Bioprocess tubing – choosing the right option
Table of contents
ShowTubing solutions for biopharma
The selection of the right bioprocess tubing solutions plays a pivotal role in maintaining product quality and process efficiency in pharmaceutical fluid management. Whether it is for transferring pharmaceutical liquids, conducting biopharmaceutical experiments, or other critical applications, the choice of biopharma tubing, and single-use assemblies, is far from trivial in biopharmaceutical fluid management.
Therefore, in this blog post, we will take a closer look at different considerations on bioprocess tubing solutions for pharmaceutical liquids. It's important to note that this is a general article providing an initial glimpse into the world of pharmaceutical tubing solutions. We will explore their exciting fields of application and compare multi-use and single-use tubing systems, illustrating why Single Use Support believes that single-use solutions pave the way of success.
Bioprocess tubing solutions
Bioprocess tubing solutions in the life sciences and biopharma sector encompass a wide range of applications, each with its own set of unique challenges and requirements. In the following sections, we will illustrate them in more detail.
Single Use Support provides biopharma companies with a great variety of customizable single-use assemblies based on silicone tubing – ready to be implemented into your fluid transfer management.
Single Use Support provides biopharma companies with a great variety of customizable single-use assemblies based on silicone tubing – ready to be implemented into your fluid transfer management.
7 fields of application for liquid tubing
Liquid tubing sets are ubiquitous in biopharmaceutical manufacturing, but also in research and diagnostics. Here are 7 prominent examples of biopharmaceutical applications of liquid tubing:
- Bioprocesses and cell culture: Tubing solutions are integral to the cultivation of mammalian cells for the production of biopharmaceuticals. They are used for media transfer to bioreactors, cell harvest, and product clarification. The success of these processes is heavily reliant on the tubing's material compatibility and integrity to maintain a sterile environment.
- Chromatography and purification: In chromatography processes, tubing connects columns, detectors, centrifuges, and peristaltic pumps. Applications like peristaltic pump tubing in chromatography setups require precision and high-purity tubing to prevent contamination and ensure accurate separation and purification of bioactive compounds.
- Bulk drug substance transfer: For biopharmaceutical manufacturers, the safe and sterile transfer of bulk drug substances is of greatest importance. Tubing solutions play a vital role in transferring these valuable and sensitive materials from one processing step to another.
Fill and finish operations: Bioprocess tubing kits are used for aseptic filling and sealing of vials, bags, and other containers. It must meet stringent requirements to prevent microbial contamination and maintain product sterility. - Diagnostics and biotechnology: Tubing solutions are employed in various diagnostic and biotechnology applications, such as DNA sequencing, PCR, and other analytical techniques, where precision, low dead volume, and high chemical resistance are crucial.
- Vaccine production: Tubing solutions are critical in vaccine manufacturing processes, ensuring the integrity of the vaccine components and preventing any cross-contamination.
- Clinical trials: Tubing solutions are used in clinical trials for investigational drug products. They must meet regulatory standards to ensure the safety and efficacy of the trial outcomes.
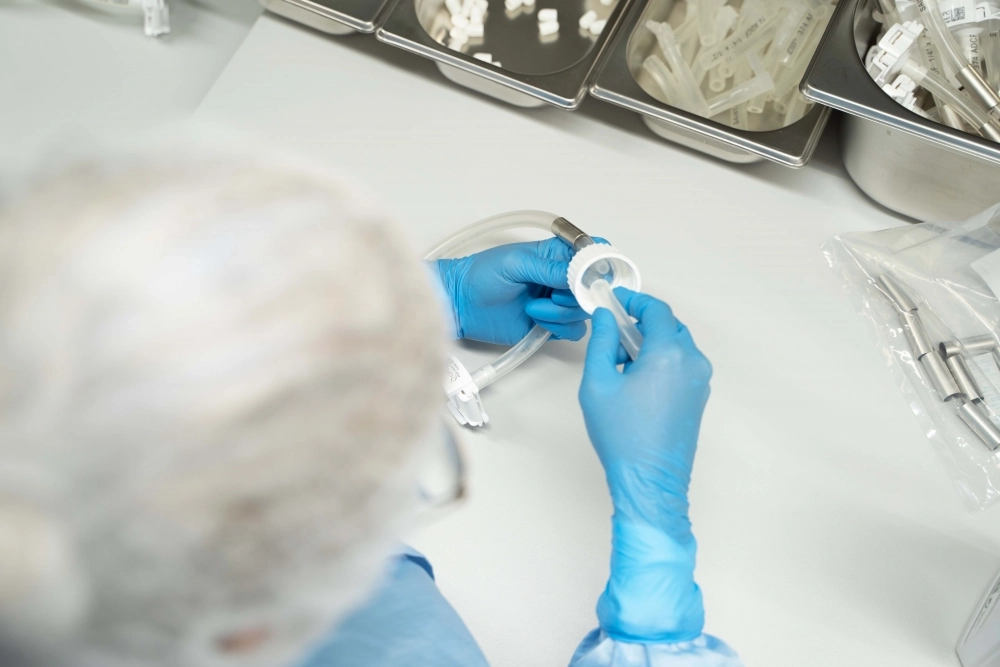
Regulatory compliance of a biopharma tubing
The biopharmaceutical industry operates within a highly regulated environment, with little tolerance for deviations, and biopharma tubing solutions must conform to a myriad of standards and guidelines. Some prominent aspects in regulatory compliance include:
- Good manufacturing practices (GMP): Tubing materials and manufacturing processes must comply with GMP standards to ensure product quality, safety, and efficacy.
- US Pharmacopeia (USP) (USP) standards: Tubing materials need to meet USP Class VI standards, which assess the biological safety of plastics used in medical devices and pharmaceutical applications.
- ISO standards: The International Organization for Standardization (ISO) has developed various standards related to tubing solutions, such as ISO 10993 for biocompatibility and ISO 14644 for cleanrooms.
- FDA regulations: The U.S. Food and Drug Administration (FDA) enforces regulations governing the use of tubing in pharmaceutical applications, particularly in the context of cGMP (current Good Manufacturing Practices) and aseptic processing.
- European pharmacopoeia: In Europe, the European Pharmacopoeia sets standards for materials and processes used in pharmaceutical tubing to ensure product safety.
- Bioprocessing standards: Organizations like BPSA (Biopro-Process Systems Alliance) have developed guidelines for single-use systems used in bioprocessing, including tubing solutions.
Multi-use or single-use biopharmaceutical tubing kits – which to choose?
When handling pharmaceutical liquids, the choice between multi-use and single-use tubing solutions holds the key to optimizing processes. Thus, the upcoming chapters will elucidate the critical aspects of these tubing options. We aim to provide you with the knowledge and insights necessary to determine the ideal tubing solution for your unique requirements.
Frequently used materials in biopharmaceutical tubing kits
Material selection in pharmaceutical tubing kits is significantly influenced by whether it is intended for multi-use or single-use applications. For multi-use systems, stainless steel and glass are preferred due to their durability and sterilizability. Stainless steel's corrosion resistance makes it ideal for long-term use, while glass's inert properties prevent interactions with pharmaceutical liquids.
Frequently used materials for multi-use tubing include:
- Stainless Steel
- Glass
- PTFE
- Polypropylene
- PVCPEEK
In contrast, single-use tubing kits typically rely on flexible, disposable materials with low permeability, such as silicone and TPE (thermoplastic elastomers). These materials are usually weldable, sealable and can withstand high pressure for optimized pump life, while they offer the necessary flexibility and biocompatibility while minimizing cross-contamination risks, eliminating the need for extensive cleaning and sterilization.
Materials for single-use tubing may be:
- Silicone tubing
- TPE tubing
- Polyethylene tubing
- Polyurethane tubing
- Fluoropolymer tubing
Tubing flexibility and versatility
Flexibility is a defining characteristic that distinguishes single-use and multi-use tubing in the field of bioprocess applications, and this difference significantly influences their applicability for various purposes.
Multi-use tubing prioritizes durability over extreme flexibility. It is designed to withstand repeated sterilization and cleaning cycles, which makes them a frequent choice for long-term applications. Materials like stainless steel or glass are often employed for their resilience in these situations. Multi-use tubing performs reliably in demanding environments, where extreme flexibility may not be the primary concern.
Single-use tubing, in contrast, is celebrated for their exceptional flexibility, making it highly versatile for a wide range of pharmaceutical applications. Their key advantages lie in their adaptability, as they readily conform to the unique requirements of each application, whether it involves bioreactor setups, chromatography columns, or aseptic filling processes. Furthermore, their flexibility minimizes residual volume, ensuring efficient pharmaceutical liquid transfer and reducing wastage – an especially important consideration when dealing with costly or limited-volume formulations or reagents. Additionally, the moldability of a single-use tubing simplifies their installation, leading to time and labor cost savings during the setup of pharmaceutical processes, such as filtration.
Cleaning and sterilization – what about sustainability?
The practice of cleaning and sterilizing tubing sets is not only essential for maintaining the integrity of pharmaceutical processes, but a considerable point of concern regarding sustainability. When comparing single-use and multi-use tubing, their impact on sustainability becomes a pivotal factor to consider.
Single-use tubing, due to its disposable nature, inherently offers certain sustainability advantages:1
- Reduced resource consumption: Single-use tubing sets eliminate the need for cleaning and sterilization, resulting in lower water and energy consumption, which is a significant step towards reducing the environmental footprint.
- Minimized chemical usage: Cleaning processes often involve the use of chemicals, which can be reduced or completely eliminated with single-use tubing kits, lessening the environmental impact associated with chemical waste.
- Lower risk of cross-contamination: A disposable tubing effectively eliminates the risk of cross-contamination, as it usually comes pre-sterilized (e.g. via autoclave, gamma-irradiation, or X-ray irradiation). Along with pre-validation and optimized extractables profiles, this ensures product safety and reducing the likelihood of costly batch losses.
Source:1
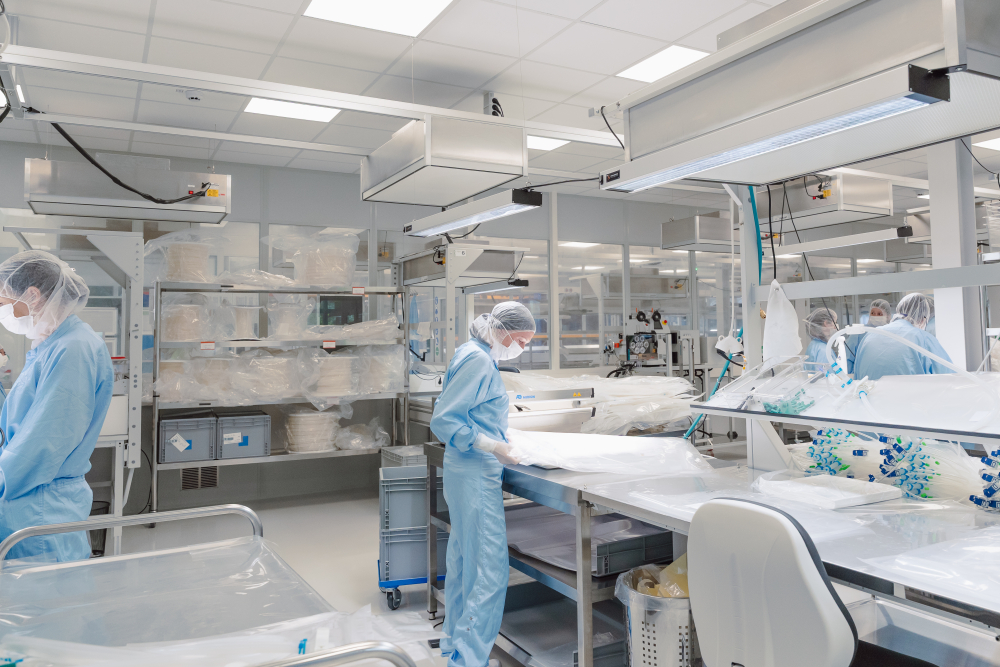
Multi-use tubing, on the other hand, requires thorough cleaning and sterilization, which can pose sustainability challenges:
- Resource-intensive cleaning: Cleaning and sterilizing a multi-use tubing demand substantial quantities of water, energy, and cleaning agents, contributing to increased resource consumption.
- Chemical waste: The use of cleaning agents can result in chemical waste, necessitating careful management to minimize environmental impacts.
- Cross-contamination concerns: Despite rigorous cleaning processes, a multi-use tubing carries a risk of cross-contamination, potentially leading to costly batch losses, which may not align with sustainable practices.
Pre-configured single-use assemblies
Either customize your single-use assemblies or choose from a selection of pre-configured options to streamline your fluid management processes.
Either customize your single-use assemblies or choose from a selection of pre-configured options to streamline your fluid management processes.
Other components of single-use manifolds for fluid transfer in biopharma
Single-use manifolds are essential in pharmaceutical fluid management. They consist of various components for the fluid paths, such as tubing products, connectors, valves, filters, pressure sensors, single-use beta bags and more. These components ensure the efficient and precise flow control of pharmaceutical fluids.
In addition to manifolds, several other non-sterile and sterile consumables are vital in pharmaceutical fluid management. These include sterile filters, caps, closures, tubing seals, clamps, stoppers, sampling bags, tubing welders, sealers, mixing systems, adapters, gaskets, flasks, pipettes, sterile adhesives and tapes. These consumables each play specific roles in maintaining the purity and sterility of pharmaceutical fluids, and are crucial for the safety and efficiency of pharmaceutical processes.
Bioprocessing tubing solutions by Single Use Support
Due to their numerous advantages for biotech companies in terms of flexibility, safety, sustainability and ease of use, Single Use Support has developed single-use consumables that accompany the single-use based fluid management systems.
At Single Use Support, we develop and customize fluid path solutions for our clients. As an independent service provider, we assemble everything according to the specific requirements of our customers. An integral component of those consumables are high-quality single-use bioprocess tubing, improving process efficiency while minimizing the risk of contamination.
These disposable tubing sets are accompanied by a wide array of additional single-use consumables, from connectors, filters and distributors all the way down to disposable bioprocess containers.
FAQs on bioprocess tubing solutions
- GE Healthcare Life Sciences. An environmental life cycle assessment comparison of single-use and conventional bioprocessing technology, https://docplayer.net/20413850-Ge-healthcare-life-sciences-an-environmental-life-cycle-assessment-comparison-of-single-use-and-conventional-bioprocessing-technology.html, Published 01.11.2013