Filling of drug substance: 5 threats you should know
Table of contents
ShowThe filtration and filling of drug substances, if not done correctly, can cause severe problems. If the production steps in drug substance management from compounding to filling, labeling and dispensing of a drug substance leaves space for contamination risks, this can lead to product loss or unwanted alterations of the product. Delays in drug product manufacturing, higher costs of clinical trials and severe health risks for patients can be consequences.
Moreover, the filtration of drug substances or active pharmaceutical ingredients as they are also known is necessary in order to achieve a contaminant free pharmaceutical product. Other than certain small molecule drugs or proteins like monoclonal antibodies for instance are often especially prone to contamination risks because they cannot withstand heat treatments for sterilization1. Consequently, product fill and transport are among the different steps of the drug product supply chain.
Therefore, GMP and regulatory instructions issued by the FDA good manufacturing practices have to be exercised before biological products leave the manufacturing facilities in filled vials, pre-filled syringes or bioprocess containers. However, even though good manufacturing practices (GMP) are followed, the different steps in fluid management are still prone to errors. Learn the five threats in order to save time and money.
1. Leakage and breaking of bioprocess containers
If a container is damaged, contaminated or breaks during manufacturing or transport, it can have serious consequences. Product loss can lead to production delays to patients. In addtion, contamination of a drug substance that goes unnoticed during monitoring can cause health risk to patients. Therefore, integrity testing and visual inspection of bioprocess containers during filling is an important process with enormous impact.
2. Contamination of the drug product
Sterility of modern parenteral pharmaceuticals like vaccines and other injectable drugs is to be protected. Cleanrooms with an ISO classification and equipment in accordance with biopharma standards are only one of the basic requirements during drug development (for example by a third party CDMO).
Although drug substance handling has to follow certain guidelines to protect drug products from the risk of contamination, errors are always possible. Accidental contamination of the product through human intervention of operators remains to be a risk. In contrast to the risk of human errors from manual handling, aseptic filling with automated processes have been shown to minimize this risk by eliminating the factor of exposure to human-transmitted materials.
Read more: Drug substance vs. drug product – the differences
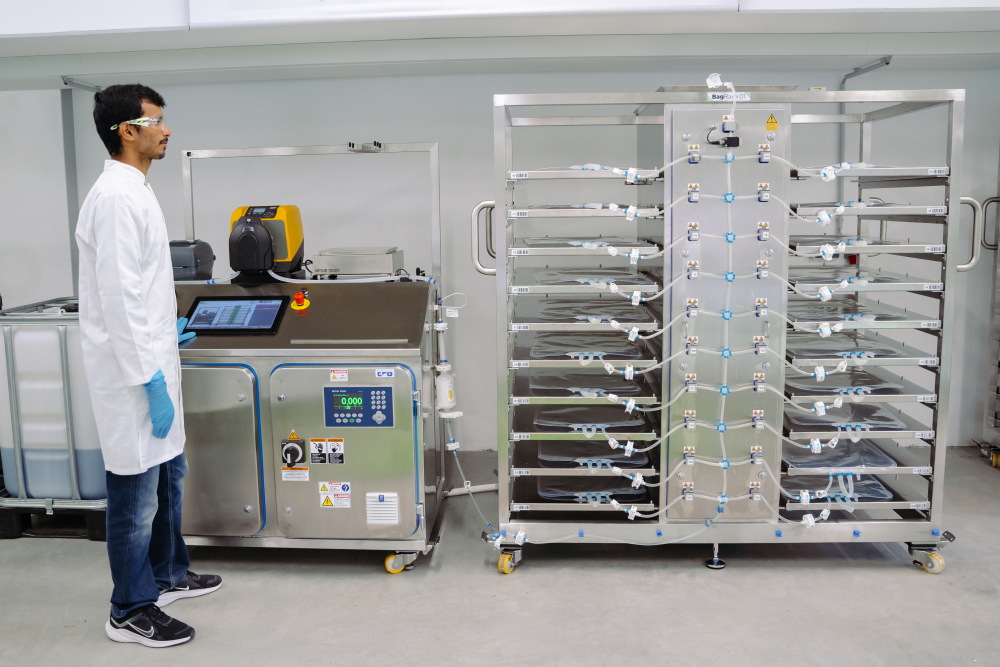
3. Incorrect filtration processes
Since the filtration of biopharmaceuticals is used to purify the bulk drug substance and rid it of unwanted microbes, incorrect filtration processes pose a serious threat to a successful manufacturing process. It can leave contamination of a drug substance unnoticed, resulting in defective products, which is why constant quality control is essential.
4. Inaccurate filling process
Usually, small volumes of ATMPs (advanced therapy medicinal products) were distributed manually into small single-use bags. Nevertheless, this procedure brings several riks, including cross contamination, inconsistent cell counts and overfilling, which can result in product loss.
RoSS.FILL Lab Scale is a fully automated cGMP-compliant aseptic filling technology for up to 12 small single-use bags of 10mL to 500mL.
5. Bottleneck due to insufficient scalability
Through insufficient scalability in the filling process, a bottleneck is likely to occur. Especially in high demand situations like during the Covid-19 pandemic, it is necessary to operate large scale production of excipient substances and quick distribution as fast as possible. Nevertheless, many systems are limited to capacities between 1 and 100 liters, whereas the modular system by Single Use Support can be used for capacities between 10 and 1000 liters.
The advantage of state-of-the-art scalable single-use solutions where a filling line can be used flexibly, does not only apply in demanding situations like a pandemic but allows for a more efficient production in general and reduces on-site footprint.
Further risks in the aseptic filling process and how to resolve them
The sensitive process of aseptic filling is prone to risks caused by human errors or faulty equipment. However, not only the risk of contamination is a big challenge, also temperature control plays a big role when working with fragile structured protein solubles.
To help reduce bottlenecks and allow for a contamination-free product, Single Use Support have developed automated end-to-end solutions to fill the gap between downstream and the fill-finish process. Through the automated sterilization of tools and containers, the aseptic and automated aliquoting systems can take over tasks that are too sensible or toxic to be carried out manually.
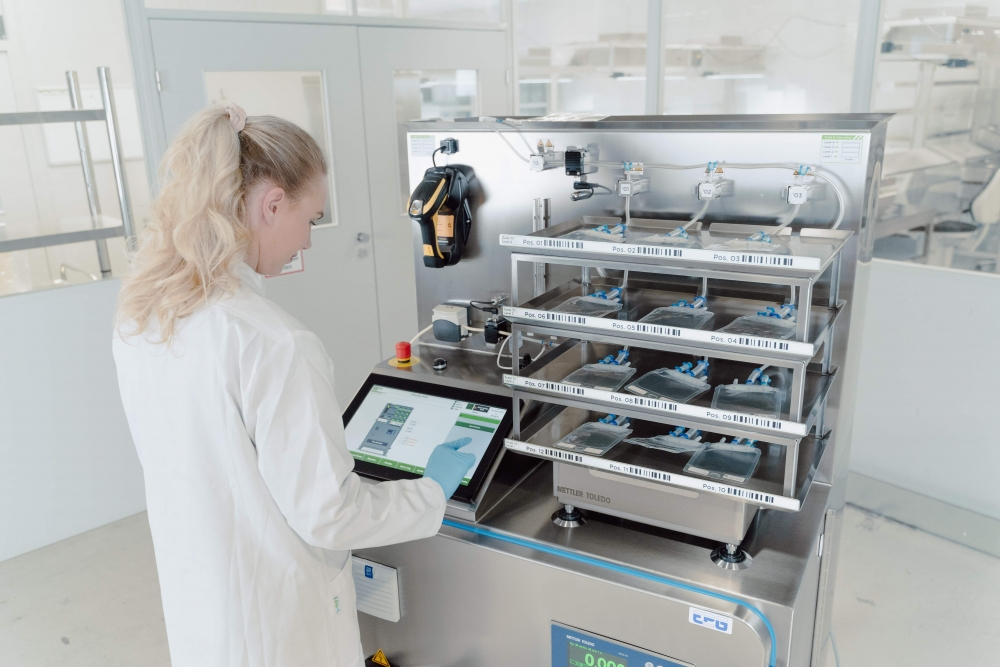
Automated single-use bioprocesses taking over
Automated bioprocessing solutions are the future and especially systems based on single-use technology components have a number of benefits that surpass the advantages of employing tried-and-tested, established platforms:
- Flexible use of add-ons (such as filters, connectors …) as needed
- Limitless scalability (both ways) with single-use bioprocess containers of any volume
- User-friendly integrability, adaptability and operation
Most importantly, the move towards automated systems will optimize output and at the same time prevent loss of drug substance by eliminating manual handling steps to rule out the risk of contamination and ensuring sterility.
FAQs about drug substance filling
What is the filling process in the pharmaceutical industry?
The filling process in the pharmaceutical industry is the process of aseptic filling different drug substances into single-use systems, such as bottles and bioprocess containers.
What does fill finish mean in pharma?
Fill-finish in pharma marks the end of the manufacturing process where a drug product is filled into a bioprocess container and packaged for transport and distribution to health care centers.
What are aseptic formulation and filling processes?
Aseptic formulation and filling processes are the different steps from making a formulation, filling it into a container, inspecting, labeling and packaging, while keeping the product free from contamination.