Aseptic filling of large volumes of drug substances
Table of contents
ShowAseptic filling, a critical process in pharmaceutical manufacturing, ensures the sterility of large-volume drug substances, safeguarding their efficacy and safety. Thus, this method plays an indispensable role in maintaining product integrity.
In this article, we will highlight essential aspects of aseptic filling of drug substance, outlining its step-by-step procedure and exploring its applications across diverse pharmaceutical sectors.
What is aseptic filling?
Aseptic filling is a crucial process within pharmaceutical manufacturing that ensures the sterility of drug substances during their transfer into containers in different formats and sizes. It prevents contamination by germs, maintaining the purity and efficacy of the product.
Aseptic filling involves a carefully controlled environment where both the product and the surroundings remain free from any microbial contamination throughout the filling process. Aseptic filling techniques are designed to uphold the integrity of the drug substance, crucial for products like injectables, biologics, and other sensitive pharmaceuticals as well as their individual components.
In which areas is aseptic filling necessary?
Aseptic filling becomes necessary for certain drug products that cannot undergo terminal sterilization methods like exposure to high heat, as they are too sensitive and complex to withstand such procedures. It is therefore necessary to create a germ-free environment in which these products can be processed, preventing them from being contaminated at any production step and thus bypassing the need for terminal sterilization of the substance.1
Examples of pharmaceutical products that necessitate aseptic filling include several injectable medications, biologics (such as mRNA vaccines, antibodies, and cell therapies), and certain liquid formulations of medications. These substances are often sensitive to heat or other sterilization methods and must maintain their effectiveness without compromising patient safety.
Moreover, aseptic filling is indispensable in producing drug products intended for injection into the bloodstream or sterile body cavities. This way of administration circumvents natural defense systems like skin or mucous membranes – contaminated drug substances could pose severe health risks to patients. Consequently, maintaining aseptic conditions during the filling process ensures that these medications remain free from harmful microorganisms, preserving their therapeutic value and patient safety.
Read more: Aseptic filling of small volumes1 2
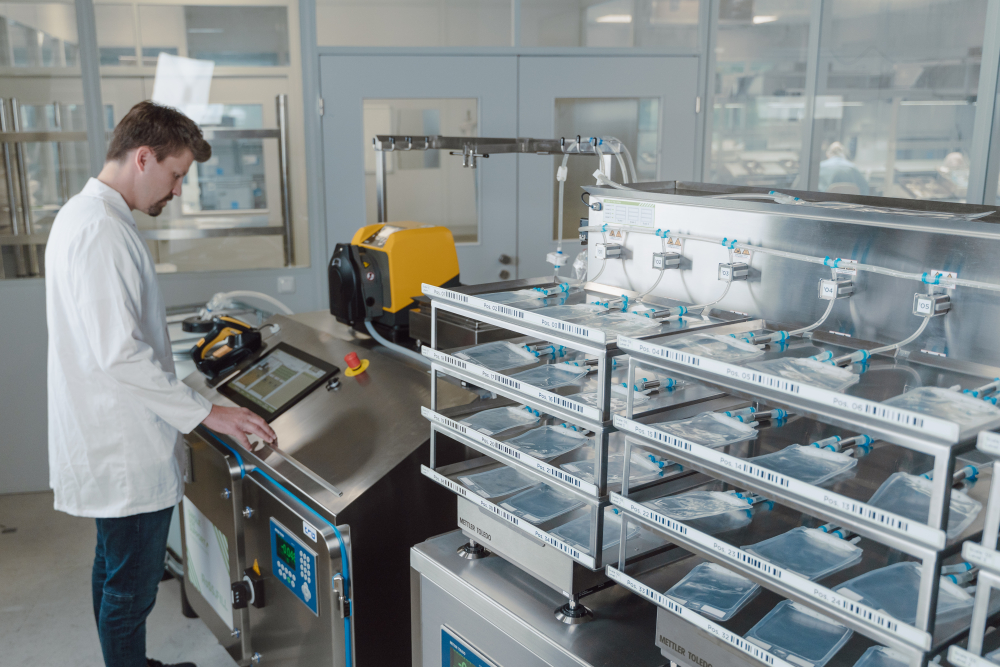
Aseptic filling of large volumes – step by step
In order to ensure a flawless aseptic filling process of large volumes, pharmaceutical manufacturers adhere to a set of process steps that many applications correspond in:
- Preparation phase
The aseptic filling process commences with meticulous preparation. This involves ensuring the cleanliness and sterility of the entire environment, including equipment, surfaces, and personnel attire. - Fluid preparation
The drug substance undergoes preparation, potentially involving filtration and homogenization, to achieve the desired purity and uniformity. - System setup
Fluid management systems are readied for use. These automated systems offer fully controlled fluid paths, ensuring a sterile environment throughout the process. - Filling stage
The prepared drug substance is fed into the aseptic filling machine, such as the RoSS.FILL system. The platform's automation facilitates precise and sterile filling into single-use bags or bottles. - Filtration (if applicable)
Depending on the substance and process requirements, a filtration step might be integrated into the filling process. This step ensures the removal of particulates or microbes that could compromise product integrity. - Packaging and sealing
Once verified, the filled drug substance is sealed into containers or bottles within the closed system. This process is crucial to maintain the sterility and integrity of the product until use. - Post-filling verification
Post-filling, thorough verification processes are undertaken. These include checks for accuracy, sterility, and overall product quality to adhere to stringent regulatory standards. - Clean-up and sanitization
Following the filling process, the used equipment must either be prepared for subsequent following cycles or, in the case of single-use consumables, dissembled and disposed. Relying on single-use technologies can significantly reduce the need for laborious cleaning and sterilization steps at the manufacturing site.
Techniques to ensure success in large-scale aseptic filling
Large-scale aseptic filling techniques encompass a range of measures designed to maintain a sterile environment during the transfer of pharmaceutical liquids. Some key techniques involved in aseptic filling include:
Isolators and barrier systems
These closed systems provide a physical barrier between the product and the external environment, preventing microbial ingress. Isolators are used to enclose specific processes or equipment, ensuring aseptic conditions.
Laminar airflow systems
These systems create a continuous flow of filtered air in a unidirectional manner to maintain a clean and sterile environment within the filling area. They minimize the risk of airborne contamination during the filling process.
Sterile barriers and enclosures
Utilizing sterile materials and barriers, such as sterile gloves, gowns, and covers, helps prevent contamination from personnel or the environment.
RABS (Restricted Access Barrier Systems)
Similar to isolators, RABS provide a physical barrier around the filling area, restricting access and minimizing the risk of contamination.
Automated filling equipment
Automated systems reduce human intervention and the potential for contamination. These machines are designed to fill containers while maintaining aseptic conditions, minimizing the risk of microbial ingress.
Challenges when filling bulk drug substance
In fluid management for large volumes, several challenges demand attention:
- Complexity of scale: Handling larger volumes poses logistical challenges, requiring specialized equipment and infrastructure to maintain aseptic conditions uniformly across the entire volume.
- Sterility maintenance: Ensuring sterility throughout the entire process becomes more challenging with larger volumes, as any contamination can significantly impact a larger quantity of product.
- Time sensitivity: Large-volume aseptic filling often requires swift processing to minimize exposure, which can pose challenges in maintaining aseptic conditions while meeting production speed demands.
- Equipment compatibility: Compatibility between equipment and the properties of larger volumes of drug substances can present technical challenges, requiring specialized machinery and processes.
- Validation and documentation: Validating and documenting aseptic processes for large volumes requires meticulous attention to detail to ensure compliance with regulatory standards.
- Demand for highest precision: Managing larger volumes requires precise control to ensure accurate dosing and uniform distribution throughout the volume, demanding advanced technologies and methods to maintain precision at scale.
- Product sensitivity: Certain drug substances, such as many biologics, can be highly sensitive to environmental conditions, temperature fluctuations, or prolonged exposure to air, intensifying the need for meticulous handling.
Regulatory compliance
Achieving regulatory compliance in aseptic fluid management involves adhering to stringent guidelines aimed at ensuring the safety and efficacy of pharmaceutical products. This necessitates a very general yet elaborate approach:
Implementing Good Manufacturing Practices (GMP) involves meticulous record-keeping and a robust quality management system. Developing and rigorously validating protocols specific to large-volume fluid management is essential, encompassing equipment, processes, and aseptic techniques to meet regulatory expectations.
Establishing a comprehensive environmental monitoring program is crucial for continuous assessment of air quality, surface cleanliness, and microbial levels within controlled environments. Timely resolution of any deviations identified during monitoring is vital to uphold compliance with regulatory standards.
Regular review and adjustment of procedures are necessary to align with evolving regulatory requirements, ensuring continuous adherence to aseptic guidelines and standards.
Source: FDA3
What’s needed for successful aseptic fluid management?
Successful aseptic fluid management requires a combination of strategic elements to ensure the integrity and sterility of pharmaceutical products. Key components for success include:
- Rigorous training programs
- Robust quality control measures
- Failsafe processes
- State-of-the-art equipment
Let’s take a closer look at some of these aspects.
Source: Aspen Survey4
Rigorous training programs
Fluid management solutions have become far more intuitive and support staff during sensitive procedures. User-friendly interfaces, failsafe interconnections and implemented integrity control measures facilitate the operation of these machines.
However, a great deal of responsibility remains with the operators of fluid management systems, the expertise of whom is required, for instance, when production lines are being altered, or when malfunctions have to be detected and corrected. Additionally, awareness of the characteristics of processed substances is required, just like general knowledge on pharmaceutical liquid processing.
Consequently, rigorous training programs for scientific staff in liquid management are required that not only cover this area in general. It is equally important to mediate the necessary know-how on individual fluid management platforms and processes.
Quality control tests
The integrity of fluid management processes, systems, equipment, and ultimately the processed pharmaceutical product is to be maintained and monitored. For that end, quality control tests are implemented to ensure product safety and effectiveness.
Notably, it is not enough to validate the quality of the final product at the end of a production cycle. Large amounts of potentially faulty batches might have been produced in the meantime due to an undetected deviation in the fluid management process.
Reasonably, individual components have to be tested in order to ensure their integrity when being implemented into fluid management systems. This applies to components like optional filters, which is why pre-use post sterilization integrity testing (PUPSIT) is often performed to guarantee that these filters meet the high standards in aseptic fluid management.
Failsafe, automated fluid management processes
Ensuring failsafe fluid management in aseptic environments requires diligent planning and execution of meticulously designed processes. For that purpose, detailed procedures and standardized protocols provide precision in upholding aseptic principles. This is further facilitated by automation, including robotics, which reduces human intervention and ensures consistency and sterility while minimizing the risk of contamination.
Closed systems and as well as end-to-end solutions physically prevent environmental contaminants. Continuous monitoring, enabled by sophisticated systems, tracks critical parameters for real-time detection of deviations, allowing immediate corrective actions.
Another key element in pharmacovigilance is validation, along with precise documentation to ensure consistent adherence to predetermined standards. Yet again, automation can help to uphold quality standards, streamlining operations, and upholding stringent aseptic conditions in fluid management workflows.
Adequate materials for tubing solutions and other components
Aseptic production demands material that adhere to strict criteria to uphold sterility and product integrity. These components must demonstrate minimal permeability to prevent contaminants or gases from compromising the product. Additionally, they should exhibit low extractables profiles to minimize any potential leaching of substances that could affect product safety.
Materials such as stainless steel, glass, or specialty polymers are often used for reusable systems. They allow maintaining aseptic conditions while providing enhanced durability. However, due to factors like increased flexibility, biopharma companies are increasingly implementing single-use technologies in their fluid management processes. And as the filling approach evolves, so do the required materials.
As for single-use tubing assemblies, for instance, commonly used materials include silicone and thermoplastic elastomers (TPE). These materials are favored for their flexibility, resilience, and suitability for single-use applications. Silicone, known for its biocompatibility and inertness, along with TPEs, offers excellent chemical resistance and low extractables, making them ideal for maintaining aseptic conditions in tubing solutions while ensuring the safety and quality of pharmaceutical products.
However, all the involved components, including materials chosen for containers, closures, and packaging undergo rigorous evaluation to meet stringent criteria for sterility, durability, and compatibility with pharmaceutical products.
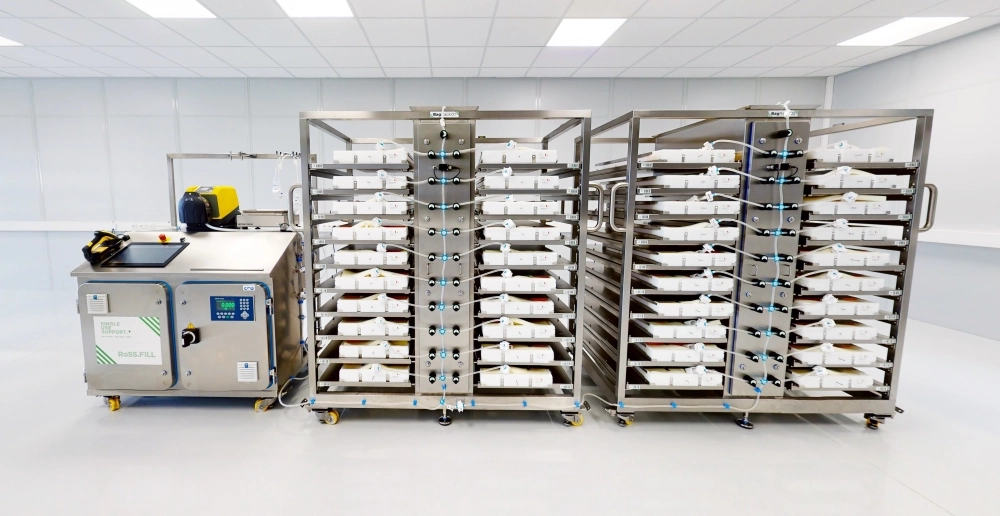
Dedicated aseptic filling machines and additional assemblies
Dedicated aseptic filling machines and complementary assemblies play a pivotal role in aseptic fluid management. These modular fluid management solutions precisely dispense the prepared fluid into containers – but there is more to it.
Filtration steps are essential for many products, ensuring the removal of particulates and microbes from the fluid. However, the need for separate filtration machines is often circumvented by the direct implementation of filtration technologies into filling platforms.
Additionally, modular fluid management systems allow the integration of homogenization machines, crucial for kneading components in order to ensure uniform, consistent product quality. These machines work in tandem, preparing the fluid for filling by achieving the required purity and uniformity.
The interplay between filtration, homogenization, and filling machines is critical. Filtration primes the fluid by removing impurities, homogenization guarantees uniformity, prior to aseptic filling into sterile containers.
Filling machines for large volumes based on single-use technologies
Within the RoSS.FILL platform for automated fluid management, Single Use Support has integrated dedicated solutions for aseptic filling of large volumes.
In aseptic large volume drug filling, Single Use Support stands at the forefront, providing innovative solutions that redefine pharmaceutical processes. Among these advancements is the RoSS.FILL system, a fully automated single-use filling and filtration platform. Offering scalability and adaptability, RoSS.FILL transforms aseptic filling and draining processes, accommodating a diverse range of consumables and manifold systems for unparalleled flexibility.
Further complementing Single Use Support's portfolio are the RoSS.FILL Bag and Bottle systems. RoSS.FILL Bag provides a flexible solution for aseptic bag filling, ensuring sterile connections and a fully disposable fluid path. On the other hand, RoSS.FILL Bottle offers efficient filling and filtration of liquid drugs into bottles, maintaining high accuracy within a closed system.
Additionally, the RoSS.PADL platform focuses on homogenization, gently massaging single-use bags while cooling to ensure a homogenous mixture of solutions. Simultaneously, the RoSS.DRAI system facilitates controlled fluid flow during the draining process, minimizing holdup volumes and enabling continuous pooling.
Innovatively integrating supplier-independent filters into the RoSS.FILL platform enhances the speed and reliability of bulk drug substance production, optionally with the possibility for PUPSIT (pre-use post sterilization integrity testing) to ensure filter integrity. This interplay further extends the range of sterile compound and segregation options, responding to the demands of the fast-paced pharmaceutical industry.
Single Use Support's fluid management systems redefine aseptic large volume drug filling, emphasizing automation, scalability, and speed. These solutions represent a commitment to advancing pharmaceutical logistics, ensuring sterility, and meeting the evolving demands of the industry.
Aseptic large volume drug filling with single-use technologies
In aseptic large volume drug filling, Single Use Support stands at the forefront, providing innovative solutions that redefine pharmaceutical processes. Among these advancements is the RoSS.FILL system, a fully automated single-use filling and filtration platform. Offering scalability and adaptability, RoSS.FILL transforms aseptic filling and draining processes, accommodating a diverse range of consumables and manifold systems for unparalleled flexibility.
Further complementing Single Use Support's portfolio are the RoSS.FILL Bag and Bottle systems. RoSS.FILL Bag provides a flexible solution for aseptic bag filling, ensuring sterile connections and a fully disposable fluid path. On the other hand, RoSS.FILL Bottle offers efficient filling and filtration of liquid drugs into bottles, maintaining high accuracy within a closed system.
Additionally, the RoSS.PADL platform focuses on homogenization, gently massaging single-use bags while cooling to ensure a homogenous mixture of solutions. Simultaneously, the RoSS.DRAI system facilitates controlled fluid flow during the draining process, minimizing holdup volumes and enabling continuous pooling.
Innovatively integrating supplier-independent filters into the RoSS.FILL platform enhances the speed and reliability of bulk drug substance production, optionally with the possibility for PUPSIT (pre-use post sterilization integrity testing) to ensure filter integrity. This interplay further extends the range of sterile compound and segregation options, responding to the demands of the fast-paced pharmaceutical industry.
Single Use Support's fluid management systems redefine aseptic large volume drug filling, emphasizing automation, scalability, and speed. These solutions represent a commitment to advancing pharmaceutical logistics, ensuring sterility, and meeting the evolving demands of the industry.
- The Basics of Aseptic Processing, https://www.pharmtech.com/view/the-basics-of-aseptic-processing, Published 2021
- Aseptic Processing: A Primer, https://www.biopharminternational.com/view/aseptic-processing-primer, Published 2013
- Guidance for Industry Sterile Drug Products Produced by Aseptic Processing — Current Good Manufacturing Practice, https://www.fda.gov/media/71026/download, Published 2004
- Aspen Survey: Which of the following represents the greatest challenges to your process? ASQ 1282 2023 121123, https://, Published 2023