CDMO in Biopharma: Opportunity or risk?
Table of contents
ShowIn this article, we will discuss the differences between CMOs (contract manufacturing companies) and CDMOs (contract development and manufacturing companies), the characteristics and types of them, the services that they typically offer, the opportunities & risks of contract manufacturing, our top 7 CDMO companies in 2025 as well as why CDMOs increasingly are using single-use systems.
What is a CMO?
A Contract Manufacturing Organization (CMO) in the pharmaceutical sector specializes in drug manufacturing. CMOs handle the production of biologics and other drug substances, catering to pharma companies that either do not have or choose not to use in-house capabilities.
Ensuring regulatory compliance and following Current Good Manufacturing Practice (cGMP) standards, CMOs offer valuable manufacturing services. Collaborating with CMOs allows pharma companies to streamline the manufacturing process, ensuring the efficient and compliant production of new drugs.
What is a CDMO?
CDMO stands for contract development and manufacturing organization. They are key players in the pharmaceutical supply chain, offering end-to-end services in drug development and commercial drug substance management. Specializing in distinctive areas in the life sciences industry, CDMOs handle the entire process from drug development to scale-up and commercial production.
Full-service CDMOs can cover all the necessary steps in finding and producing Active Pharmaceutical Ingredients (APIs), all the way from preformulation and formulation development, through clinical trials of biologics and commercial production. Often, a CDMO partners with other, even more specialized service providers, creating an interplay that drives advancements in biotechnology and supports pharmaceutical companies in bringing innovative products to market.

CMO vs. CDMO: What is the difference?
Comparing CMOs and CDMOs, here is an overview of key similarities and differences:
Aspect | CMOs | CDMOs |
Scope | Primarily manufacturing-focused services | Services covering development and manufacturing |
Types | Various types including end-to-end CMOs, individual component manufacturers, and collaborative manufacturing | Predominantly categorized into scale CDMOs, focused CDMOs, and specialized CDMOs |
Services | Tailored manufacturing services | End-to-end solutions often specialized in specific areas such as API or biologics |
Benefits | Cost efficiency, specialized expertise, flexible capacity | Comprehensive solutions, specialized knowledge, flexibility, and risk management |
Risks | transfer of accountability, dependency, communication challenges | Potential lack of customization, dependence on external partners, transfer of accountability, and communication intricacies |
CMO services
While no two contract manufacturing organzations are completely alike, they are all defined by certain services as part of their portfolios. Roughly, contract manufacturing organizations can be broadly categorized as follows:
- End-to-end CMOs: Provide services covering the entire manufacturing process, from process development to the production of finished pharmaceutical products.
- Component manufacturers: Specialize in the production of individual components, such as Active Pharmaceutical Ingredients or specific drug formulations.
- Collaborative manufacturing partners: Emphasize a collaborative approach, working closely with pharmaceutical companies to tailor manufacturing services based on specific requirements and stages of drug production.
CMOs extend a suite of services to startups and long-established pharma companies, addressing critical aspects of drug manufacturing. These services encompass:
- Formulation development
- Drug product manufacturing
- Regulatory compliance measures
- Validation processes
- Pricing strategies
- Time-to-market acceleration
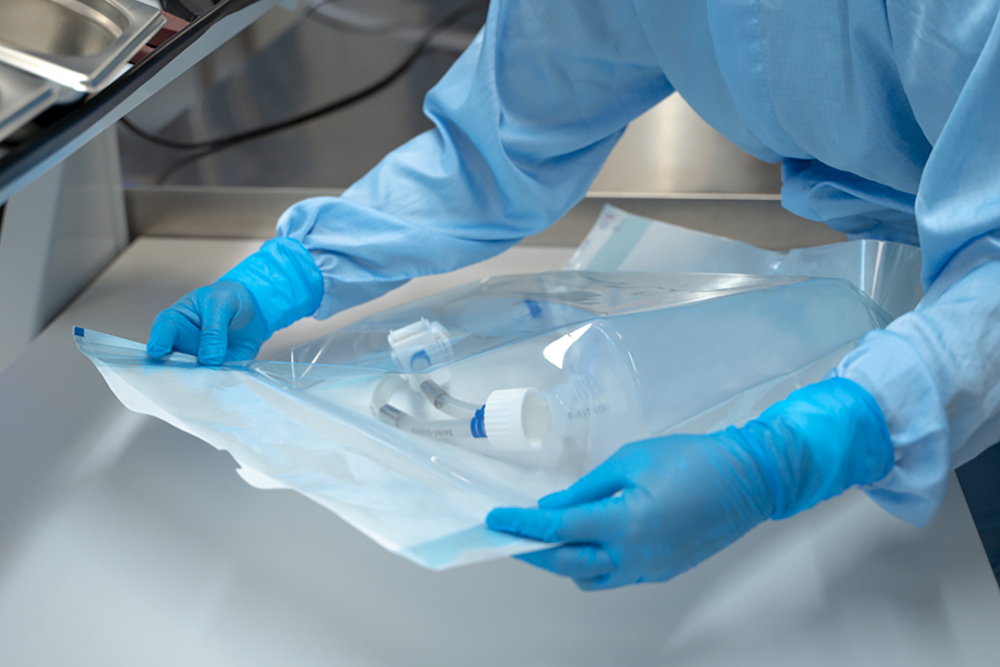
CDMO services
CDMOs can be distinguished as follows:
- Scale CDMOs: Specialize in large-scale manufacturing, providing the capacity and capabilities to offer a wide variety of services.
- Focused CDMOs: Concentrate on distinctive types of drug substances (e.g. monoclonal antibodies), offering in-depth expertise and efficiency.
- Specialized CDMOs: Tailor their services to niche areas, bringing unique capabilities and knowledge to the development and manufacturing of specialized pharmaceutical products
Contract development and manufacturing organzations offer an array of specialized services to meet the diverse needs of the pharmaceutical industry, emcompassing:
- End-to-end development and manufacturing
- API development and manufacturing
- Biologics development
- Clinical trial support
- Customized solutions
Most types of CMOs and CDMOs are increasingly using single-use systems to benefit from flexible end-to-end solutions. 1
Contract manufacturing: advantages and risks
CDMOs are able to provide highly specialized drug development and manufacturing services, which in turn will help pharmaceutical companies push their average output and increase their market cap.
In addition to providing access to operational excellence as well as the necessary expertise, CDMOs generally offer on-demand scale-up and allow the outsourcing companies to stick to timelines and tight deadlines that are part of the highly contested TTM (Time To Market) race.
The greatest opportunities and benefits working with CDMOs are:
- Access to state-of the art equipment and technology
- Scalability
- Access to additional expertise
- Meeting deadlines
- Risk mitigation
CDMOs provide end-to-end solutions, covering the entire drug development and manufacturing cycle. This approach can streamline processes and enhance efficiency. Additionally, CDMOs often specialize in areas such as API development and biologics, offering tailored expertise for specific projects as well as connections to even more specialized service providers, managing their seamless interplay.
Nevertheless, challenges exist. While CDMOs offer specialized services, there might be a lack of customization for unique project requirements. Dependence on external partners for critical stages of drug development and manufacturing can introduce risks: The CDMOs choose which technologies they want to rely on, which has an impact on overall product quality and production speed. Furthermore, the collaboration with CDMOs may result in communication challenges and potential coordination issues.
How to choose a CDMO?
Pharmaceutical companies are most likely looking for establishing long-term partnerships for their outsourcing rather than having to change their CDMO partners regularly. Topics to take into consideration for the selection are the level of product development and process development, but also questions regarding supply chain as well as validation and quality.
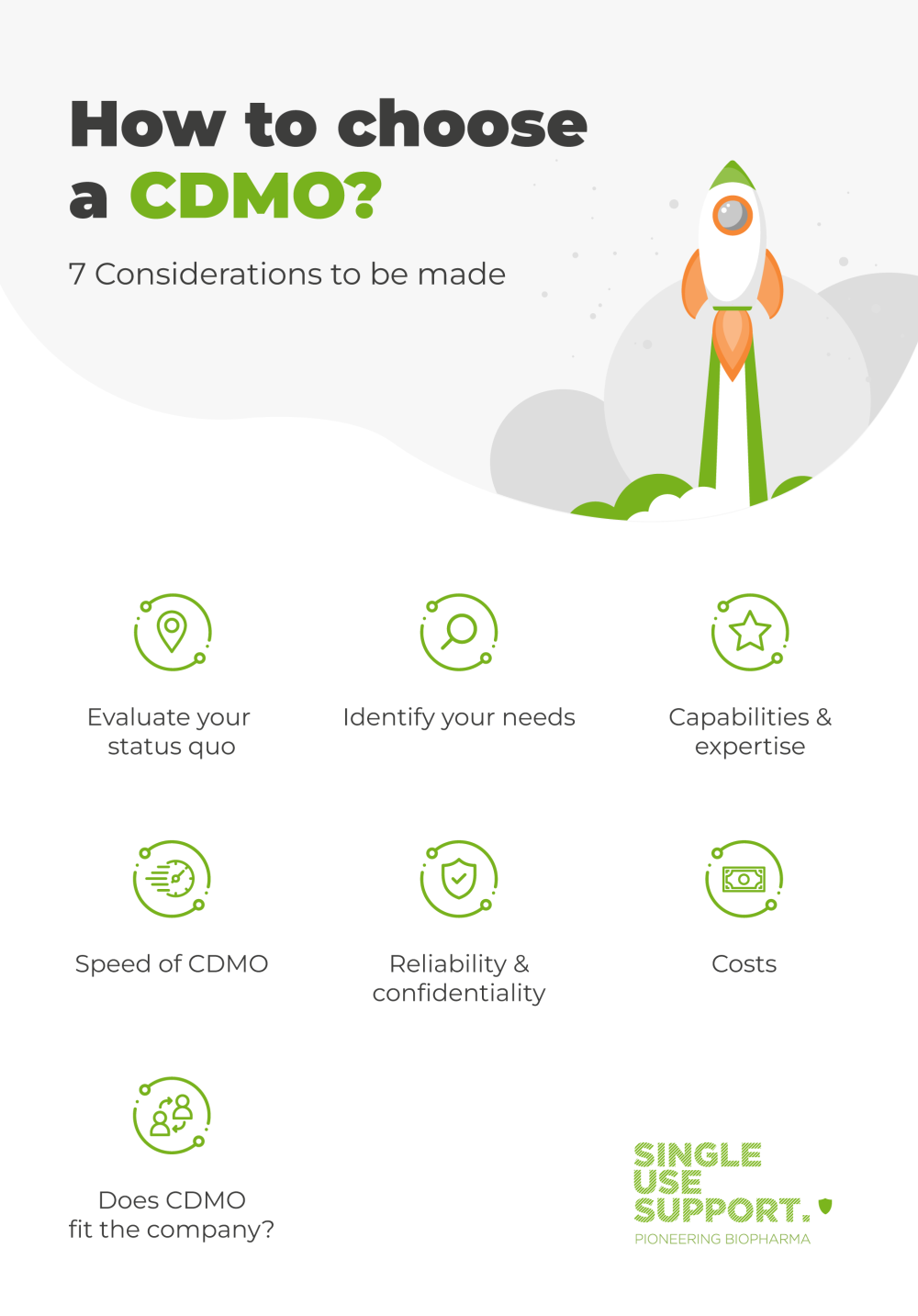
Costs of contract manufacturing
Important aspects to select a CDMO are the status quo, identification of needs, the CDMOs capabilities and expertise, the CDMOs speed, a high level of reliability and confidentiality.
While all of the above mentioned benefits speak for themselves, costs are an additional decisive factor when establishing a partnership with a CDMO. As traditional pricing and costing does not take added value into account, new models are required. The reality is that most executives simply add up the costs of materials, labor and other components when calculating the final costs. This results in highly complex offer and costing structures that differ between countries and even sites.
What is needed is an approach based on a harmonized cost-accounting method that reflects the value added. CDMOs might use cost rates that are differentiated by service lines and departments to reflect efforts and resources more accurately, not least if they are seeking to be listed by NASDAQ or other stock exchanges worldwide.
Amongst the main drivers of cost reduction are more rapid changeovers as well as a reduction in water and wastewater requirements and the elimination of both clean-in-place (CIP) and sterilize-in-place (SIP) validation. Along with an increased level of automation, this leads to a reduced need for labor - and energy - thus minimizing costs further.
According to an evaluation by the German biopharmacy and biotechnology company Rentschler, the annual costs of stainless steel are higher than those of disposable virus filtration systems in all but one category (Read the article in https://bioprocessintl.com). So generally speaking, it is advisable to consider the full life-cycle costs when contemplating a switch from traditional stainless-steel tanks to single-use technologies.
Outsourcing manufacturing: opportunity for growth
If done right, outsourcing to CDMOs certainly has great benefits, especially for young companies and start-ups that do not yet possess the means to cover all manufacturing stages in-house. Experience and expertise coupled with flexible available capacities and compliance with CMC standards or CGMP and GMP guidelines make API production easier for up-and-coming businesses. In the end, it’s always down to choosing the right partner, but also the right systems and platforms.
Single-use technologies are an ideal solution that help both CDMOs and self-sufficient companies improve their processes and push their output.
Top 7 CDMO companies
Pharmaceutical CDMOs are involved in the supply chain of often groundbreaking pharmaceuticals, and trusted partners for both start-ups and big players in the pharma industry. Ranked by revenue in 2022, the top contract drug manufacturing companies include:2
#1 – Lonza Group
Revenue 2022: USD 6.97 billion1. Lonza's commitment to meeting the diverse needs of the industry, spanning from small molecules, health ingredients and capsules to biologics and cell & gene therapies, positions Lonza as a trusted partner for pharmaceutical companies seeking reliable and comprehensive CDMO services. The company will continue to drive progress in various fields, such as microbial fermentation, bioconjugates, and more.
#2 – Thermo Fisher Scientific
Revenue 2022: USD 6.97 billion1. Thermo Fisher Scientific focuses on commercial manufacturing, advanced therapies, small and large molecules as well as clinical trials, the company offers multiple end-to end services in pharmaceutical development and production – in areas like antibody production, cell culturing, and DNA technologies.
#3 – Catalent
Revenue 2022: USD 4.28 billion1. Catalent’s focus lies on services concerning brand extensions in consumer health, blockbuster drugs, and personalized medicine. It plays an important role in the production of Novo Nordisk’s Wegovy, used in diabetes therapy. In 2024, it was announced that Novo Holdings would acquire Catalent, which would also allow increasing the production of Wegovy and Ozempic.3
#4 – WuXi Biologics
Revenue 2022: USD 2.11 billion1. With a global footprint and a focus on biopharmaceuticals, WuXi Biologics offers a wide range of services, even extending to research processes, such as antibody and protein services as well as vaccines, bioconjugation, and mRNA services.
#5 – Samsung Biologics
Revenue 2022: USD 1.77 billion1. Samsung Biologics' contributions to fields like cell line development as well as the production of a variety of biopharmaceuticals make it a trusted ally in advancing the possibilities within the biopharmaceutical sector.
#6 – Siegfried AG
Revenue 2022: USD 1.38 billion1. Siegfried is engaged in APIs, process optimization, intermediates or finished drug products. Additionally, Siegfried AG has a strong focus on sustainability, aiming to make supply chains greener and more environmentally friendly.
#7 – Fujifilm Diosynth Biotechnologies
Revenue 2022: USD 1.31 billion1. Fujifilm Diosynth Biotechnologies stands out as a trusted partner for pharmaceutical companies, with services in areas like fermentation, CGT, and cell culturing. In the latter, for instance, the company has extensive expertise in culturing insect cells, and is “a licensed manufacturer of a commercially approved baculovirus-expressed product”.34
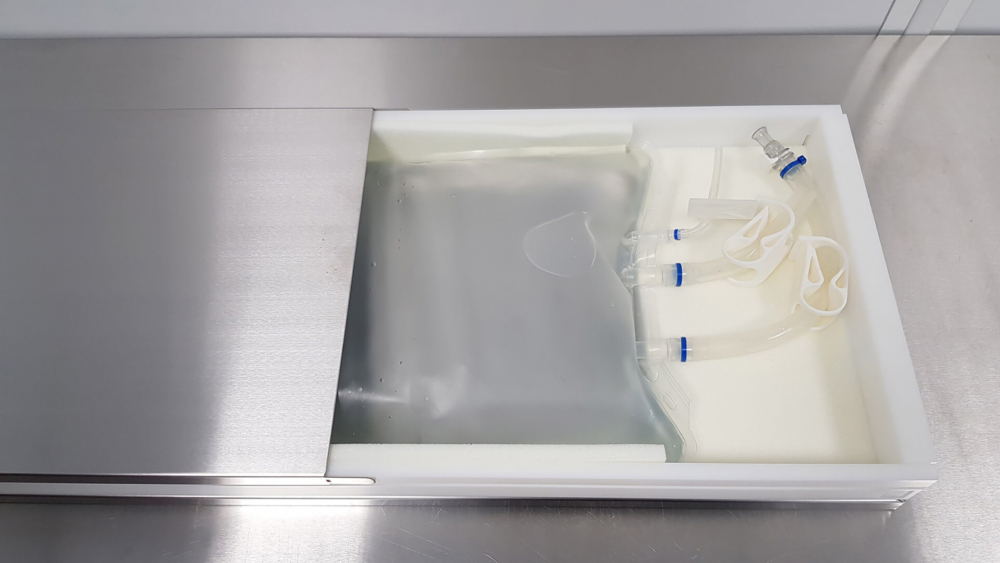
Why CDMOs increasingly use single-use systems
When it comes to the handling and processing of cell-based and biological drug substances, CDMOs (contract development and manufacturing organizations) are increasingly switching to single-use technology. There are several reasons for this shift, the advantages and disadvantages of which have been extensively discussed and debated for years.
As part of their fee-for-service activities, CDMOs typically operate several manufacturing lines. Manufacturing lines differ in scale and type of equipment - which forces the CDMOs to adopt systems that allow for flexible production capacities, fast changeovers, and rapid production at different scales.
By combining a number of benefits, single-use technologies that are compliant with cGMP and GAMP seem the perfect choice. For manufacturers of drug substances, they provide a more efficient, cost-effective, and scalable solution than stainless-steel tanks by offering:
- increased flexibility and faster set-up times
- reduced risk of contamination
- lower cleaning and maintenance costs
- easier scalability
- more efficient use of space
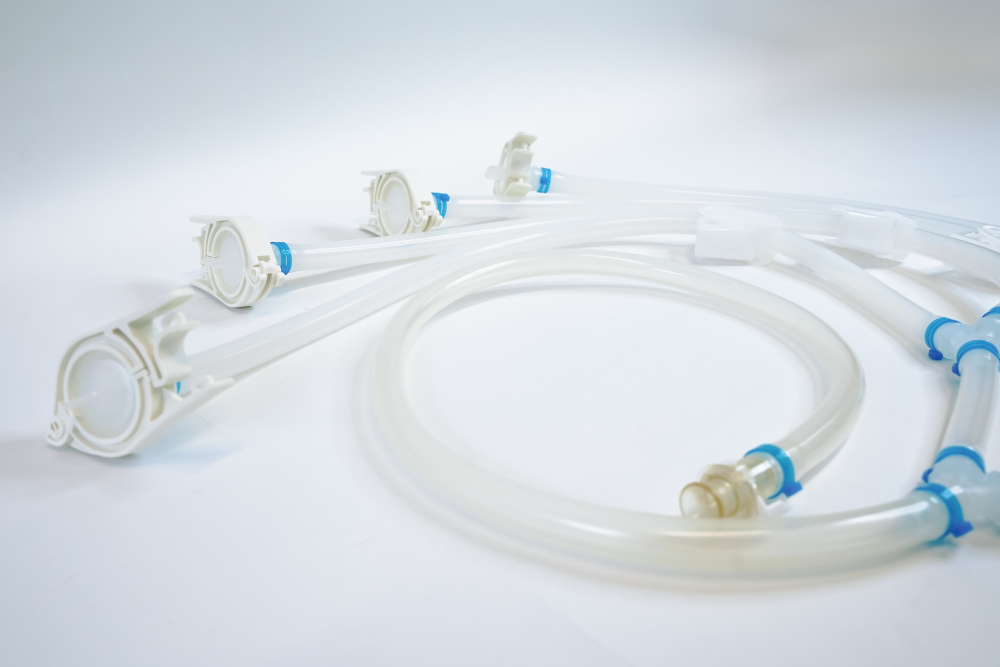
CDMOs as early adopters of single-use technologies (SUT)
Flexibility and scalability are great benefits with the use of Single-use compared to stainless steel technology applications. Apart from that, there are other reasons that explain why CDMOs are early adopters of single-use technology. CDMOs have to speed up biopharmaceutical processing of a fed-batch production and reduce process changeover times between different batches. Contract organizations are service providers and as such, if they want to be or remain successful, they have to keep up with the demands of the market if not be leaders in terms of new developments.
Both of these can be achieved with single-use systems, which offer flexible and more efficient alternatives to traditional multi-use equipment and processes. In addition to enabling manufacturers to respond quickly to changing market demands, they have the added benefit of reducing the risks of cross-contamination. This is vital when it comes to handling drug substances that are as sensitive as they are valuable.
Efficiency: Flexibility, scalability & high speed
Coming back to the biggest advantages of single-use technologies, how can SUTs take flexibility, scalability and high speed be taken to the next level?
Flexibility and scalability basically go hand in hand: Platforms consisting of single-use systems can be flexibly tailored to meet specific customer requirements, including the option to scale up or down quickly and easily, according to the volumes required. Modular systems enable flexibility, and automated systems coupled with state-of-the art process solutions enable limitles scalability. With single-use technology, it is possible to scale from 10mL to 400L per batch.
In addition, by enabling faster production processes and reducing lead times, they also increase the overall speed, be it in terms of speed to market, speed of reacting to changing requirements or changeover between processes.
What about sustainability and energy consumption?
It may sound paradoxical, but the reality is that disposable single-use components for biopharmaceutical manufacturing are in fact more sustainable than stainless steel. Traditional systems require high purity water and heat for cleaning and sterilization purposes, both of which have an impact on our environment. Single-use components, on the other hand, have a reduced need for cleaning and maintenance, which leads to a decreased consumption of water and energy.
This being said, disposal is still a consideration, not least because components might be classified as bio-hazardous. In addition, single-use systems are typically made up of different types of plastic materials that are difficult to separate. Using the mixed plastic waste for the production of durable products, such as pallets and plastic boards, could be a solution. This is just one approach to improve sustainability issues. Another idea is to develop sterile consumables that can be reused, such as the option of a multi-use protective shell for single-use bags. Single Use Support is developing in this area and provides the option of a multi-use protective RoSS shell.
In addition, most suppliers of single-use components are striving to further reduce energy consumption. Single Use Support has been certified according to the EcoVadis Sustainability Rating 2022.
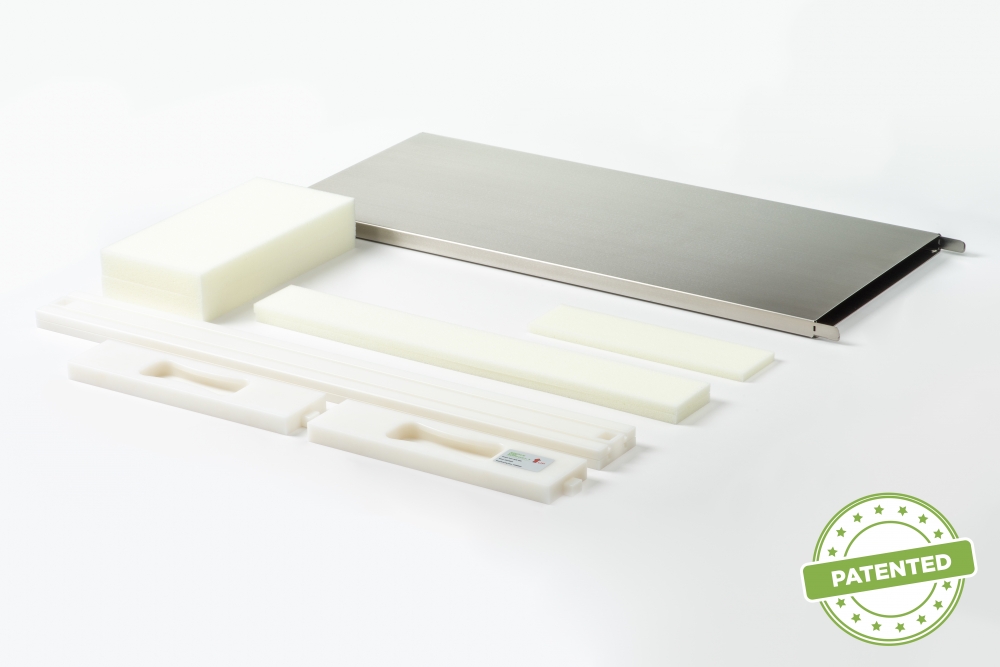
Why will many more CDMOs switch to single-use technology?
With SUT solutions constantly improving, there is an increasing number of reasons why CDMOs are or should be adopting single-use technology. From a production perspective, the most obvious benefit of single-use is time savings, with the potential of reducing setup time for each process from several days to mere hours. Flexibility and scalability offer great benefits and are important reasons why more and more CDMOs are moving to disposables. Single-use technologies can be beneficial for all areas of application, including ADC CDMOs, viral vector CDMOs, mRNA CDMOs, and more.
The minimized need for cleaning and maintenance further reduces time spent while it also proves to be more environmentally friendly than traditional stainless steel equipment. Not to forget the safety and quality aspects that single-use systems offer. Closed systems reduce product loss and cross contamination.
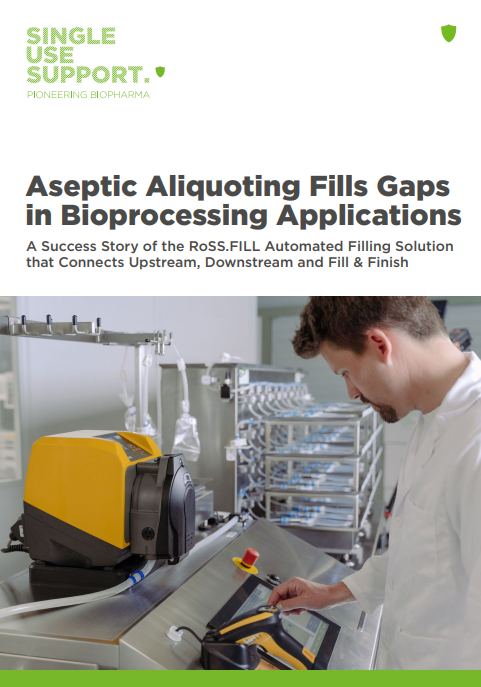
Download Success Story
Success Story: Aseptic Aliquoting
Download our success story on the RoSS.FILL automated filling solution that connects upstream, downstream and fill & finish processes. It covers applications such as seed train intensification, bacterial fermentation, media perparation, and fill finish of small volumes in single-use bags.
Single Use Support – trusted partner for pharma companies and CDMOs
Single Use Support stands out as a reliable and strategic partner for both pharmaceutical companies and CDMOs, which increasingly use single-use systems. Specializing in providing innovative solutions for the biopharma industry, Single Use Support provides top pharmaceutical CDMOs with a range of products that contribute to the efficiency of fluid and cold chain processes. Its efficient, automated process solutions are designed to decrease the total cost of ownership of automated single-use technologies. Several case studies based on real-world evidence, the evaluations confirm an early ROI of investments in single-use technologies. A key aspect is reducing OPEX (operational expenditures). Lower operating costs go hand in hand with automated solutions to achieve:
- less labor
- less time-consuming processes (less resources)
- automated documentation thanks to 21 CFR Part 11 instead of manual documentation
Single Use Support’s portfolio includes the sophisticated fluid management platform RoSS.FILL, which improves process flexibility with its modular and scalable setup. The automated aliquotation solutions cover various stages in pharmaceutical development and manufacturing, from lab scale to commercialization.
The plate-based freezing platform RoSS.pFTU is equally scalable and versatile, providing extensive control over the delicate freezing process of biopharmaceuticals. The controlled rate freeze and thaw platforms, available in different sizes, are a part of Single Use Support’s broad portfolio of innovative freeze and thaw solutions.
With several other solutions based on single-use technologies, such as ultra-low temperature storage freezers, bioprocess containers, there are cleanroom capabilities for single-use consumables, including single-use bags, secondary packaging, single-use assemblies and many more. Single Use Support is a sought-after partner for CDMOs, CMOs, CROs, and pharmaceutical companies themselves.
Fluid management solutions for CDMOs
Cold chain solutions for CDMOs
Single-use consumables for CDMOs
FAQs about CDMOs
What are CROs in the pharma industry?
Contract Research Organizations (CRO) are specializing in early-stage development and clinical research and play a vital role in the drug discovery and clinical trials in the pharmaceutical sector. CROs facilitate the progression of pharmaceutical products through regulatory requirements, including compliance with Good Manufacturing Practices (GMP) and FDA regulations.
What is the difference between CDMO and CRO?
As opposed to CDMOs and CMOs, CROs - short for contract research organizations - are hired to handle clinical trials after drug development by the CDMO.
CROs plan, coordinate, execute and supervise all processes involved in developing and running a clinical trial, including the recruitment of participants, monitoring of the trial, managing of data and more. It manages feedback and requirements from different stakeholders, such as manufacturers, sponsors, researchers or regulatory agencies.
Is Single Use Support a CDMO in biopharma?
No. Single Use Support is a process solution provider for biomanufacturers, many of which are CDMOs. Single Use Support offer end-to-end solutions in fluid and cold chain management that allows CDMOs to handle small to large volumes of drug substances. With. The company's state-of-the-art single-use systems offer reliable and sterile protection, thus minimizing product loss. Process solutions include protection shells, aseptic filling and controlled freeze-thaw platforms, optimize the cold chain process. Single Use Support offers expertise and state-of-the-art technology to both self-sufficient manufacturing companies and CDMOs, and enables them to become more flexible and agile - both in terms of volume and constantly changing demands.
What is the difference between CDMO and CMO?
The difference between a contract development and manufacturing organization (CDMO) and a contract manufacturing organization (CMO) is - as the name suggests - development. CMOs are companies that take a pre-formulated drug and manufacture it, while CDMOs also offer development services.
CDMO are the preferred choice of many pharmaceutical companies as they provide a higher degree of consistency than CMOs and still adhere to strict timelines.
- Pharma Contract Development and Manufacturing Organization (CDMO) Predictions for 2030, https://www.alvarezandmarsal.com/sites/default/files/2023-05/Pharma%20Contract%20Development%20and%20Manufacturing%20Organization%20%28CDMO%29%20Predictions%20for%202030.pdf, Published
- Leading 10 contract development and manufacturing organizations (CDMOs) based on revenue in 2022, https://www.statista.com/statistics/1419931/top-cdmo-companies-by-revenue/, Published 2022
- Novo Holdings Completes Acquisition of Catalent, https://www.catalent.com/catalent-news/novo-holdings-completes-acquisition-of-catalent/, Published 18.12.2024
- Fujifilm Diosynth Biotechnologies. Your Cell Culture Partner for Life, https://fujifilmbiotechnologies.fujifilm.com/capabilities/biologics/mammalian-cell-culture/, Published