Fluid management solutions for biosimilar production
Table of contents
ShowThe growing demand for biosimilars and significant increases in the biosimilar market call for innovative solutions for their fluid management process. This relates to steps like filling and filtration, as well as cooling, storage and transport of biosimilars. While it is of utmost importance to produce high-quality products, manufacturers are also interested in finding ways to optimize production times and create a reliable process that is as cost-efficient as possible.
In this article, we are going to highlight the challenges manufacturers of biosimilars have to face in fluid management and introduce effective and innovative fluid management solutions.1
Challenges in biosimilar fluid management
Since biosimilar manufacturing is a costly and time intensive operation, it is important to design the whole process to be as efficient and safe as possible. This includes addressing biosimilar manufacturing challenges connected to fluid management like product loss, streamlining production to save time and navigating biosimilar regulatory requirements.
Product loss in biosimilar production
There are different occurrences to lose a product – either when carrying out tedious and monotonous tasks in fluid management manually or when primary packagings are damaged. To maximize safety and guarantee continuous product quality, it is essential for manufacturers to minimize the risks for contamination and product loss due to damaged primary packaging.
This can be reached by minimizing the need for manual intervention and errors during production, integrating automated solutions for the entire process or different production steps. Further improvements are protective, durable cases that embed single-use bioprocess containers to prevent ruptures in the fragile when frozen container components.2
Efficient manufacturing for shorter production times
There are several factors to be considered when aiming to exploit the full potential of biosimilar manufacturing. These include upping production speed, as well as the ability to adjust to changing conditions and market demands. In terms of fluid management, this means relying on scalable fluid management solutions for biosimilars and biologics that are preferably automated to reduce downtime. Modular solutions are especially requested, as they can easily be scaled up without the need to replace every machine along the fluid pathway. 3
Navigating regulations in biosimilar manufacturing
There is an extensive regulatory framework involved in the production of biosimilars to ensure not only the similarity with its reference biologic, but also achieve continuous quality and safety of the product.
Concerning biosimilar fluid management, strategies have to be found to ensure clean room requirements and aseptic filling processes, product protection and regular testing.
Therefore, it is vital for manufacturers to find ways to integrate testing practices like pre-use post sterilization integrity testing (PUPSIT) for sterile filters in a way that consumes as little time and effort as possible, but with no compromise on safety.
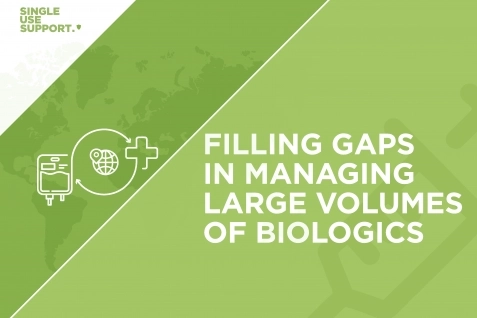
Download eBook
Filling Gaps in Managing Large Volumes of Biologics
Advantages of fluid management with single-use technology
Single-use technology has proven to be a successful approach for advanced fluid management in bioprocessing. Costs and production times can be significantly reduced by falling back on automated solutions, which is bound to change the biopharmaceutical industry by lowering expenses for innovative treatment options.
To ensure the safety of a biosimilar product, it is critical to provide protected and sterile manufacturing conditions. By integrating single-use technologies into the fluid management of biosimilars, it becomes possible to eliminate the process of cleaning and sterilization at the manufacturing site, which costs time and resources. Instead, single-use solutions rely on sterile tubing, connectors, and containers, along with other equipment to increase efficiency and safety that are easily disposable after usage. 4
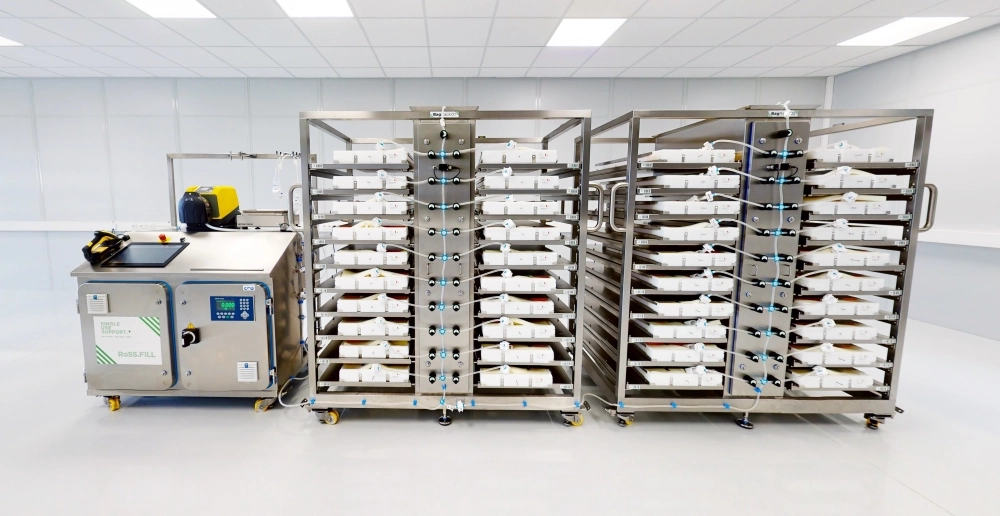
Another important advantage of single-use solutions is their scalability. This addresses the challenge of up-scaling during production. As the size of production batches may significantly vary along development stages and manufacturing, modular single-use platform systems with easy plug & play racks allow for more freedom and flexibility.
To summarize, the main advantages of fluid management with single-use technology are:
- Scalability
- Reducing production costs and time
- Lowering contamination risks
- Compliance with cGMP regulations
Single-use fluid management solutions for biosimilar production
There are many ways in which manufacturers can benefit from integrating single-use fluid management solutions into biosimilar production. These range from automated homogenizing units to aseptic filling and filtration systems, as well as robust protective secondary packaging for single-use bags.
Homogenizing liquids with RoSS.PADL
Achieving a consistently homogeneous mixture in biosimilar solutions is essential to guarantee uniformity in high-quality products. Since process reproducibility is key, Single Use Support has developed RoSS.PADL, a homogenizing platform that gently kneads and cools single-use bags simultaneously.
The cooling process prevents product alterations during massaging by maintaining the appropriate temperature for the biosimilar product. This automated homogenizing solution removes the need for human intervention, for instance during draining, and operates in a standardized and reproducible way. It is also possible to combine several RoSS.PADL units with each other and control them with one single operating system.
Aseptic filling and filtration with RoSS.FILL
By integrating automation into aliquotation processes, it becomes possible to minimize the inherent risks for contamination and streamline the process simultaneously to stay economically competitive. With RoSS.FILL, Single Use Support takes on the challenge with a completely scalable design that is able to reach filling speeds up to 300 liters per hour.
Single-use bioprocess containers are filled in an aseptically closed system and in a fully automated manner. The process can be controlled via a computerized system. Not only can additional racks be added via plug & play to the aseptic filling and filtration unit, but it is also possible to attach it to other systems and devices, such as RoSS.PADL.
RoSS® Shell: Advanced protection for single-use bags
Protecting single-use containers during transport and storage is essential to prevent damage and product loss. With RoSS® Shell, Single Use Support has developed a robust protective case for single-use bags. The resilient shell protects 2D single-use bags of different sizes and all vendors and is not only optimized for transport situations but also for freezing biosimilars – another critical step for manufacturers. The durable and compact protective shell also offers enough space for tubing and sterile connectors and maximizes storage density. This leads to a reduction of required space in freezers once advanced plate freezing has been performed, which is also enabled by RoSS® Shell.
Ready for the next steps in bioprocessing – with Single Use Support
With automated solutions by Single Use Support, manufacturers are not only able to optimize their fluid management process, but can also optimally prepare themselves for the following steps in the supply chain: Freezing, storage, and transport.
Maintaining the cold chain is essential to ship and store high-quality biosimilar products. To help manufacturers achieve this goal more easily, Single Use Support has designed the high-performance freezer RoSS.pFTU, an automated system for freezing and thawing biosimilars and other liquid drug substances, including vaccines and mAbs. The plate-freezing technology allows for controlled freezing of single-use bags, which provides optimal freezing results.
For cell and gene therapies requiring cryogenic freezing, Single Use Support has developed RoSS.LN2F. The cryogenic controlled rate freezer is an innovative platform system that freezes substances in single-use bioprocess containers down to -170°C. Controlled cryogenic freezing offers the best product stability results to protect high value substances.
As a safe and scalable option for storing biologics and biosimilars, the storage freezer RoSS.FRDG keeps biosimilar drug substances reliably cool at temperatures down to -75°C. It provides advanced temperature stability, precise monitoring, and high storage density.
Single-use technologies represent innovative solutions to help optimize biosimilar production. To this end, Single Use Support offers automated platforms and equipment to perform a successful fluid and cold chain management in bioprocessing.
- The rise of the biosimilar, http://dx.doi.org/10.1586/ecp.12.60, Published 2012-12-12
- The process defines the product: what really matters in biosimilar design and production?, http://dx.doi.org/10.1093/rheumatology/kex278, Published 2017-07-03
- A Single-use Strategy to Enable Manufacturing of Affordable Biologics, http://dx.doi.org/10.1016/j.csbj.2016.06.007, Published 2016-07-06
- A Single-use Strategy to Enable Manufacturing of Affordable Biologics, http://dx.doi.org/10.1016/j.csbj.2016.06.007, Published 2016-07-06