Safe storage & handling of viral vectors
Table of contents
ShowViral vectors like Adeno-associated viruses (AAVs) are popular vectors for gene therapy and vaccines. And yet, there is product loss due to leakages of primary packagings or other mishandling of fluids. In order to deliver high-quality and viable products efficiently, safe handling experience a growing interest.
To do so, there is a need for technologies and platforms that facilitate reliable and safe handling all the way from the first steps of production up to the shipping and storage process.
In this article, we clarify the safe handling of all viral vectors, such as:
- adenoviral vectors (AVVs),
- adeno-associated viral vectors (AAVs),
- lentiviral vectors (LVVs),
- retroviral vectors (RVVs).
We explain the processes and technologies using the example of adeno-associated virus vectors, even though the measures are valid for all viral vectors.
AAVs in biopharma
AAVs can deliver the therapeutic gene directly to the central nervous system and provide long-term and functional correction of missing or mutated genes. Therefore, they were initially developed as a promising non-pathogenic gene delivery vector for the treatment of neurodegenerative diseases in the central nervous system. Today, AAV technology has evolved to target a wide range of tissues and cells for the treatment of a number of diseases, including Parkinson's and Alzheimer's disease.
Adeno-associated viruses are favored for their generally safe profile: They do not result in human disease nor do they need other viruses to replicate. This makes them the most popular choice for transferring and delivering genes to target a number of different tissue and cell types with the goal to improve if not cure patients where traditional approaches have failed.
The constantly growing number of clinical trials and new products calls for production technologies and platforms that are flexible enough to meet the requirements of both lab- and bulk-scale production without the need for major adaptations. These can be provided by single-use technologies and its modular design options.
Considerations in the handling of Adeno-associated viruses
Adeno-associated viruses and all medical drugs or therapies are valuable products. And the stakes are high if something goes wrong. Time is of the essence, and where time is of the essence, efficient procedures must be put in place to ensure fast, user-friendly and reliable processes and handling.
This necessitates process flexibility and scalability in order to skip tedious and time-consuming adaptations that may in turn lead to contamination. Single-use systems have proven to be easy to handle while offering the highest levels of flexibility, so that production platforms can be scaled from miniscule amounts to bulk production.
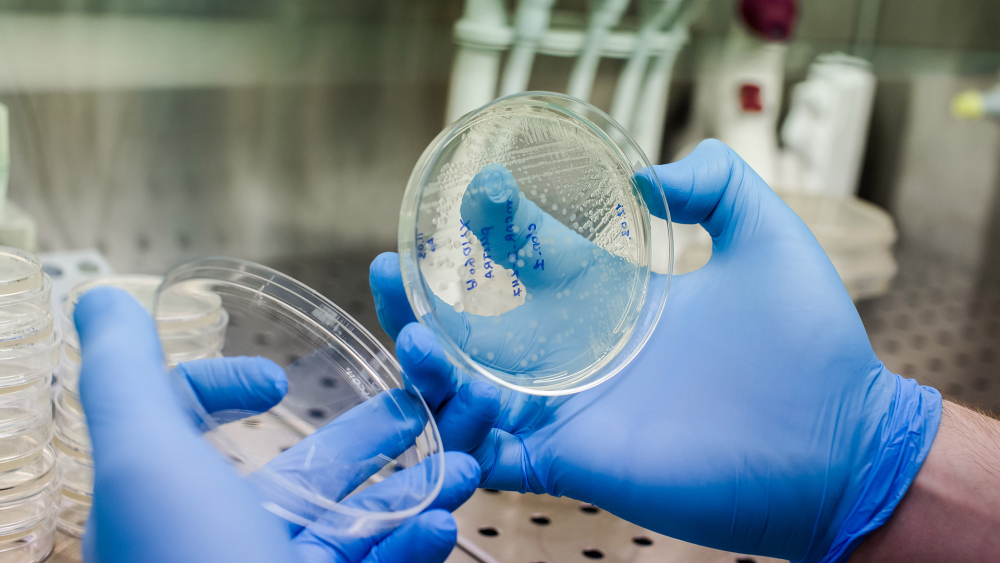
Risks associated with the handling of AAVs
AAVs are not known to cause human disease; in addition, they cannot replicate in the human body like other viruses can. This is why they have become the dominant vector for gene therapy, with a number of clinical trials underway.
In terms of biosafety, recombinant AAV constructs can be handled in a Biosafety Level 1 facility as long as they are produced in the absence of a helper virus and do not encode a potentially tumorigenic gene product or a toxin molecule. Otherwise, they should be handled as a biohazardous material under Biosafety Level 2 containment.
Safe protection of AAVs
Ensuring the safety of all parties involved, from laboratory development to commercial manufacturing, and safeguarding the highly valuable substances from any potential loss is of utmost importance when dealing with viral vectors.
This protection is achieved through appropriate packaging methods. Primary packaging refers to the direct contact between the viral vectors and the packaging materials, while secondary packaging provides an additional layer of protection for the product beyond the primary packaging. Read more here: Primary vs. Secondary Packaging of drug substance
Single-use bags are gaining popularity as primary packaging for viral vectors. They leverage the benefits of single-use technologies, eliminatie the risk of contamination from open handling and thereby ensure liquid transfer under sterile conditions. Bioprocess containers also offer easy scalability and flexibility in subsequent processing steps, withstanding withstand temperatures ranging from -196°C to +50°C and meeting all requirements for freezing and thawing viral vectors.
Highest protection of the single-use bags is ensured in a robust single-use shell. Single Use Suppport's goal is to safeguard drug substances to the highest degree possible. Its RoSS® Shell is designed to protect all available single-use bioprocess containers from external influences and trusted by many manufacturers. This secondary packaging has been proven to reduce product loss to less than 0.001%. Additionally, it allows for the freezing of bags in suitable plate freezers and facilitates the long-term storage and secure transport of viral vectors.
AAVs are not known to cause human disease; in addition, they cannot replicate in the human body like other viruses can. This is why they have become the dominant vector for gene therapy, with a number of clinical trials underway.
In terms of biosafety, recombinant AAV constructs can be handled in a Biosafety Level 1 facility as long as they are produced in the absence of a helper virus and do not encode a potentially tumorigenic gene product or a toxin molecule. Otherwise, they should be handled as a biohazardous material under Biosafety Level 2 containment.
Proper storage and handling of AAVs
While vectors can be stored at -20°C or +4°C for short periods of time, long-term storage requires a temperature of -80 °C, which is where ultra-cold freezers come into action. AAVs are being aliquoted into single use portions to avoid repeated freeze/thaw cycles.
Single-use technologies are the ideal choice to ensure consistent freezing results while maintaining the characteristics and quality of the frozen goods.1
Safe handling in AAV manufacturing
Due to their highly sensitive nature, AAVs must be handled with the utmost care. Safety and sterility must be ensured throughout the supply chain.
This is where closed and automated systems based on single-use technologies offer the perfect end-to-end solution as they allow for the greatest flexibility and agility. Furthermore, single-use designs are fully disposable, thus warranting an absolutely sterile fill process.
Automated filling: Aliquotation & homogenization of viral vectors
Safe filling or aliquoting of viral vectors into individual batches is recommended to be automated and in a closed system to avoid contamination and human error.
Single Use Support’s RoSS.FILL platform allows for a fully automated and monitored filling process that can be scaled to meet varying needs, all the way from preclinical to bulk production.
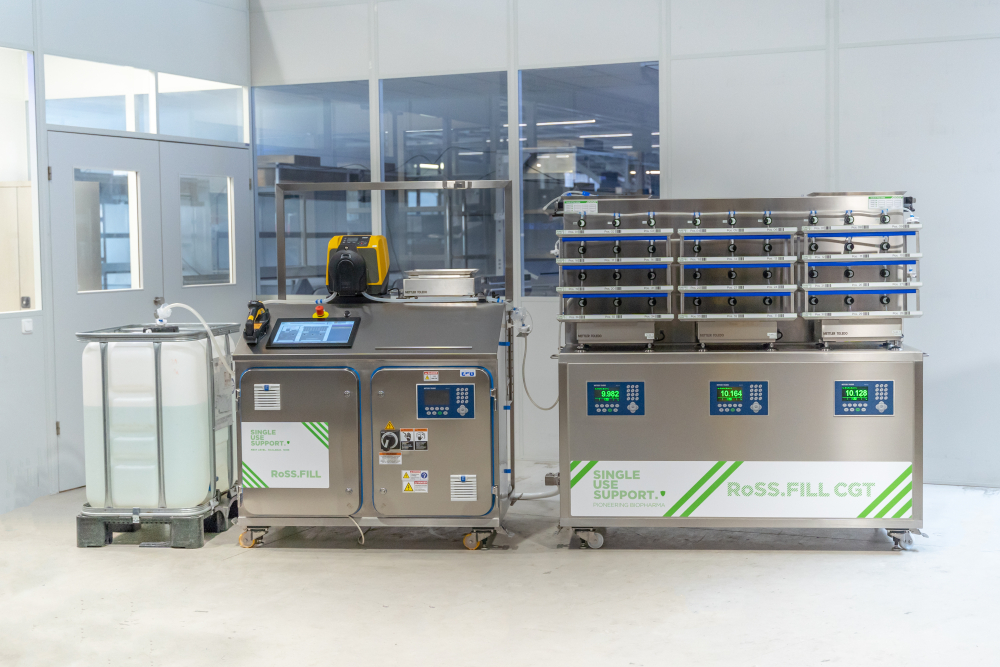
Freezing AAVs
A reliable freeze/thaw process of viral vectors with consistent results is extremely important in order to maintain the characteristics of the vectors.
Single Use Support’s freeze-thaw platform RoSS.pFTU provides controlled freezing/thawing of any drug substance and can be easily scaled from lab- to mid- to large-scale requirements. In the specific area for AAVs, the RoSS.pFTU Mid Scale is the right choice as it can fill very small single-use bags in the milliliter range and is still scalable up to 100L.
Storage & transport solutions for AAV viral vectors
Once frozen, AAVs need to be stored and shipped in a protected manner, in an environment that ensures that frozen state is maintained.
Single Use Support’s RoSS.ULTF is an ultra-cold storage freezer that keeps the desired set point temperature and is scalable to different sizes. In addition, it is fully moveable and modular to facilitate easy handling and compact storage. It not only allows for a seamless transition between deep-freezing and shipping or thawing but also offers a high degree of flexibility due modular interior design.
FAQs: Safe handling of viral vectors
Are adeno-associated viruses hazardous?
AAVs are generally considered safe for research and therapy, but proper precautions are crucial. They can pose biosafety risks at higher concentrations or if mishandled. Adherence to biosafety protocols and institutional guidelines is essential to minimize potential hazards.
How to safely handle AAVs?
In manufacturing AAVs, it is suggested to use automated and closed processes to minimize contamination risk and robust protection as secondary packaging. Implement end-to-end solutions for streamlined production and quality control. Utilize single-use technology for flexibility and sterility, ensuring efficient and safe AAV production.
At which temperature should AAVs be stored?
AAVs should be stored at ultra-low temperatures, typically at -80°C for long-term stability. Short-term storage at -20°C is also acceptable.
How long and at what temperature can AAVs be stored?
AAVs can typically be stored at ultra-low temperatures, around -80°C, for long-term cryopreservation. At this temperature, they remain stable for several years. For short-term storage, AAVs can be kept at -20°C or even up to +4°C for a short period of time. It's essential to avoid multiple freeze-thaw cycles, as they can reduce AAV vector stability and efficacy.
- UNC Vector Core: Safe Handling, https://www.med.unc.edu/genetherapy/vectorcore/safety-handling/, Published 20.09.2023