Biopharma supply chain – 7 risks to be aware of
Table of contents
ShowHow can biopharma supply chain risks be minimized so that patients can be provided with their medications? The supply chain is threatened by many challenges and modern types of medications such as cell and gene therapies (CGTs) aggravate many issues. Traditional biologics consist of high-tech drug substances and their production involves the pinnacles of life science achievements.
Active pharmaceutical ingredients (API) are quite sensitive and their handling is in most cases not straightforward. Additionally, individualized medicines like advanced therapies need a completely different supply chain strategy. On top of that, sterility throughout drug manufacturing is required.
This article will discuss seven risks between upstream and downstream processes in biopharma supply chains for patients and show how single-use technology in drug substance management can be used to mitigate many issues and at the same time increasing efficiency of operations.
Risk 1 – Loss of drug substance at the manufacturing site
Loss of drug substance is painful: The full amount of the cost of goods (COG), i. e. raw materials, labor costs, machine operation time etc. to produce the drug product has already been spent but none of its commercial value can be retrieved.
The reasons for loss of API or drug substance at the manufacturing site are numerous: human error, machine failure, malfunctioning components, faulty containers or other external mechanical influences. While many occurrences of errors along biopharmaceutical processing can be reduced by adapting to robust production processes, some residual risks remain when using traditional equipment.
The implementation of reliable single-use technologies for liquid handling, fill and finish processes and bioprocess containers minimizes these risks.
Biopharmaceutical therapeutics are most vulnerable during transport to the site of use. The majority of such products require stringent cryo-logistics and careful handling. The risk of container failure (rupturing of bags or breakage of bottles) is real, but can be mitigated by use of dedicated protective transport cassettes.
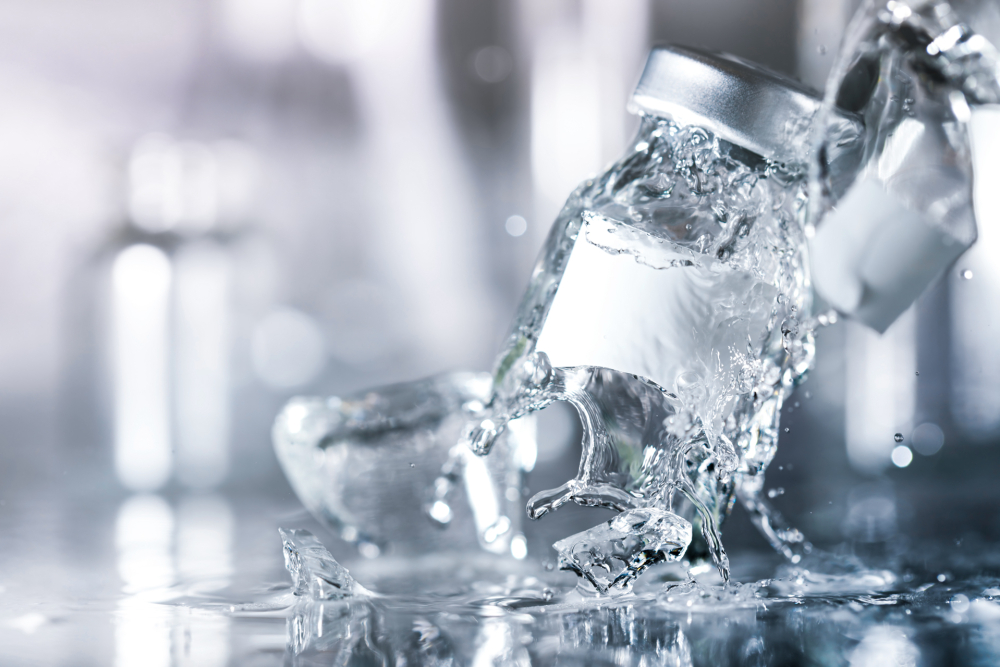
Risk 2 – Handling with toxic ingredients in biopharmaceutical manufacturing
While biopharmaceuticals are lifesaving tools in the toolbox of our healthcare system, especially treatments for cancer like ADCs (Antibody Drug Conjugates) are potentially toxic and hazardous during manufacturing, and the risk of exposure for workers at the manufacturing site, during transport or for the general public must be minimized.
Risk mitigation starts at the manufacturing site by using closed systems to handle intermediates and formulated drugs to prevent contamination of the products as well as exposure to aerosols, splatters, fumes etc.
An efficient way to implement such strategies is by deploying closed liquid management systems. Disposable end-to-end systems have the benefit of being delivered already sterilized and ready to use. After a manufacturing campaign, the used components can be safely contained and handed over to waste management partners, thus avoiding the need to flush, clean and re-sterilize equipment.
Risk 3 – Contamination of drug substances
Contamination risk assessment is of utmost importance in securing a steady biologic drug supply. Basically, two sources of contaminations are conceivable:
- impurities from the manufacturing process itself: cell remnants, side products, reagents etc contaminations
- impurities from the outside: impurities from the employed equipment and from the environment.
Nowadays, proper contamination risk management takes care of most of these issues: cleaning and sterilization protocols, efficient purification methods and their validation and the use of clean rooms and closed systems for liquid handling are the norm. But some solutions are better than others: cost-efficiency, ease of use, sustainability are aspects that have to be considered.
Innovative single-use technologies in the biopharma industry allow operators to obtain samples from processes in situ in aseptic fashion, to order custom made, pre-assembled liquid handling systems and to deploy the very same bioprocess bag in the huge temperature range from -196 °C to +50 °C.
Risk 4 – Interruption of the cold chain along the supply chain
The risk of cold chain disruption gained public awareness during the COVID-19 pandemic, when for the first time large amounts of COVID-19 vaccine had to be delivered under stringent cryo-conditions over large distances. Prior to that, no capable infrastructure was in place, which initially led to interruptions of supply chain, vaccine and drug shortages and intense media coverage for the pharmaceutical industry due to high public attention and involvement of political stakeholders.
Keeping reliable cryo-conditions along the pharmaceutical supply chain is a challenge in itself, and many biopharmaceuticals require tight thresholds, which is aggravating the issue. Innovative solutions were inspired by the increased need for supply chain resilience: dedicated single-use and multi-use equipment for shipping biopharmaceuticals under stringent cryo-conditions for several days were developed.
Some embodiments of these concepts allow for real-time monitoring of crucial parameters like temperature and impacts thus enabling pharmaceutical companies to permit decision-making and initiate corrective measures to save the shipment of frozen drug substances.
Another issue is the use of suboptimal freeze and thaw processes, which has been shown in many case studies to severely affect the quality of molecular biopharmaceuticals as well as cellular gene therapies. Drug manufacturers are just now beginning to implement the use of intelligent freeze and thaw platform systems to ensure optimal active freeze and thaw processes, offering high degrees of automation.
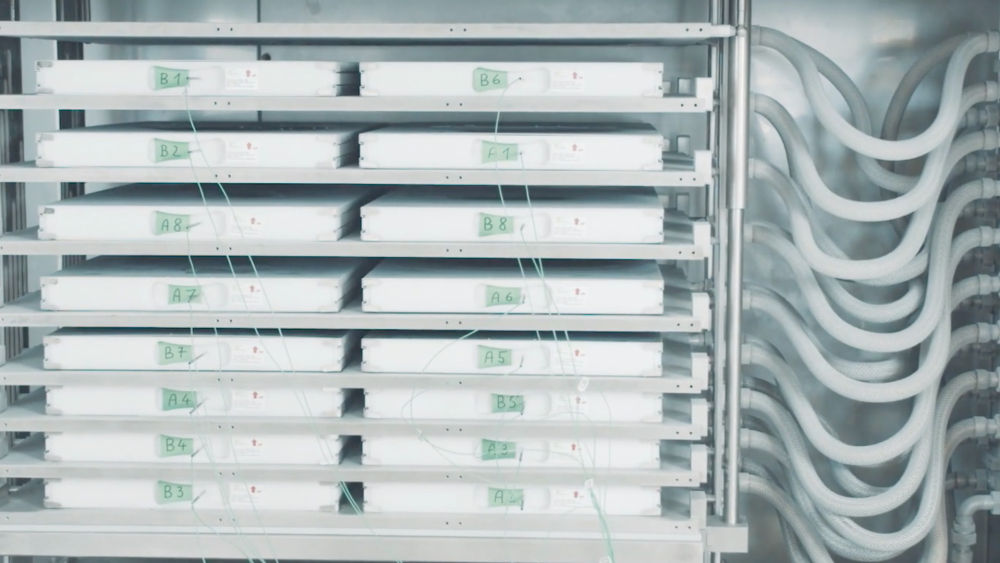
Risk 5 – Failure to meet compliance standards
Biopharma supply chains must conform to high quality standards: Regulatory bodies such as the US FDA require the pharma industry to adhere to strict constraints and record keeping of key parameters during pharmaceutical manufacturing, also when outsourcing to providers like CDMOs in India, China or any other country. Should a pharma company fail to comply with these regulations, entire batches of valuable products might be useless.
While the cleaning and sterilization of production equipment is a given, cGMP guidelines demand extensive record keeping of these processes. Therefore it is paramount to employ the kind of equipment and consumables that allow for the best manner of conducting operations: FDA approved single-use equipment.
Risk 6 – Loss of efficiency
With the advent of innovations like advanced therapies, the efficiency of biopharma supply chains must be assessed from entirely new angles. Increased stocks do not alleviate any bottlenecks if the medication is personalized for one patient. These drugs have a very short product life cycle and traditional supply chain strategies cannot be applied for personalized therapies.
Individual tissue samples must be transported to dedicated manufacturing plants and after production the finished drugs must reach the patient at the site of administration. The expenses during such operations easily skyrocket beyond profitability. The implementation of single-use technologies facilitates the streamlining, parallelization and automation of many steps along the way to save time and resources.

Risk 7 – Failure to deliver timely
Failing the timely delivery of a complete order – on time in full (OTIF) – might constitute a breach of contract, thus damaging the reputation of a supplier and leading to penalties. In addition to that, shortages in drug supply can have drastic consequences for patients that are in need of one specific product at a set date.
All of the aforementioned risks might contribute to failing OTIF deliveries but administrative issues might play a role as well. The procurement of raw materials and consumables as well as the accurate forecasting of market demands play a critical role. Thus, ensuring the supply chain visibility down to sub-providers of materials and services are becoming increasingly important in supply chain risk management.
Minimizing risks with automated single-use systems
The importance of single-use systems in mitigating pharma supply chain risks is continuously growing. They offer convincing solutions to issues regarding product quality, compliance, product purity and efficiency of operations. This is implemented in the form of efficient disposables, being adaptable to leaner and more robust processes and high-throughput equipment.
They enable process engineers to set up processes with a high degree of automation and parallelization of unit operations. Single-use technologies facilitate the implementation of Pharma 4.0, using cloud solutions to collect, process and analyze data in real time.
Single Use Support has developed an entire product lineup based on single-use technologies, designed to provide supply chain security and flexibility at every production step. With automated fill/filtration platforms, several risks in liquid drug substance management can be circumvented, while Single Use Support’s plate-based freeze-thaw solutions allow for fast freezing processes for maximum product stability.
The product portfolio of Single Use Support is completed by solutions for safe storing and shipping of frozen drug substances. They provide protection against variations in temperature as well as physical stress for the biopharmaceuticals, being enclosed in RoSS Shell – an innovative case for single-use bag protection.
These and more solutions illustrate the huge potential of single-use technology in the biopharma industry, and contribute to safer, more flexible and resilient biopharma supply chains.