Overview of filter integrity testing methods
Table of contents
ShowFilter integrity tests are essential in ensuring the reliability of biopharmaceutical processes – a stringent field governed by regulatory requirements such as those set forth by the FDA and GMP standards. These tests are critical components in upholding the quality and efficacy of filtration processes from the upstream side to downstream activities, affecting both multi-use and single-use technologies.
The consequences of filter failure in the life sciences industry can be drastic, ranging from product loss due to contamination to serious patient health issues. To prevent such failures, biopharmaceutical companies use a variety of filter integrity testing methods, as discussed in this article.
Filter integrity test – a definition
Filter integrity testing plays a pivotal role in assessing the reliability and efficiency of membrane filters, especially in critical applications such as sterile filtration. This testing process ensures that the membrane filters retain their intended functionality, specifically in preventing the passage of bacteria and other contaminants, thereby preserving the integrity of the entire filtration process.
Users and filter manufacturers commonly perform filter integrity testing to validate filter performance. Such evaluations include parameters to assess, e.g. the ability of bacterial retention by the surface area of a filter, ensuring that it adheres to the necessary standards for its designated applications.
PUPSIT – why validate filtration processes?
Pre-Use Post-Sterilization Integrity Testing (PUPSIT) is performed for the validation of filtration processes for biopharmaceutical companies, ensuring the reliability and effectiveness of membrane filters.
Read more: Annex 1 and the PUPSIT requirement
Validation is an essential step in maintaining the integrity of filtration processes within biopharmaceutical settings, and PUPSIT specifically focuses on the upstream side of the filtration system. This method is crucial for biopharmaceutical companies as it validates the integrity of the filters after the sterilization process and is mandatory following regulatory demands like Annex 1 as issued by the EU.1
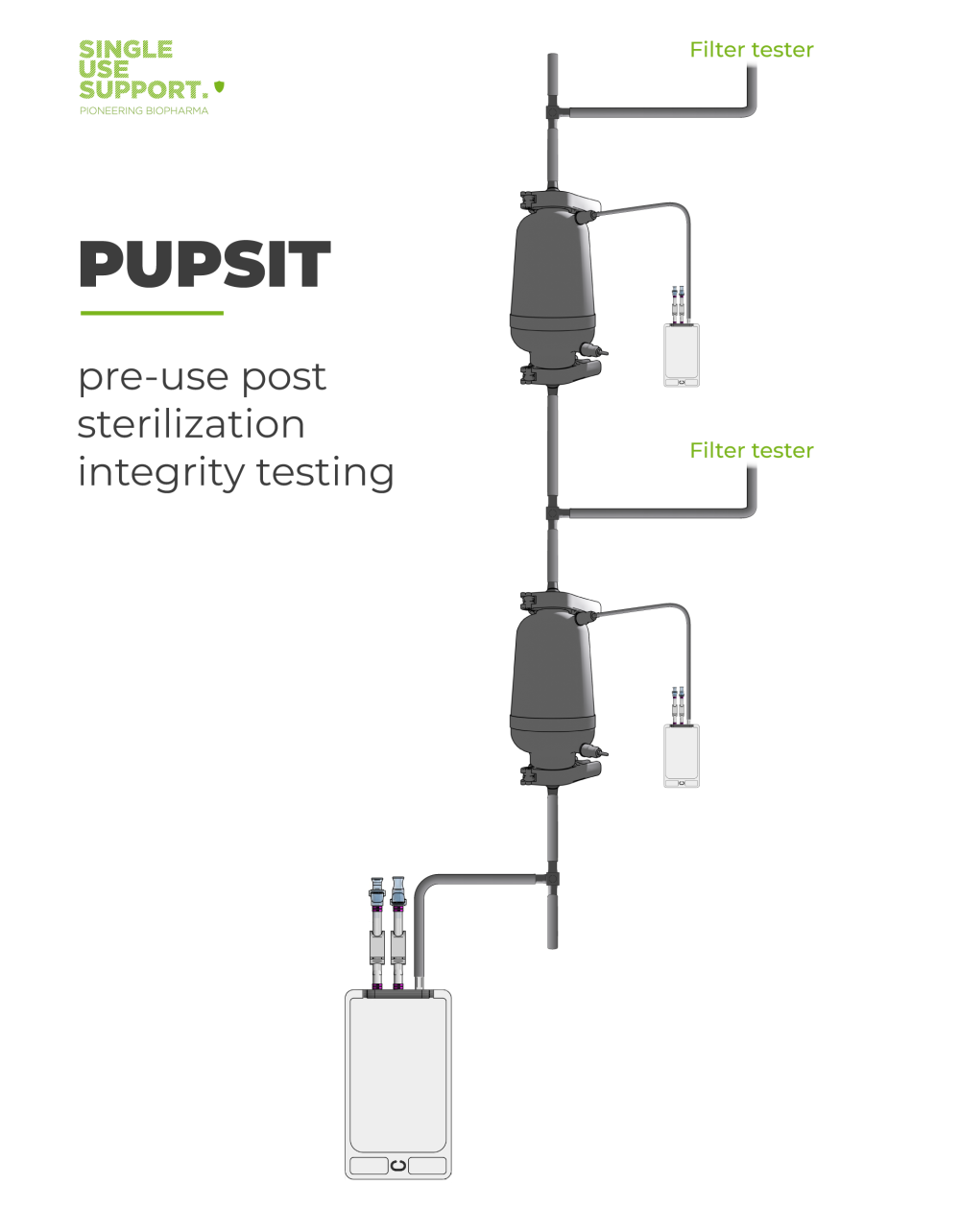
PUPSIT involves test procedures that assess the filter's performance in real process conditions, providing valuable insights into the efficacy of the overall process filtration. Implementing PUPSIT contributes to the establishment of a robust integrity test system within biopharmaceutical facilities, ensuring the proper functioning of filters.
Destructive vs. non-destructive testing methods
Destructive testing involves intentionally altering the structural integrity of the filter, providing tangible test results. This method is particularly useful for understanding the filter's limitations and failure points. On the other hand, non-destructive methods allow for the assessment of filter performance without altering its composition.
Key factors, such as flow rate, integrity of the filter housing, and the measurement of the largest pores, play crucial roles in determining the appropriate testing method. But as the name already suggests, destructive tests lead to damages in the very filter that has been tested, while non-destructive methods allow for a – now tested – filter to remain in place and be used for its intended purpose.
Methods in filter integrity testing and how they work
Filter integrity testing employs diverse methods, each crucial for assessing hydrophobic membrane filters as well as hydrophilic filters. Methods for filter integrity testing include:
- bubble point test
- diffusion test
- pressure hold test
- water intrusion test2 3
They utilize distinct procedures and measurements. Evaluating parameters like pore size, air flow, filter housing integrity, and differential pressure, users can understand the performance of the filter assembly. By using these methods and associated test equipment, users can ensure the reliability and optimal functioning of membrane filters in varied applications.2 3
Bubble point test
The bubble point test assesses the point at which a wetted filter membrane allows gas to pass through under increasing pressure. As pressure increases, the smallest pores open, enabling gas flow and creating bubbles. The pressure at which this occurs, known as the bubble point, correlates with the filter's pore size and surface tension.
Key to reviewing the filter's integrity, the bubble point test provides a quantitative measure of the filter's ability to resist pressure and maintain its structure. This method aids in identifying potential issues such as blockages or structural damage, impacting pressure drop and gas flow. Consequently, by leveraging the bubble point test, users can ensure the reliability and efficiency of their filtration processes.
Diffusion test
The diffusion test, also referred to as forward flow test, focuses on diffusive flow, measuring how gas passes through a wetted membrane under controlled conditions. In order to achieve measurable results, this method is frequently performed on filters with larger surfaces, as this results in larger amounts of diffused gas.
Crucial parameters, including flow rate, are integral to the diffusion test. Employing a flow meter, this method provides valuable insights into the effectiveness of the wetted membrane in facilitating or restricting gas diffusion.
Pressure hold test
The pressure hold test (or pressure decay test) focuses on the stability and endurance of the filtration system. This test involves subjecting the filter to a specified pressure and monitoring its ability to sustain that pressure over time. The key parameter assessed during the pressure hold test is pressure decay, measured using a pressure gauge.
The pressure hold test is particularly effective in identifying any potential issues related to the filter's stability, ensuring it can withstand the designated pressure without compromising its integrity.
Water intrusion test
The water intrusion test is a fundamental method in filter integrity testing, particularly for evaluating the performance of hydrophobic filters. This test assesses the filter's ability to prevent water intrusion under controlled conditions. During the test, water is applied to the filter, and the rate of water flow through the filter is assessed.
This test method helps pharmaceutical manufacturers determine the filter's effectiveness in resisting water intrusion and maintaining its integrity. It is especially promising as it does not require solvents to wet the hydrophobic filters prior to testing.
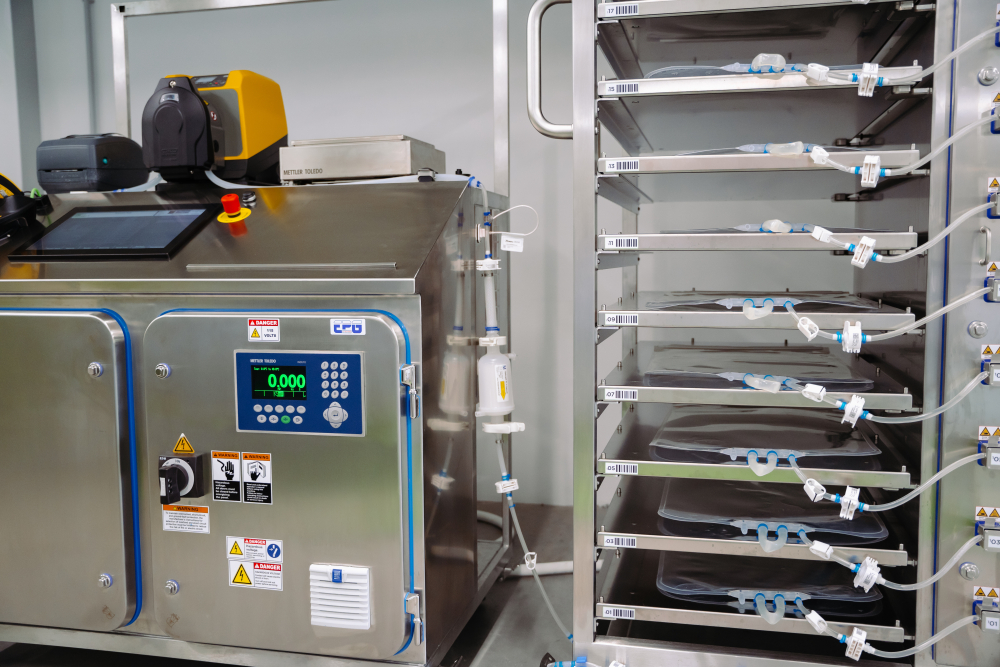
Automated filter integrity testing in closed single-use systems
In biopharmaceutical manufacturing, the adoption of closed single-use systems has revolutionized fluid and cold chain management. However, the mandatory performance of PUPSIT may pose challenges as it must not disrupt end-to-end processes, which hence have to be designed to facilitate filter integrity testing.
Single Use Support offers cutting-edge fluid management solutions tailored to allow Pre-Use Post Sterilization Integrity Testing within these automated, closed systems. By integrating automated filter integrity testing directly into the fluid management platform RoSS.FILL and the related single-use assemblies, biopharmaceutical companies can ensure stringent quality control and compliance with regulatory standards. RoSS.PPST is a fully automated, advanced PUPSIT skid designed to be customized for specific biopharmaceutical applications. It performs integrity testing on up to two filters, ensuring sterility and compliance with EU GMP Annex 1. In addition to its flexibility, the system is compatible with all common product filters and prevents contamination prevention and product loss.
- Annex 1 : Manufacture of Sterile Products, https://health.ec.europa.eu/system/files/2020-02/2020_annex1ps_sterile_medicinal_products_en_0.pdf, Published
- Filter Integrity Testing in the Pharmaceutical Process Environment, https://www.biopharminternational.com/view/filter-integrity-testing-pharmaceutical-process-environment, Published 2006
- 8 Tips to Ensure a Successful Filter Integrity Test, https://www.genengnews.com/news/8-tips-to-ensure-a-successful-filter-integrity-test/, Published 2013