Annex 1: All you need to know
Table of contents
ShowGMP Annex 1, the European guideline for “Manufacture of sterile medicinal products”, has been updated in 2023. The revision’s changes have added several challenges, but also chances for manufacturers in order to comply with the new regulations.
This article aims to provide an overview of Annex 1, its applicability, and the necessary actions that biopharma industry stakeholders must take to comply with its requirements, particularly in relation to single-use assemblies.
What is Annex 1?
Annex 1 is the European Union’s guidelines for the manufacturing of sterile medicinal products. The original draft of Annex 1, also known as “EU GMP Annex 1: Manufacture of sterile medicinal products”, from 1971, was expanded and updated in August 2022. It came into effect on August, 25 2023.
EU GMP Annex 1 outlines the GMP-specific requirements (Good manufacturing practice) needed to ensure product quality and patient safety when it comes to sterile medicinal products. The guidelines were not only directed at pharmaceutical manufacturers, but also towards partnerships between contract manufacturing organizations and their clients. 1
Annex 1: Requirements for pharmaceutical manufacturing
GMP Annex 1, also known as the "Manufacture of Sterile Medicinal Products," is a guideline published by regulatory authorities, such as the European Medicines Agency (EMA) and the U.S. Food and Drug Administration (FDA). It outlines the principles and practices for the manufacture of sterile medicinal products to ensure their safety, efficacy, and quality as laid down in Commission Directive (EU) 2017/1572 for medical products for human use and veterinary use.
GMP Annex 1 applies to pharmaceutical manufacturers, contract manufacturing organizations (CMOs), and other entities involved in the production of sterile medicinal products. It is applicable to a wide range of biopharmaceutical processes, including fluid management, where single-use assemblies are commonly employed.
In the past, individual components for advanced therapy medicinal products, like mRNA or viral vectors, were filtered aseptically and then filled into sterile components with a large share of manual handling (e.g. in laminar air flow or filling lines). Now, there is a greater focus on automated processes and closed systems.2
Manufacturers and industry professionals must assess the quality, performance, and suitability of single-use systems to meet the specified requirements.2
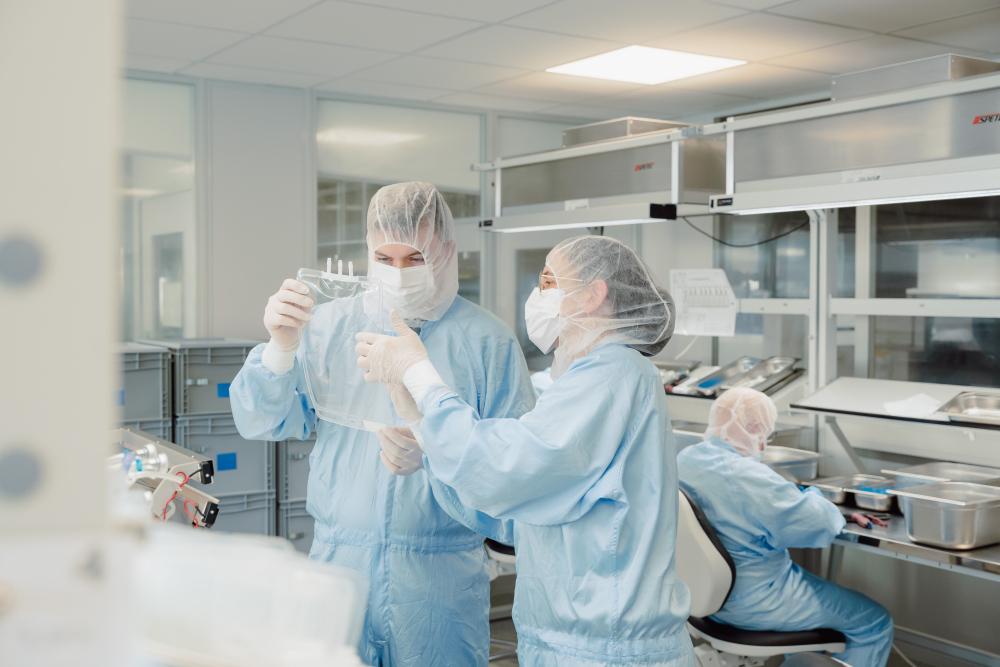
EU Annex 1 and the changes in 2023
Annex 1 is the European GMP guide, while the American equivalent by the FDA is titled “Guidance for industry: Sterile drug products produced by aseptic processing current good manufacturing practice”.3 In China, the National Medical Products Administration (NMPA) has issued equivalent regulations under the “Good Manufacturing Practice for Drugs”.4
The first version of Annex 1 was published in 1971. Since then, the document experienced several adaptations, but a complete revision process was only started in 2012.
For the revision, the EU commission worked closely together with the World Health Organization (WHO), the Pharmaceutical Inspection Co-operation scheme (PIC/S) and the Food and Drug Administration (FDA)5. One of the goals was to achieve a more unified version of guidelines for the manufacturing of sterile medicinal products.
The aim of the mission was to react to new changes in manufacturing environments, which is mirrored by the strong focus of the guidelines on contamination risk management.3 4 5
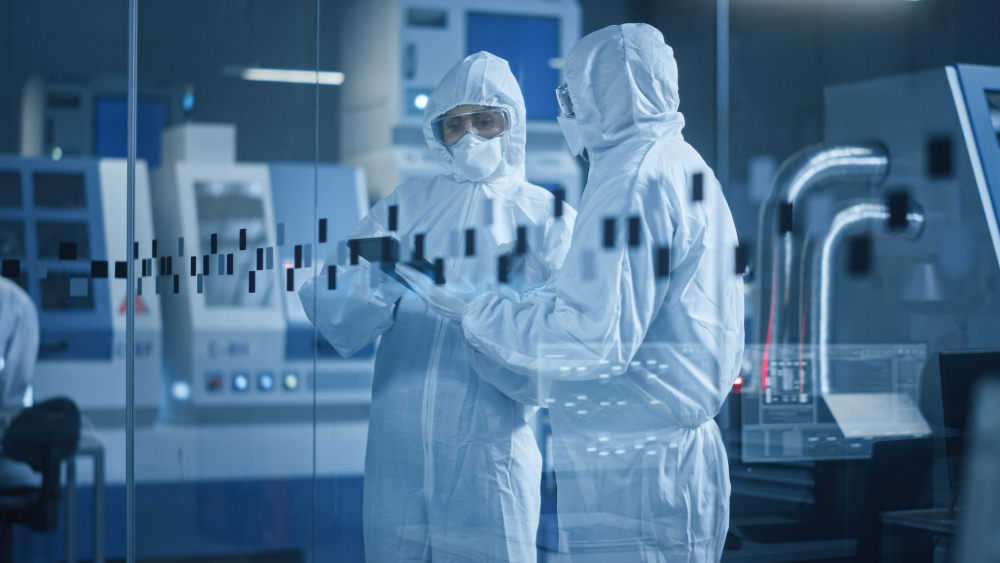
Content of Annex 1 – the main focus areas
The main focus areas of Annex 1 include the application of Quality Risk Management (QRM)6. Manufacturers are required to implement a Contamination Control Strategy (CCS), include the Pharmaceutical Quality System (PQS) into their manufacturing process, and apply the principles of QRM (monitoring, disinfection and staff training).
Next to updated cleanroom requirements7, Annex 1 determines regulations for Pre Use Post Sterilization Testings (PUPSIT) for filters used in bioprocessing.8
Further, a new set of technologies is addressed in Annex 1, ranging from restricted access systems (RABS) for cleanrooms to isolators and single-use technologies.6 7 8
Risk management and contamination control strategies
The revision of Annex 1 has a main focus on the aspects of Quality Risk Management and the development of Contamination Control Strategies for pharmaceutical manufacturers. CCS strategies are laid out as a “set of controls for microorganisms, endotoxin/pyrogen and particles, derived from current product and process understanding that ensures process performance and product quality.”7
As the revised guidelines aim for improved quality, safety, and overall-contaminant-free products, manufacturers have to come up with strategies to achieve this. These include regular controls of risk factors to cleanroom environments, such as raw materials, excipient and drug product components, as well as facility and equipment design. Further, thorough documentation of the whole process from design to the administration of the product has to be provided in order to comply with Annex 1.9
Cleanroom regulations
In Annex 1, cleanrooms experience a heightened amount of attention. The most striking changes involve regulations on how to move within cleanrooms (slow and controlled movements, so not to shed more particles than needed), as well as specially designed clothing items.
The rules laid out for the different cleanroom classes from A to D can differ. While hair, for example, does not need to be covered in Grade A and B environments, members of staff need to wear a cap and cover beards and jewellery in C and D environments.
Further, it is laid out how technologies for cleanrooms like Restricted Barrier Access Systems (RABs) require special testing and control strategies. The integration of automated systems helps manufacturers reach GMP requirements more easily. Closed processes prevent exposure times and help to maintain sterility by reducing the need for manual intervention.
PUPSIT: Pre-Use Post Sterilization Integrity Test
PUPSIT is the abbreviation of Pre Use Post Sterilization Integrity Testing. The process helps pharmaceutical manufacturers to make sure that a filter is fully functional before it is used in bioprocessing.
Before a membrane filter, for instance, can be used in a bioreactor, the filter has to be sterilized. After that, testing is performed to verify the filter’s integrity, meaning it has not been damaged during sterilization.
The most widely used filter integrity testing method is the Bubble Point Test, during which water is injected to moisten the filter. The test depends on sterile filter test tubes, which are often made out of stainless steel. However, the use of single-use-technologies is on the rise. With single-use filtration assemblies, the whole system, and not just the filter, is replaced after every cycle. They eliminate the need for autoclaving procedures and help guarantee that the drug formulations are not diluted by water residues after filter testing.
The role of single-use technologies in complying with Annex 1
Single-use technologies are increasingly used on production lines and could help to ensure compliance. For example, single-use bioprocess containers make it easier to maintain sterility across powder and liquid transfers or open handling by manual filling. Single use systems should be designed to reduce the need for manipulations and complexity of manual interventions. (8.132 of Annex 1). In detail this includes
- the interaction between the product and product contact surface (such as adsorption, or leachables and extractables)
- the fragile nature of the system compared with fixed reusable systems
- the performance of the pre- and post-use integrity testing for sterilizing grade filters
- the risk of holes and leakage
- the potential for compromising the system at the point of opening the outer packaging and
- the risk of particle contamination
Single Use Support can provide customers with documentation, risk assessments and product specified information, such as data for extractables and leachables of single-use systems, proving how the company fulfills the criteria with its solutions.
GMP Annex 1 significantly impacts the use of single-use assemblies in fluid management processes within the biopharmaceutical industry. It requires manufacturers and stakeholders to adopt a risk-based approach, implement proper controls, and ensure the integrity and sterility of single-use systems. Compliance with GMP Annex 1 is essential to maintain product quality, meet regulatory requirements, and safeguard patient safety.
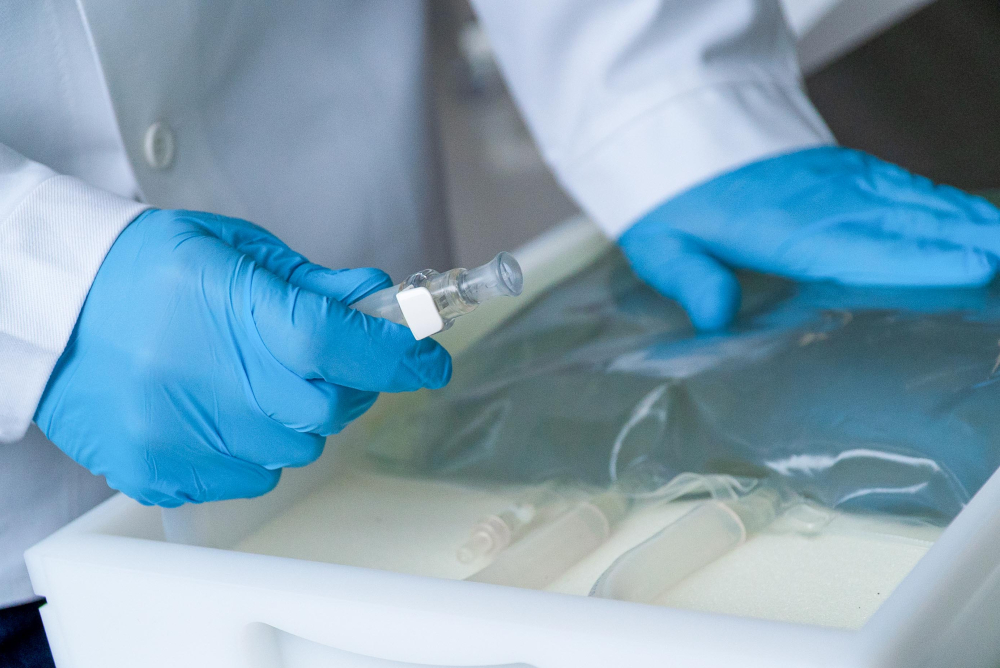
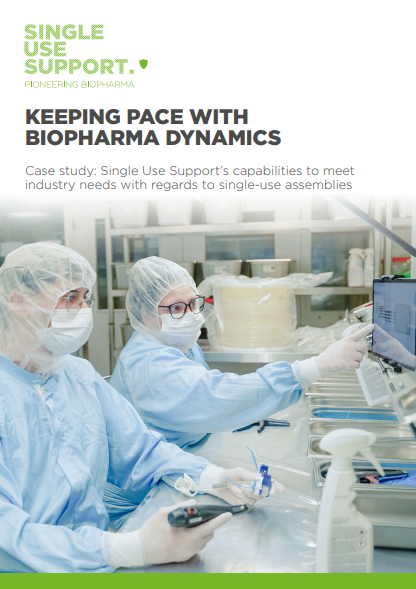
Keeping pace with biopharma dynamics
Case study: Meeting industry needs with single-use assemblies
We have provided sterile single-use assemblies to many biopharma companies in a variety of scenarios:
- Production of single-use manifolds during pandemic unavailability
- Pandemic preparedness to stock diverse manifolds for future unexpected events
- Increasing quantity of single-use assemblies
Read our case study on reliable global supplies capabilities.
Single Use Support aiding in Annex 1 compliance
Adopting the necessary changes to comply with Annex 1 sets a challenge for many manufacturers of biologic drugs. Defining the scope of a CCS can be a great difficulty because Annex 1 guidelines do not only include the products and components on-site, but also starting materials and other products provided by other parties.
With changes in cleanroom regulations and strategies to prevent contamination like regular filter controls, the necessary changes pharmaceutical and biotechnology companies have to make call for holistic solutions.
RoSS.FILL: Filling and filtration system
The advanced filling and filtration system RoSS.FILL can be expanded with a PUPSIT rack for sterile filtration. It was designed by Single Use Support to guarantee compliance with Annex 1 guidelines. This closed automated system offers the benefits of modularity and scalability and is compatible with single-use bioprocessing containers in different sizes to cater to smaller and large-scale productions.
IRIS single-use assemblies
Single Use Support also offers the single-use assemblies needed for GMP-compliant fluid and cold chain management, from tubes to filters for sterile fluid management. With holistic process solutions, the company helps manufacturers achieve the highest product quality and patient safety.
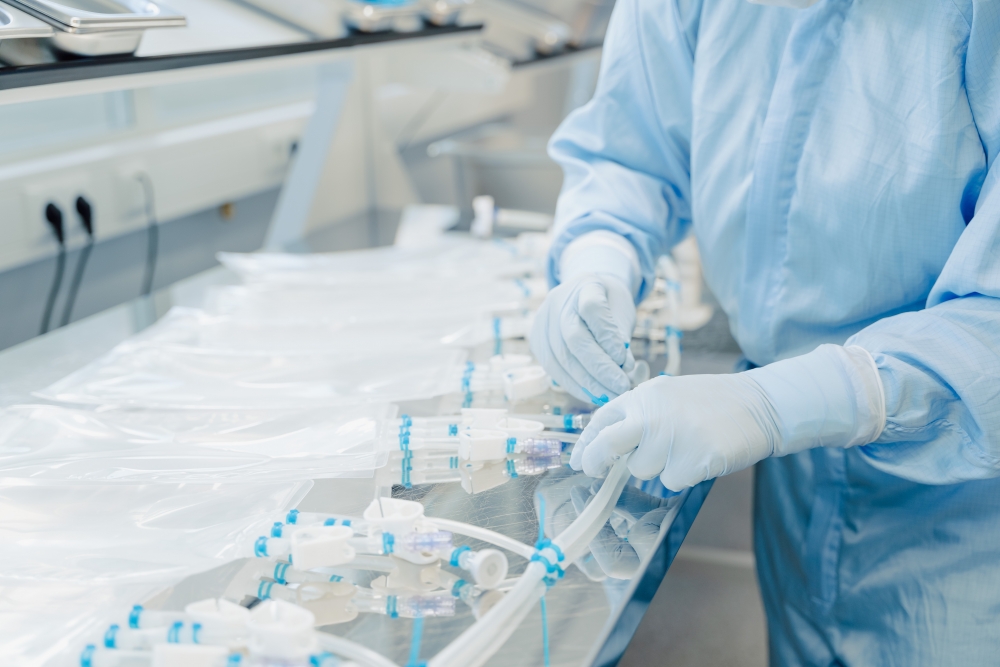
Conclusion: What Annex 1 means for pharmaceutical manufacturing
GMP Annex 1 significantly impacts the use of single-use assemblies in fluid management processes within the biopharmaceutical industry. It requires manufacturers and stakeholders to adopt a risk-based approach, implement proper controls, and ensure the integrity and sterility of single-use systems. Compliance with GMP Annex 1 is essential to maintain product quality, meet regulatory requirements, and safeguard patient safety.
Single Use Support is pioneering the biopharmaceutical industry and is at the forefront of advancing fluid and cold chain solutions. The process solutions provider takes the same approach as Annex 1, that automated single-use technologies and closed and protected systems help reduce the risk of contamination. As a trusted partner to multiple biopharmaceutical manufacturers and contract development and manufacturing organizations, Single Use Support is here to offer guidance in achieving maximum product quality, patient safety and navigating GMP Annex 1.
* IRIS Single use systems are developed product-specifically. All filter capsules available on the market can be installed. Filter types are selected depending on product and quantity. Single Use Support takes the recommended redundancy into account. The use of high-pressure resistant material, such as braided silicone (platinum cured) tubing and the interconnection protection with Oetiker clamps enables leakage-free testing of the filter components prior to filtration at high pressures and filtration after testing. The recommended working pressure is determined during development of the assmenly and the feasibility of testing is ensured. The venting and flushing of the system is taken into account in the configuration. Each assemly is a custom solution for the manufacturers process
Read more about GMP & cGMP regulations
- Second targeted stakeholders' consultation on the revision of Annex 1, on manufacturing of sterile medicinal products, of Eudralex volume 4, https://health.ec.europa.eu/consultations/second-targeted-stakeholders-consultation-revision-annex-1-manufacturing-sterile-medicinal-products_en, Published
- RNA-based drugs and regulation: Toward a necessary evolution of the definitions issued from the European union legislation, http://dx.doi.org/10.3389/fmed.2022.1012497, Published 2022-10-17
- Main Responsibilities of the National Medical Products Administration, https://english.nmpa.gov.cn/2019-07/18/c_377587.htm, Published 07/2019
- FDA and EU GMP Annex 1 Differences in Cleanroom Specifications, https://www.raps.org/News-and-Articles/News-Articles/2019/7/FDA-and-EU-GMP-Annex-1-Differences-in-Cleanroom-Sp#citation, Published 07.2019
- The Rules Governing Medicinal Products in the European Union Volume 4 EU. Guidelines for Good Manufacturing Practice for Medicinal Products for Human and Veterinary Use, https://health.ec.europa.eu/system/files/2022-08/20220825_gmp-an1_en_0.pdf, Published
- ISO 14698 or EN 17141: Is There a Choice for Cleanroom Compliance?, http://dx.doi.org/10.2345/0899-8205-57.s1.15, Published 2023-05-05
- Sterilisation Methods, http://dx.doi.org/10.1007/978-3-031-20298-8_30, Published 2023-06-15
- Enhancing Compliance with EU GMP Annex 1 Requirements, https://www.americanpharmaceuticalreview.com/Featured-Articles/609715-Enhancing-Compliance-with-EU-GMP-Annex-1-Requirements/, Published 12/2023
- The Rules Governing Medicinal Products in the European Union Volume 4 EU. Guidelines for Good Manufacturing Practice for Medicinal Products for Human and Veterinary Use, https://health.ec.europa.eu/system/files/2022-08/20220825_gmp-an1_en_0.pdf, Published