Loss of drug substance - the challenges and chances of product loss
Table of contents
ShowIn recent years, if not decades, gene therapies have proven to be key drivers of growth in the pharmaceutical industry. Production is often complex, challenging manufacturers with new hurdles:
The fragile nature of medical drug products has forced the industry to find new approaches for filtering and fill finish as well as the drug substance logistics process.
In an extremely complex, competitive and constantly evolving field like the biopharmaceutical industry, the tiniest mishaps have far-reaching consequences on several levels. In order to get a valuable drug product to its final destination without compromising quality or risking loss of drug substance, an efficient and reliable bulk drug substance management is required.
Read on if you want to find out what is or can be done to minimize biopharmaceutical product loss and how scalable and agile solutions are offering innovative ways forward for many sectors in life sciences.
Product loss of biopharmaceuticals
Even though they are often overlooked, fill/finish operations fulfill an important task when manufacturing biopharmaceuticals. They cover a critical step in the drug production process, especially during early-phase clinical evaluation: Medical drug products like mAbs are a complex and highly sensitive matter that require a sterile environment and absolutely reliable logistics processes - terminal sterilization is not an option.
This means that irrespective of volume, any medical product needs to be sterilized by point-of-fill filtration, which poses a number of challenges for biopharma companies, both in operational and regulatory terms – e. g. in the context of directives by the Food and Drug Administration (FDA). And if anything goes wrong, it will lead to dire consequences not only for the pharmaceutical company:
The loss of just 1 L of drug substance may incur exorbitant costs and pose a danger for the patient whose life might depend on the timely delivery of said drug (for instance in the case of CAR-T therapies).
This is why the loss of drug substance during filling, storage and shipping needs to be kept to an absolute minimum, be it for clinical trials or during bulk production. Fill/finish facilities are challenged to address these issues and find ways to reduce the loss of drugs to an absolute minimum while complying with regulatory standards as well as testing and quality guidelines.
Product loss of APIs and other biopharmaceuticals – risks along the supply chain
Product loss of APIs (active pharmaceutical ingredients) and other biopharmaceuticals is a risk that biotech companies encounter all along the various supply chains. However, there are certain critical steps that need to be considered in the handling of substances like small molecules, different formulations of biologics and biosimilars.
With upstream and downstream processes often geographically detached, measures must be taken by manufacturing facilities to provide seamless transitions between different production steps. Optimization of the processes like filling/filtration of drug substance, freezing/thawing of drug substance and storing/transporting APIs and other biopharmaceuticals is necessary, along with (ideally) real-time monitoring, considering that inconsistencies might lead to severe consequences for manufacturers and patients.
Read more: Drug substance vs. drug product – the differences
Loss of drug substance regarding Car NK or Car-T therapy
In 2012, 6-year-old Emily Whitehead, who was suffering from leukemia, received a promising new CAR-T cell therapy. None of the other applied therapies had proven successful, and specialists had already given up hope. Against all odds and thanks to a novel therapeutic approach, Emily could be healed and has remained cancer-free since. Her case was a breakthrough and signified the start of a new era in the fight against cancer.
The basic idea behind CAR-T and CAR-NK therapies is to attack tumorous cells with the patient’s own cells. NK and T-cells are elements of the human immune system that can be genetically manipulated to recognize cancerous cells as a threat to the body and will thus start to attack them. What may sound simple is in reality a highly complex and time-consuming developmental process. Every single therapy has to be tailored to the respective patient, which makes it a laborious and challenging process.
The volumes required for such personalized therapies are naturally much smaller than for blockbuster medication. However, loss of drug substance remains an issue even - if not even more so - with small amounts, and the pharma industry is challenged with finding logistical solutions that are 100 % safe and reliable.
Scalability and agility in drug manufacturing - as solution
Today’s market is more complex than ever before - timelines are shortened thanks to technical progress and the number of new products being developed and brought to the market has reached an unprecedented scale. There is a noticeable shift to niche therapies that increases the need for more flexibility and agility. The market requires versatile manufacturing processes and variable supply solutions that can be brought to small-scale or large-scale more or less effortlessly as required while at the same time preventing any loss of drug substance.
Selecting the appropriate manufacturing scale to satisfy individual process yields is key when wanting to ensure that product demands are met at every stage - from trials to final launch. In order to keep costs down and minimize risks, scalable solutions are the way forward. Thanks to their modular nature, solutions based on single-use technologies offer a comprehensive and elaborate logistics approach, at the same time ruling out risks of incompatibility and potential product loss or other damages caused by human error.
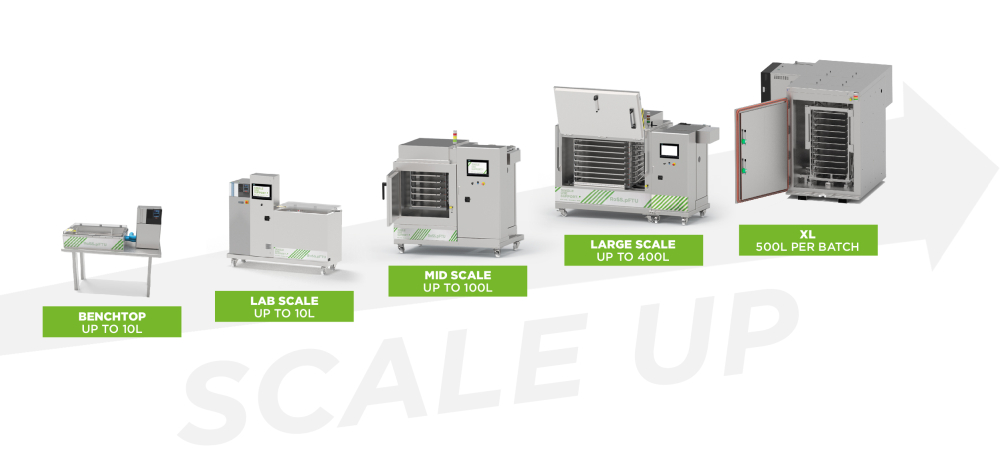
Reducing product loss of biopharmaceuticals with single-use bags
Product loss of biopharmaceuticals is much more than an inconvenience: Delays in certain therapies might be crucial, and the loss of valuable biopharmaceuticals is bound to considerable costs for stakeholders in the healthcare sector.
Within the validation of a supply chain, certain components might turn out to be unsuitable and thus responsible for product loss of biopharmaceuticals – e. g. when single-use bags tend to break. A case study shows just how much cost efficiency depends on the reduction of product loss.
Avoiding product loss of APIs with RoSS®Shell
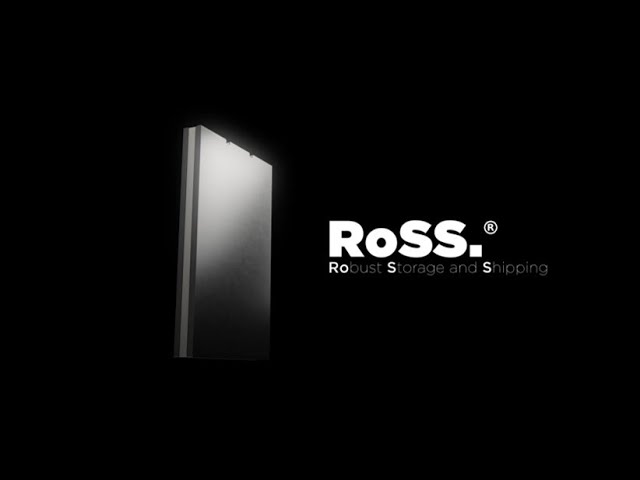
Protection of single-use bags for APIs
APIs (active pharmaceutical ingredients), sensitive raw materials and biopharmaceutical products in general need to be stored and transported in a protected manner in order to ensure product quality and safety. This is why biopharmaceutical companies are in need of new technologies and dedicated solutions for every biomanufacturing process step along the supply chain of biopharmaceuticals – from drug development and biopharmaceutical manufacturing to cold chain management and drug delivery.
With the RoSS® shell (Robust Storage and Shipping) the single-use bag is covered by soft 3D foam, which provides a protective embedding of the single-use bag and absorbs the expanding energy of the bag/liquid of about 8% due to the density drop during freezing. The heavy-duty plastic and stainless-steel lids withstand even the lowest temperatures and make up the robust frame of RoSS®.
The implementation of RoSS® with the effect of a much more robust secondary packaging has diminished the risk of leakages or ruptures towards 0%. The single-use bag and its tubing are perfectly adapted in the RoSS® shell, which in turn maximizes the protective effect. After experiencing the freezing and shipment process with RoSS® for more than 500 times, the product loss has decreased from up to 5% down <0.001%.
Protein activity / potency
As protein activity should be granted even after scaling up the volumes, the target is to reach the same protein activity for different scales after freezing and/or thawing. A general approach for any protein or when comparing different proteins is not possible due to complex and protein-specific denaturation modes.
Sensitivity to denaturation at the ice liquid interface depends on the protein’s reaction. In collaborations, the DoE (Design of Experiment) regarding the effect of different controlled freezing rates and bag fill volumes was successfully tested on Laccase enzyme activity. Results showed that the controlled freezing in the example of plate freezers has a lower impact on the enzyme activity.
With their slow and not very homogenous freezing processes, traditional static freezers lead to large crystalline structures that are the cause of friction, which in turn leads to the destruction of valuable proteins. Up to 20% of proteins can be destroyed like this. In some circumstances the loss of viral potency can rise to even 56%. Effect: After thawing, the substance has lost a considerable amount of its original concentration, thus dropping in value.1 2 3
Fast controlled freezing with plate-based freezer lead to a more homogeneous freezing with higher protein activity - ultra cold freezer

Slow uncontrolled freezing (e.g. in static or blast freezer) decreases protein activity by occurring cryoconcentration.

We have achieved a 0% failure rate out of several batches after implementing RoSS shells
Principal Engineer, Multinational Biotechnology CompanySolution & Conclusion
Size may matter but so does a sophisticated scalable manufacturing and logistics process that is consistent in its flexibility and agility. A closed system that can be adapted offers a versatile solution that can be utilized from early-stage trials and lab purposes all the way to blockbuster production.
Single Use Support is closing the gap between downstream and the fill & finish process with end-to-end solutions from filling to freezing and thawing. The RoSS shell system makes sure that every filled single-use bag is protected during the entire freeze and thaw process, covering storage and shipping. On the basis of single-use bags, they are providing access to a new, reliable and secure logistics process for liquids, allowing you to safely store high-quality substances in a faster and more secure manner, and at a lower loading volume than to date.
Automated processes help increase transparency and improve confidence of delivery. They allow for new levels of transparency and reliability all the way from fill to finish. Single Use Support are utilizing these automated processes in order to minimize the risk of biocontamination and product loss towards 0%, at the same time minimizing the potential for human error and increasing patient safety.
- TU Wien: Freezing Analyse DoE im LabScale – Final Results, https://, Published 2019
- Bezavada A, et al.: Use of Blast Freezers in Vaccine Manufacturing - Bioprocess International, https://bioprocessintl.com/manufacturing/monoclonal-antibodies/use-of-blast-freezers-in-vaccine-manufacture-322317/, Published 2011
- Single Use Support: Challenges in Bulk Drug Substance Logistics: eBook, https://www.susupport.com/challenges-bulk-drug-substance-logistics/, Published 2020