cGMP cell banking: Aliquoting & controlled freezing of cells in less than 1 hour
Table of contents
ShowAs the market for high-quality biopharmaceuticals is growing rapidly, the importance of cell banking as the basis for high-standard products is increasing simultaneously. In order to achieve a streamlined production process with reproducible, impurity-free cell lines, cGMP cell banking and new inventions in biotechnology key elements for streamlined manufacturing processes.
Fully automated solutions are offered to make GMP cell banking and cGMP cell banking easier to achieve. Single Use Support’s solutions do not only reach out to help make the handling of cell banks safer and more efficient, but also help to support smaller-scale projects through scalable solutions. And faster - if irequired.
Cell Bank Manufacturing
Cell bank manufacturing is an essential step in the production of biopharmaceuticals or stem cell research. Cell lines can range from microbial and bacterial cells to mammalian cells. A master cell bank (MCB) is established after cell line development in vivo or in vitro. It is the main factor for continuous quality during manufacturing and has an important influence on the outcome of a successful drug product.
As the repetition of subculturing over different generations can result in genetic changes and cross contamination, it is essential to work with a two-bank system to preserve the product’s integrity through sufficient supply of a uniform cell population. Biopharmaceutical drugs mostly work on the base of a master cell bank, which is multiplied into a working cell bank (WCB). Cell bank production makes it easier to maintain overall quality through the preservation of the original cell substrate. Read more: How to maintain a cell bank?1
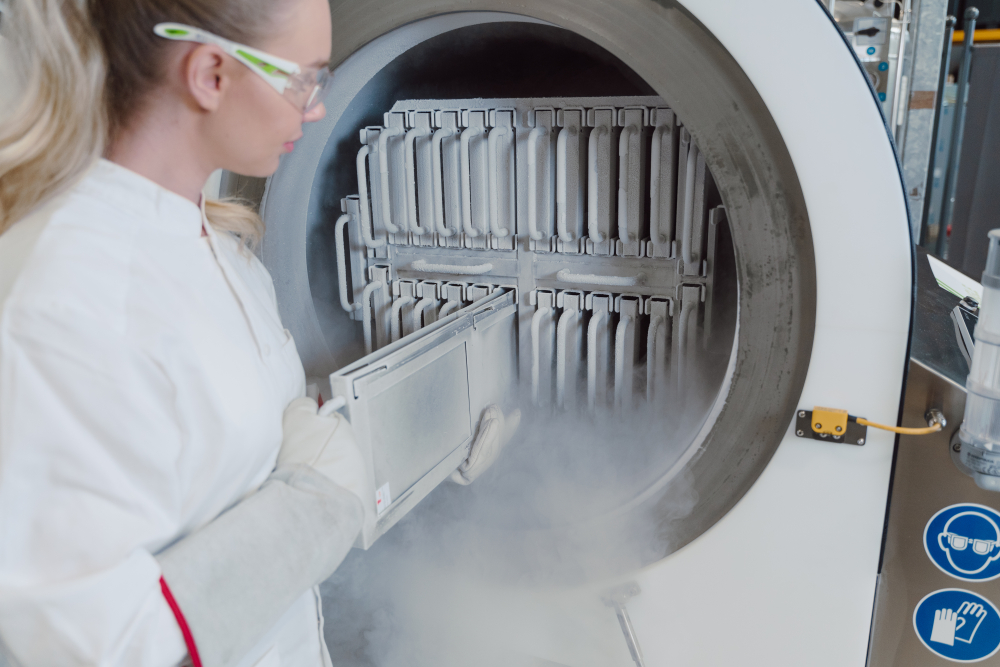
Storage of Cell Banks
To maintain the cell culture’s viability during cell banking storage, cryopreservation has proven to be the most efficient method. Before the cell lines are stored in vials or single-use bags, they are multiplied to ensure a supply of identical cells. Often, cryoprotection agents are used to protect the material from biodegradation through crystallization during freezing. Once the small containers are labeled with the cell line’s information, they are put into cryogenic freezers, where they are frozen and stored at -170 °C/-274°F in vapor-phase liquid nitrogen.
It is important that this process is acted out in a steady and controlled manner to prevent damage in the cell line. Full characterization and regular assays as quality control help to ensure cell viability. As cell banks and adventitious agents are prone to impurities, regular testing for bacteria, mycoplasma and viruses has to be performed to guarantee sterility and genetic stability of the raw materials.
Requirements for GMP & cGMP cell banking
To ensure that pharmaceutical products are safe for use by patients, the FDA has established mandatory regulations for pharma manufacturing services. Good manufacturing practices (GMP) are designed to prevent product contamination, mix-ups through wrong labeling and incorrect ratios in production batches. Principles like cleanroom and methods for quality assurance like stability testings in clinical trials have to be performed until the end of production and involve thorough documentation of aspects such as cleanliness, worker qualifications or equipment verification.2
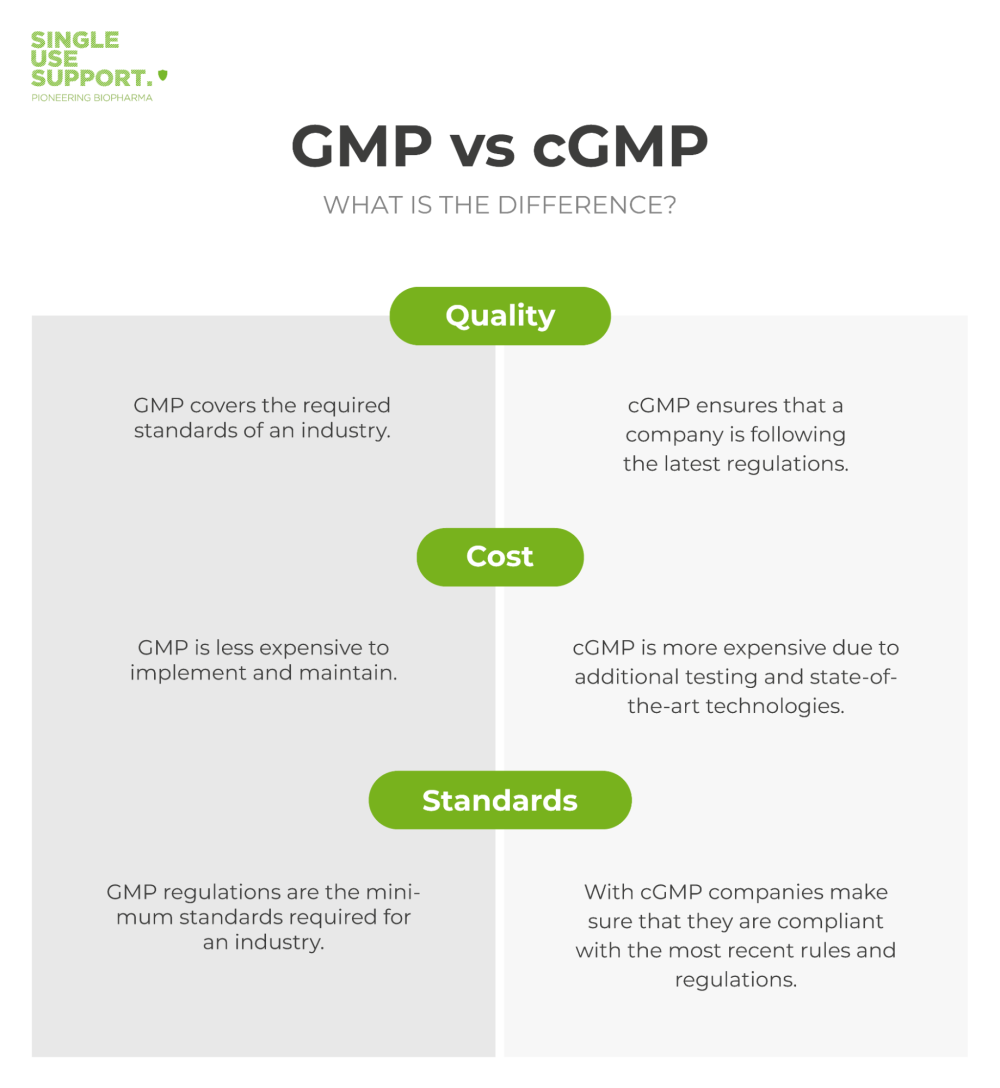
Further, current good manufacturing practices (cGMP) according to FDA-standards have to be applied during manufacturing, processing, and packaging of pharmaceuticals. They are constantly updated and have the purpose to allow for safe medical products through different monitoring and testing techniques. One could say the main difference between GMP and cGMP guidelines is that GMPs are meant to guarantee safety, quality, and purity of pharmaceutical products through process validation, while cGMP guidelines shine a light on the most recent regulations.The main aim for companies is to comply with both. However, by concentrating on cGMPs, both standards can be met most of the time due to a lot of overlaps.
The most recent regulation, which comes into force at the end of August 2023, is EU GMP Annex 1, a regulatory guideline for manufacturing sterile medicinal products. It's set by the European Medicines Agency (EMA) and FDA, focusing on aseptic processing and contamination control to ensure product safety and quality. A significant aspect influenced by Annex 1 is the use of single-use assemblies in fluid management, emphasizing a risk-based approach for integrity and sterility in closed systems.
As cell banks are particularly prone to contamination and impurities if not handled correctly, cGMP compliance is of utter importance and mandatory during pharmaceutical production.
Read more about that topic in the article: Meeting cGMP requirements with single-use technology
cGMP compliant solutions for cell banking
The production of pharmaceuticals and new drug compounds comes with different challenges. Cell banks have to be handled efficiently and carefully to guarantee the best-possible quality.
Even freezing and thawing rates must be specified to achieve that. MBC and WBC have to be checked for plasmid impurities regularly, which includes testing of amplification reagents. Especially, cell lines used in vaccine production have to be tested for tumorigenicity through gene sequencing, cell line characterization and testing like antibody tests for virus detection. The risk of impurities, thus contamination in the liquid transfer must be avoided at all costs.
To help overcome these challenges, Single Use Support has designed fully automated solutions that allow for safe filling, freezing/thawing and transport. Scalable bags and plate-freezing make it possible to achieve best results for any project size.
Cell freezing: Fast and reliable
Speed and accuracy are both important factors when it comes to handling cells. During drug manufacturing, timelines are often tight and delays can lead to bottlenecks. Due to their sensitive nature and risk of contamination, the cold chain has to be preserved and the materials have to be handled quickly and with care.
Single-use technologies streamline fluid management and cold chain, speeding up the process of aliquoting and freezing cells with liquid nitrogen down to -170°C/-274°F in less than one hour.
However, the speed is not always what counts. Especially, when product quality might suffer from a fast fluid & cold chain handling. Too fast freezing can negatively influence cell survival rates due to potential damages on cellular structures. The recommended freezing rate of CHO cells to achieve optimal cell recovery ranges from -1°C/min to -4°C/min. This would mean a freezing duration between 100 and 25 minutes, when freezing from ambient temperature to -80°C. 3
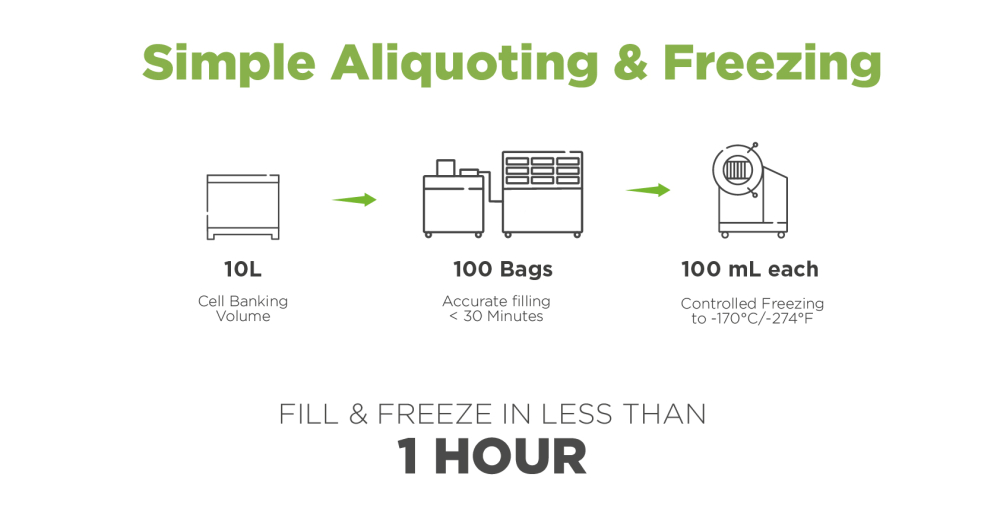
cGMP compliant Aliquoting
For cGMP compliant aliquoting of cells, fully automated solutions are the future for quick and safe handling of substances during the manufacturing process. To support your project, while staying cGMP compliant, Single Use Support developed RoSS.FILL CGT, a cell and gene therapies filling system, which allows for aseptic, automated filling into bags from 1 ml to 1000 ml.
With RoSS.PADL, a platform designed to standardize the homogenization and cooling of single-use bags, the single-use bags are gently kneaded during cooling to ensure a homogenous mixture of the substance before dispensing. The cooling and kneading mechanisms can be placed side by side to scale-up with one control system, to meet your individual project’s needs.
cGMP compliant Freezing of cells
As cell banks are sensitive to changes in temperature, it is important that cell freezing happens at a steadily fast rate. One of a kind and currently the only cryogenic controlled rate freezer using liquid nitrogen on the market, Single Use Support’s RoSS.LN2F is the most efficient way for cGMP compliant freezing of cells.
The cryogenic controlled rate freezer is able to cool cells down to -170°C/-274°F without exposing cells directly to the cold and without the help of mechanical compressors. With all its qualities combined, it ensures safe, low-maintenance and energy efficient cell handling. Freezing down to -80°C/-112°F and controlled thawing of cells is possible with the RoSS.pFTU Lab Scale, providing optimal cGMP compliant cell handling in laboratories. Frozen cells can then be transferred at below -47°C to rapid cooling, for example with liquid nitrogen tanks, whithout noticeable negative effects on post-thaw cell viability.4
The importance of cell banks for the development of new biopharmaceuticals is constantly growing, and consequently the demand for cGMP and GMP compliant manufacturing methods is increasing. However, many companies specializing in filling, freezing, and thawing do not offer smaller-scale cell banking services because they lack the relevant equipment.
Single Use Support’ product solutions are easily scalable, this issue can be resolved, while staying cGMP compliant during all parts of the production process. Fully-automated solutions and aseptic filling technologies eliminate the contamination risk through human errors while allowing for a more streamlined and efficient production process at the same time.
Conclusion: cGMP & GMP cell banking
The importance of cell banks for the development of new biopharmaceuticals is constantly growing, and consequently the demand for cGMP and GMP compliant manufacturing methods is increasing. However, many companies specializing in filling, freezing, and thawing do not offer smaller-scale cell banking services because they lack the relevant equipment.
Single Use Support’ product solutions are easily scalable, this issue can be resolved, while staying cGMP compliant during all parts of the production process. Fully-automated solutions and aseptic filling technologies eliminate the contamination risk through human errors while allowing for a more streamlined and efficient production process at the same time.
- Cell Banking, http://dx.doi.org/10.1016/B978-0-12-410396-2.00003-7, Published 2014-12-06
- , Published
- Brandmayr P.: Optimization of the freezing process with a liquid nitrogen freezer to increase cell viability of a mammalian cell line., https://www.susupport.com/knowledge/biopharmaceutical-products/cell-gene-therapy/study-optimizing-cell-viability-during-cell-freezing , Published 2024
- Meneghel J. et al: Physical events occurring during the cryopreservation of immortalized human T-cells., https://pubmed.ncbi.nlm.nih.gov/31120989/, Published 2019