Filling & aliquoting LNPs in single-use bags
Table of contents
ShowThe use of lipid nanoparticles (LNPs) has gained significant attention due to their potential applications in drug delivery systems. LNPs have shown promise in encapsulating and delivering various therapeutic molecules, such as nucleic acids, proteins, and small molecules. The technology is used in the development of mRNA-based vaccines and therapies, including the COVID-19 vaccines.
To meet the growing demand for LNPs, efficient and scalable production processes are required. This article explores the process of filling and aliquoting LNPs in single-use bags, highlighting its significance and key considerations.
Adequate filling of lipid nanoparticles – why is it important?
For mRNA & LNP manufacturing, a variety of production steps is necessary. Drug substances are transported and temporarily stored at several manufacturing sites. Safe handling is essential in this process. In addition to freezing to achieve long-term stability of the substances, fluid management is another vulnerable aspect.
Filling and aliquoting LNPs involves transferring the formulated LNPs into individual containers, ensuring accurate volume and maintaining sterility. Aseptic filling and aliquoting techniques are essential to maintain product quality, consistency, and safety throughout the manufacturing process.
Single Use Support focuses on the protection of bulk drug substances and therefore provides systems for filling LNPs in single-use bags, along with other solutions to encompass further processes – such as freezing, storage and transportation.
Challenges in filling LNPs
Filling drug substances into bioprocess containers comes with challenges that need to be addressed to ensure a successful manufacturing process. Contamination of the drug product is a significant concern. Despite following guidelines like Annex 1, process inconsistencies and human intervention can still introduce contaminants. Automated filling processes within closed systems help minimize this risk by avoiding human errors.
Additionally, there is always a risk of leakage and breaking of containers, which can lead to product loss, contamination, production delays, and potential health risks for the staff. Automated filling in single-use bags reduces product loss significantly.
Further challenges are insufficient scalability. Scaling-up the manufacturing volumes can create bottlenecks in the filling process, hindering large-scale production and timely distribution. Implementing scalable single-use solutions allows for more efficient and flexible production, especially during high-demand situations like a pandemic, while reducing on-site footprint.
In summary, there are 3 main challenges to address:
- contamination
- product loss & leakage
- scalability
All of these factors can be best addressed with automated filling machines. The processes reduce human intervention, are cGMP compliant, and therefore safe for the biopharmaceuticals and the people involved in its production.
Read more: Automated aliquoting system: From small volume aliquoting to bulk filling with RoSS.FILL
Choosing the right single-use bag
One has the choice of different bioprocess containers in terms of size, material and manufacturer. So what container is best to choose to safely fill LNPs into?
Single-use bioprocess containers offer several advantages in bioprocessing since they eliminate the need for cleaning, sterilization, and validation associated with traditional stainless-steel systems, also reducing downtime and operational costs. Bags provide flexibility, scalability, and faster turnaround times. Additionally, single-use containers minimize cross-contamination risks, ensure product integrity, and enable efficient process transfer and disposability, enhancing productivity and simplifying operations. One important aspect to consider is to have an extractable and leachable free container that offers ideal conditions for further process steps, such as freezing, transporting or storing.
IRIS single-use bioprocess containers by Single Use Support provide robustness and flexibility at the same time, ensuring the protection of lipid nanoparticles during transport and storage. With a PE film showing an ultra-low extractables & leachable profile, they are suitable containers for drug products like such based on LNPs. The single-use bags are highly customizable, allowing for any size, fill volume, tubing, connector, and port fitting.
Single-use bags are connected to different manifold assemblies, enabling a fluid transfer in a closed system to ensure a safe, accurate and reproducible fluid management process.
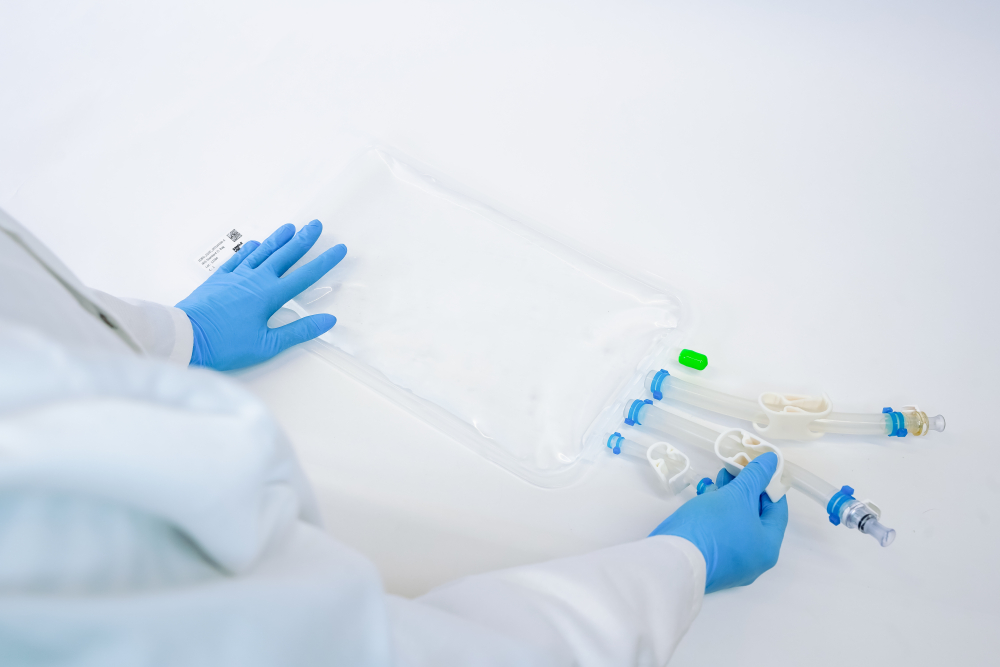
How to best fill LNPs? Decision on modularity and flexibility
It is recommended to keep LNPs in a closed sterile system to avoid contamination and human error. Lipid nanoparticles themselves do not require any particular temperature control requirements for filling. However, they are frequently used in combination with mRNA, which is when temperature control becomes an issue. It is important to fill at a controlled rate – not too fast to jeopardize destabilization, and with not too much pressure.
Finally, the aliquotation and filtration must also be flexibly scalable in order to be able to react to fluctuations in volumes and to provide cost efficiency – regardless of the quantity.
How is all this implemented in the best possible way? To avoid contamination in filling LNPs in single-use bags, it is recommended to implement pre-use post-sterilization integrity testing (PUPSIT) as outlined in Annex 1. With its fill & filtration platforms, Single Use Support offers the ideal solutions to accurately fill biopharmaceutical liquids, such as LNPs and mRNA. Closed systems ensure contamination-free processing, and individual solutions can be found for specific requirements in the respective LNP production to maximize efficiency and quality.
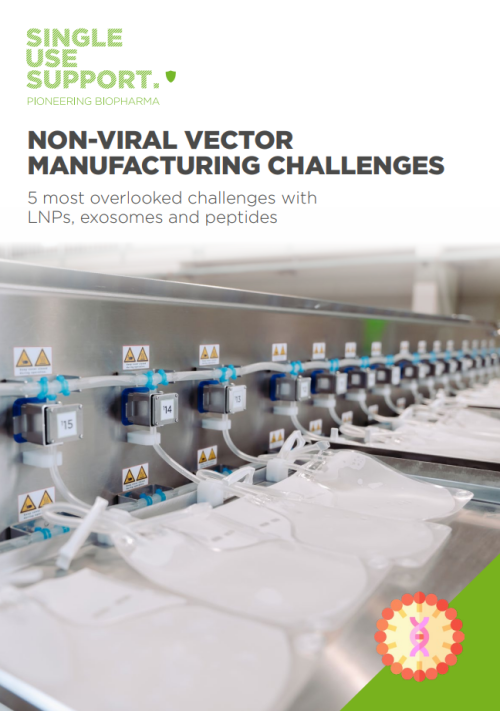
Download Guide
Download: Non-viral vector manufacturing - 5 overlooked challenges
Navigate the most overlooked challenges in non-viral vector manufacturing. Our guide covers topics like degradation and instability of LNP during freezing, scalability concerns in exosome manufacturing, homogenization of plasmid DNA in liquid transfer and much more.
Solutions for LNP & mRNA manufacturing
The actual purpose of LNPs is the safe transport of mRNA molecules to the cell. At Single Use Support, we make sure that the transport routes between the manufacturing steps of LNPs are safe and that the substances are kept stable.
For this reason, we offer our customers individual solutions that comply with all regulations and enable maximum scaling and efficiency in production.