Microbial Fermentation Manufacturing: Advances through single-use technologies
Table of contents
ShowMicrobial fermentation is a powerful, flexible microbiology process used to generate microbial cells or biomass such as proteins and enzymes for the production of vaccines and therapeutics.
Consequently, fermentation technology is a rapidly growing field within the biopharmaceutical industry. However, growth and ongoing development are accompanied by constant challenges, including
- product quality and
- potential of toxic by-products
- lack of scalability
- cost-effective solutions
- timelines
- capacities
- capabilities
Many of these challenges in fermentation manufacturing can be solved by replacing traditional systems with single-use technologies. A change to more agile systems supports manufacturers and CDMOs, if manufacturing is outsourced, so such a move pays off twice.
Production of pharmaceutical compounds through microbial fermentation
As a multi-disciplinary methodology, fermentation technology offers the option to recover and purify specific desired APIs out of the molecular repertoire. The process involves the use of microorganisms that can be harvested in much bigger quantities and at higher levels of concentration than the results of mammalian cell expression.
There is a clear preference from chemical synthesis shifting to microbial fermentation, but there are still a number of hurdles to be taken. One of the most important ones is to find integrative solutions that are flexible and allow for scale-up, still keeping product quality high.
However, apart from an existing technology gap and the need for scalability, there are other issues that need to be addressed in pharmaceutical fermentation. These include, most notably, timelines, costs, and expertise.
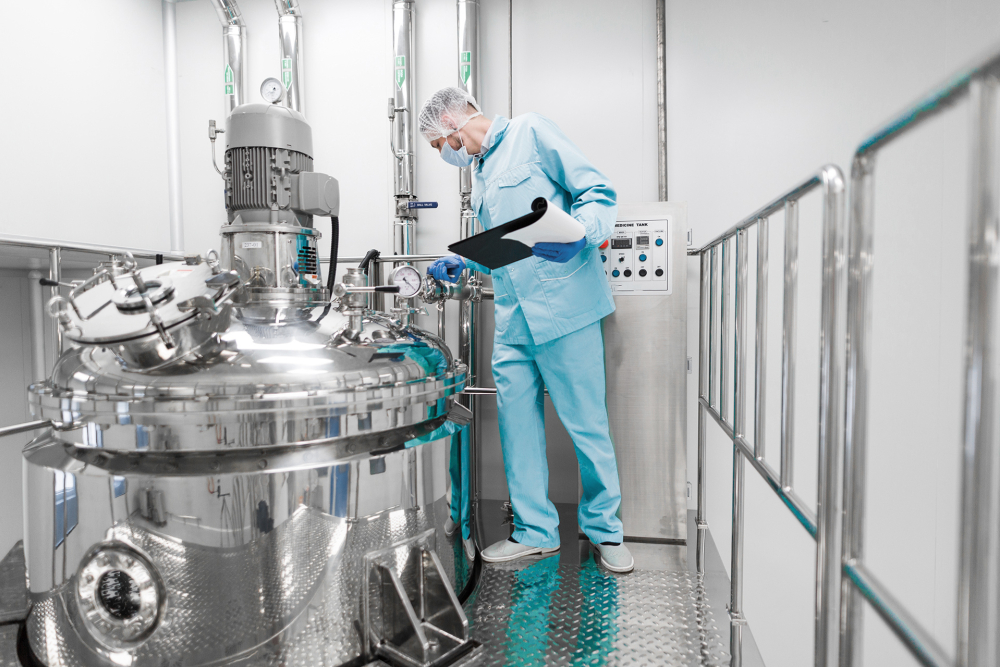
Application of single-use technology in microbial fermentation manufacturing
So far, the common approach in fermentation processes was to use stainless-steel bioreactors for microbial production. And even though single-use systems are gaining traction, there is still a lot of room for optimization, both in terms of process development and manufacturing process.
As one of the key topics in many biotech processes, scalability needs to be considered from the initial stages of process development. Manufacturers have to be able to achieve immediate scale-up once the product has been given the green light for production on an industrial scale. However, not only does large-scale production call for additional equipment and different infrastructures. The entire process requires careful monitoring to ensure stability as well as product quality, process control and safety.
This is where single-use technologies come in: The modular systems provide efficiency, flexibility, scalability and reliability along the fluid management and cold chain logistics in upstream and downstream processing.
How are single-use technologies contributing to drive the microbial fermentation industry?
While cost and time savings could be among the most cited advantages of single-use technologies in biotechnology, they are only representative of one aspect. Far more importantly, they drive agility, flexibility, and speed to market while also reducing the risk of cross-contamination and improving sustainability in contrast to stainless steel. However, there are also differences within single-use technologies.
Below are some of the most important benefits of single-use technologies employed in biomanufacturing, with a focus in microbial fermentation:
- Single-use technologies create good conditions for fast freezing of large volumes - at least the solutions from Single Use Support do
- More cost-effective processes thanks to an increased flexibility in responding to on-demand production
- Accelerated speed to market by removing the need to clean, sterilize and recycle components - again, at least solutions from Single Use Support do so
- Improved sterility thanks to automated processes and improved controls
- Reduced need for cleaning and minimized process downtime thanks to pre-assembled and sterilized fluid flow paths
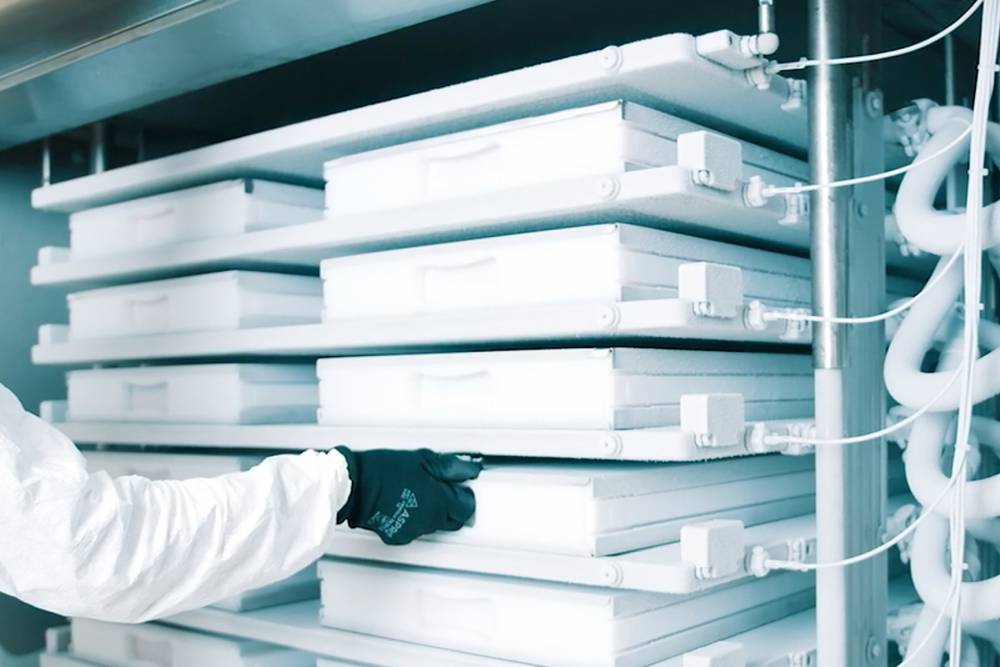
What matters in microbial fermentation manufacturing?
With the biologics market expected to reach a volume of USD 450 billion by 2025, the time-to-market rate is increasing continuously, but apart from time there are important factors. Below we have provided some answers and solutions for the most pressing topics in microbial fermentation:
- Speed: Fast processing of the ferments is important to maintain product quality. In the case of downtime or transport, the liquids are advised to be frozen quickly. This is to avoid affecting the viability of the product as in other freezing methods, e.g. spray drying.
- Quality: Product activity is kept high by freezing the substances quickly and homogeneously. Plate-based freezing in single-use bags is the best way to do so.
- Sustainability: Manufacturing can become more environmentally sustainable by employing processes that save material, time and energy consumption. Manufacturing based on single-use technologies, unlike stainless-steel, is more efficient and consumes less energy due to the elimination of cleaning.
- Safety: This can be achieved through a higher level of automation, a lower risk of human error or contamination, and improved protection offered by single-use components.
- Compliance: This can be ensured by using cGMP-compliant single-use components that are, notably, more efficient, cost-effective, and scalable than stainless-steel tanks.
Single-use consumables for microbial fermentation
The clear trend towards single-use technologies brings with it an increasing range of components and products. Single Use Support’s solutions are available for or adaptable to different processes, respectively process and logistics steps from upstream to downstream, freezing and fill/finish, storage and shipping.
IRIS bioprocess containers can be tailored to different needs to store, ship and freeze anything from cell culture samples to drug substances on a large scale.
RoSS shells protect single-use bags safely. The robust solution for storage and shipping during cold chain management protects any bioprocess container to reduce product loss towards 0%.
IRIS single-use assemblies ensure a GMP-, FDA- and ISO-compliant sterilized fluid flow and aseptic handling of pharmaceutical products. Availability and compatibility prevents downtime thanks to an uninterrupted supply chain.
RoSS.SHIP shipping containers are ideal for the storage and monitored shipping of bulk drug substances by maintaining the cold chain for almost and offering integrated Smart Tracking.
In addition to single-use consumables, there are end-to-end processes based on single-use technologies that help drive efficiency and safety while reducing product loss and human error. Since they are primarily based on single-use technologies, those automated processes allow for the greatest process flexibility while also complying with important cGMP/GMP criteria.
Single Use Support’s flexible end-to-end process solutions for advanced fluid management and freeze-thaw logistics facilitate aseptic automated aliquotation into single-use bioprocess containers and controlled freezing to -80 °C. 200 liters or more can be filled and frozen in less than 8 hours. Read more: Fast filling and freezing large volumes for fermentation
The vendor-agnostic and modular systems simplify the handling of process intermediates on a large scale. They can be used for different areas of applications like plasmid DNA, viral vectors, antibody-drug conjugates and vaccine manufacturing.
Automated end-to-end processes based on single-use technologies
In addition to single-use consumables, there are end-to-end processes based on single-use technologies that help drive efficiency and safety while reducing product loss and human error. Since they are primarily based on single-use technologies, those automated processes allow for the greatest process flexibility while also complying with important cGMP/GMP criteria.
Single Use Support’s flexible end-to-end process solutions for advanced fluid management and freeze-thaw logistics facilitate aseptic automated aliquotation into single-use bioprocess containers and controlled freezing to -80 °C. 200 liters or more can be filled and frozen in less than 8 hours. Read more: Fast filling and freezing large volumes for fermentation
The vendor-agnostic and modular systems simplify the handling of process intermediates on a large scale. They can be used for different areas of applications like plasmid DNA, viral vectors, antibody-drug conjugates and vaccine manufacturing.
FAQs about microbial fermentation manufacturing
Why are E. coli bacteria one of the preferred microbes used in fermentation processes?
Escherichia coli is one of the preferred microbes for cell factories used in the fermentation process because of their short fermentation times and high cell density. In addition, E. coli stands out thanks to their simple and rapid strain development. All of these are highly desirable characteristics in microorganisms used for the production of biopharmaceuticals and other pharmaceutical products.
What does microbial fermentation entail?
Fermentation is a biochemical process that occurs within cells. During fermentation, microorganisms metabolize organic compounds to produce energy and generate various end products. Strain selection and optimization, media and process development are - besides the ability to scale-up - some of the key elements of microbial fermentation. Read more about the differences between microbial fermentation and mammalian cell culture
Why has microbial fermentation become so popular?
This process results in larger volumes and higher concentrations than is possible with mammalian cell expression. It involves the use of bacteria like E. coli, yeast - for example Pichia pastoris - and other microorganisms to generate APIs like acids, recombinant proteins and monoclonal antibodies.
What exactly are APIs?
APIs are Active Pharmaceutical Ingredients used in vaccines and medical therapies. The molecules that are of primary interest to the pharmaceutical industry can be cultured and grown via microbial fermentation. They include small molecules such as short peptides, larger molecules like proteins and nucleic acids (DNA, RNA) and macromolecules such as lipids and carbohydrate polymers. All of them could serve as a drug’s Active Pharmaceutical Ingredient (API). (Source: manufacturingchemist.com)