Cold Chain Logistics in the pharmaceutical industry with Single-Use Bags
Table of contents
ShowWhen it comes to the manufacturing and development of biopharmaceutics, single-use bioprocess container exhibit a vast number of advantages for cold chain logistics: Handling is easy, costs – both for acquisition, storage and transport – are low, and as opposed to bottles, single-use bags require almost no space. They are easy to store, yet they offer a high degree of reliability.
This is not to say that there aren’t several phases during the cold chain logistics process that require closer inspection, as medical substances in various developmental stages are shipped around the globe. Some simple hacks can contribute to a safe journey to warrant the single-use bag’s intact arrival at its final destination and keep its precious contents protected from biocontamination and other damages.
Protecting Single-Use Bags The Right Way
Temperatures of -80 °C (-62 °F) can cause single-use bags to rupture and materials to break, which can lead to an excessive waste of materials and resources, especially when it comes to high-quality substances. This is why it is imperative to protect the single-use bag during its controlled freezing – and afterwards – from the outside.
For this reason, Single Use Support has developed a compact shell for the single-use freezing process. It ideally protects the single-use bag during storage, shipping and the bag freezing process. The shell is made of high-quality stainless steel that offers protection against external impact, while on the inside the bag is bedded in specially developed soft 3D foam.
Each shell is tamper-proof so the bag contained in the RoSS Shell cannot be accessed during the entire controlled freezing and logistics process. The RoSS Shells are compatible with single-use bags of all established brands and manufacturers.
Prior to their utilization, all bags should be tested on their integrity. The integrity test kit MITS.2D is based on helium and allows for the detection of microscopically tiny holes in the bags. Deficient single-use bags pose a risk of contamination with bioburden and endotoxins, and in the worst case the entire content of the bag will be lost. As such, deficient single-use bags not only pose a safety risk but the financial aspect plays a role too.
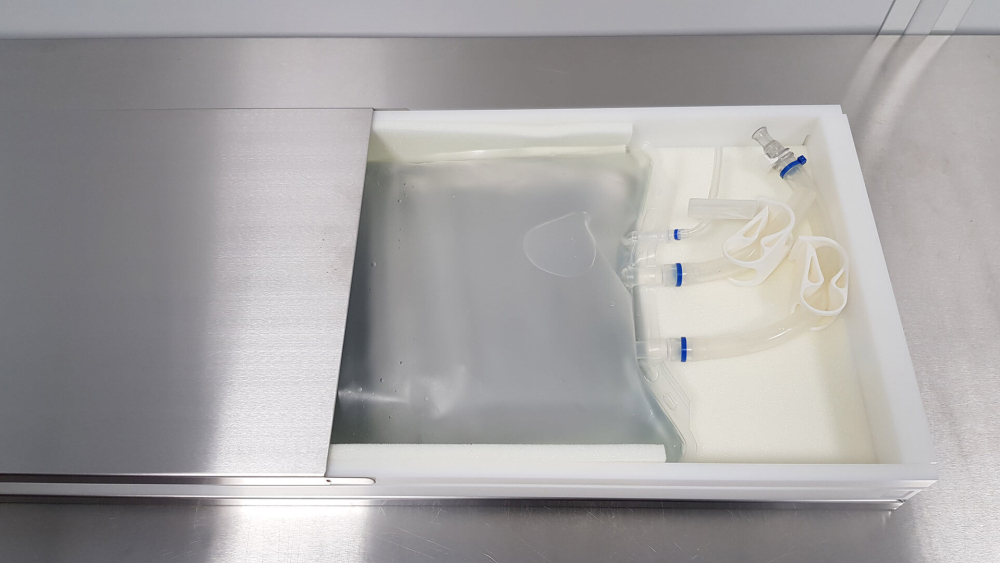
High-quality freezing for advanced cold chain logistics
Most manufacturers use traditional freezers to freeze their valuable biopharmaceutical substances. However, the most logical solution is not always necessarily the best one. The slow freezing process of traditional freezers impacts the quality of the medical substance. It leads to the formation of large crystals that can cause friction and will increase cryoconcentration. As a result, up to 20% of proteins can get destroyed.
This can be countered with fast freezing. So-called plate freezer allows for a shock-like freezing effect that will maximize the quality of frozen biopharmaceutical substances.
Plate freezing leads to a speedy and at the same time controlled freezing of the valuable liquid solution contained in the single-use bag.
During freezing, the bags are protected by stainless-steel RoSS single-use shell, with the stainless steel offering the best possible temperature transfer from freezer to bag to liquid.
The following curve illustrates the freezing speed during single-use freezing:
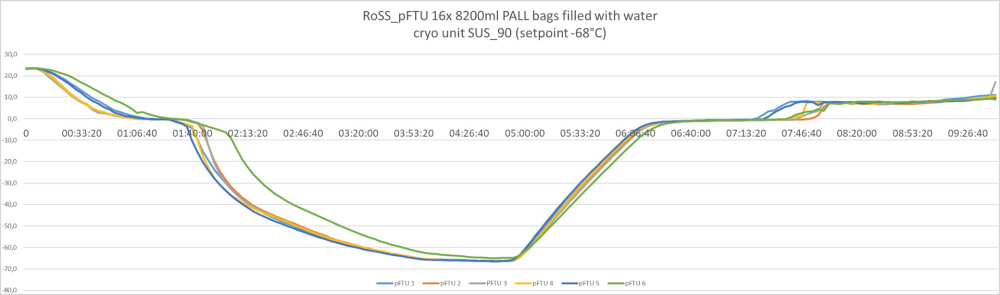
Special Shipping Containers maintain the Cooling Chain during cold chain logistics
As already mentioned, drug substance logistics is characteristic for covering enormous distances during development and production of biopharmaceuticals. In order to maintain the cooling chain during the entire frozen bag shipment and storage, specialized shipping containers are required for a reliable pharmaceutical cold chain management.
That is why we have developed cold chain shipping boxes and ultra cold storage containers with minimum space requirements to keep the RoSS Shells and their contents cool after the bag freezing process.
The containers can carry up to 20 RoSS Shells and are, like the shells themselves, made from robust stainless steel. The cooling system inside the isolated containers is based on dry ice or so-called “Phase-Change Materials” (PCM).
The containers are equipped with GPS chips so they can be tracked and localized throughout their journey. At the same time those chips allow for a constant monitoring of the temperature inside the containers to guarantee for a reliable and safe frozen bag shipment.
FAQs
What is cold chain logistics?
Cold chain logistics describe measures that are taken during transport and storage of temperature-sensitive products in order to prevent loss in quality and safety. By maintaining a temperature-controlled environment, sensitive products are shielded from ambient temperature and temperature excursions, while they are stored and transported within a temperature range fit for the respective product.
Depending on the product that is to be stored and shipped, there are different measures to be taken within cold chain logistics. Frozen food, for instance, requires different levels of refrigeration and temperature monitoring than temperature-sensitive pharmaceutical products like gene therapies or COVID-19 vaccines.
What role does cold chain logistics play in the pharmaceutical industry?
Pharmaceutical cold chain logistics play a crucial role in the production and distribution of several biopharmaceutical products and are thus an important constituent of pharmaceutical supply chains. With regards to the individual requirements of specific products in terms of storage and transport temperature, cold chain management in the biopharma industry requires dedicated cold chain solutions to facilitate storing and transport of highly valuable drug products with a minimized quality loss and safety risks.