Bioconjugates manufacturing & the advances with single-use technology
Table of contents
ShowBioconjugates have been used to develop a range of novel therapeutics, including antibody-drug conjugates (ADCs), which have shown great potential in cancer therapy.
The manufacturing of bioconjugates is a complex process that involves linking a drug payload with a targeting moiety using a linker. The process is highly specific and requires careful optimization to ensure that the bioconjugate is effective and safe for use in patients.
Single-use technology has revolutionized the manufacturing of bioconjugates by offering a range of benefits over traditional stainless-steel manufacturing. Therefore, this article will pay special attention to this subject.
Drug Substance Bioconjugation Service
Bioconjugation services include linking a drug substance (API) to a specific biomolecule such as protein, antibody (monoclonal antibody), peptide, or nucleic acid. Various companies offer bioconjugation services, including Lonza, Catalent, and Abzena, to name a few. These companies specialize in conjugation techniques for different classes of biologics and offer a range of services for custom synthesis, process development, scale-up, and commercial manufacturing of bioconjugates.
One of the most significant classes of bioconjugates is antibody-drug conjugates (ADCs). ADCs consist of an antibody that is linked to a cytotoxic payload, which can kill targeted cells. ADCs have gained popularity in cancer therapy as they offer the potential for improved efficacy and reduced toxicity compared to traditional chemotherapy. PEGylation of proteins, antibody-siRNA conjugates, and vaccine conjugates are some other examples of bioconjugates.
Manufacturing of Bioconjugates faces significant challenges due to the toxicity of the cytotoxic payload. The process development and optimization of ADCs involve understanding the physicochemical properties of the antibody, the linker, and the payload. Optimizing the techniques for conjugation and the manufacturing process, with the switch to single-use technologies as an example, can overcome these challenges and improve the overall safety in ADC manufacturing.
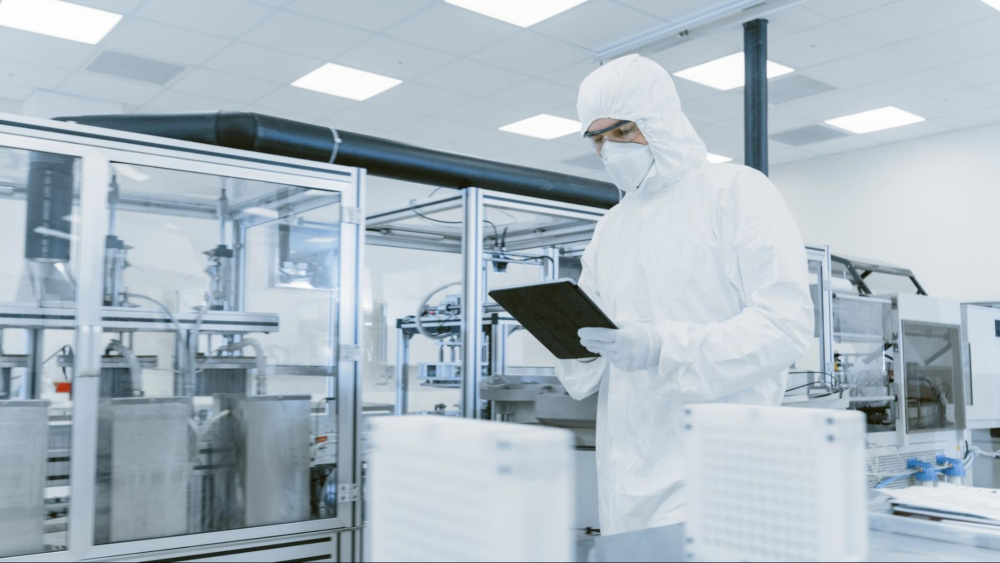
cGMP manufacturing of bioconjugates
GMP or cGMP manufacturing of bioconjugates is a critical step in the production of safe and effective therapeutics. The process involves strict adherence to current good manufacturing practices (cGMPs) to ensure the quality, safety, and efficacy of the final product. In addition, the regulations ensure other aspects like safety of employees during production, efficiency for manufacturing companies and the quality of the manufacturing process - for example, reproduction is enabled by standardized processes. Single-use technology has made cGMP manufacturing more efficient and flexible, allowing for faster scale-up and commercial production.
CDMOs for bioconjugates manufacturing
CDMOs, or Contract Development and Manufacturing Organizations, play a crucial role in bioconjugate manufacturing, as they offer a range of expertise and services in drug development, including process engineering, scale-up to commercial scale, services like characterization or formulation development and cGMP compliant manufacturing.
Some of the leading CDMOs for bioconjugate manufacturing include GTP Bioways, Lonza, Abzena, and Ajinomoto Bio-Pharma Services. These companies offer customized services for the development and manufacturing of a variety of bioconjugates, including antibody-drug conjugates (ADCs), PEGylation of proteins, antibody-siRNA conjugates, and vaccine conjugates.
When producing bioconjugates, or ADCs to be specific, working with a CDMO could provide several advantages for pharmaceutical companies. ADCs require specialized expertise and facilities, which can be costly for a pharmaceutical company to develop in-house. By partnering with a CDMO, a pharmaceutical company can access the necessary manufacturing capacity, expertise, and regulatory compliance to bring their ADC to market efficiently and cost-effectively.
Most CDMOs are experienced with single-use technologies, which can increase flexibility, reduce contamination risks, and decrease production times in ADC manufacturing. Working with a CDMO can help a pharmaceutical company bring their final ADC to market faster and with less risk, while allowing them to focus on their core competencies.
The application of single-use technologies has become increasingly popular in the CDMO industry, as they offer a range of advantages over traditional stainless steel equipment in bioprocessing. Therefore, CDMOs are continuing to invest in single-use technologies to stay competitive and meet the evolving needs of the biopharmaceutical industry.1
ADC manufacturing & the advances with single-use technology
The use of single-use technology has revolutionized the development and manufacturing of ADCs. Single-use technology offers a range of benefits over traditional stainless-steel manufacturing, including flexibility, cost-effectiveness, and advanced bioburden management.
And above all, it is a tamper-evident, closed system. The automated end-to-end solutions thus ensure maximum safety in processing.
The technology has made it easier for companies to develop and manufacture ADCs, leading to a growing number of therapeutics in preclinical development and clinical trials. This is leading to huge advances in ADC manufacturing, concerning almost all production steps of antibody-drug conjugates.
Flexible Manufacturing Services
Flexible manufacturing services are not only but especially crucial for CDMOs offering the development and commercialization of bioconjugates. Single-use technology has made it easier to offer flexible production, allowing manufacturers to scale up and meet the demand for commercial supply. This has led to shorter timelines and reduced costs, making bioconjugates more accessible to patients.
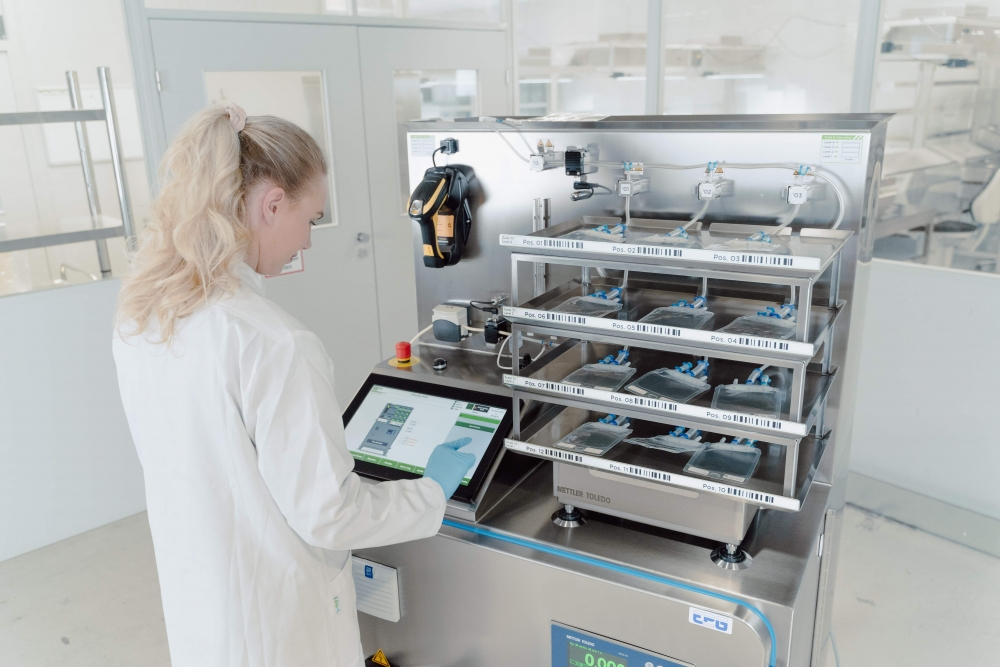
Cost Reductions
Cost reductions result from the combination of the advantages described above. The modular single-use technologies are more efficient and cost-effective than traditional stainless-steel manufacturing. Furthermore, they eliminate the need for expensive and time-consuming cleaning and validation processes. This allows ADCs to be manufactured at a feasible cost to offer the product to the market.
Outlook for Bioconjugate Manufacturing Services
The outlook for bioconjugates manufacturing is bright, with the spread of improved technologies, such as single-use technology, allowing for greater flexibility and cost-effectiveness.
The popularity of single-use technology in the manufacturing of bioconjugates is expected to continue to grow. The ability to rapidly scale-up and manufacture high-quality drug products using single-use technology is a significant advantage in the biopharmaceutical industry. As demand for biologics and ADCs continues to rise, the adoption of single-use technology is likely to become increasingly common in the commercial scale manufacturing of these products.
Several companies provide single-use technology solutions for ADC manufacturing, including Single Use Support, Merck, GE Healthcare, Sartorius, and Thermo Fisher Scientific.
As a leader in providing fully automated biopharmaceutical end-to-end solutions based on single-use technology, Single Use Support is proud to improve bioconjugate and ADC manufacturing in making production processes safe, efficient, cost-effective and flexible.
FAQs about bioconjugates manufacturing
What Services could a CDMO offer for ADC manufacturing?
CDMOs for ADC manufacturing typically offer services such as process development, scale-up, optimization, characterization, validation, and commercial manufacturing of drug substance and drug product. They also provide services for clinical development, including preclinical and clinical trials, as well as offering chromatography and assay development. CDMOs also provide technical support, including white papers and webinars, to educate their clients about the latest advancements in ADC manufacturing.
How are bioconjugates manufactured?
Bioconjugates are typically manufactured through a process called bioconjugation, which involves attaching a payload molecule to a monoclonal antibody (mAb) or other biologic via a linker. This process can be performed using a variety of techniques, including chemical conjugation, enzymatic conjugation, and genetic engineering.
What is the bioconjugation process?
Bioconjugation is the process of covalently linking two or more molecules together, typically a protein such as a monoclonal antibody (mAb) or a small molecule drug, to create a single entity with enhanced therapeutic properties.
- How a CDMO can Support ADC Manufacturing, https://www.adcreview.com/news/how-a-cdmo-can-support-adc-manufacturing/, Published 15.08.2021