Extractables and leachables: definitions, differences & facts
Table of contents
ShowExtractables and leachables are contaminants that are causing biopharmaceutical manufacturers headaches, as they can lead to impurities of highly valuable drug products.
The FDA defines the two terms as follows:
- Extractables are compounds that can be extracted from the container closure system when in the presence of a solvent
- Leachables are compounds that leach into the drug product formulation from the container closure system as a result of direct contact with the formulation
Extractable and leachable impurities can be caused by pharmaceutical processing- and container closure systems, as well as other packaging material.
While extractables and leachables both describe foreign matter that can lead to contamination of highly valuable drug products, it is important to understand their characterization but also the difference between the two.
What are extractables?
Extractables are substances or compounds that can be extracted from a primary container, component material, delivery system or manufacturing surfaces when laboratory manipulation occurs (solvent or heat exposure), leading to contamination of pharmaceutical products.
Extractables are mostly generated by interaction between a drug product and its packaging, either consisting of single-use consumables or other biopharma packaging components, such as single-use bioprocess container. Usually, extractables are the consequence of extreme conditions like the presence of strong solvents or high temperatures. Furthermore, extractables can be caused by gamma-irradiation by degradation of the packaging material/primary container mainly consisting of polymers.
What are leachables?
Leachables are compounds that leach into the drug product from the container-closure system, be it from elastomeric, polymer, other plastic components, or coating materials.
Leaching is mainly a result of direct contact with the formulation. Leachables are typically a subset of extractables, but as opposed to extractables, they can occur under normal conditions of use. The cause of leachables can be additives or release agents, coatings and similar inorganic materials.
Difference between extractables and leachables
As already mentioned, leachables are a subset of extractables. They are both caused by either inferior manufacturing techniques or a lack of control of additives or agents used in the raw materials.
However, while extractables are caused by extreme conditions, leachables can occur even under normal circumstances. To highlight the difference: There is a potential leachables may always be present in an inferior quality sample storage container, whereas extractables may only be present after gamma irradiation has been applied to sterilize containers manufactured in a clean room.
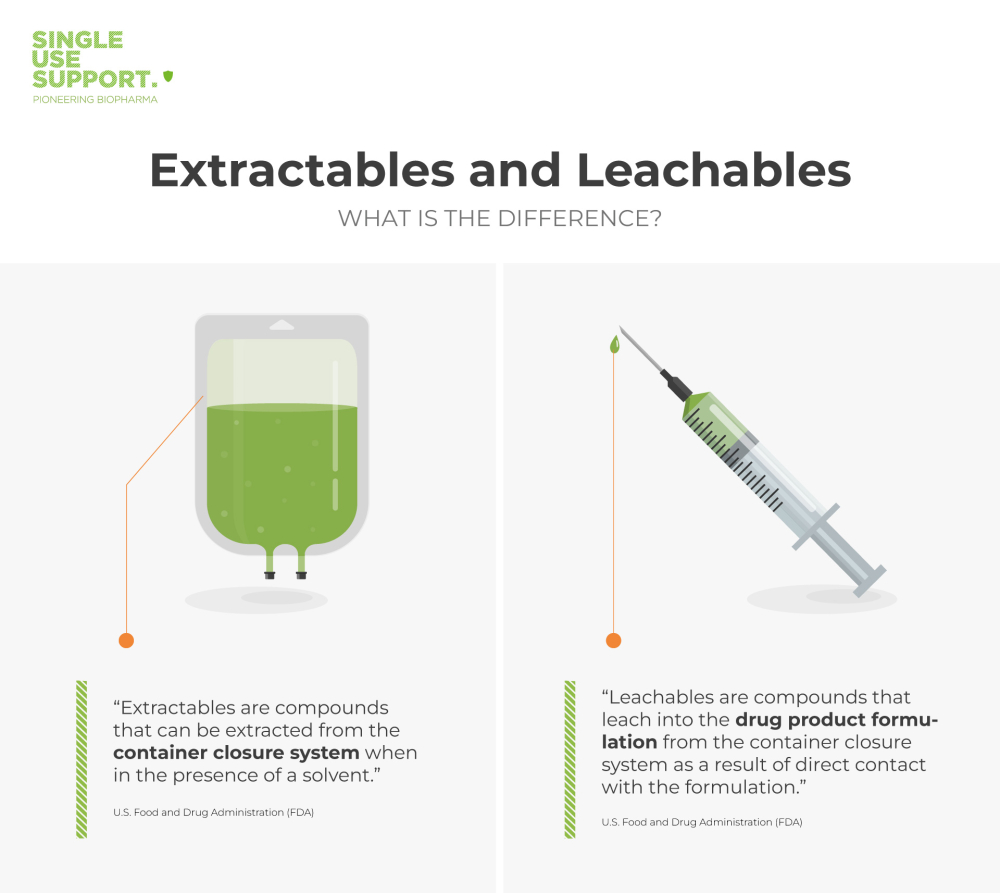
What is extractables and leachables testing?
With the integration of single-use systems into downstream processing - and thus closer to the final drug product - extractable and leachable studies are becoming increasingly important in the pharmaceutical industry. The aim of E&L analysis is to find out and evaluate possible toxicological risks.
To prevent impurities and ensure patient safety drugs, medical devices as well as combination products, such as pre-filled syringes, must be free of harmful materials. Since extractables and leachables can both lead to contamination, the FDA requires extractables and leachables testing to guarantee that no chemicals transfer into the drug from its packaging materials or during production.
Only products that have been given the green light after such an analysis or study are considered compliant with regulatory standards and safe for use. The toxicological tests required for the validation of pharmaceutical products are usually conducted in specialized analytical laboratories.
Different types of extractables and leachables testing
There are many different methods to test for extractables and leachables. Apart from HPLC (high-performance liquid chromatography), analytical methods used to detect impurities include various types of mass spectrometry such as ICP-MS (inductively coupled plasma), (Head-space) GC-MS (gas chromatography) and LC-MS (liquid chromatography).
Additionally, one can differentiate between various compounds, which could possibly be harmful. There are volatile organic compounds (VOCs), semi-volatile organic compounds (SVOCs), non-volatile organic compounds (NVOCs) and elemental impurities. In order to choose the right study design, it must be clear which compounds are going to be analyzed.
All the different analytical techniques like HPLC and different types of mass spectrometry are able to identify and quantify even the lowest concentration of toxicity or impurities. External product quality research institutes carry out those different risk assessment tests to ensure that materials of concern are not transferred from the device or product to the patient.
As a standard, the results of any pharmaceutical analysis, be it E&L studies or other related toxicological assessment, should be reviewed by qualified toxicologists. The goal is to minimize patient safety concerns with regards to the exposure to potentially harmful leachable compounds. The route of administration/dosage form (parenteral, topical, inhalation or oral) and dose of the drug product (acute versus chronic) are key factors to be considered in any extraction study or toxicological report. Furthermore, the nature of the process and use of the processing materials are also important factors.
Which products have extractables and leachables?
Extractables and leachables are mostly mentioned in connection with bioprocessing. But while (elemental) impurities do have an adverse effect on biopharmaceutical formulations, they also concern the biotech industry. Apart from biologics, medical devices and combination products (skin batches, syringes) are also affected by extractable and leachable contaminants.
In order to rule out any impurity and guarantee patient safety, all of these medical devices and drug products require extractable and leachable studies.
Impurities that can lead to contamination of the product caused by extractables and leachables include polymer and various packaging materials, inks and adhesives.
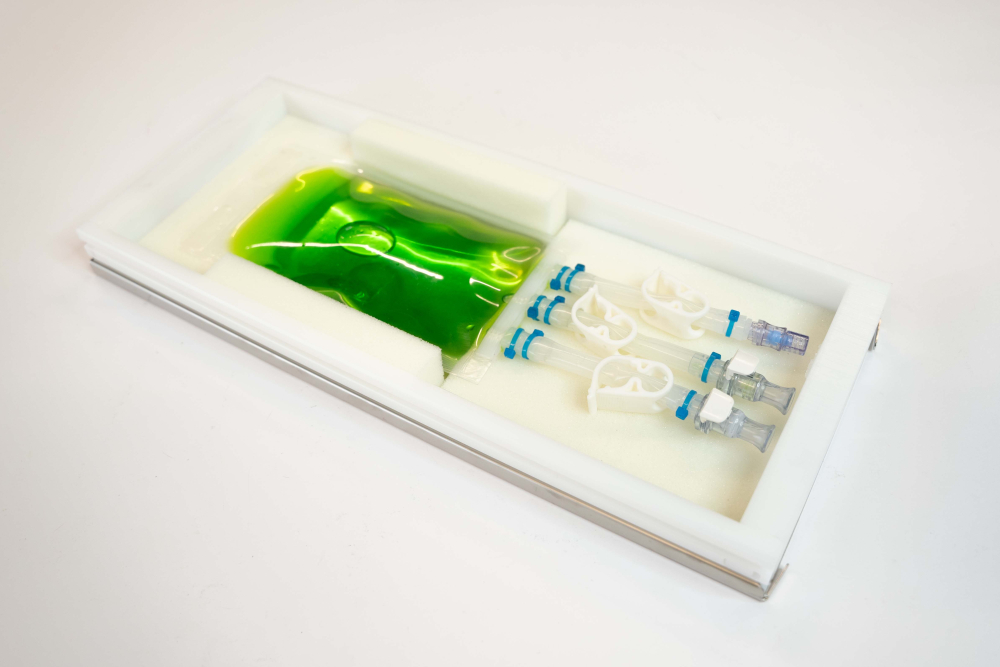
Validation of processing material
Generally speaking, any processing material utilized for biopharmaceutical processing and/or the manufacturing of medical devices have very low probability of not being safe. However, because certain materials such as elastomers, polymers or adhesives can cause extractables and leachables, different testing and analytical techniques are necessary.
E&L studies for single-use systems
The importance of extractable and leachable studies with regards to reducing patient safety risks should not be underestimated. If a drug product is contaminated in any way by a chemical derived from its packaging, it can cause immense problems for patients. This is why various regulatory agencies, including the BioPhorum (BPOG), the International Council for Harmonisation of Technical Requirements for Pharmaceuticals for Human Use (ICH) and the Food and Drug Administration (FDA), stipulate that any biopharmaceutical processing materials be evaluated to determine whether they impact the final drug product in terms of safety and efficacy. The same is true for medical devices.
There are different guidelines for medical devices and combination devices (like ISO 10993) which have to be strictly followed.
Extractables and leachables in single-use systems
According to regulatory agencies, single-use systems are classified as processing materials and thus require validation regarding their integrity. While there is, as of yet, a lack of standardization, regulatory agencies such as the European Medicines Evaluation Agency (EMEA) and FDA have published validation and testing guidelines and recommendations for the packaging material of final drug products. The final packaging guidelines provide risk assessment strategies that can be applied to processing materials.
Collaboration (in the form of initiatives such as the Product Quality Research Institute (PQRI) or ICH) and clear definition of roles between manufacturers of single-use bags and systems, suppliers, and drug product manufacturers are crucial to ensuring patient safety and product efficacy. This is true even for the transportation and storage of single-use components and assemblies prior to use in the drug product manufacturing process.
Single Use Support is a member of the BioPhorum (BPOG), which is a worldwide collaboration of experts and industry leaders in the biopharma industry. BPOG has published a “Best Practices Guide for Extractables Testing”, which is a protocol presenting every step needed to test E&L considering all mandatory regulations.
All of Single Use Support’s PE films are drawn from a supplier who follows BPOG protocol and has conducted extensive studies regarding extractables, which showed ultra-low levels of extractables and leachables. Additionally, it has been stated that the PE films show extremely low extractables and resistancy to a wide range of chemicals.