Aseptic filling & processing of biologics
Table of contents
ShowAseptic filling represents a fundamental process within pharmaceutical manufacturing, serving to preserve the potency and safety of biologics throughout the production process. With stringent standards issued by regulatory authorities like the FDA, the filling of drug substance demands for a highly controlled environment and execution, ensuring the utmost quality and efficacy of pharmaceutical products.
In this article, we will discuss the central role of aseptic filling in biopharmaceutical processing. We will provide a comprehensive definition of the term, compare it to similar concepts, and illustrate the aspects that shape the field of aseptic filling.
Aseptic filling – a brief explanation
Aseptic filling serves as the foundation of drug product packaging, operating within stringent sterile conditions. This meticulous practice is performed to prevent microbial contamination, ensuring the safety, efficacy, and shelf life of pharmaceutical products.
Throughout aseptic filling, the primary focus remains on maintaining a germ-free environment. A stringent protocol safeguards drug products from contamination, guaranteeing their reliability and safety for consumers.
Difference between sterile and aseptic processing
Sterile processing and aseptic processing are two distinct methodologies, each with specific characteristics and applications.
Sterile processing involves ensuring the complete absence of viable microorganisms. This method is commonly used for pharmaceutical products that can withstand terminal sterilization processes using high temperatures, filtration, or chemical means. Sterilization is usually performed at the end of a manufacturing process – unlike aseptic filling, which requires a more holistic approach.
This is because aseptic processing aims to maintain a germ-free environment during the entire handling and packaging process of pharmaceuticals, but without necessarily achieving absolute sterility in the final product. It involves strict controls to prevent contamination, utilizing techniques such as isolators, laminar airflow, and sterile barriers to safeguard against microbial ingress during the filling process.
Benefits of aseptic filling
Aseptic filling presents several key advantages, as it allows manufacturing sterile products that are safe and effective for clinical use. Additionally, aseptic filling comes with some other key advantages:
- Preservation of product integrity: The nature of aseptic filling contributes to maintaining the integrity of pharmaceutical products. By minimizing exposure to heat, chemicals, or physical stress bound to sterilization methods, the quality and efficacy of the products are preserved.
- Adherence to regulatory compliance: Aseptic filling aligns with stringent regulatory standards, such as those set by the FDA. Compliance with these regulations is crucial for ensuring product safety and meeting industry standards.
- Extended shelf life: Aseptic filling techniques contribute significantly to prolonging the shelf life of pharmaceutical products. By maintaining a sterile environment throughout the filling process, these products remain shelf-stable and thus viable for longer durations.
Aseptic filling – fields of application
Aseptic filling extends its significance across diverse industries, ensuring sterile packaging and product integrity:
Pharmaceuticals: Aseptic filling is paramount in pharmaceuticals (e.g. in vaccine production), maintaining sterility to uphold the potency, safety, and regulatory compliance of medicinal products.
Food products: In the food industry, aseptic filling safeguards various food items, preserving food safety, nutritional quality, and compliance with standards.
Cosmetics: Aseptic techniques are utilized in cosmetic industries, maintaining sterile conditions during the packaging of beauty and personal care products.
Healthcare products: Aseptic filling is essential in healthcare for packaging items such as medical devices and sterile solutions, ensuring safety and compliance.
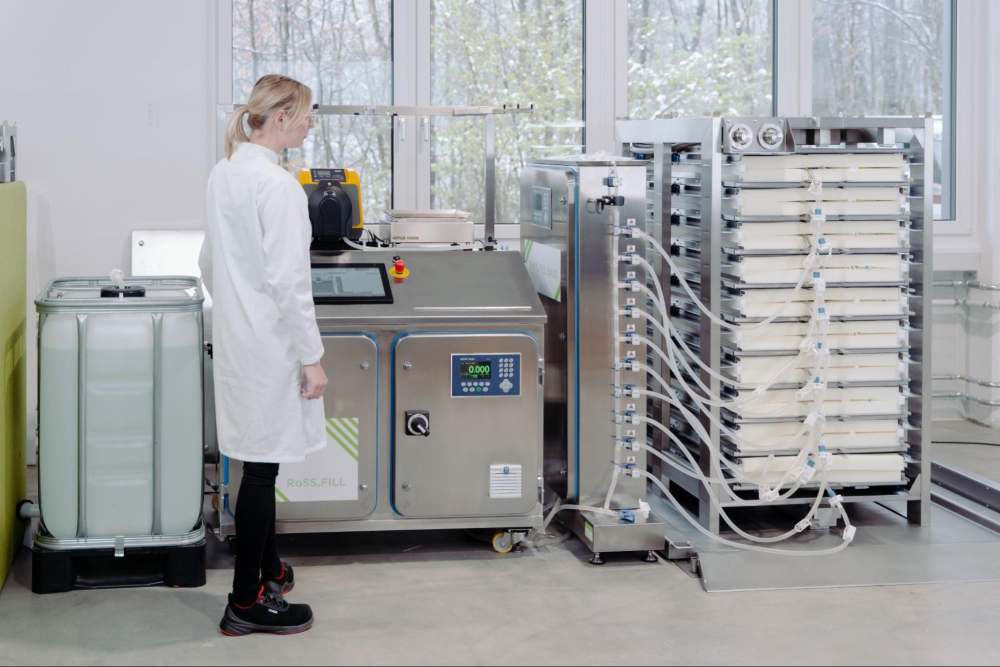
Components of fluid management systems in biopharma
In biopharmaceutical manufacturing, fluid management systems involve several crucial components that collectively ensure the integrity, sterility, and precision of the final product. These components, meticulously designed and integrated into the fill-finish systems, may include:
- Isolators and barrier systems: These specialized enclosures create a thoroughly controlled, sterile environment for aseptic processing. By isolating the filling area from the external environment, they effectively prevent any microbial ingress during critical filling operations.
- Laminar airflow hoods: Operating by providing a continuous flow of filtered air, these hoods establish a clean and sterile workspace. They significantly reduce the risk of contamination by effectively controlling airborne particles, e.g. during the fill-finish process.
- Tubing solutions: Sterile tubing assemblies make sure that neither final drug products nor their individual components are contaminated during the multiple fluid transfer processes.
- Sterile bioprocess containers: Specialized containers undergo stringent sterilization processes to maintain their sterility. They ensure that the pharmaceutical product remains uncontaminated during the filling process into, as they are increasingly frequent, single-use bioprocess containers.
- Filtration units: Employed for the filtration of liquids or gases, these units eliminate particulates and microorganisms, ensuring that the substances entering the containers are free from contaminants before the filling stage. As their integrity is vital, PUPSIT (pre-use post sterilization integrity testing) is mandatory.
- Closing and sealing systems: Automated systems play a crucial role in securely sealing containers. These systems are designed to ensure aseptic disconnection and the integrity of seals, preventing any contamination post-filling.
- Sterilization equipment: X-Ray sterilization or gamma irradiation are examples of sterilization approaches that can be deployed before components enter the aseptic filling process. This ensures that all components are suitable for aseptic filling.
- Process monitoring and control instruments: Incorporating sensors, tracking and monitoring devices (such as RFID sensors1), these instruments regulate and oversee various parameters during the filling process, maintaining optimal conditions and ensuring precision along with traceability.
- Validation equipment: These tools and systems are pivotal for the validation processes, ensuring that the entire fill-finish system functions reliably and complies with stringent quality standards.
Fluid management does not always require all the aforementioned tools, but may also demand for several more to be implemented. Let’s highlight some components that are essential in a multitude of aseptic filling processes.1
Aseptic filling machines
Aseptic filling machines operate within highly controlled, sterile environments. Their primary function is to precisely fill drug products while upholding stringent sterility standards. These machines serve as the frontline defense against contamination, ensuring that the drugs remain uncontaminated throughout the fluid transfer process.
The precision engineering of solutions like the RoSS.FILL platform allows for accurate automated aliquotation, minimizing any margin of error and optimizing the use of pharmaceutical ingredients while reducing wastage. Integrated seamlessly into larger filling lines, aseptic filling machines work in tandem with components like fillers designed for specific drug formulations.
Tubing solutions for pharmaceutical liquids
Contamination prevention and precision in pharmaceutical compounding and filling processes heavily rely on the right bioprocess tubing solutions. These solutions act as the vital conduits for pharmaceutical liquids, ensuring their integrity from formulation to packaging.
During compounding, these tubing solutions facilitate the precise transfer and mixing of various pharmaceutical ingredients, ensuring uniformity and accuracy in the final product. In filling processes, their role is paramount in maintaining sterility, preventing contaminants from compromising the product's quality.
The choice of tubing solutions involves careful consideration of material compatibility, sterilization methods, and adherence to stringent regulatory standards. Additionally, manufacturers have to decide whether to opt for multi-use or single-use tubing solutions, the latter of which are often preferred due to their flexibility, safety, and ease of use. By selecting appropriate tubing solutions, pharmaceutical manufacturers uphold the highest quality and safety standards in their processes, guaranteeing that every pharmaceutical liquid meets rigorous criteria before reaching consumers.
Bioprocess containers
When speaking of filling, it is only logical to ask where a fluid is filled into. However, the answer to this question is far from trivial when it comes to pharmaceutical processing, as there are multiple options regarding the primary packaging of drug substances.
Single-use bags have become a frequently chosen primary packaging for liquid pharmaceuticals, able to protect their contents from contamination while being flexible and easy to use. Additionally, IRIS single-use bioprocess containers are able to withstand the expansion and mechanical influences that come with cryogenic or ULT freezing, which is, however, necessary to preserve a variety of complex drug products.
Homogenizers
Homogenizers stand as crucial components in pharmaceutical and aseptic manufacturing practices, ensuring product uniformity and quality. They are instrumental in the production of consistent and homogeneous mixtures by breaking down particle sizes and ensuring uniform distribution of components within pharmaceutical formulations.
In aseptic manufacturing practices, homogenizers play a dual role. They not only contribute to product uniformity but also have to align with stringent standards of sterility. Homogenizers like Single Use Support’s RoSS.PADL are designed to operate within controlled aseptic environments, ensuring that the homogenization process occurs without compromising the sterile conditions required for pharmaceutical production. It is therefore vital that homogenizers, if required within the fluid transfer process, can be seamlessly integrated into the surrounding technological environment.
Challenges in aseptic filling
Aseptic filling within pharmaceutical manufacturing poses a spectrum of challenges that demand close attention to detail. Contamination remains a lurking concern, capable of causing substantial product loss and compromising consumer safety. Additionally, scalability as well as sustainability and efficiency can be challenging.
Read more: Aseptic filling of small volumes
Many of the challenges regarding process safety are sublimated in the stringent standards set by regulatory bodies, such as the FDA (Food and Drug Administration). Compliance entails meticulous validation of processes, stringent cleanroom protocols, and adherence to labeling requirements. The absence of terminal sterilization processes like irradiation necessitates all the more attention to detail, providing product safety and efficacy while ensuring regulatory compliance.
Pharmaceutical companies strive to meet these challenges by investing in advanced technologies, robust quality control measures, and comprehensive training programs to foster a culture of compliance and precision even in aseptic filling of large volumes. The aim is to curtail product loss, maintain product integrity, and, most importantly, ensure consumer safety.
In terms of process solutions, single-use technologies are being more and more implemented for several reasons. They reduce the need for cleaning and sterilization at the manufacturer’s site, as single-use components usually come pre-sterilized and ready for implementation. This saves water, energy, time and costs while ensuring flexibility and safety in aseptic filling processes.
Automated solutions for aseptic liquid handling with Single Use Support
Automated aseptic filling systems by Single Use Support transform aseptic liquid handling in pharmaceutical manufacturing. These systems epitomize advanced technology and precision, reshaping the way sterile liquids are managed in the industry.
Single Use Support's automated fluid management platform RoSS.FILL can seamlessly integrate into manufacturing processes. It ensures accuracy, sterility, and adaptability across various applications, from lab-scale manufacturing, CGT and other small-scale processes to bulk production of biopharmaceuticals like vaccines.
Engineered to comply with highest industry standards, RoSS.FILL guarantees regulatory compliance and adherence to cGMP regulations while being complemented by single-use bags, single-use tubing assemblies made of silicone and additional professionalized systems, such as the homogenizer RoSS.PADL, but even solutions that go beyond fluid management alone.
In order to create a seamless end-to-end process for pharmaceuticals, Single Use Support has designed a complete product line up that also covers various freezing processes of temperature-sensitive drug substances. Plate freezing solutions like RoSS.pFTU, ULT storage freezers and shipping containers – to name just a few – enable pharmaceutical manufacturers to create a closed and safe environment in drug production from start to finish.
More about aseptic filling
Automated aseptic filling systems by Single Use Support transform aseptic liquid handling in pharmaceutical manufacturing. These systems epitomize advanced technology and precision, reshaping the way sterile liquids are managed in the industry.
Single Use Support's automated fluid management platform RoSS.FILL can seamlessly integrate into manufacturing processes. It ensures accuracy, sterility, and adaptability across various applications, from lab-scale manufacturing, CGT and other small-scale processes to bulk production of biopharmaceuticals like vaccines.
Engineered to comply with highest industry standards, RoSS.FILL guarantees regulatory compliance and adherence to cGMP regulations while being complemented by single-use bags, single-use tubing assemblies made of silicone and additional professionalized systems, such as the homogenizer RoSS.PADL, but even solutions that go beyond fluid management alone.
In order to create a seamless end-to-end process for pharmaceuticals, Single Use Support has designed a complete product line up that also covers various freezing processes of temperature-sensitive drug substances. Plate freezing solutions like RoSS.pFTU, ULT storage freezers and shipping containers – to name just a few – enable pharmaceutical manufacturers to create a closed and safe environment in drug production from start to finish.
- RFID sensors as the common sensing platform for single-use biopharmaceutical manufacturing, http://dx.doi.org/10.1088/0957-0233/22/8/082001, Published 2011-07-16