Plate freezing: best approach for freezing biopharmaceuticals
Table of contents
ShowPlate freezing is a process where a product’s temperature is reduced by the means of contact with cold surfaces. Thus, a defining step in the freeze-thaw process for conservation.
Things to know about plate freezing techniques
Although plate freezing is very commonly known in food production, this freezing process has proven equally indispensable for the biopharma industry. After all, it is to fullfill the same purpose in both fields of application: to freeze products for storage and transport in order to ensure maximum product quality – be it frozen food like fish fillets or highly delicate biologics like mRNA vaccines.
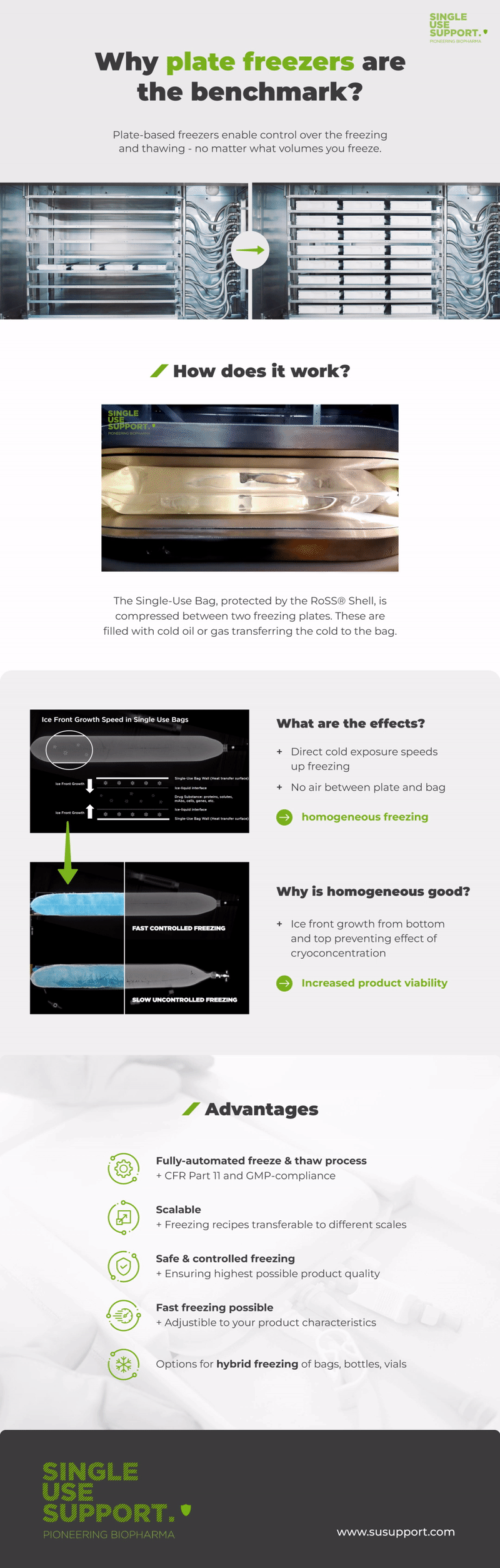
How freezing techniques emerged
Like many scientific discoveries, the advantages of freezing (then) food for shipment were found by chance: In general, cold environments have been used for ages in order to cool food with the aim to impede the growth of microorganisms. After all, it was in 1890 when, by accident, refrigerated meat that was being transported overseas from Australia to Britain got frozen. This had such remarkable results on the quality of the delivered food that the procedure of freezing has soon been widely adopted in food transport and storage. Later on, in the 20th century, quick freezing has shown to be advantageous for various kinds of food.
Since its beginnings, refrigeration systems have undergone many steps of evolution and improvements – from the combination of salt brine and ice that products were induced in (a patent on this dates back to 1848’s Britain) up to high-performance automatic plate freezers. Alongside, freezing time has been optimized, freezing capacities expanded and new fields of application discovered.
What freezing techniques are most counted on?
The most frequently used freezing techniques are:
- brine freezing: A product is submerged in a brine that is additionally cooled by refrigerants.
- cryogenic freezing: Liquid nitrogen is applied on a product in order to instantly freeze it; this is a quick yet costly freezing procedure. A cryogenic freezer freezes down to -180°C/-292°F.
- blast freezing: Products are put into an environment which is cooled by the means of cold air – a very common practice, i.e. for ultra cold storage in laboratories.
- contact freezing (plate freezing): A product is frozen via direct contact with cooled surfaces like those of a contact plate freezer.
Considering the different approaches in refrigeration with multiple challenges and benefits, a focus on the plate freezing process shall illustrate the huge potential and its key role in pharmaceutical production.
Plate freezer vs. blast freezer – the main differences for biopharma
During the process of blast freezing, air is blasted on a product in order to set or keep it at low temperature; it is frequently chosen to create a cold storage for frozen items, conserving them over a longer time. Plate freezing, on the other hand, relies on cooled surfaces themselves rather than a cooling air blast: Via direct contact with these freezing plates, heat transfer is induced between them and the yet to be frozen products – often stored in carton –, allowing quick freezing of drug substance between the two metal plates. In that a plate freezer requires the product to be touched by both surrounding surfaces, the shape of its containers is to be taken into account as well.
Advantages of plate freezing for biopharma
As for biopharma, the use of a pharmaceutical freezer can be substantial e.g. on the attempt to exactly control the freezing time according to the requirements of the processed substance. Recipe-driven setpoints for product-tailored freezing allows cGMP-driven standardization and reproducibility of freezing kinetics.
Plate freezers facilitate fast and controlled freezing of bulk drug substance which has proven to significantly reduce the occurrence of cryoconcentration: Caused by the different solubilities of a product’s components, the ongoing emergence of crystals leads to the separation of certain ingredients. With fast plate freezing it is hence possible to minimize reduction of product quality by achieving high homogeneity in the liquids. Homogeneous freezing is a result from quicker heat exchange.
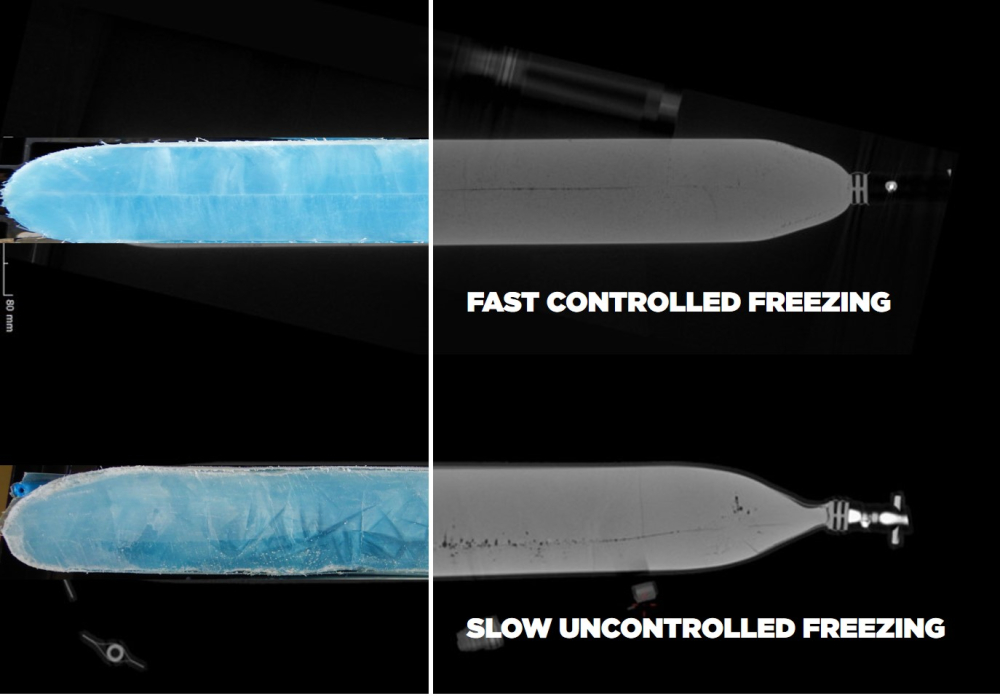
As a result of a slow freezing process through conventional freezing techniques, larger crystals with proteins coagulate in the center of primary packaging which causes tensions that lead to diminishing product quality.
Yet another benefit of the use of plate freezing compared to blast freezing is its high cost efficiency due to its lower energy consumption. Instead of cooling the surrounding air, items in the process of plate freezing – be it by the means of a vertical plate freezer or, if the plates are arranged accordingly, in a horizontal plate freezer – are in direct contact with cooled surfaces made of stainless steel, flown through by a refrigerant.
Freezing solutions for biologics – from lab- to bulk-scale
Acknowledging the many benefits of plate freezing in the production of high quality biologics, Single Use Support has developed an elaborate product lineup of freeze-thaw-platforms to address a wide array of applications with RoSS.pFTU (plate-based freeze-thaw unit). Having the choice between four different sizes (from 100 mL up to more than 200L), customers are provided with the appropriate freezing solution for their very needs. From the use in studies conducted in labs with the small lab freezer for pharma up to bulk production of biopharmaceuticals, a fully scalable freezing option has been developed to ensure maximum product quality.
Even though compatibility with single use bottles and bags of all sizes and manufacturers is given both in lab-scale and in large-scale freezing systems, RoSS shells are a valuable complement to the reliable end-to-end solution provided by Single Use Support.