Evolving Methods of Bulk Freezing
Table of contents
ShowUnlocking Potential: From outdated CryoVessels to state-of-the-art Plate Freezers
The freezing method with multi-use cryogenic containers, also called cryovessels, has been used for decades. The open stainless-steel container is still largely in use but will be replaced bit by bit by new technologies.
Why? Because the risk of contamination is much higher with cryovessels.
It is barely scalable.
It is not possible to control the freezing process.
And the total cost of ownership is high.
Cold chain process setups are not yet industrialized. New technologies, such as plate-based freezing and thawing based on single-use systems, improve process efficiency and product quality. Innovative solutions are breaking the ice for the evolution of bulk drug substance freezing.
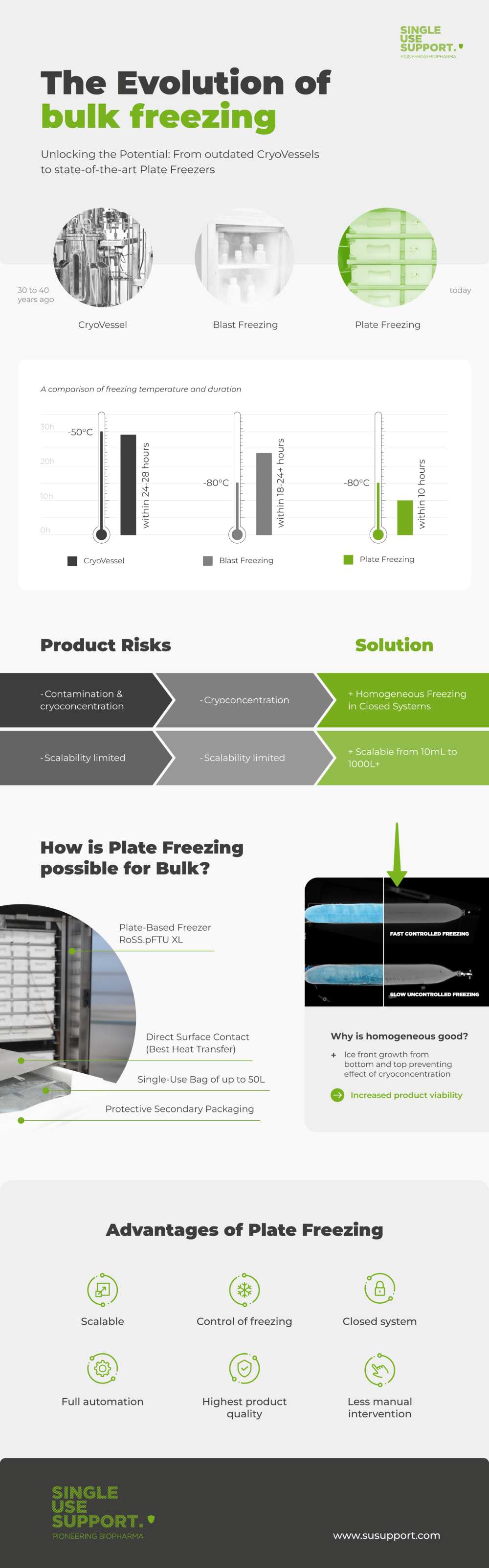
How it began: CryoVessels and their scope of application
The use of cryovessels in biopharmaceutical manufacturing revolutionized the freezing process of bulk drug substances. 30 to 40 years ago.
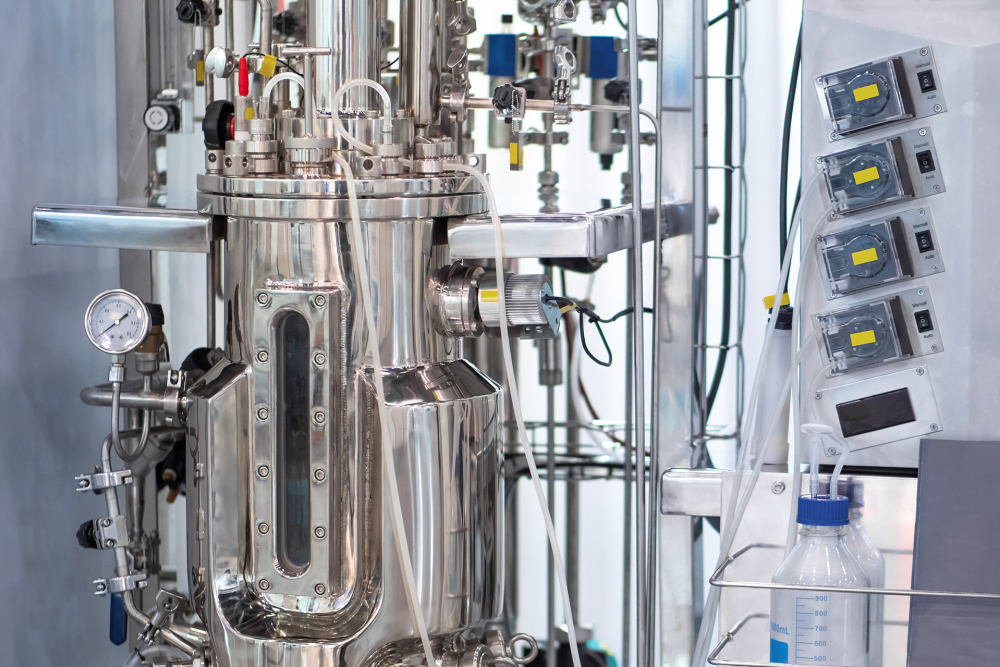
The method has a long history, with advances in cryopreservation technology and vessel design contributing to improved freezing protocols. However, the use of cryovessels for freezing bulk drug substance also comes with some drawbacks. These include the need for specialized equipment, the potential for cryovessel-related challenges during scale-up, and the need for careful handling and storage conditions. Manufacturers are limited to the temperatures down to max. -50°C and must accept long freezing times of up to days until the biopharmaceutical liquids are frozen entirely in the bulky shape of the cryovessel.1
Switch to single-use: Blast Freezing to be established
The open architecture of cryogenic steel containers has intensified the need for closed systems. Single-use technologies appeared to be the freezing method that would further reduce the risk of contamination and make the freezing process more sterile, safer and, as now proven, more sustainable.2
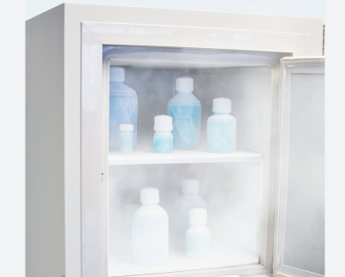
Bulk products are now filled into single-use primary packagings in which it is frozen. These primary packagings are single-use bags, bottles and other custom single-use containers. After filling into single-use bioprocess containers, they have been placed into static or blast freezing devices.
Blast freezing is a commonly employed technique in the biopharmaceutical manufacturing of large volumes to achieve faster and more uniform freezing of biomaterials than with cryovessels. This method involves subjecting the samples to high-velocity cold air. However, both static and blast freezers have their disadvantages. Since they’re originally designed to hold ultra-low temperature with air circulation, freezing in static and blast freezers can lead to cryoconcentration, where solutes accumulate in unfrozen regions, potentially impacting product stability and quality. Additionally, the lack of precise control over the freezing process in both static and blast freezers pose challenges in maintaining consistent freezing conditions in different scales.
Read more: Cold storage requirements for APIs
While cooling energy is dispersed in blast and static freezers, the energy in plate-freezers transfers directly to the liquid. Direct surface contact makes it easier to control the temperature inside the single-use bag and regulate the last point of freeze within the recommended scope of controlled cooling rate. The single-use bag is carried in the protective RoSS® shell. The secondary packaging around the bioprocess container enables state-of-the-art plate-based freezing with direct contact between the bag and the cooling medium.
Advantages of plate-based freezing
Compared to traditional and older methods of freezing biopharmaceuticals, plate-based freezing now enables the following:
- Scalable freezing performance from 10mL to 50L single-use bags
- Control of freezing at a cooling time of less than 10 hours to -80°C of all sizes of 2D single-use bags
- Closed system to safeguard sterility throughout aliquoting, freezing, storing, shipping, etc.
- Full automation in compliance with cGMP and 21 CFR Part 11
- Customized freezing rates ensuring highest product quality after cold chain management
- Less manual intervention, less documentation/validation, shorter process cycles
CryoVessel Platform 1 | Blast-Freezer Platform 2 | Plate-Based Freeze Thaw Platform RoSS.PFTU XL | Comments | |
Fast Freezing | × | × | ✅ | The RoSS.pFTU XL achieves controlled freezing to -80°C in less than 10 hours. |
Low Footprint | × | ⁓ | ✅ | Optimized for a maximum volume on the lowest footprint needed |
Vendor-agnostic primary packaging | ⁓ | × | ✅ | Full freedom on choice of your primary packaging supplier to ensure a closed system. |
Modularity & Scalability | × | × | ✅ | Scalable freezing with the RoSS.pFTU plate-freezers from 1L up 500L nominal volume per batch |
Minimum Manual Handling | ⁓ | ⁓ | ✅ | Fully automated freezing process & simple loading/unloading of the palette-size racked |
Product Viability | × | × | ✅ | Higher product quality with controlled plate-freezing preventing the effect of cryoconcentration . |
Entering new realms of freezing large volumes
In step with the biotech industry, supporting process solutions are also evolving. Novel therapies require an advanced manufacturing process. The requirements for each product are constantly changing, whether in the commercial production of monoclonal antibodies (mAbs) or antibody-drug conjugates (ADCs), or preparation and processing fluids, such as buffer solutions. These sometimes complex needs can now be answered on a product-specific basis.
The freeze-thaw industry has evolved from rigid processes through rigid stainless-steel vessels. Plate-based freezing allows manufacturers to adjust the freezing rate, processing volumes and endpoint temperature to meet their needs. Previously unthinkable.
Cryovessels are still in use mostly because of their history. Even though the majority of biomanufacturers still have them in day-to-day operation, the technology is outdated and not efficient. The future of freezing and thawing large volumes in biomanufacturing belongs to plate-based freezing.
- Large-Scale Freezing of Biologics: A Practitioner’s Review, Part 2: Practical Advice, https://, Published 2009
- Streamlined life cycle assessment of single use technologies in biopharmaceutical manufacture, https://pubmed.ncbi.nlm.nih.gov/35007778/, Published 2022