Defying the shortages in single-use manifold assemblies
Table of contents
ShowSingle-use components might not be considered as the most essential parts in biopharmaceutical manufacturing. However, they are quite capable of temporarily paralyzing the entire production of biopharmaceuticals on-site. Procurement bottlenecks of single-use components have intensified the strong demand that even influenced companies to re-consider abandoning the dependency on single-use components.
On the other hand, the pressure on the industry to ensure single-use manifold assemblies availability has amplified as well. However, increasing the quantity is not as simple as it sounds. Materials such as biopharmaceutical grade tubings are manufactured under special standardized procedures to ensure sterility before use.
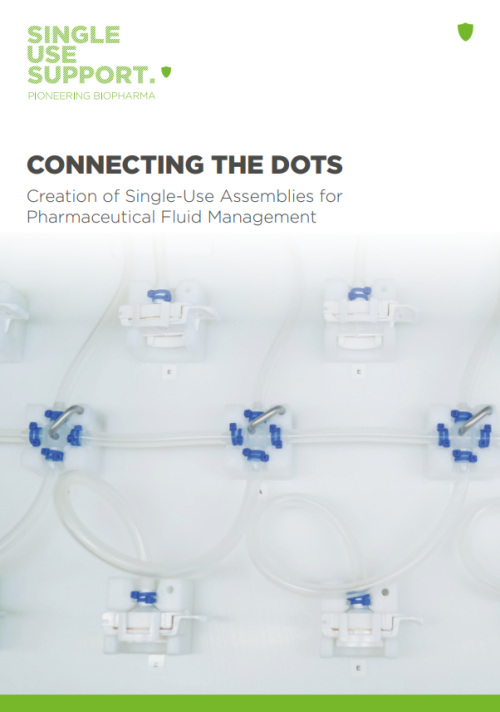
IRIS Single-Use Assemblies
Whitepaper: Connecting the Dots
Creation of Single-Use Assemblies for Pharmaceutical Fluid Management
Where to source single-use manifold assemblies?
Angel, working for a CMO that manufactures a non-COVID-19 related vaccine at a commercial level, has felt helpless after he realized that he ran out of options. He uses single use manifolds as sterile consumables to control the fluid transfer for distributing the vaccine after production into single use bags in an automated and sterile manner. The increased batch sizes and the urge to make the filling process more efficient and reproducible has forced him to switch to automated filling.
However, he did not expect the industry to fail in making available single use components for fluid management in an industrialized manner. Standardized assemblies might still be available – with inconsistent lead times though. However, the lead times deteriorate drastically if one deviates from the standard manifold. The lack of customization has jeopardized the biopharmaceutical products that have been produced under surveillance of Angel.
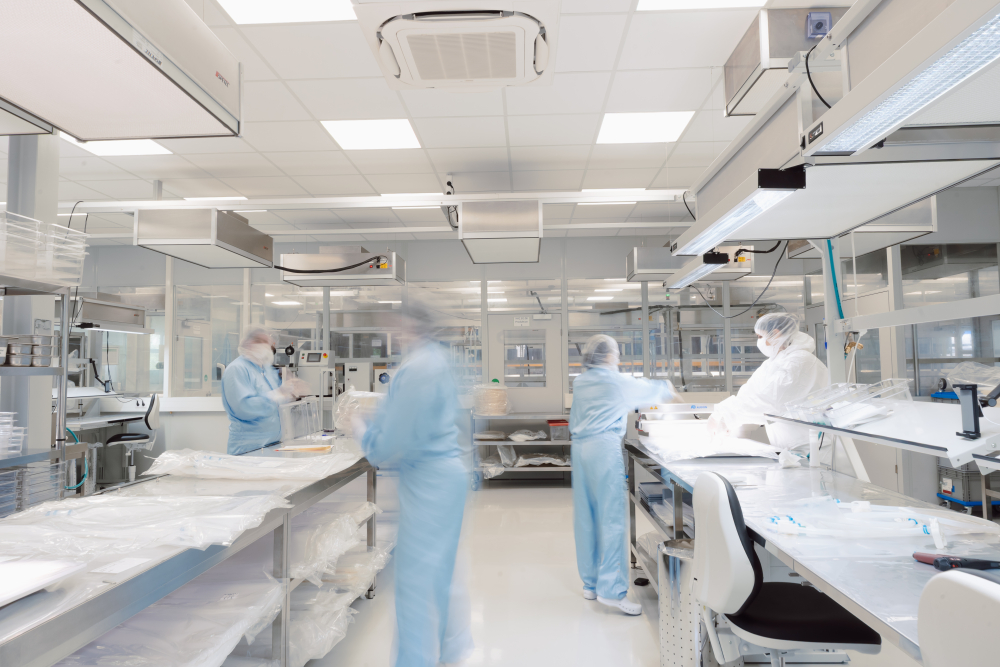
Beyond COVID-19 operation warp speed
All COVID-19 related supply to foster the manufacturing of the vaccine has been accelerated through operation “warp speed”. Due to scarce availability and stockpiling of the remaining single-use manifolds on the market for the prioritized use of COVID-19 vaccines this did not apply in Angel’s case. Single Use Support, as an existing supplier for BDS handling solution, has got wind of the urgence of Angel’s situation. As a manufacturer of single-use manifold tubing, the Austrian process solution provider customizes single use manifolds for its customers.
A lead time of 2 weeks
Taking the urgency as top priority Single Use Support has decided to fuel up the pace. Enabling a magical timeline of just 14 days between PO placement and on-site delivery of the manifolds. The manifold components were defined, sketched, and assembled in the Assembly Center in Kufstein, sent for sterilization, resent for quality control, and delivered to Angel. The last attempt to keep the drug substance in use has been successful.
This is one of many examples how custom-made adaptions are more than necessary to avoid the unfortunate product loss due to supplier process inefficiencies. Single-use manifolds are without any doubt the cohering element that keep running the biomanufacturing of drug substances. And it is indeed the supplier’s duty to adapt on customers’ needs.
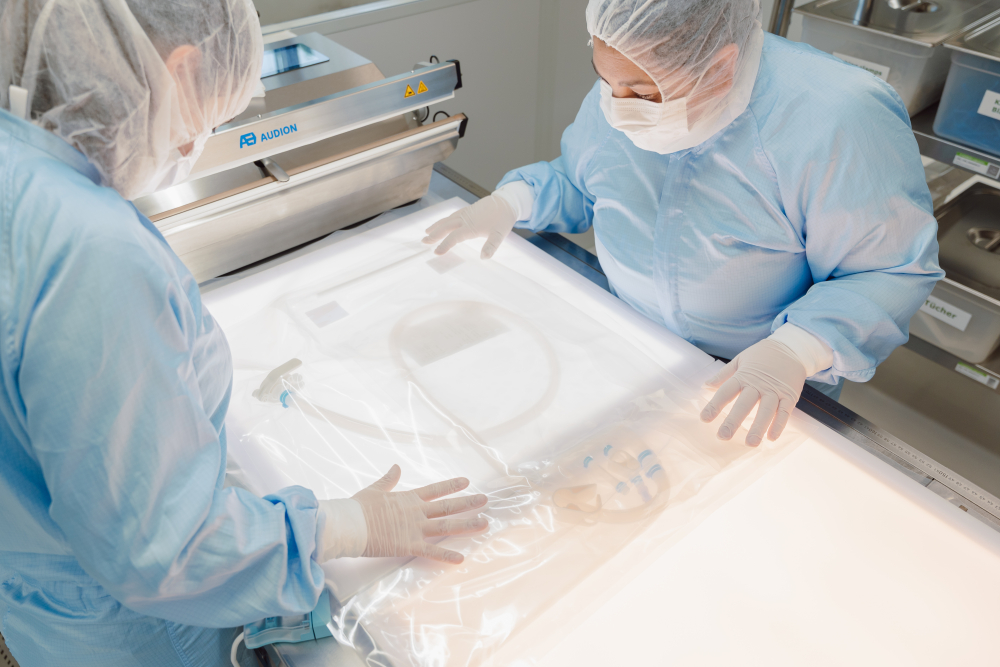