Safe Filling & Aliquoting of Antibody Drug Conjugates (ADCs)
Table of contents
ShowThe safe handling of ADCs or other HPAPIs is a complex and elaborate process that requires specialized facilities and a safe, sterile environment.
The filling/aliquoting step in particular calls for great care and specific equipment to ensure sterility and rule out any potential cross-contamination as well as potential harm to handling staff. After all, most ADCs contain extremely active cytotoxic molecules, making process safety in fluid management a top priority for biopharmaceutical manufacturers as well as CMOs.
With growth rates expected to remain in the billions, it pays off to put into place and invest in technologies that facilitate automated and scalable filling/aliquoting processes, that are safe and sterile.
Hurdles in safe handling of ADCs
The production of ADCs call for cGMP-compliant aseptic environments that are to ensure containment of the highly toxic drug compounds. This is to ensure that the drug products are both
- consistently efficacious and
- safe from cross-contamination or bioburden
Not only are these requirements governed by rigorous administrative and quality standards but they present significant operational challenges.
The processing and handling of substances and molecules such as monoclonal antibodies and toxic payloads calls for a multi-disciplinary approach. In order to allow for streamlined sterile filling and aliquoting, equipment that is versatile and compatible with various needs is indispensable.
The entire filling process must be validated. This includes validation of the equipment, the environment, and the process itself.
Apart from ensuring a clean environment that is free from bioburden, all primary packaging, such as single-use bioprocess containers, must be sterilized. This can be achieved by autoclaving or gamma irradiation.
When utilizing single-use technologies, however, manufacturers and CMOs can dispense with these processes, because all components are supplied sterilized. This means that time-consuming and cost-intensive cleaning or sterilization processes are no longer required.
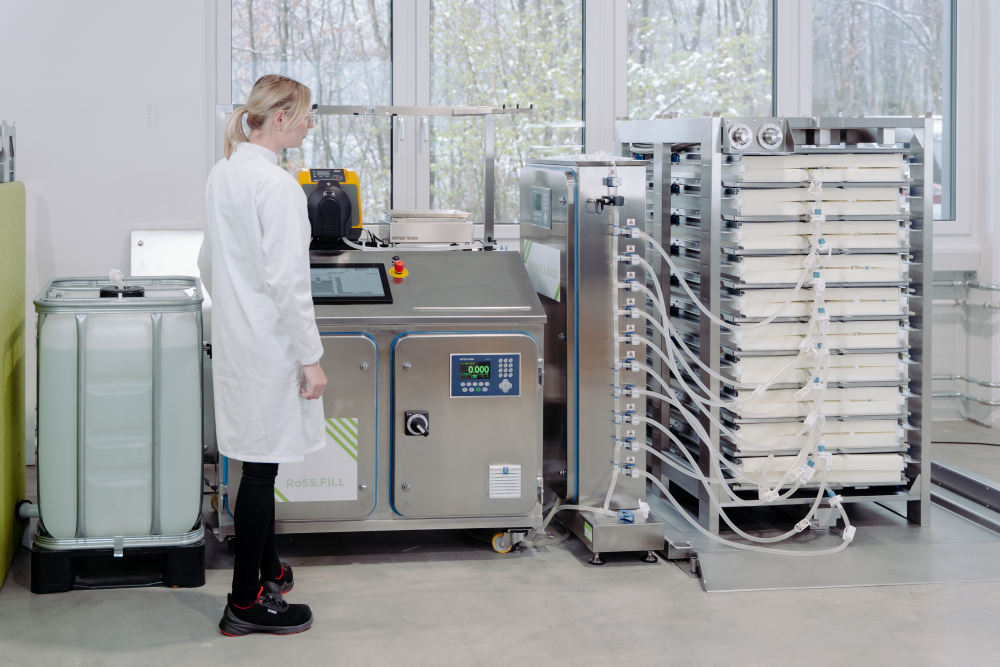
Solutions for safe aliquoting & filling of ADCs
Considering the complexity levels of antibody-drug conjugation, any advances made to improve or simplify the process are welcome news in the world of biopharma.
Single-use systems are closed systems that ensure the most important aspect in ADC processing - Safety. Even better if those advances come with the added benefits of being able to reduce costs and add to a more sustainable manufacturing and logistics process.
Single-use systems are closed systems that ensure the most important aspect in ADC processing - Safety.
This is the case with single-use technologies, which are replacing traditional stainless-steel systems at an increasing rate. Single-use components can simplify systems for aliquoting and filling of ADCs.
Single-use components, such as sterile
- tubing,
- filter cartridges, or
- bioprocess containers
all contribute to the design of closed systems for the handling of potentially toxic substances that are required for the production of ADCs and other therapeutic drugs. By eliminating the need for manual handling, any risks of contamination can basically be ruled out.
Advantages of single-use technology
Single-use technology has several advantages over traditional stainless-steel equipment, not only because the latter requires extensive cleaning and sterilization between uses. In addition to being delivered sterilized, the systems can be assembled in modules, making them flexible to use. This also makes processes scalable - and it allows for quick and easy adaptation, making it easier to streamline operations.
In the long run, single-use technologies also help manufacturers and CMOs become supplier-independent, but they also contribute to cutting prices and reducing a company’s footprint.
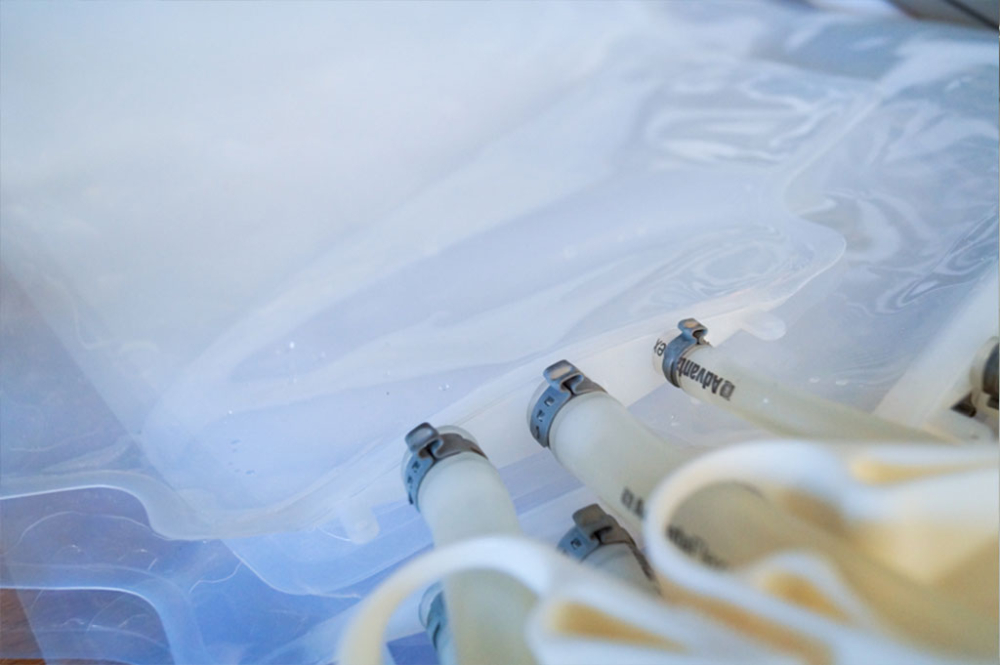
Single-use aseptic filling in detail
Thanks to their scalability, single-use technologies can cover the entire spectrum from small-scale lab sampling to full-scale bulk production. While lab samples are miniscule, bulk drug substance needs to be aliquoted in large bags, and protected for a safe and reliable transport.
As a fully automated and scalable aseptic filling and filtration system for bags or bottles, Single Use Support’s RoSS.FILL enables maximum flexibility for both the aseptic filling and draining process. With RoSS.FILL, it is possible to fill unlimited volumes per batch at a speed of up to 300 liters per hour. And because the entire process is fully disposable, it guarantees an absolutely sterile filling and aliquoting process.
The platform is available as a standard version that can be adjusted to meet varying needs - for small-volume 3D bags all the way to 1,000 L and more. Depending on the project criteria or requirements, for example speed, filling accuracy, scalability or homogeneity, with RoSS.FILL Single Use Support can fulfill all needs.
Summary - How single-use technology will advance ADC manufacturing
By employing single-use technology, CMOs and manufacturers can significantly advance ADC manufacturing while also increasing process efficiency, process flexibility and sustainability and reducing costs.
Some ways single-use technology can advance ADC manufacturing include:
- By reducing the risk of cross-contamination between batches of products. This is particularly important for ADC manufacturing because cytotoxic drugs are highly potent and can be hazardous to both patients and workers.
- By eliminating the need for expensive cleaning and validation processes that are required for traditional stainless-steel equipment. This reduces the overall cost of production and makes ADCs more accessible to patients.
- By increasing flexibility and speed, which allows manufacturers to produce smaller batches more frequently, thus reducing the risk of drug shortages and improving patient access to life-saving treatments.
- By improving product quality, minimizing product loss and reducing filling deviations. This means that ADCs produced using single-use systems are more consistent and have a higher level of purity.
- By enhancing sustainability due to minimized need for cleaning and thus more economical use of resources
In summary, single-use technology can significantly advance ADC manufacturing by improving efficiency, reducing costs, and increasing flexibility. As the demand for ADCs continues to grow, the adoption of single-use technology is likely to become more widespread.