Vaccine development: challenges & solutions
Table of contents
ShowBefore it even comes to vaccine manufacturing, the vaccine must first be developed. The obstacles are manifold and the fragility of supply chains or requirements in cold chain management are just two of the challenges in vaccine development. Also the vaccine development process depends on the drug's efficacy, tolerability and safety evaluated in clinical studies which influence the FDA vaccine approval process timeline.
Single-use technologies prove to be particularly suitable when it comes to dealing with highly sensitive and expensive materials that need to be handled not only with care but also in sterile conditions. Additionally, single-use technologies provide the flexibility and agility needed in an industry that relies on the possibility to scale up on demand.
Development of vaccines and the stages involved
From drug discovery to regulatory FDA drug approval and post-market monitoring – the different steps around vaccine development include rigorous research, testing, and approvals that secure antidotes against diseases.
Vaccine discovery
Vaccine discovery marks the inception of the development process, involving extensive research and identification of potential antigens. Scientists explore various avenues to pinpoint antigens that trigger an immune response against the targeted pathogen. The selection criteria prioritize antigens capable of eliciting a robust immune response while ensuring safety and feasibility for further development stages. Successful antigen identification forms the cornerstone of subsequent vaccine development endeavors.
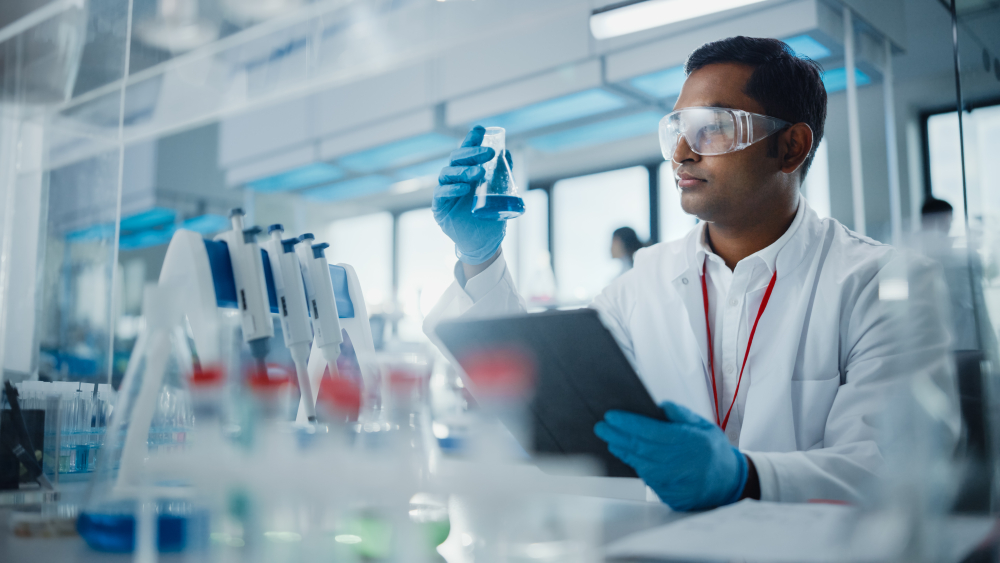
Concept optimization in pre-clinical testing
Concept optimization encompasses the refinement and enhancement of vaccine candidates identified during the discovery phase. Pre-clinical testing plays a pivotal role, often conducted using animal models to evaluate safety, immune response, and potential side effects. This allows researchers to fine-tune the formulation and dosage, aiming for optimal effectiveness in eliciting immune responses while ensuring safety standards are met. Rigorous assessments during concept optimization lay the groundwork for advancing promising candidates to the clinical trial phases.
Vaccine testing
Vaccine are typically tested in Phase I-III clinical studies before the submission for FDA approval. Additional vaccine testings are Phase IV and clinical trials which are conducted after FDA approval, each serving critical purposes before and after the submission for FDA approval.
- Phase I: Initial trial of a vaccine in humans for safety and dosing, and early efficacy infrormation in a two-digit number of healthy volunteers.
- Phase II: Subsequent trial on a drug's efficacy and safety, to a larger population of over 100 people in particular disease settings.
- Phase III: Larger clinical study, with more than 1,000 people often spanning regions or countries, to confirm efficacy and safety by monitoring adverse reactions. The vaccine is compared against a placebo or standard treatment.
- Phase IV: Trial conducted after FDA approval to gain additional information about the vaccine's risks and benefits.
Scale from lab production of vaccines
Already in clinical reasearch, manufacturers must think of scaling-up vaccine manufacturing. It involves transitioning from small-scale production to mass manufacturing while maintaining quality and consistency, and is one of the major challenges in vaccine development. Implementing scalable manufacturing systems that comply cGMP standards from the outset is crucial to streamline scaling.
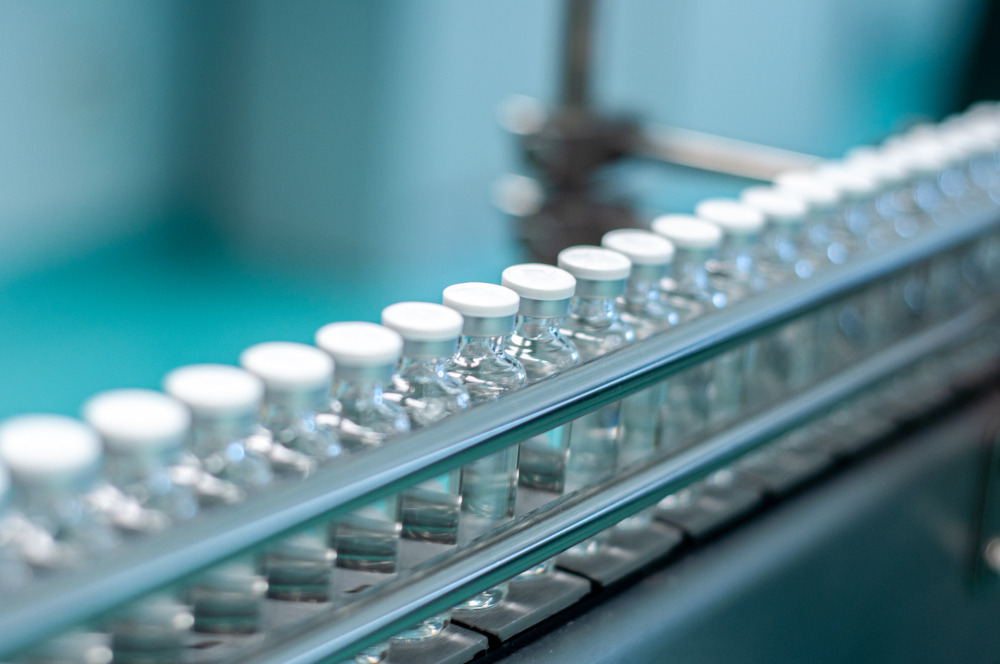
Regulatory approval
Vaccine development timelines from drug discovery to regulatory approval can take up to more than 10 years. It involves thorough assessment by health authorities, such as the FDA or the European equivalent EMA, to ensure the vaccine meets strict safety and efficacy standards. Based on collected clinical trial data, the approval signifies the vaccine's readiness for public distribution, assuring its safety and effectiveness.
The approval for commercialization goes hand in hand with advisory committees to review clinical trial results, considering efficacy, safety, and potential public health impact. Their evaluation informs recommendations for specific populations, dosage schedules, and priority groups for vaccination. Post-market monitoring is the vigilant surveillance conducted after a vaccine is deployed to the public. Pharmacovigilance ensures continued safety and effectiveness by detecting and assessing any adverse events or unexpected patterns
Challenges in vaccine development
While the challenges in vaccine development may differ according to the respective product and the parties involved in vaccine development and production, there are several hurdles that apply globally. To improve efficiency, there needs to be a collaborative effort between regulatory bodies, vaccine manufacturers, healthcare providers and public health organizations.
Cold chain management
Given the fact that the half-life of a vaccine correlates to the temperature it is stored at, the importance of a functioning cold chain management becomes apparent.
From smallpox to mRNA: What vaccines have special cold chain requirements?
Several vaccines demand meticulous temperature control due to their inherent properties and composition. These requirements stem from various factors, including the vaccine's formulation, stability, and susceptibility to temperature variations. Vaccines targeting diseases like measles, mumps, smallpox and rubella are typically stable when stored between 2°C to 8°C. However, large-molecule vaccines, such as COVID-19 and other novel mRNA vaccines, are more sensitive and necessitate ultra-cold storage below -15°C or even -70°C. Vaccines, particularly those sensitive to temperature variations, can lose their potency when exposed to inadequate or fluctuating temperatures. This degradation impacts the vaccine's ability to confer immunity, leading to potential health risks and reduced effectiveness in preventing diseases.
Hit the right temperature?
Ensuring vaccines reach and maintain precise freezing temperatures is pivotal in preserving their efficacy and safety. Uneven freezing rates pose a substantial risk to vaccine integrity. When vaccines are exposed to uncontrolled freezing, varying ice crystal formations may develop within the formulation. Uncontrolled formation of ice crystals leads to cryoconcentration of API in the center of primary packaging, causing stress to the product.1
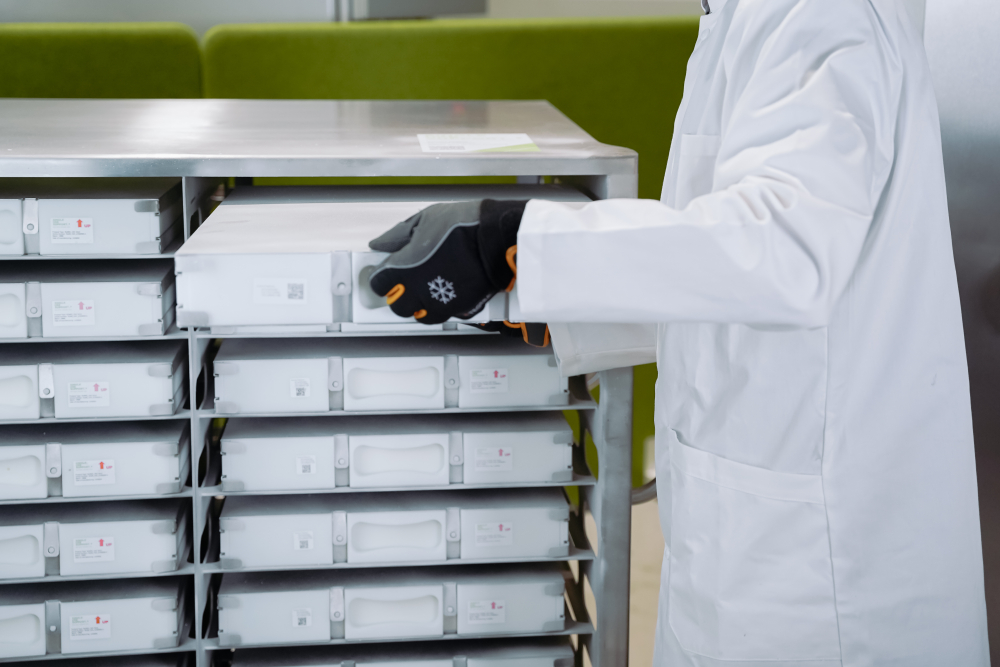
Cost of vaccine development
High costs are without a doubt one of the most challenging hurdles in vaccinology, both in terms of the development of candidate vaccines and manufacturing. Extensive R&D and preclinical or clinical trials, regulatory approvals and quality control, as well as the necessary technology and infrastructure all contribute to those high costs.
The nature of vaccine research, development and production calls for processes and systems that allow for scale-up for large-scale production runs of vaccine doses. This can be achieved by implementing adaptable platforms and systems that allow for a high degree of flexibility.
The implementation of technologies that offer agility and flexibility can reduce the cost of vaccine manufacturing in the long run. Efficient scalable solutions from development in laboratories to production sites reduce costs through lower error rates, product loss and optimized usage of resources.
And finally, an effective cold chain can help to reduce further operational costs. Advanced cold chain solutions for vaccines minimize the risk for contamination and maintain vaccine efficacy – to remain capable of neutralizing antibodies or protecting our immune systems.
Given the fact that vaccines are crucial in preventing the spread of infectious diseases like the Coronavirus, mpox or hepatitis, it will be essential to generally curb costs, for instance by advanced production technologies or cooperations to enable cost-efficient research, production and distribution.
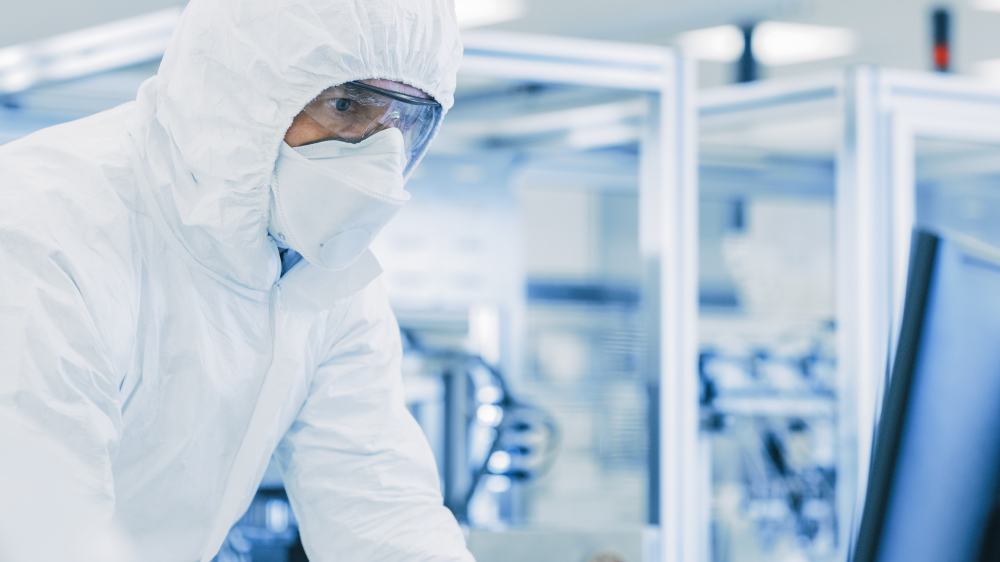
Sustainable development & manufacturing
Sustainability in vaccine manufacturing poses a great opportunity, but also a multifaceted challenge that demands a balance between meeting global healthcare needs and minimizing environmental impact.
The traditional vaccine production process often relies on resource-intensive methods, such as extensive consumption of water, energy and chemicals. To sustainably develop and manufacture vaccines, there is a growing need to adopt greener technologies and practices. This shift involves exploring alternative, eco-friendly production methods, reducing waste generation, and implementing energy-efficient processes.
Embracing single-use technology represents a sustainable solution for vaccine manufacturing, offering a viable alternative to traditional stainless steel equipment. Numerous life cycle assessment studies have consistently demonstrated that transitioning from stainless steel to single-use systems within the biopharma and pharma industry can lead to substantial reductions in carbon emissions, as well as lower energy and water consumption.
A key contributing factor to these environmental benefits is the diminished need for extensive cleaning processes associated with stainless steel equipment. Moreover, the adoption of single-use technology enhances operational flexibility and minimizes the risk of cross-contamination.2 3
Efficiency in vaccine development & production
As vaccine development timelines can be up to 10 years, there are calls for vaccines to be developed as efficiently as possible. The aim is to increase productivity in the vaccine design, development and production of new formulations – and it is one of the main factors contributing to high costs. It is thus crucial to address and improve efficiency, both in development and production.
Efficiency encompasses both the speed and quality in the development of new vaccines in the laboratory, as well as the effectiveness of production processes. Enhanced quality and rapid, safe procedures contribute to heightened efficiency and success in the global vaccine market.
Manual processing still constitutes bottlenecks in certain stages. Human intervention poses a risk of contamination, potentially resulting in the loss of valuable substances. Therefore, implementing automated fluid management solutions is a crucial strategy to elevate quality, accelerate processing, and ultimately enhance overall efficiency.
Single Use Support’s technologies offer viable solutions that are both integrable and scalable to address challenges on several fronts. By eliminating the need for manual processing and handling, they reduce
- the potential for human error
- product loss caused by primary packaging leakages
- the potential for contamination.
In addition, they ease and streamline processes by replacing rigid stainless-steel containers with adaptive single-use consumables that can easily be integrated in existing processes across various platforms.
Scale-up challenges in vaccine development
Once a new vaccine has been given the green light by the Food and Drug Administration (FDA) and other regulatory bodies, vaccine manufacturers are faced with the challenge of scaling up their processes. In reality, manufacturers are preparing to scale up production in good faith long before official approval.
Scalability was exhausted to the extreme during the COVID-19 pandemic when formulations were required in large scale as soon as they had passed phase 3 trials and adverse events could be ruled out. But even beyond the pandemic, scaling remains an important topic. Once a formulation is approved, titers of raw material need to be bumped up. Raw material includes antibodies, RNA, various viral vectors, pathogens or adjuvants to boost immune response and increase the duration of antibody responses.
In addition to having to handle increased volumes of raw material, large scale vaccine platforms require an increasing amount of components, many of which are often provided by different suppliers. Any issues in the procurement of just a single component will stall the production of valuable vaccine doses, thus impacting the global health sector.
Furthermore, standardization is an essential aspect in scaling up vaccine manufacturing. The FDA approval and clinical phases rely on findings from small volumes. When scaling to large volumes of drug substances, minimizing deviations becomes imperative to guarantee both efficacy and, more importantly, safety. To attain the desired properties, scalable processes - from laboratory procedures to the handling of bulk drug substances - need to adhere to a certain degree of standardization. In addressing this challenge, the solutions from Single Use Support, ensure freezing curves that maintain uniformity or similarity for both small and large volumes.
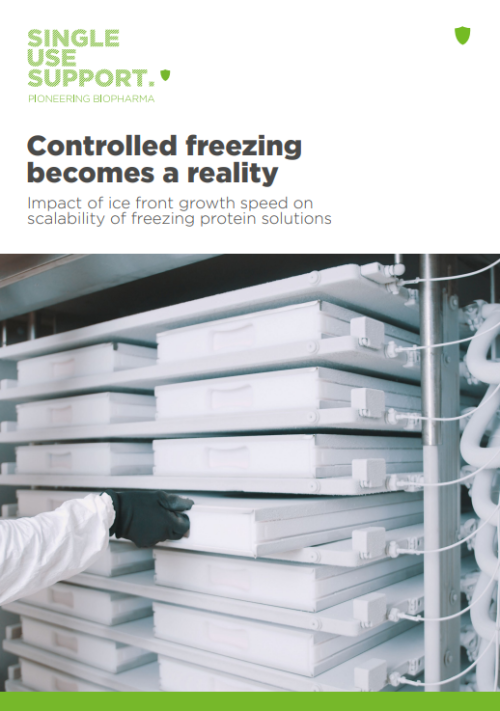
Download Whitepaper
Whitepaper: How Controlled & Scalable Freezing Becomes Reality
As one of the most essential parameters in terms of achieving control over freezing & thawing bulk, the freezing rate has been considered and evaluated in different tests in this whitepaper. Using the ice front growth speed as a leverage had a significant impact on controllability and, as a result, on protein quality.
Efficient solutions for vaccine development based on single-use technology
Single-use technologies are a promising solution in addressing several of the challenges faced by vaccine manufacturers. Every stage of the vaccine manufacturing process, can be supplied with single-use systems and technologies: be it single-use connectors for vaccine development, sterile single-use consumables or aseptic dispensing, ultra-cold storage and cryogenic freezers.
They help address characteristics of each vaccine, including monoclonal antibodies, viral and non-viral vectors, nucleic acids, bioconjugates and advanced therapies.
Safe handling and storing of vaccines in single-use bags
Bioprocess containers for extreme temperature conditions are pivotal in preserving vaccine integrity during the manufacturing journey. Consumables, such as the IRIS single-use bioprocess container by Single Use Support, are purpose-built to withstand extreme cold, ensuring vaccine stability in demanding environments. Produced from robust materials, these containers hold vaccines as intermediates during production from temperature variations, maintaining their efficacy throughout storage and transportation. The IRIS bioprocess container, renowned for its adaptability in ultra-low temperatures, plays a crucial role in fortifying the reliability and resilience of vaccine production workflows.
The RoSS® Shell is a secondary packaging designed to protect single-use bags containing the highly valuable substances. The bioprocess containers are protected inside the RoSS shell throughout process steps in fluid and cold chain logistics. It helps minimize the product loss in biomanufacturing, both in terms of loss of product quality and in terms of single-use bag leakages. Primary packagings are susceptible to leakages caused by temperature variations and physical stress during storage and transport.
This innovative casing, equipped with 3D foam technology, ensures a secure and insulated environment for single-use containers. RoSS® Shell's tamper-evident, closed system minimizes the risk of temperature excursions and contamination, making it a versatile and reliable choice for maintaining the cold chain integrity during vaccine storage and transportation.
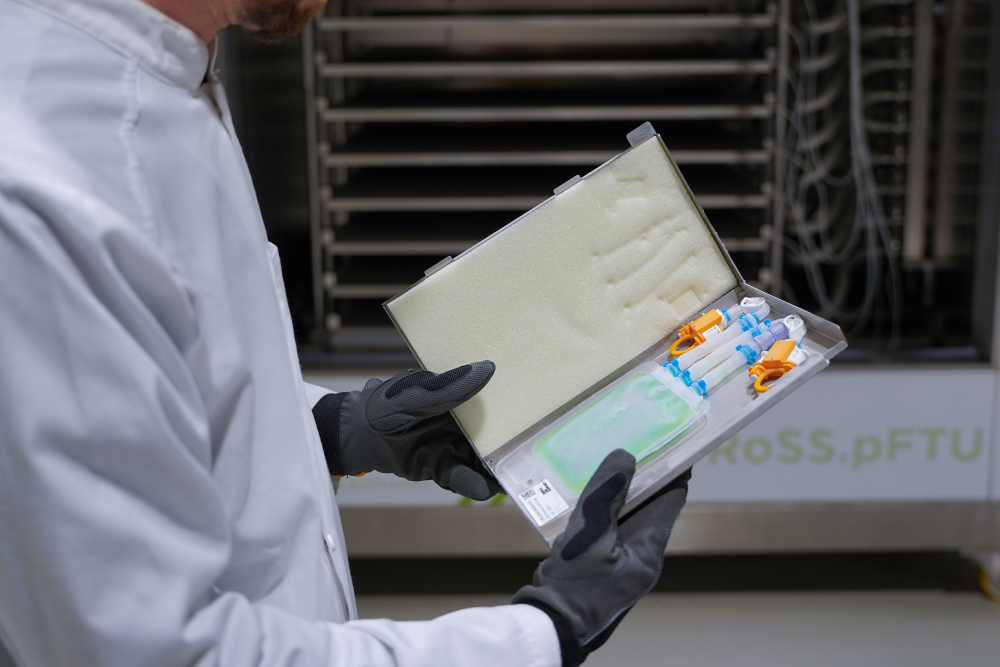
Automated filling & filtration of vaccines
Fluid management occurs with a seamless process from homogenization to filling into single-use bags and freezing, eliminating the need for manual handling. Single Use Support's RoSS.FILL contribute to a safe fluid flow in a closed automated system. They help to improve efficiency while at the same time reducing human errors, ergo product loss and costs. In order to improve operational productivity, further fluid management solutions advance fluid management. This includes cooling and homoegnization with RoSS.PADL, filter testing equipment for PUPSIT, mixing and shaking, and further process improvements.
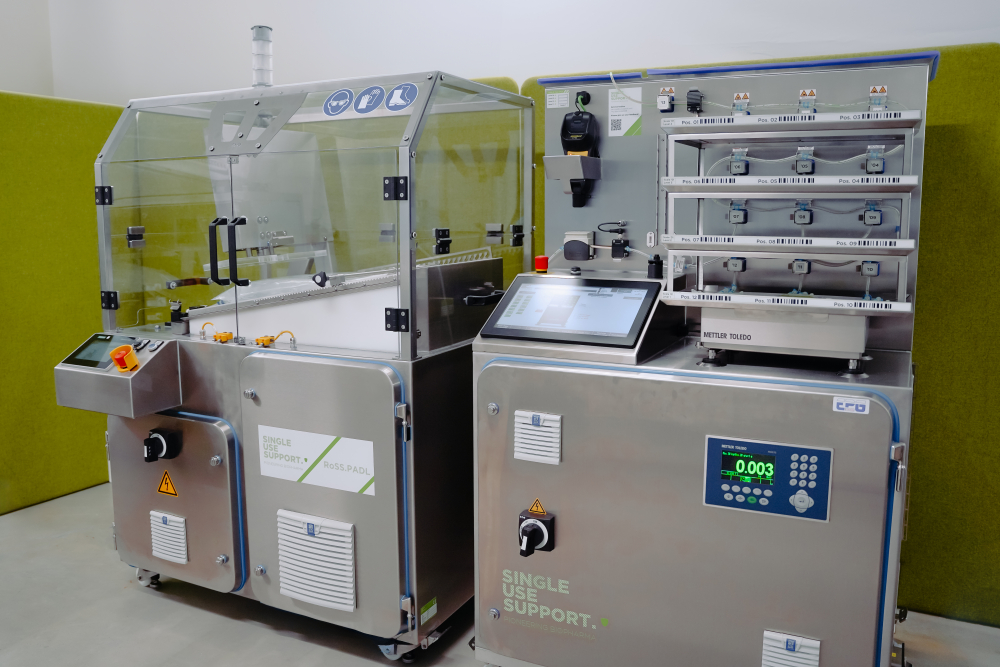
Controlled vaccine cold chain management
Single-use technologies facilitate end-to-end solutions that meet the specific needs of both cold chain storage and handling. Single-use systems are universally applicable for different drug products – be it mAbs, ADC or mRNA vaccine. Not only are those solutions tamper-proof, but they also allow for monitored temperature control as well as tracking throughout shipping and storage.
While static freezers may still be the norm, more flexible and faster plate freezing platforms such as Single Use Support’s RoSS.pFTU are gaining traction. The slow freezing process of traditional freezers impacts the medical substance’s quality. It leads to the formation of large crystals that can cause friction and will increase cryoconcentration.
On the other hand, controlled rate plate freezers for biopharma not only speed up the freezing process; more importantly, the increased freezing rate also leads to better results, meaning that the substance’s characteristics will be maintained in the best possible way. Plate freezers facilitate a speedy and at the same time controlled freezing of valuable vaccines and other liquid solutions contained in the single use bag and protected by the tamper-proof RoSS Shell. Additionally, RoSS.pFTU offers the added benefit of not only providing an advanced freezing technology, but also controlled thawing and draining - all with a single, flexible and scalable platform.
In order to maintain the cold chain throughout the entire shipment and storage process, specialized shipping containers are required. Single Use Support provides vaccine manufacturers with RoSS.ULTF, a storage freezer to keep the vaccines in the RoSS Shells cool once they have been frozen. The modular interior of the ultra low temperature freezer provides a flexible storage solution and works ideally – yet not only – with RoSS® Shell, contributing to preserving the potency of vaccines and biopharmaceuticals while optimizing storage capacity. Shipment of vaccines can be performed in RoSS.SHIP, the cooling system for days of transportation inside the isolated containers is based on dry ice or so-called “Phase-Change Materials” (PCM).
Read more about freezing of drug substance, thawing of drug substance or advanced cold chain solutions for vaccine development
Single Use Support's solutions for vaccine development
Vaccine development hinges on the meticulous preservation of temperature-sensitive products throughout the manufacturing process. Single Use Support stands at the forefront, offering a suite of innovative, flexible and scalable solutions that revolutionize cold chain management in this domain.
From advanced bioprocess containers designed to withstand extreme temperatures to the groundbreaking RoSS® shell, which ensures utmost protection for single-use bags, the product portfolio redefines standards of temperature control in vaccine manufacturing. These pioneering advancements not only ensure vaccine stability and security but also address critical needs for adaptability, scalability, and operational efficiency.
FAQs about vaccine development challenges
What are the 4 phases of vaccine development?
In clinical research a vaccine undergoes several tests in terms of efficacy, safety and tolerability. These are Phase I, Phase II and Phase III trials, followed by Phase IV and/or clinical trials which are performed after regulatory approval for commercialization.
What are key characteristics in vaccine development?
Immunogenicity, which refers to the ability of a substance like antigens or a vaccine to provoke an immune response in an organism, is a key characteristic in the development of vaccines.
How are vaccines tested for safety?
Vaccine are typically tested in Phase I to Phase III clinical studies serving the examination of a vaccines's efficacy and safety, before the submission for FDA approval. Additional vaccine testings are Phase IV and clinical trials which are conducted after FDA approval.
Which viral vectors are most commonly used in vaccine development?
In the field of immunology and genomic research, various viral vectors play a crucial role in vaccine development. Commonly utilized vectors include Adenovirus, Adeno-associated virus, Herpes simplex virus, measles virus, and retrovirus vectors. The development process typically integrates a combination of in vitro, ex vivo, and in vivo approaches. According to a study accessible on PubMed, "Adenoviruses are efficacious vaccine vectors against diseases in which traditional vaccine development strategies have proven ineffective. Source: https://www.ncbi.nlm.nih.gov/pmc/articles/PMC4847555/
What are global health associations, and what is their role to improve vaccination access?
Global health partnerships have been established to support expensive vaccination programs worldwide. A current example would be Gavi, a vaccine alliance initiated by the World Health Organization (WHO) and different other stakeholders. Its aim is to increase and improve access to immunization in low income nations, such as the majority of countries in Africa.
Read more about vaccine development & manufacturing
- Cost-effectiveness of the controlled temperature chain for the hepatitis B virus birth dose vaccine in various global settings: a modelling study, http://dx.doi.org/10.1016/S2214-109X(18)30219-5, Published 2018-05-15
- Is Sustainability Possible With Single-Use Technology?, https://www.bioprocessonline.com/doc/is-sustainability-possible-with-single-use-technology-0001, Published 12.08.2015
- Advancing sustainability in the pharmaceutical industry, https://cen.acs.org/acs-news/comment/Advancing-sustainability-pharmaceutical-industry/98/i17, Published 02.05.2020