Single-use bioprocessing: Why it pays off to switch to single-use systems now
Table of contents
ShowSingle-use bioprocessing has recently experienced tremendous growth in biopharmaceutical manufacturing market share and enjoyed technological advances ranging from material properties, to implementation of Industry 4.0.
In contrast to traditional bioprocessing, relying on durable stainless steel equipment, modern single-use systems (SUS) engage in the single use of disposable components. This approach comes with the promise of increased productivity, reduced cost of goods, higher quality products and the potential to streamline personalized medicine supply chains.
With this article, we will give background information on the key concepts of single-use systems, their advantages and downsides, and whether they can hold their promises in biopharmaceutical processing.
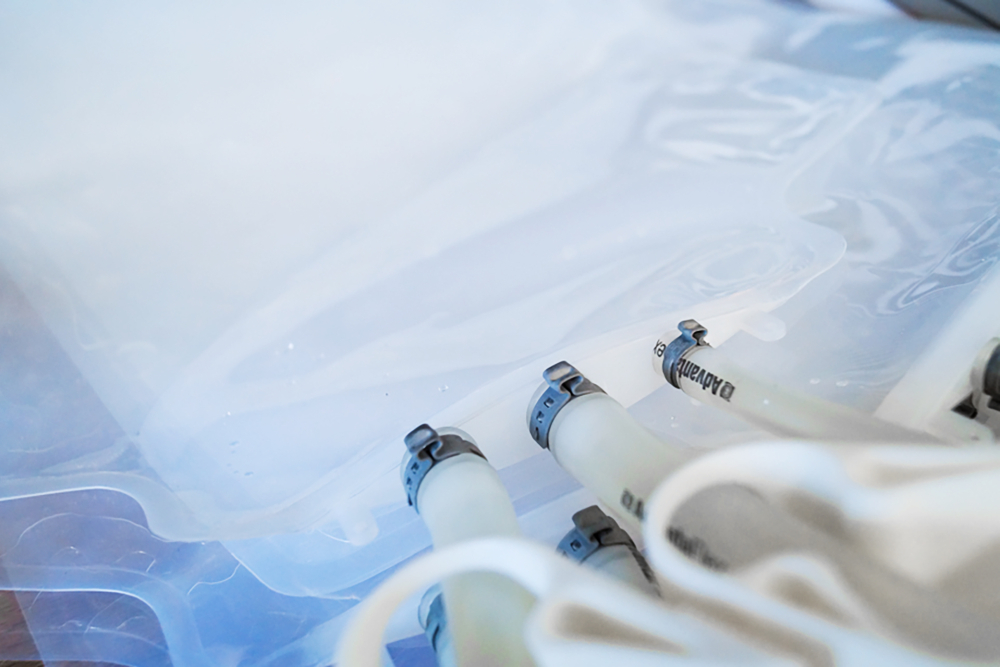
What is the role of single-use systems in bioprocessing?
Single-use bioprocessing is a relatively new concept in the production of biopharmaceuticals. All of the active pharmaceutical ingredients must be sterile for their administration. Therefore, they must be produced under aseptic conditions.
Compared to single-use systems, traditional production with stainless-steel equipment is generally expensive and thus requires a high degree of maintenance for re-use and hence high operational expenditures for several years.
The downsides to the manufacturing processes relying on stainless-steel equipment are the low degree of flexibility (i. e. dedicated production lines for single products or manufacturing steps) and large outlay in time and labor to ensure the equipment is ready. This entails clean-in-place (CIP) and sterilize-in-place (SIP) procedures and final validation of re-used bioprocessing equipment that are time-consuming and binding ressources.
Single-use equipment is bound to revolutionize the vast majority of biomanufacturing process steps in facilities of biopharmaceutical companies. There is high potential in making processes more cost-effective due to simplification and customization of several aspects of bioprocessing technology and reducing cost-of-goods.
The next section will provide insights on key advantages of single-use technology in biopharmaceutical production.
Six advantages of single-use bioprocessing solutions when producing biopharmaceuticals
Here are six key benefits of single-use bioprocessing solutions over traditional bioprocessing hardware, that relate to economic factors, product safety and quality, and business model feasibility.
1. Cost reduction
As opposed to bioreactor systems, single-use facilities are easier to maintain. Costs for complex production stages like cleaning (CIP) and sterilization (SIP) become void when using single use technologies, thus saving costs and resources.
Those direct savings in terms of material and labor costs are one of the main advantages of single-use systems in biopharmaceutical processing. Direct labor costs for installation as well as costs for water and chemicals can be minimized. Furthermore, the facilities do not require cleaning and sterilization, which in turn leads to a prolonged operating life and further reduction of total cost of ownership.
In addition, single-use bioprocessing solutions help reduce initial investment as well as R&D costs, which is a huge advantage given the tremendous market growth in the sector of biopharmaceuticals. The initial investment costs are approximately 40% lower than the price for a comparable stainless-steel facility.
2. Increased productivity
For biopharma companies and contract manufacturers, the use of single-use technologies leads to an increase in productivity. Costs and the complexity of automatization are markedly reduced. Complex steps like cleaning and validation between the separate production stages can be omitted.
Traditionally, the production of biopharmaceuticals requires steel-based bioreactors. These need to be thoroughly cleaned and sterilized for the production of contamination-free bioproducts, thus increasing costs for the manufacturer.
3. Simplified disposal
It is relatively easier to dispose spent single-use equipment than stainless steel equipment. Single-use systems do not require any elaborate cleaning and disinfection, but can rather be disposed of immediately after their utilization.
In contrast, recycling of stainless steel involves melting processes and is a very energy consuming process.
4. Reduced energy and media consumption for sustainable manufacturing processes
The operation of a traditional biotechnology plant requires large amounts of energy to heat the steel equipment to operating temperatures and consumes diverse media between and during runs: pressurized air, water in several qualities from deionized to sterilized (water for injection, WFI), exhaust air, waste water, etc.
Single-use assemblies are shown to allow large reductions of media consumption relative to steel equipment based plants (approx. 46% for water). All in all, the average reduction of the carbon footprint (includes reduction of water, energy, chemicals, etc.) was 40% compared to stainless steel!
In terms of sustainability, single-use products offer even more benefits compared to their multi-use pendants: As already stated, single-use biotechnology systems are mostly made of plastics which can be recycled in the form of other plastic items or alternatively be incinerated to release their stored chemical energy for electricity or heat generation. Generally speaking, studies have shown how the implementation of single-use systems can significantly reduce the environmental impact of biopharma manufacturers.
5. Efficient use of time and resources
Related to the first two points, the adoption of single-use technology such as single-use bioreactors allows the redistribution of time and resources from cleaning and sterilization to productive tasks.
With CIP and SIP becoming unnecessary, dedicated staff for these procedures are freed up to engage in other activities like immediately taking care of set-up of the next batches or disposing of used equipment. Generally, most of the time and labor previously consumed for preparing for and cleaning-up after each batch can be cut out of the manufacturing plant’s schedule, thus significantly increasing the plants output per time unit.
Additionally, the set-up of single-use bioprocessing solutions can be designed more space-efficient, quick and easy, leading to even more conservative use of time and resources and finally more competitive pricing of pharma products.
6. Cross-contamination risk minimized
A point of concern for biotech companies when re-using equipment is the risk of cross-contamination between batches and products. Although measures are taken to reduce the risk for the end user, rare mistakes might still happen.
Single-use solutions render cross-contaminations virtually impossible, since the whole setup is disposed of when the batch is transferred to the next manufacturing step.
Frequently used materials
Bioprocessing equipment is generally used in upstream and downstream processing steps. Upstream sterile consumables are e. g. bioreactors, disposable mixers, media bags, etc. Popular downstream components are aseptic connectors, filters and tubing assemblies, separation columns.
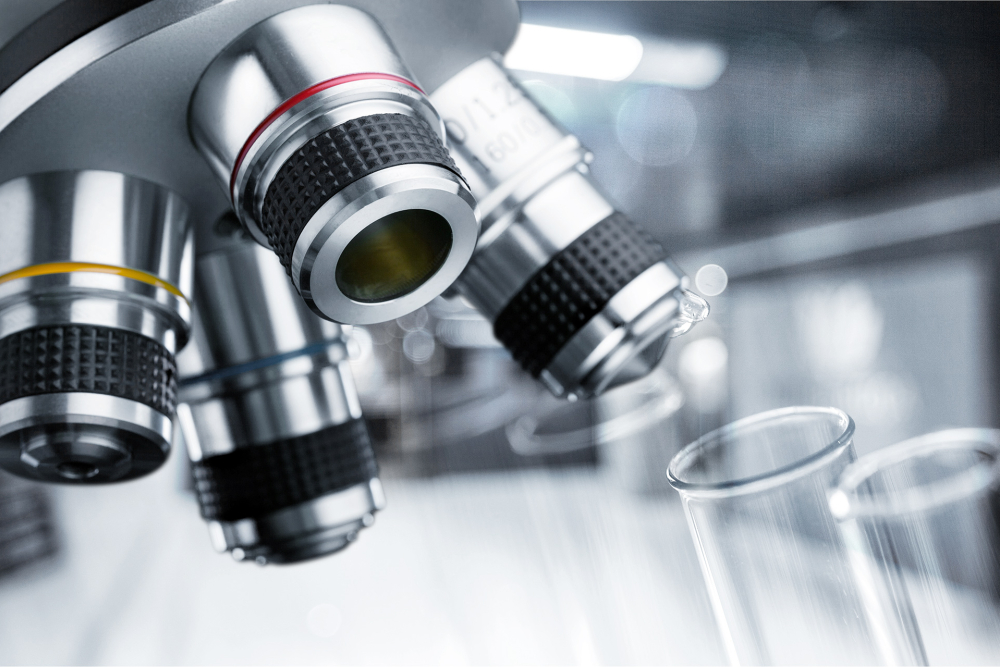
Single-use components are generally made of high performance polymer materials. The top 6 most important ones are:
- Polyethylene (PE) and Polypropylene (PP) – transparent, chemically inert to aqueous media, PP’s material properties can be adjusted over broader ranges than PE
- Polyethersulfone (PES) – heat-resistant, impact-resistant plastic, great for processes with elevated temperatures, approved for baby articles
- Polytetrafluorethylene (PTFE) – known as Teflon; chemically very inert and FDA approved for pharma and food applications, weak under mechanical stress; good for inner layers when using more aggressive materials
- Cellulose acetate (CA) – hard material, made from cellulose by esterification with acetic acid, popular single-use material for filtration cartridges
- Polyamide (PA) – nylon is a well known example of polyamide, PAs are very mechanically resistant and durable, good material for outer layers in composite components
- Polycarbonates – Polyethylene terephthalate PET is probably the best known representative; widely used in food containers and bottles, although not very resistant against strong acids and bases
Since each of these materials comes with unique properties, advantageous and disadvantageous, high performance single-use components often consist of multiple plastic materials. As an example, bioreactors are usually laminated foil bags with several layers serving different functions:
- inert inner layers to contain aggressive chemicals or solvents, or for protection of the contents against plasticizers from outer layers
- gas tight layers to contain a specific atmosphere (elevated CO2 inside, keeping oxygen out.
- outer layers conferring mechanical resistance against tearing, impacts, etc. (up to six layers overall).
Speaking of multi-layer: Another product that is compound of multiple layers is Single Use Support’s IRIS 2D Bag – the single-use bioprocess container is designed to protect biologics for an uninterrupted supply chain and is available in different sizes.
The biggest manufacturers of single-use components are Merck-Millipore, Sartorius and Thermo Fisher Scientific. Assembling single-use components to custom designs are also provided by vendor-agnostic companies like Single Use Support.
Single-use bioprocessing and where to find it
Some process steps are expected to remain multi-use, e.g. chromatography columns by the means of chromatography systems for monoclonal antibody purification; large-scale Protein A columns come with expenses of several 100K USD and are relatively easy to re-use (cave: cross contamination risk).
However, the range of applications where single-use components are employed is continually broadening, with innovative new products getting on the market. But the field has experienced a sharp surge recently during large capital influx into the healthcare system and life sciences for vaccine-related product development beyond COVID-19 during the pandemic. Find an overview of novel single-use biotechnology systems:
Fluid management with single-use systems
Management of liquids is an essential aspect of bioprocessing, since all manufacturing steps occur in liquid phases. Modern, integrated platform solutions allow for a high degree of automation in managing and handling fluids with dedicated fill and filtration systems.
Single Use Support supplies the global single-use bioprocessing market with the fully automated single-use bag filling system RoSS.FILL Bag that allows the aseptic transfer of liquids with materials flows of up to 300 liters per hour.
The other end of the spectrum is covered by the cell and gene therapy filling system RoSS.FILL CGT. It is able to fulfill all requirements of Cell and Gene Therapy (CGT) manufacturing, ranging from aseptic fluid transfer of small volumes with highest precision to coupling with freezing storage solutions.
Ready for storage and transport
Modern biopharmaceuticals are often delicate substances that require special conditions during storage and transport. Production environment around CGTs is a tremendous challenge for the big players in pharmaceutical business, their scale-up and supply chain bears challenges. Nevertheless, they work very well for otherwise hard to treat conditions and offer hope for countless patients, so the effort pays off!
This motivates us to find solutions to overcome these troubles – for instance, we deliver solutions for the protection of drug substances with smaller volumes – the RoSS.KSET – and single-use bag protection RoSS Shell that provide ample protection against mechanical stress like impacts.
What to consider when switching to single-use bioprocess systems
A few key aspects of single-use systems have to be taken into account when switching from stainless steel equipment.
When choosing materials, one must consider the specific applications, since extractables and leachables (e. g. plasticizers) should be avoided. When using solvents, a modern multi-layered component with solvent resistant inner lining would be chosen over cheaper PVC components.
Single Use Support can help to find the ideal options of single-use component platforms to ensure compatibility and interoperability of components, thus taking full advantage of single-use technology for your bioprocesses.
Meeting cGMP requirements with single-use technology
Requirements related to cGMP (current Good Manufacturing Practice) must be met at all times in order for the produced products to meet safety and quality standards. With automated end-to-end solutions based on single-use technologies, these standards can be met along the entire manufacturing process. Single Use Support's automated platform systems and single-use consumables reduce human error and product loss, therefore it is a good option to rely on single-use technology to meet cGMP requirements.
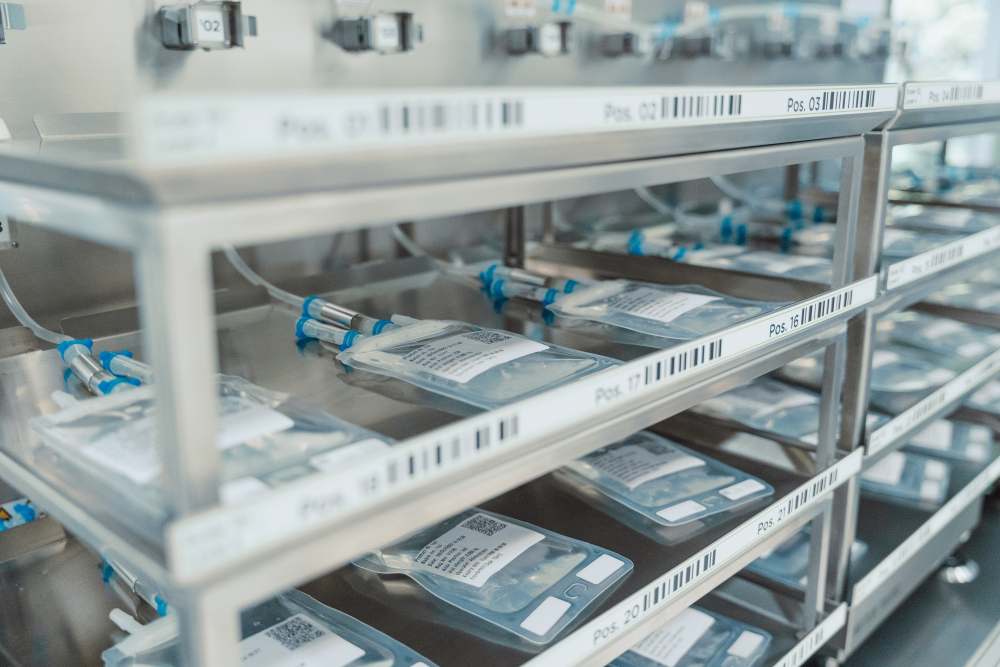
A bright future ahead – looking at recent developments
As outlined above, single-use systems were virtually non-existent a few decades ago and have since experienced huge growth. Traditional stainless steel containers still dominate the largest commercial scale bioprocesses (10.000 liter scale).
Here lies great room for growth of single-use bioprocessing market size, with double-digit compound annual growth rate (CAGR) estimates in the coming five years. This is accelerated even more by biopharma’s bottlenecks that were highlighted during the COVID-19 pandemic, attracting many government investments to push developments forward. This momentum is generally expected to keep going in the coming decade.1
FAQs
What is single-use bioprocessing?
Single-use bioprocessing describes the use of single-use technologies in the production of biopharmaceuticals. In contrast to multi-use technologies (e. g. based on stainless steel), single-use bioprocessing solutions are used in the manufacture of one single batch and afterwards disposed of. Single-use bioprocessing is considered to be sustainable, in that fewer resources are bound in an elaborate cleaning process.
What is meant by bioprocessing?
Bioprocessing means the production of biopharmaceutical products, i. e. products that partly or entirely consist of material from living individuals (e. g. antibodies, cells, …).
What is single-use technology?
Single-use technology is based on systems that are designed for one specific use before being disposed of. As components and systems based on single-use technology do not need to undergo a resource- and time-consuming cleaning process, bioprocessing solutions based on single-use technologies are frequently chosen as a sustainable option for the biopharma industry.
What is single-use biomanufacturing?
Single-use biomanufacturing is a process in biotechnology where single-use systems are relied on during the production of biopharmaceutical products. Biomanufacturing itself describes the use of living sources to produce biological material, designed to be part of pharmaceutical products.
What are single-use components?
Single-use components in the biopharma industry make part of single-use systems that are used along the supply chain of biopharmaceuticals. Single-use components are designed to be disposed of after their onetime use and can be found in the production, packaging, storing and transportation of biopharmaceuticals.
- Single use Bioprocessing Market by Product (Media Bags and containers, Bioreactors, Mixers, Assemblies), Application (Cell Culture, Mixing, Storage, Filtration, Purification), End User (Biopharma Companies, CROs, CMOs) (2022 - 2026), https://www.marketsandmarkets.com/Market-Reports/single-use-bioprocessing-market-231651297.html, Published