes has been a worthwhile tactic to ensure an efficient, high quality manufacturing process.
Most companies are not in the position to encompass research, development, regulatory affairs, administration, and at the same time performing process development and scaling up novel production processes, including single use technology.
Partnerships with reliable contract development and manufacturing organizations (CDMOs) keep operations streamlined and increase profitability.
CDMOs provide biotech companies with available commercial manufacturing infrastructure, skilled and experienced workers and the necessary focus on key competences.
They can often rely on dependable raw material suppliers. Continuous open and clear communication between the partners is of utmost importance to overcome the hurdles of CGT manufacturing lifecycles. Efficient communication channels facilitate the characterization of attainable common objectives, definition of milestones, and meeting realistic timelines.
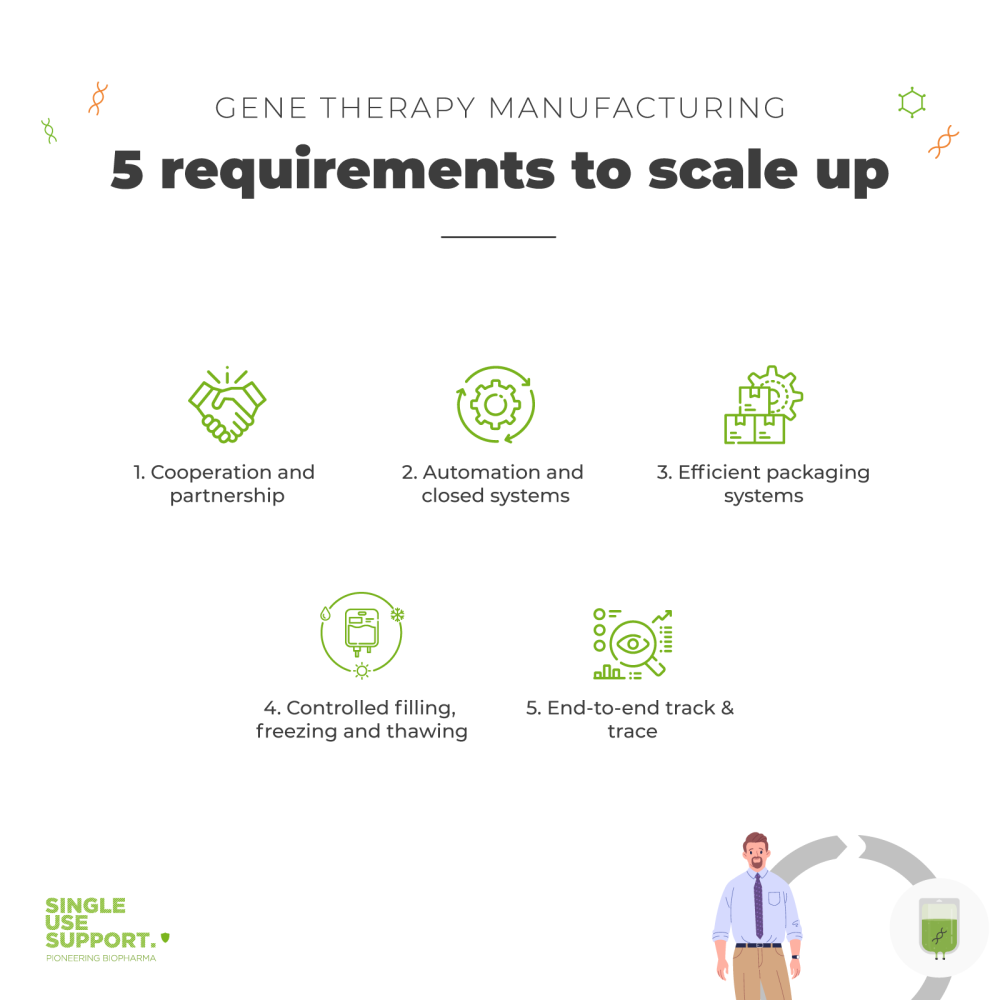
2. Automation and closed systems
Gene therapy is a sensitive technique that involves altering genes in human cells that consist of sensitive protein structures with large surfaces. They are often administered intravenously or applied directly to the affected organ. Moreover, cell and gene therapies are prime examples of personalized medicine, since each batch is produced solely for one individual patient. Therefore, any confusion during production, packaging or transport has serious consequences.
Gene and cell therapy manufacturing companies strive to eliminate these process risks by removing manual steps that are prone to human error and contamination.
Automated process workflows during downstream and upstream are preferred to protect products from contaminants as much as possible by using closed systems and sterile fluid transfer technologies to and from bioreactors. These methods minimize exposure to the environment and avoid the need to manually move containers between staff.
Having a closed system in place helps to make gene therapy manufacturing more efficient and increases safety for the patients. In addition, heavy use of automation and closed systems in manufacturing facilities of course facilitates adherence to GMP and cGMP (good manufacturing practice) requirements.
3. Efficient packaging systems
Due to the sensitivity of the products towards e.g. temperature and critical time constraints (“vein-to-vein time”, fast progressing diseases), several requirements must be met by the packaging systems used in gene therapy manufacturing.
In general, CGTs must be stored and shipped under cryogenic conditions. Therefore, bags and containers are required to withstand freezing cycles and keep their physical properties across large temperature ranges (between room temperature and down to -150 °C).
For instance, containers should not lose their mechanical properties at cryogenic temperatures in order to minimize the risk of container failure and subsequent loss of product. Single-use bags made of high quality plastics have a proven track record to meet these requirements.
The tight schedules for manufacture and delivery of CGTs mandates the use of air freight for parts of the supply chain and involves meeting several regulatory requirements (e.g. by the International Air Transport Association). For instance, containers and closures must withstand pressure differences to prevent leakage during flights. Air-free single use bags in specialized secondary and tertiary containers are efficient solutions.
4. Controlled filling, freezing and thawing
Gene therapy manufacturing workflows involve time-consuming processes, and production intermediates have to be stored between individual steps at low temperatures to maintain the viability of the genetic material and/or cells.
It is well known that slow freezing of biopharmaceutical solutions and suspensions (e.g. plasmid DNA, RNA, proteins, vaccines and cell lines) decreases the quality of the drug product. One reason is the accumulation of drug substance in the liquid phase during freezing and subsequent irreversible aggregation of the drug material..
Rapid freezing and thawing reduce the propensity for quality loss during storage. The use of dedicated freeze-thaw platforms for single use bags is a flexible and efficient way to achieve controlled freezing with minimal loss of active product.
5. End-to-end track & trace
Because autologous CGTs are individualized biopharmaceuticals, every single batch is designed for one specific patient. Any confusion may lead to at best an ineffective treatment or at worst very serious toxic side effects. Therefore, it is of crucial importance for biotech companies to have systems in order that eliminate the possibility of such incidents.
End-to-end monitoring of each batch and real-time tracking of manufacture and shipping process is an effective way to overcome this challenge.
Single Use Support provides RFID-tags (radio-frequency identification tags) for their products such as the protective shell for small single-use bags, RoSS.KSET, and enables the manufacturers to monitor and document the product on its way through manufacturing sites of contract manufacturing until when patients receive their advanced therapy at healthcare centers.
RoSS.KSET is fully designed for single-use platforms such as the Fill-Drain platform, Freeze-Thaw platform and Cold Chain Shipping containers. The CGT bag protection system automatically communicates with these products and collects real-time data that is critical to document the quality of processes, e.g. filling volume, filtration speed, temperatures, mechanical impacts etc.
Single Use Support’s integrated process system of automated data collection allows for easier cGMP process documentation and optimization, facilitates meeting of regulatory requirements and provides transparency throughout the entire manufacturing process.