What are Active Pharmaceutical Ingredients (APIs)?
Table of contents
ShowActive Pharmaceutical Ingredients (APIs) are the cornerstone of pharmaceutical drugs, serving as the primary agents responsible for delivering therapeutic effects to patients. In this article, we give a definition of APIs and their significance. We further discuss the manufacturing process and future prospects and trends in the production of active pharmaceutical ingredients.
Definition of Active Pharmaceutical Ingredients
APIs can be defined as the biologically active components within pharmaceutical formulations. These are the chemical compounds specifically chosen for their ability to exert a therapeutic effect on the body.
APIs directly interact with biological targets to produce the desired physiological response. Whether it's relieving pain, reducing inflammation, or targeting specific pathogens, APIs are responsible for the efficacy of pharmaceutical products.
Active pharmaceutical ingredients can take various forms such as liquids, powders, crystals, and extracts. These substances are typically derived through chemical synthesis, plant extraction, or biotechnology processes. They are not directly consumed by patients but serve as essential components in the production of medications.1
Importance of APIs
Active pharmaceutical ingredients serve as the foundation upon which pharmaceutical products are built, dictating their therapeutic properties and clinical outcomes. The careful selection and precise dosing of APIs are critical factors in ensuring the effectiveness and safety of medications.
APIs and Drug Products
APIs and drug products are inextricably linked, with the former serving as the active agents encapsulated or formulated into the latter. While APIs provide therapeutic benefits, drug products encompass various components, including excipients, binders, fillers, and coatings, to facilitate delivery, stability, and patient compliance. Together, APIs and drug products work synergistically to address medical needs and improve patient outcomes.
Drug substances & APIs: Is there a difference?
The term "drug substance" refers to the pure, active ingredient in its raw form before it undergoes formulation into a final dosage form. In contrast, an API, or active pharmaceutical ingredient, refers to the same active ingredient but within the context of a formulated drug product, encapsulated or combined with other components such as excipients, binders, and coatings.
Examples of APIs
Active pharmaceutical ingredients are essential components in the formulation of pharmaceutical products, covering a wide range of therapeutic areas. Below is a list of popular APIs and their therapeutic uses.
API examples in injectables:
- Epinephrine: A hormone and neurotransmitter used as an emergency treatment for severe allergic reactions, asthma attacks, and cardiac arrest.
- Insulin: Hormone therapy used to manage diabetes by regulating blood sugar levels.
- Morphine: Opioid analgesic used to alleviate severe pain, such as that associated with surgery or trauma.
- Enoxaparin: Low molecular weight heparin used to prevent blood clots in conditions such as deep vein thrombosis and pulmonary embolism.
- Adalimumab: Monoclonal antibody therapy used to treat autoimmune diseases such as rheumatoid arthritis, Crohn's disease, and psoriasis.
API examples in tablets:
- Paracetamol (Acetaminophen): Used as an analgesic and antipyretic to relieve pain and reduce fever.
- Ibuprofen: Nonsteroidal anti-inflammatory drug (NSAID) used to alleviate pain, inflammation, and fever.
- Omeprazole: Proton pump inhibitor (PPI) used to treat gastroesophageal reflux disease (GERD) and peptic ulcers.
- Metformin: Oral antidiabetic medication used to manage type 2 diabetes mellitus.
- Simvastatin: HMG-CoA reductase inhibitor (statin) used to lower cholesterol levels and reduce the risk of cardiovascular events.
Differentiating Active Ingredients and Excipients
In contrast to active ingredients, excipients are inert substances added to pharmaceutical formulations to facilitate drug delivery, stability, and patient admission.
While active ingredients exert the desired pharmacological effects, excipients play essential roles in ensuring proper dosage form, solubility, and bioavailability. There is a wide range of excipients employed to cater to the diverse needs of drug formulations, distinguishing between those used in liquid formulations and tablets:
Some examples of excipients for liquid formulations:
- Solubility enhancers, such as Polyethylene glycol (PEG) 300, PEG 400, Propylene glycol (PG), and α-d-Tocopherol, Labrasol, and Oleic acid, are utilized to enhance the solubility of drugs intended for oral and injectable administration.
- Flavoring agents like Benzaldehyde, Menthol or Ethyl vanillin are commonly used to improve the taste and palatability of liquid preparations.
- Sweeteners such as Sucrose, Saccharine, Aspartame, and Sorbitol are added to both liquid and solid dosage forms to enhance sweetness.
- Preservatives, including Methyl Paraben, Ethyl Paraben, Benzoic acid, Sorbic acids and their salts, Benzalkonium chloride, and Chlorobutanol, are incorporated into oral liquids, ophthalmic solutions, and sterilized liquids to prevent microbial growth and maintain stability.
Some examples of excipients for tablet formulations:
- Antiadherents like Magnesium stearate are crucial components in tablets manufacturing to prevent sticking to manufacturing equipment.
- Lubricants like PEG, Magnesium Stearate, and Stearic acids and their derivatives are used in tablets to facilitate smooth tablet compression processes.
- Binders including Gelatin, Cellulose, or Starch are essential in tablet and granule formulations to bind the active ingredients together.
- Disintegrants such as Polyvinylpyrrolidone are added to tablets to promote their disintegration upon ingestion.
- Coating agents like HPMC or Gelatin are used to coat tablets for various purposes.
The API Manufacturing Process
The production of APIs is a multi-step process that encompasses synthesis, purification, and formulation stages.
The manufacturing process begins with the synthesis of the active ingredient, where chemical reactions are carefully controlled to produce the desired compound. This synthesis step involves selecting appropriate starting materials, applying specific reaction conditions, and optimizing process parameters to achieve high yields and purity levels.
Following synthesis, the API undergoes purification processes, such as crystallization, distillation, or chromatography, to isolate and remove impurities, ensuring the final product meets stringent quality standards.
Once purified, the API is formulated into dosage forms, such as tablets, capsules, or injections, using excipients and other additives as necessary to enhance stability, solubility, and patient acceptability.
API manufacturing is subject to rigorous regulatory oversight to protect public health and ensure compliance with quality standards. Regulatory authorities, such as the U.S. Food and Drug Administration (FDA) and the European Medicines Agency (EMA), establish guidelines and requirements for API production like current Good Manufacturing Practices (cGMP), including documentation of manufacturing processes, validation of analytical methods, and submission of regulatory filings.13
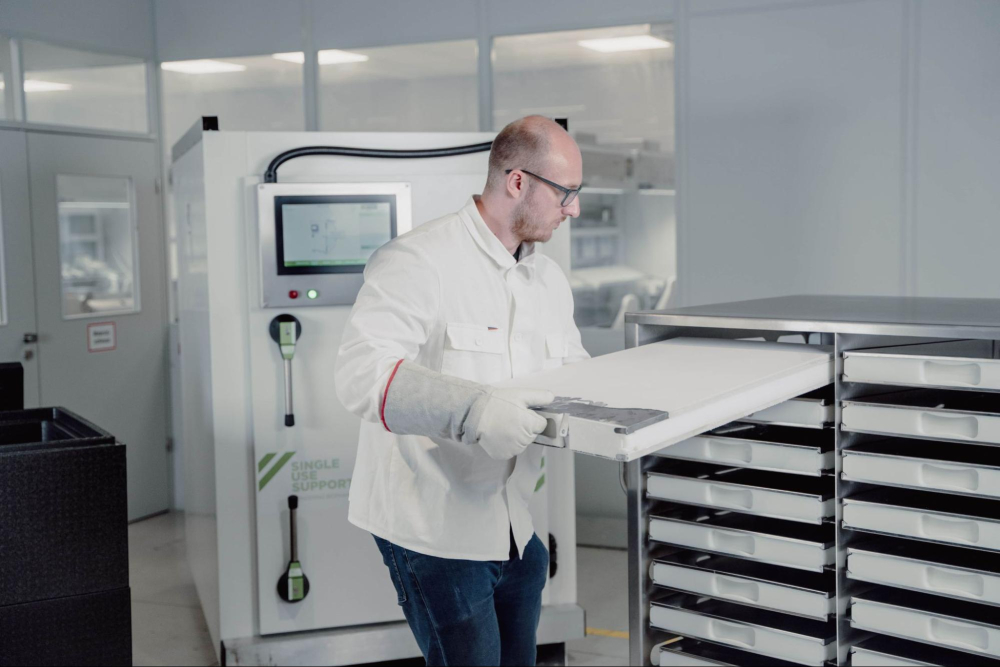
Good Manufacturing Practices (GMP) in API Production
GMP guidelines provide comprehensive regulations and standards for pharmaceutical manufacturing, covering aspects such as facility design, equipment maintenance, personnel training, and documentation practices.
By implementing GMP principles, API manufacturers minimize the risk of contamination, cross-contamination, and product variability, thereby safeguarding the integrity and efficacy of pharmaceutical products.
cGMP compliant drug substance management
Single Use Support specializes in the development of solutions for the production of active pharmaceutical ingredients using single-use technology. The maintenance of closed systems and automation of processes are designed to uphold the highest quality standards in production, effectively eliminating human error and minimizing product loss. These factors are crucial for GMP requirements such as reproducibility, standardization, and reduced risk.
Another aspect of cGMP compliance is the documentation of batch production records and manufacturing processes. Records are essential for pharmaceutical manufacturing sites as they provide detailed information about production performance and product quality. Automated systems streamline these processes by taking over documentation tasks.
Single Use Support provides comprehensive drug substance management solutions, encompassing filling and primary packaging, as well as protective solutions for single-use bags and platform systems for freezing and thawing. Our goal is to offer drug substance manufacturers maximum flexibility, efficiency, and safety throughout the production process.
Recommended Articles
Quality assurance and control measures are implemented throughout the API manufacturing process to maintain stringent quality standards and meet regulatory requirements.
This involves establishing robust quality management systems, conducting risk assessments, and implementing preventive measures to mitigate potential quality deviations.
Quality assurance protocols include comprehensive documentation practices, such as batch records, standard operating procedures (SOPs), and quality control testing protocols, to ensure traceability and accountability throughout the manufacturing process.
Analytical Assays
Assays provide critical data and insights into the quality attributes of raw materials, intermediates, and finished products. These assays involve a variety of analytical techniques, including chromatography, spectroscopy, and titration, to quantify the concentration of active ingredients, assess purity levels, and detect impurities or contaminants.
Quality Assurance and Control in API Manufacturing
Quality assurance and control measures are implemented throughout the API manufacturing process to maintain stringent quality standards and meet regulatory requirements.
This involves establishing robust quality management systems, conducting risk assessments, and implementing preventive measures to mitigate potential quality deviations.
Quality assurance protocols include comprehensive documentation practices, such as batch records, standard operating procedures (SOPs), and quality control testing protocols, to ensure traceability and accountability throughout the manufacturing process.
Analytical Assays
Assays provide critical data and insights into the quality attributes of raw materials, intermediates, and finished products. These assays involve a variety of analytical techniques, including chromatography, spectroscopy, and titration, to quantify the concentration of active ingredients, assess purity levels, and detect impurities or contaminants.
Suppliers of APIs
APIs are manufactured by a range of companies worldwide, with some prominent players including Novartis, AbbVie, Pfizer, Sanofi, Merck or Lonza Group. These companies are renowned for their expertise in API manufacturing across various therapeutic categories, including generic and specialty pharmaceuticals.
With extensive experience and advanced facilities, they play a crucial role in supplying high-quality APIs to drug manufacturers or produce drug products themselves.
Global Trends in API Production
Several trends are shaping the landscape of API production. As an example, outsourcing of API production to contract manufacturing organizations (CMOs) and emerging markets is on the rise, driven by factors such as cost efficiencies, flexibility, and access to specialized expertise.
Furthermore, single-use technology has gained traction in the production of biopharmaceuticals, offering numerous advantages over traditional stainless steel systems for pharmaceutical companies. Single-use bioprocessing equipment, such as single-use bioprocess container, tubing, and filters, provide greater flexibility, efficiency, and cost-effectiveness in biopharmaceutical manufacturing.
Additionally, single-use systems enable a simplified process scale-up. As a result, biopharmaceutical companies are increasingly embracing single-use technology to streamline their production processes and meet the growing demand for biologics in the healthcare market.
FAQs about Active Pharmaceutical Ingredients
How to freeze and thaw active pharmaceutical ingredients during manufacturing?
Freezing and thawing active pharmaceutical ingredients (APIs) during manufacturing is best achieved using specialized platform systems like the RoSS.pFTU from Single Use Support. Single-use bioprocess containers are utilized to contain and protect the APIs during these processes, minimizing the risk of contamination and ensuring product integrity. Plate-based freeze-thaw platforms with controlled freezing rates have been shown to yield optimal results in this regard. Read more: Freezing drug substance
How to avoid product loss in API manufacturing?
Product loss, or loss of bulk drug substance, poses a risk throughout the supply chain of API manufacturing. Contamination during production, filling, freezing, storing, shipping, and thawing processes can lead to significant costs and compromise product integrity. To mitigate this risk, seamless transitions between each step of the manufacturing process and proper secondary packaging meaning protection of single-use bags are essential. Read more: Loss of drug substance the challenges and chances
How to fill and drain APIs in single-use bioprocess containers?
Disposable equipment allows seamless transfer of the entire process from development to logistics with minimal risk. Single Use Support’s RoSS.FILL system offers fully automated single-use bag filling and draining, ensuring maximum flexibility and scalability. With volumes of up to 200 liters filled in less than an hour, the process is entirely disposable, ensuring sterility. Read more: Filling drug substance
Where are APIs produced?
Several regions are well known for API production, each contributing unique advantages to the biotechnology market. The USA boasts a robust pharma industry with advanced technologies and stringent regulatory standards, making it a key player in API production for both domestic consumption and export. India and China had emerged as a dominant force in API manufacturing, driven by its large-scale production capacities, competitive costs, and supportive government policies. Additionally, Europe maintains a strong presence in API production, characterized by its focus on innovation, quality, and sustainability.
Are active pharmaceutical ingredients small molecules?
Active pharmaceutical ingredients encompass both small molecules and large molecules, such as proteins or nucleic acids. Small molecule APIs are organic compounds with relatively low molecular weights and defined chemical structures, while large molecule APIs are complex biological substances, often derived from living organisms, such as monoclonal antibodies or gene therapies.
- National Cancer Institute, https://www.cancer.gov/publications/dictionaries/cancer-terms/def/active-pharmaceutical-ingredient, Published 21.03.2024
- , https://pubchem.ncbi.nlm.nih.gov/compound/Epinephrine#section=UNII, Published
- , https://www.canada.ca/en/health-canada/services/drugs-health-products/compliance-enforcement/information-health-product/drugs/active-pharmaceutical-ingredients-questions-answers.html, Published
- , https://pharmaoffer.com/api-excipient-supplier/opioid-analgesics/morphine-sulfate/cep-coa-fda-gmp, Published
- , https://pharmaoffer.com/api-excipient-supplier/heparins/enoxaparin#:~:text=Enoxaparin%20is%20a%20type%20of,and%20treating%20blood%20clotting%20disorders., Published
- , https://go.drugbank.com/drugs/DB00051, Published
- , https://pharmacentral.com/product/paracetamol-active-pharmaceutical-ingredientiers-and-specifications-copy/, Published
- , https://pubmed.ncbi.nlm.nih.gov/33346165/, Published
- , https://www.pharmacompass.com/active-pharmaceutical-ingredients/, Published
- Wikipedia, https://en.wikipedia.org/wiki/Excipient, Published 21.03.2024
- , https://www.sciencedirect.com/topics/agricultural-and-biological-sciences/excipient, Published
- , https://www.sciencedirect.com/topics/agricultural-and-biological-sciences/excipient, Published
- The synthesis of active pharmaceutical ingredients (APIs) using continuous flow chemistry, http://dx.doi.org/10.3762/bjoc.11.134, Published 2015-07-17