Biopharmaceutical processing – how disposable solutions increase safety and efficiency
Table of contents
ShowBiopharmaceutical processing is an integral part of the life sciences, biotech and pharmaceutical industries. The associated market for biopharmaceutical manufacturing equipment and consumables is expected to grow with a double-digit CAGR for the next five years. A large part of this growth is due to the adoption of single-use disposable equipment by the biopharmaceutical industry.1
Single-use technologies revolutionize major aspects of biomanufacturing, such as upstream processing with single-use bioreactors, downstream processing with disposable filter systems and chromatography cartridges and the option to implement a high degree of automation as well.
These are the ingredients to an unfolding success story leading to unprecedented safety for personnel and patients, efficiency of bioprocessing and sustainability of biotechnology.1
Biopharmaceutical processing: Single-use vs. stainless steel
In biopharmaceutical processing, single-use, disposable platform systems are beginning to replace the concept of stainless steel vessels and durable piping.
Traditionally, biotherapeutic manufacturing processes relied on multi-use stainless steel equipment due to being seemingly longer lasting, less susceptible to critical product losses by leakage or rupture and extractables and leachables should be of no concern.
Modern high-performance polymers which are used in single-use equipment have come a long way and are now being adopted by chemical engineering and process development.
Disposables are manufactured with high purity, food and medical-grade biocompatible polymers that are largely resistant to many chemicals commonly used in protein, vaccine and gene therapy production.
Single-use bioprocessing requires less capital investment, is susceptible to comparably easy scale up and does not require any clean-in-place or sterilization-in-place, thus saving reagents and freeing workers and increasing productivity.
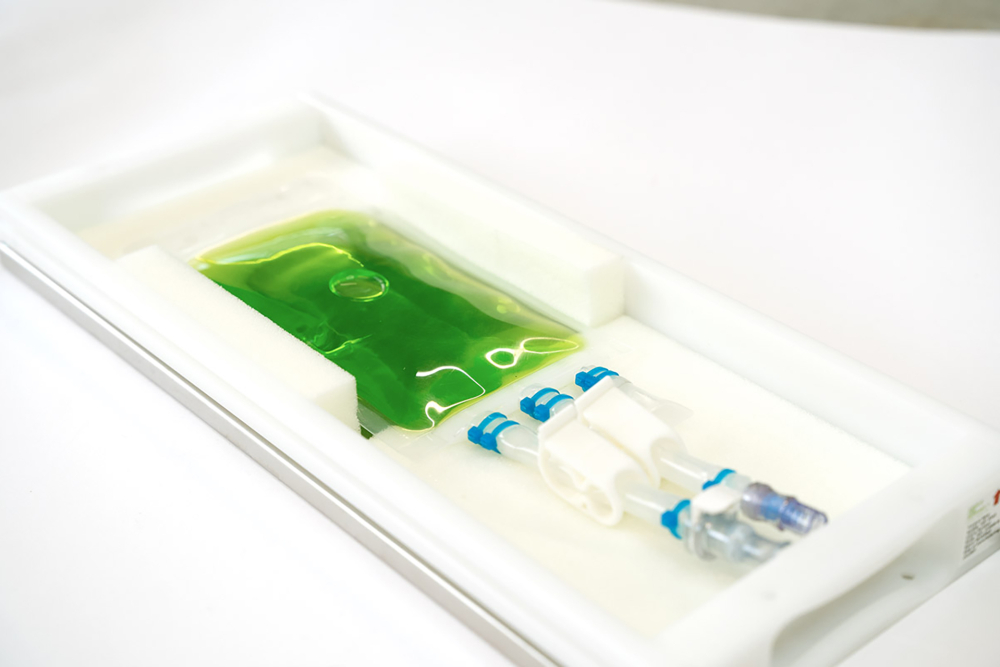
Higher time efficiency in the biologics supply chain
Time efficiency is high on the agenda – time is money, also in the healthcare industry. Single-use systems enable more efficient process designs. Therefore, Single Use Support offers innovative solutions to support the adoption process with solutions such as customizable manifolds to perfectly match any process needs and help to minimize downtime due to maintenance. They are custom manufactured under ISO 7 clean room conditions and delivered after sterilization.
Lower resource consumption in biopharmaceutical processes
Although biopharmaceutical processes today deliver highly valuable products, resource consumption has become a critical parameter for plant operation due to environmental concerns and the demand for cost reduction.
A large part of a traditional biopharma plant’s resource consumption can be traced back to the required cleaning-in-place, sterilization-in-place and validation protocols when using stainless steel equipment: these necessary processes use significant amounts of water and energy and chemicals.
Single-use systems are not subject to these requirements. After filtration or purification processes, the equipment is simply replaced with new immaculate units. This simplicity frees up labor capacity to increase plant efficiency, and reduce energy, water and detergent consumption. Even though the use of disposable equipment appears wasteful, the bottom line is a smaller environmental footprint and more sustainability with single-use technology.
Automated biopharmaceutical processing with modular end-to-end processes
End-to-end solutions are highly sought-after in biopharmaceutical processing of biologics such as monoclonal antibodies.
Single Use Support has developed an array of innovative platform systems to enable biopharmaceutical manufacturers to enjoy the advantages of single-use systems: high degree of automation is attainable to free workers for other tasks, minimization of the impact of human errors, and simplified maintenance.
Additionally, end-to-end solutions for automated bioprocessing developed by Single Use Support provide increased protection of storage containers, adding another layer of worker safety measures for the production team. Single-use fluid management solutions reduce the risk of contamination.
- Space saving shells to protect single-use bags during handling, freezing and thawing operations and transport
- Protective cases for small-scale single-use bags designed to fulfill the specific requirements of CGT (cell and gene therapy) logistics: high grade stainless-steel and a robust frame on the outside and 3D foam on the inside to ensure safe transport of high value medications. They are compatible with various freezing technologies, including liquid nitrogen cryogenic conditions down to -196 °C, and available as single-use and multi-use solutions.
- Bioprocess containers: disposable 2D bags for all bioprocesses with nominal volumes ranging from 10 mL for CGT applications up to 50 liters for large scale uses.
- Sterile, fully customizable fluid transfer assemblies – the one stop shop for all transfer logistics solutions.
- Cold chain shipping containers that allow the transport of products of high value under ultra-low temperatures for at least 6 days. Optional track and trace equipment and a multi-use option are available.
- Smart single-use bag totes to protect bulk drug substances in 1000 L 3D single-use bags. Automated smart filling and draining is enabled by an attached radar sensor. They are robust and stackable to allow maximal space efficiency. Conforms to cGMP.
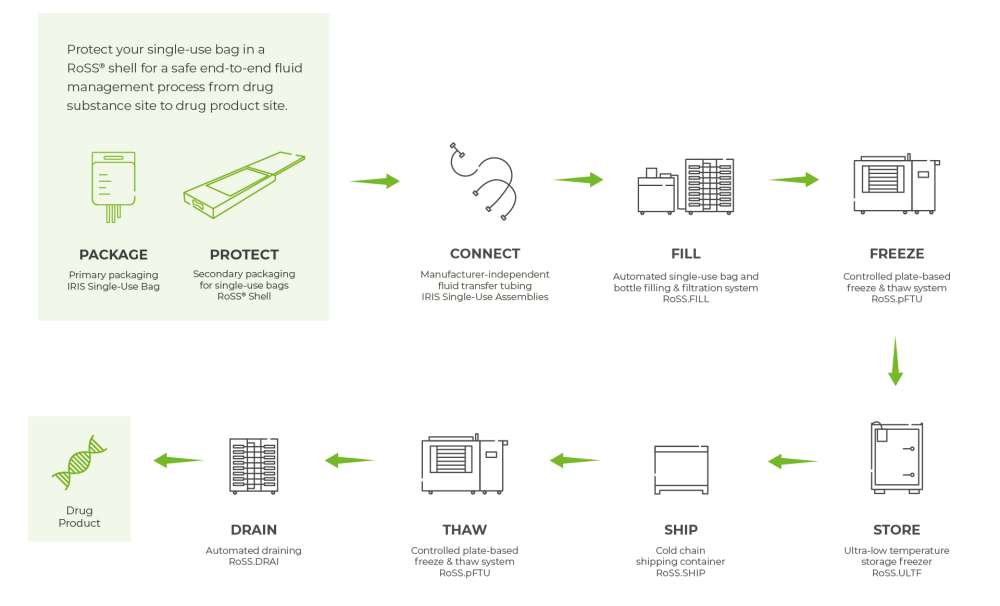
How biopharma companies achieve safety and regulatory compliance with single-use solutions
21 CFR Part 210 describes current Good Manufacturing Practices (cGMP) for pharmaceutical manufacturing and handling of pharmaceuticals. Additionally, companies must ensure product effectiveness and safety for FDA approval of their drug products or medical devices.
An example to highlight how solutions by Single Use Support simplify the operation of cGMP plants are the regulations for equipment cleaning and maintenance specified by § 211.67. The paragraph stresses the importance of proper cleaning, sterilization of equipment and an inspection prior to use. Record keeping of each instance is mandated.
By the implementation of single-use technologies, the cleaning effort can be extremely reduced, as many components are disposed of after usage. Not only does this help to comply with regulatory requirements, but it also helps to save water, energy and costs.
CDMOs as early adopters of SUT
CDMOs (Contract Research and Manufacturing Organizations) are partners that are frequently relied on by biopharma companies. Contract Development and Manufacturing Organizations offer various outsourced services concerning the development and production of biopharmaceutical products.
Many CDMOs have already switched to single-use technologies to optimize efficiency and security aspects. Flexibility and scalability play an important role for CDMOs in order to respond quickly to customer needs. Read more about: Why CDMOs are increasingly using single-use systems
Making pharmaceutical processing safe and efficient with Single Use Support
Single Use Support is a trusted partner of renowned biopharmaceutical manufacturers. They rely on the holistic approach of customizable end-to-end solutions for all of their process steps. Additionally, the high compatibility enables clients to use individual manufacturer-independent modular systems to connect single process steps to fulfill their specific needs.
Biopharma companies value the ease of interaction, since Single Use Support is their single point of contact for all after sale activities. Moreover, Single Use Support products score with their simplicity while keeping their capability to scale up and low operating costs.
Recommended articles
Single Use Support is a trusted partner of renowned biopharmaceutical manufacturers. They rely on the holistic approach of customizable end-to-end solutions for all of their process steps. Additionally, the high compatibility enables clients to use individual manufacturer-independent modular systems to connect single process steps to fulfill their specific needs.
Biopharma companies value the ease of interaction, since Single Use Support is their single point of contact for all after sale activities. Moreover, Single Use Support products score with their simplicity while keeping their capability to scale up and low operating costs.
- Biopharmaceutical Processing Equipment and Consumables Market by Product Type {Filtration, Chromatography [Consumables, Equipment], Disposable Bioreactors, Cell Culture Media, Shakers, Services), Application (Vaccine, mAb, R&D), and End User- Forecast to 2029, https://www.meticulousresearch.com/product/biopharmaceutical-processing-equipment-consumables-market-4200, Published