Bulk drug substance management
Table of contents
ShowWith the rising need for novel therapies - and, based on the changes in the disease landscape as most currently highlighted by COVID - the global biopharmaceutical industry is evolving, and market needs are shifting.
We are seeing an increasing number of drug products and APIs produced by an equally growing number of pharmaceutical and biopharmaceutical companies, as well as third-party CMOs.
The following article aims to take a closer look at the term “bulk drug substance” and its meaning, as well as to investigate smart solutions to shorten the phase between development and blockbuster production.
It furthermore aims to give a concise definition alongside an extended view on the daily challenges in biopharmaceutical processing.
Bulk drug substance definition (FDA)
According to FDA’s (Food and Drug Administration) definition, bulk drug substance describes substances in various suitable forms used as an active ingredient in the compounding, manufacturing, processing, or packaging of a drug.
Suitable forms can be liquid solutions as well as fine powder or crystals. The scientific definition of the term “bulk drug substance” does not include intermediates used in the synthesis of a medical drug.
Bulk drug substances or APIs (active pharmaceutical ingredients) - as they are also known - are used in the production of compounded medical drugs. As such, they must meet certain statutory requirements in order to be available for clinical use.
Additionally, the FDA issued an interim policy, giving advice to manufacturers of compound using bulk drug substances, for instance on the additional information on the labels of dosage forms.1
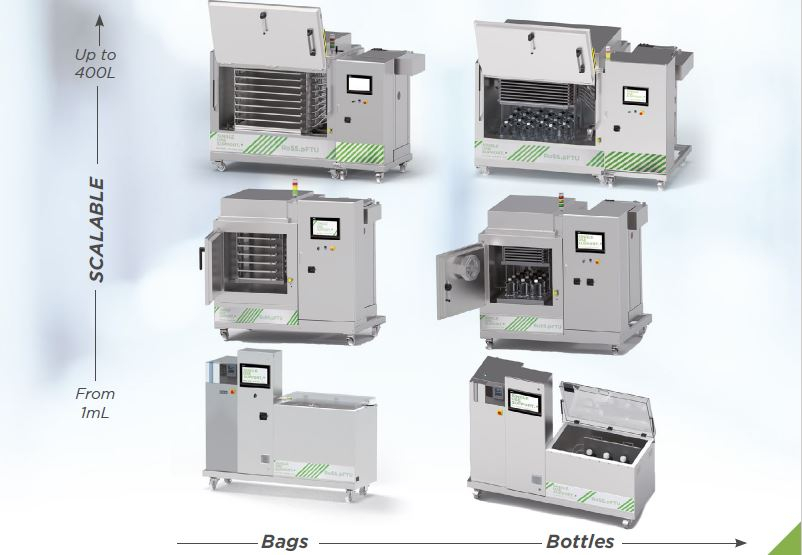
The use of bulk drug substances can serve an important role for patients for whom an FDA-approved drug product is not appropriate, such as patients who, for example, have an allergy and need a medication to be made without a certain dye or a different kind of inactive ingredient.
In such cases, certain physicians and pharmacists (in accordance with section 503A) or outsourcing facilities may be able to provide compound drug products, having to meet several regulatory demands. Outsourcing facilities as nominators, for instance, need to be registered under section 503B of the Federal Food, Drug, and Cosmetic Act (to be found in the Federal register).
Additionally, only compound drugs may be produced that are included in the FDA drug shortage list. Otherwise, an appearance of the nominated bulk drug substance in FDA’s 503B bulks list (a list of bulk drug substances with clinical need) is required.
Pharmacists and physicians, as well, need to comply with various regulations in the production of bulk drug substances – an applicable United States Pharmacopeia (USP) and National Formulary monographs, for instance, need to be taken into account.
In order to be approved, any bulk drug substance must be manufactured by an establishment that is registered under section 510 of the FD&C Act (Federal Food, Drug and Cosmetic Act), and additionally it must be accompanied by a valid certificate of analysis.2
Micro to macro - from lab to commercial scale
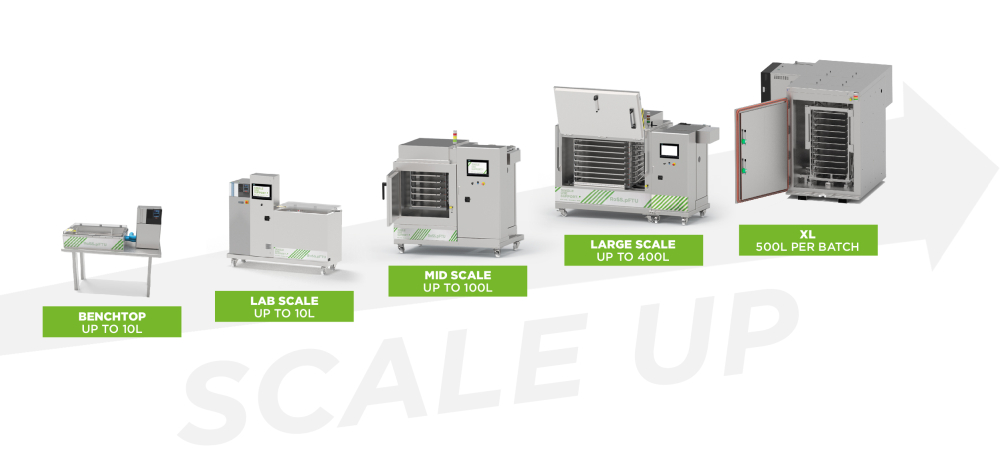
Once a newly developed product has been approved for the market, manufacturers are faced with having to scale up, so they can move from preclinical to commercial scale manufacture. This is a complex process concerning the entire supply chain that needs to be well managed, as it is not without its challenges. Furthermore, no two production sites are the same and the chemistry processes differ from manufacturer to manufacturer.
The obstacles and challenges are manifold, and they apply to scientific as well as to technical aspects, while legal regulations and standards have to be adhered to and complied with. Additionally, moving from micro to macro might lead to the the Food and Drug Administration having to newly approve the entire process.
And if this was not complicated enough, the different departments involved in research, development and production may be spread out across various sites. Even if they all operate within the same organization, they may be geographically removed from each other.
These are all factors that influence the outcome of any project, and so they should be considered early on, with
- clear steps determined for the scale-up process and
- clearly assigned responsibilities for all individuals involved
While during research, medicinal chemists are focused on whether a certain idea is feasible, once they move ahead, they are more concerned with the scale-up of procedures and logistics. Good Manufacturing Practice (GMP) is key, and strict regulations mandate extensive documentation to safeguard both quality and traceability.
Single-use technology - the modern, agile choice for drug substance logistics
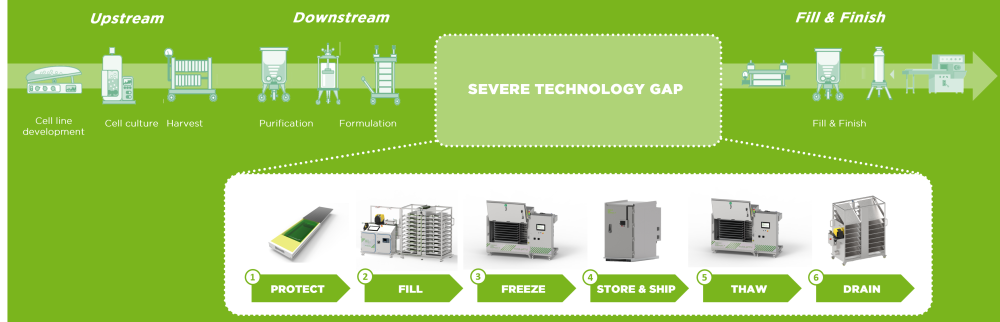
While the challenges of scaling up the production process for bulk drug substances are obvious, all parties concerned are constantly working on improving existing technologies or coming up with new approaches to make life easier. One such development is the use of single-use components, which was first employed in lab environments.
Single-use technology has become an accepted standard in small-scale environments such as the lab and when administering the drug to the patient. However, their modular design allows for great flexibility and as well as scalability, which is why is becoming increasingly common as an agile solution in all areas - all the way to large-scale commercial production.
The utilization of disposable equipment allows manufacturers to transfer the entire process - ranging from early-stage development to final product and logistics - relatively easily and without any major risks. The system, which involves both technology and equipment (including bags, connectors, tubings and assemblies) can be scaled up and adapted relatively easily thanks to the nature of the single-use components employed.
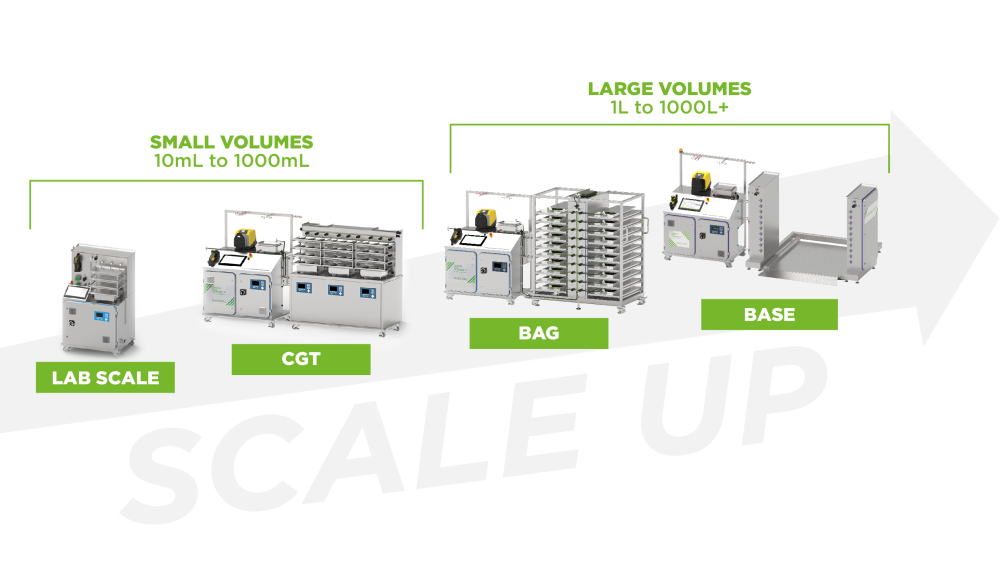
blast freezer
"slow freezing"

plate freezer
"fast freezing"

Thawing drug substance: best practices
Thawing of drug substances has to be carried out with as much diligence as there has to be in every other step in the supply chain of bulk drug substances. After all, there need to be seamless transitions from one step to another, achievable by dedicated end-to-end solutions.
In general, one can distinguish between an uncontrolled and a controlled thawing process. While uncontrolled thawing leaves little to no control over thawing rates, controlled thawing processes allow to adapt the heat supply to a high degree. However, there is a lot more to consider in order to achieve optimal thawing results.
Avoiding product loss of bulk drug substance
Loss of drug substance (product loss) is a risk that generally exists within every step within the supply chain of bulk drug substances.
Contamination of bulk drug substances can cause enormous trouble in the production of drug products, leading to considerable costs. But the risk of product loss persists during filling and freezing processes, the latter of which have to be carried out in accordance with the product’s requirements. Further protection is required during storing and shipping, and the thawing process can also pose the risk to damage highly sensitive substances.
However, there are measures to ensure that the loss of these valuable substances is avoided. Seamless transitions from one step to another, provided by end-to-end solutions for bulk drug substances, are therefore key to a lossless product management.
Risk management for a safe handling of bulk drug substances
In safe handling of bulk drug substances, risk management is an important aspect to be considered – be it human drugs or compounded animal drugs, since staff must be prevented from being exposed to potentially hazardous substances. This is why, in pharmacy compounding, several regulations are installed, e. g. the Drug Quality and Security Act.
Critical steps in the production of bulk drug substances include filling and freezing, but also transport/storage as well as thawing and draining – all of which have to be executed with high regards to the respective risks for product and stuff.
In order to minimize safety risks for staff when handling bulk drug substances as well as to ensure product quality and to meet regulatory standards with no exemption, according measures must be applied all along their supply chain.
Trend: decentralized manufacturing means growing complexity
The biopharmaceutical industry has always been a fast-paced and challenging field but with an increased rate of new developments and growing decentralization, the already existing complexity is only bound to increase.
Teams spread out over geographically removed sites have to collaborate and work together, which has been made possible or easier thanks to a growing degree of digitization. Digitization can be seen as one of the reasons for ever-increasing levels of decentralization, as well as outsourcing to third-party CMOs or CDMOs.
These developments bring with them a growing need for standardized processes that are flexible and reliable in equal terms. They need to be compatible so as to ensure uniform processes across all sites and phases.
Thanks to its modular nature, single-use technology is ideal when it comes to finding innovative solutions for the design of bioreactors and decentralized biopharma manufacturing processes.
While in the past disposable production methods have generally been used for lower volume manufacturing and processing for clinical and commercial requirements, they are on the rise for large-scale production purposes and are set to become an established industry standard.
Conclusion
Where innovation and technology are working hand in hand, they can come up with revolutionary solutions that in turn allow to improve the time to market. However, this is only possible with a comprehensive and sustainable approach and by considering long-term prospects.
A newly developed medical drug is only as good as the entire process surrounding it. In other words, the initial work in the lab can be negligible if the required basic conditions have not been thought through and set up well in advance.
Single-use bioprocessing offers ideal premises for the development and production of bulk drug substance: Single-use systems are modular, thus allowing for the highest possible degree of agility. Flexible and scalable solutions are the future, and single-use is the way forward.
FAQs
What is a bulk drug substance?
A bulk drug substance is an active ingredient within pharmaceutical products. Prescribers may rely on compound drugs containing certain bulk drug substances, for instance, when a patient is allergic to an inactive ingredient of a drug product. Therefore, they play an essential role in the treatment of patients worldwide.
What is a drug substance?
A drug substance is an active ingredient of a drug product, inserted in order to have a therapeutic impact on the person it is administered to.
What is the difference between API and bulk drug?
Bulk drugs, also known as active pharmaceutical ingredients (API), are ingredients of drug products that are inserted in order to have a biological impact on the person it is administered to.
Recommended articles
- Interim Policy on Compounding Using Bulk Drug Substances Under Section 503B of the Federal Food, Drug, and Cosmetic Act, http://www.ncbop.org/PDF/FDAUseofBulkDrugProductCompOutsFacilities503BJan2017.pdf, Published 01/2017
- Bulk Drug Substances Used in Compounding, https://www.fda.gov/drugs/human-drug-compounding/bulk-drug-substances-used-compounding, Published 12/2022