How to safely connect a single-use tubing set?
Table of contents
ShowWith single-use technology becoming more and more prevalent in the pharmaceutical and medical sector, there is an increased need for solutions that are applicable across the board.
Single-use tubing and manifold assemblies for sterile filling are an approach that is both flexible and scalable. With the proper systems in place, they allow users to design their own aseptic systems containing tubing, connectors, fittings or filters.
In this article, you will learn how to safely connect and disconnect the tubing with the necessary techniques like sealing and crimping.
What are molded manifold assemblies?
Molded manifolds are an alternative to the plug-in technology with cable tie fixation. They eliminate the need for barbed fittings and offer a user-friendly way to connect various components of an assembly. Molded single-use manifolds are custom-made to meet the varying requirements of the pharmaceutical sector.
Two single-use components are simply plugged into each other before being molded together to allow for an uninterrupted and uncompromised flow of liquid drug substance. They incorporate anything from simple molded sanitary ends to complex configurations with varying lengths of silicone tubing and several connectors.
At Single Use Support we work with the plug-in technology which offers several advantages, especially the easy connection of the different parts.
How to safely disconnect a single-use tubing?
When working with a single-use manifold assembly, connecting silicone tubing to a single-use bag for filling purposes is only half of the job: In order for the bag to be sent to its next destination, it needs to be disconnected again.
Thanks to the use of silicone or TPE (thermoplastic elastomers) tubing, both the connection and disconnection have become a breeze. Single-use manifolds offer several techniques available to do this, namely crimping, welding or RF sealing.
RF sealing (radio frequency)
Radio frequency welding and sealing makes use of high frequency electromagnetic radio waves to provide highly localized heat when working with different types of polymers.
One of the main benefits of RF welding is a consistent quality of connection accompanied by quick cooling action, which is why it is increasingly used for welding silicone tubing. Made this way, connectors between manifolds and bags allow for an easy and clean disconnection, making it a viable solution for sterile applications.
Welding of single-use manifolds
Welding of tubing utilized in single-use manifold assemblies requires a special device that will not impact the fluid flow of two ends of tubing connected that way. It uses compressed air to cut and weld tubing of different sizes and will not work if air pressure is too low. A disadvantage is that the inner and outer diameters must be the same, otherwise the welded area may break.
While the device can be used anywhere it is needed, it can only be operated by a trained person, and material costs as well as time spent will depend on this person's experience. Connectors created that way can be easily and cleanly disconnected, which makes welding an ideal solution for pharmaceutical needs.
Safe Connection of single-use manifold assemblies
When safety, time and flexibility are of the essence, the solution should be an easy one. Single Use Support's single-use tubing sets and manifold assemblies take processing and sterile filling to the next level. Contact us to get manifold assembly solutions tailored to your needs.
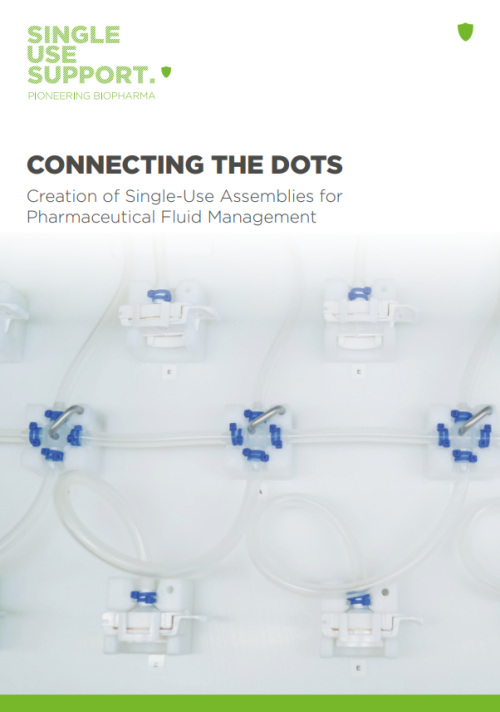
IRIS Single-Use Assemblies
Whitepaper: Connecting the Dots
Creation of Single-Use Assemblies for Pharmaceutical Fluid Management